Shear strength and wettability of active Sn3.5Ag4Ti(Ce,Ga) solder on Al2O3 ceramics
Materials & Design(2011)
摘要
Highlights ► Sn3.5Ag4Ti(Ce,Ga) used for ultrasonic soldering. ► The best wettability on Al 2 O 3 : Θ = 46° at 850 °C/3 min. ► X-ray diffraction analysis: Ag 3 Sn, Ti 6 Sn 5 , Ti 3 Sn phases. ► The shear strength Al 2 O 3 /Al 2 O 3 and Al 2 O 3 /metal joints: from 17 to 35 MPa. Abstract The work deals with the study of wettability of Sn3.5Ag4Ti(Ce,Ga) solder on ceramic material of Al 2 O 3 . The Sn3.5Ag4Ti(Ce,Ga) solder is used for ultrasonic soldering of metallic and ceramic materials. The microstructure of Sn3.5Ag4Ti(Ce,Ga) solder consists of a tin matrix, where non-uniformly distributed constituents of partially dissolved Ti and uniformly distributed fine needles of Ag–Sn phase were observed. The solder was of heterogeneous composition. X-ray diffraction analysis has revealed the presence of following phases: Ag 3 Sn, Ti 6 Sn 5 , Ti 3 Sn. For determination of melting point, the Differential scanning calorimetry analysis (DSC) was performed. Wettability of Sn3.5Ag4Ti(Ce,Ga) solder was determined at temperatures 800, 850 and 900 °C in dependence on wetting time. The best wettability of solder Θ = 46° was achieved at 850 °C/43 min. The experiments with high-temperature activation were performed in vacuum of 10 −4 Pa. On the basis of experience attained by measurement of contact angle, the soldered joints of Al 2 O 3 /Al 2 O 3 and Al 2 O 3 /metal were fabricated in conditions of high-temperature activation in vacuum at temperature 850 °C/10 min. For comparison, also the joints fabricated in the conditions of ultrasonic activation in the air at temperature 280 °C/1 min were applied. The shear strength of joints of Al 2 O 3 /Al 2 O 3 and Al 2 O 3 /metal fabricated with Sn3.5Ag4Ti(Ce,Ga) solder varied from 17 to 35 MPa. The shear strength of joints fabricated in vacuum is slightly higher than in the case of joints fabricated by use of power ultrasound. 1 Introduction There are many reasons in the electronic and electrotechnical practice for necessity to join the parts made of material combination as ceramics [1–7] and metal [3–5] . Formation of a good bonding of material combination composed of ceramic and metal depends on the fact whether a close contact to atomic distance is achieved on the faying surface and whether ceramic material is wetted with a metallic solder [6] . Wetting the ceramics with metallic solder is the main precondition for soldered joint formation. A common metallic solder does not wet the ceramic material. Therefore special measures must be taken, to assure the wettability of ceramic material, for example metal coating on ceramic surface and/or application of an active solder is inevitable. Active solders contain an active element, most often Ti or Zr [1–8] . Active element reacts with the surface of ceramic material during soldering process resulting in reaction layer formation. The reaction layer allows the wetting of ceramic material [9–11] . Active soldering/brazing alloys are divided into solders and brazing alloys. The active solders may be based on tin, lead or indium. Owing to economical reasons, mostly tin based solders alloyed with a small addition of indium are used [12] . Wetting angle of an active metallic solder on a substrate of ceramic or metallic material is the main quality indicator of the future soldered joint. For this reason, experiments with wettability of Al 2 O 3 ceramics with an active solder type Sn3.5Ag4Ti(Ce,Ga) were performed in conditions of high-temperature activation in vacuum at temperatures 800, 850 and 900 °C. High temperature of soldering (above 800 °C) is essential for activation of titanium in the solder. Besides the high temperature, titanium in solder may be activated also by the aid of ultrasonic power, whereby a local temperature increase is achieved. The presented work deals with wettability of active solder type Sn3.5Ag4Ti(Ce,Ga) and shear strength of joints fabricated with Sn3.5Ag4Ti(Ce,Ga) solder. The Sn3.5Ag4Ti(Ce,Ga) solder little oxidizes in the air and therefore it is suitable for soldering with ultrasound [13,14] . In case of soldering with Sn3.5Ag4Ti(Ce,Ga) solder with ultrasonic activation, full wetting on Al 2 O 3 ceramics is achieved [14] . 