An Advanced Deburring and Chamfering System
international symposium on robotics(1990)
摘要
A second-generation automated deburring cell is currently under development at the National Institute of Standards and Technology. This cell will be capable of automatically generating, from part geometry and machining information, a series of robot paths for deburring aerospace parts made from superalloys. In order to compensate for the inaccuracy of robots when following computed coordinates, an actively-cont rolled end effector will be used to precisely position a rotary file in response to forces sensed at the part edge. The process planner can be effectively implemented as an expert system which encapsulates the knowledge of a human. The role of the process planner is twofold. First, it must determine the likely nature and location of burrs based on the part geometry and machining history. Second, it must consult models of burr removal to determine which deburring processes will effectively remove the burrs. The trajectory planner uses the sequence of part features and the processes to be applied to these features to develop a set of robot trajectories that will accomplish the deburring. These trajectories consist of coordinates corresponding to the part features to be deburred, augmented with housekeeping data such as tool commands, approach points, and depart points.
更多查看译文
AI 理解论文
溯源树
样例
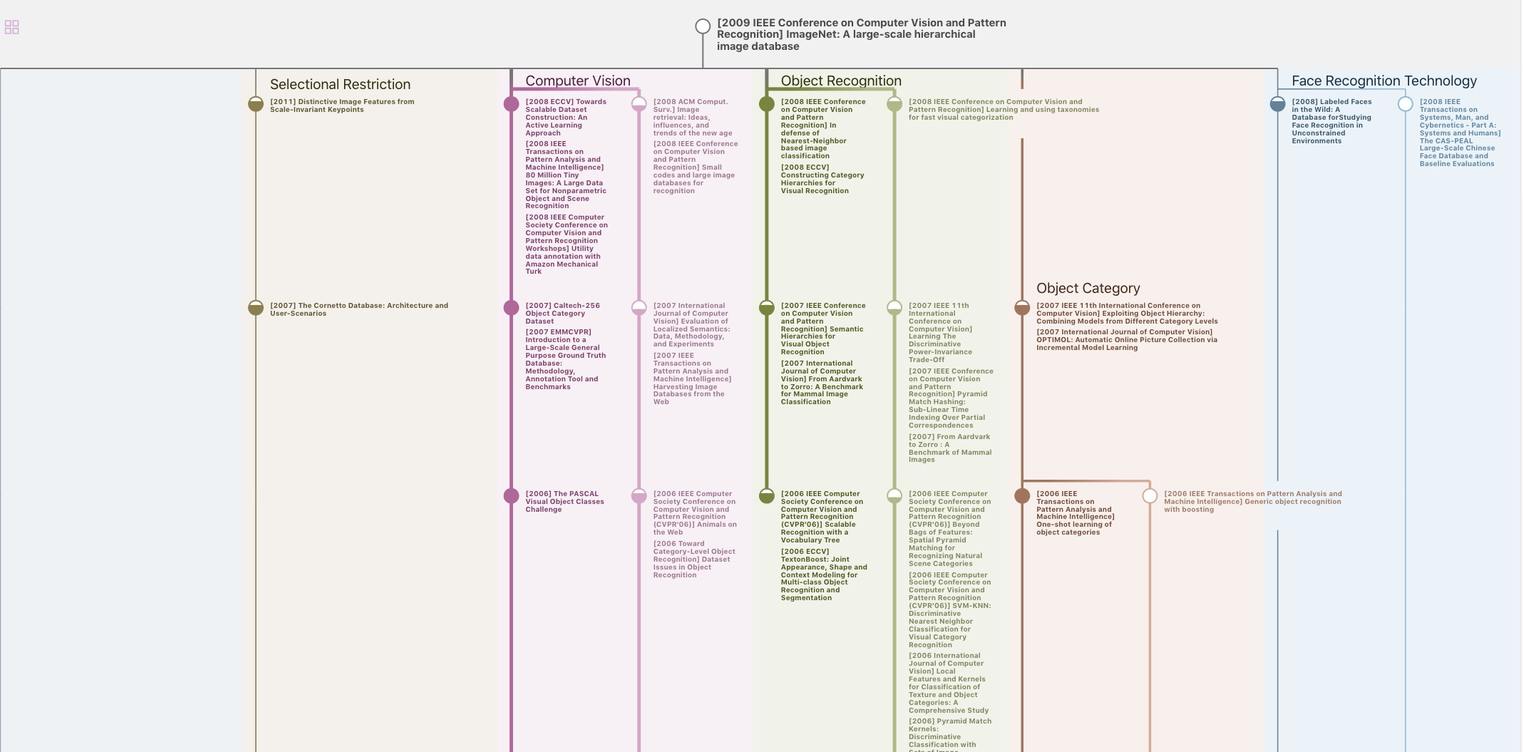
生成溯源树,研究论文发展脉络
Chat Paper
正在生成论文摘要