2 Experimental The Sn3.5Ag4Ti(Ce,Ga) solder is manufactured and supplied by Euromat Co. Heinsberg, Germany. Microstructure of Sn3.5Ag4Ti(Ce,Ga) solder was observed by use of scanning electron microscopy (SEM) on instrument type TESLA BS 300. Semiquantitative analysis of solder was performed on Energy-dispersive X-ray (EDX) spectroscopy analyser, which was a part of microscope type JEOL JXA-840A. X-ray diffraction analysis was applied for identification of phase composition by use of Philips PW 1710 equipment. Differential scanning calorimetry was used to examine the melting point of the solders. The measurements were carried out on the PERKIN-ELMER DSC7 instrument in the continuous heating mode. All the courses of measurement were controlled and evaluated by means of the software Pyris 3.0. The wettability of Sn3.5Ag4Ti(Ce,Ga) solder was measured by use of equipment which scheme is shown in Fig. 1 . This equipment allows to measure the wetting kinetics at constant temperature. Measurement was performed in vacuum of 10 −4 Pa. The specimen is photographed in regular time intervals and after assessment the time dependence of the values of wetting angle is plotted. Specimens machined as shown in Fig. 2 were used for the shear strength measurement. The specimen consists of a ring 15 mm in diameter. The ring was made of Al 2 O 3 ceramics with 3 N purity. The metallic part of specimen was made of stainless steel type AISI 321, copper with 3 N purity and aluminium alloy type Al5Si. Specimens were inserted into graphite fixtures. Soldering was performed at 850 °C/10 min in a vacuum oven type PZ 810 in vacuum of 10 −4 Pa. Oven charge consisted of four specimens for each temperature. At soldering of specimens in the air at temperature 280 °C/1 min. Ultrasound equipment with 40 kHz frequency and 400 W output power was used for activation. The scheme and description of equipment is shown in Fig. 3 . The prepared test specimens were tested on the tearing machine type INSTRON with force recording. 3 Results and discussion 3.1 Microstructure, EDX analysis, RTG diffraction analysis and DSC analysis of Sn3.5Ag4Ti(Ce,Ga) solder Microstructure of Sn3.5Ag4Ti(Ce,Ga) solder is documented in Fig. 4 a. The solder is composed of tin eutectic matrix Sn3.5Ag, where large dark constituents of Ti–Sn intermetallic phases are irregularly distributed. The results of EDX analysis of chemical composition of solder are documented in Table 1 . Microstructure in Fig. 4 a was obtained by SEM. The shape of Ag 3 Sn phase in Fig. 4 a can be partially distorted after grinding and polishing. Dark zones (measurement point A1) are by 99 wt.% formed by titanium. The intermetallic Ti–Sn phase at measurement point A2 – Fig. 4 a, corresponds to composition of Ti 6 Sn 5 phase. Diffraction analysis performed on SnAg3.5Ag4Ti(Ce,Ga) solder in dimensions 10 × 10 mm was aimed at finding the presence of intermetallic phases containing titanium. The Ti 6 Sn 5 a Ti 3 Sn phases were observed. In works [15–17] there was also proved the presence of Ti 6 Sn 5 phase in the matrix of Sn3.5Ag4Ti(Ce,Ga) solder. Besides this phase, also presence of TiSn x phase was observed in the study [17] . The existence of TiSn x phase was for the first time published in [18] . In Sn–Ti system also Ti 5 Sn 3 , Ti 2 Sn and Ti 3 Sn phases may be formed, depending on the conditions of solder manufacture and/or soldered joints. In principle, each of these phases may be identified in Sn–Ti system under certain conditions. Fig. 4 b shows a real shape of Ag 3 Sn phase observed on SEM. As shown in Fig. 4 b, in the eutectic tin matrix of SnAg3.5Ag4Ti(Ce,Ga) solder, there are uniformly distributed fine acicular phases of Ag–Sn. More realistic observing the shape of Ag 3 Sn phase was achieved by deep etching of the tin matrix of solder. Distribution of Sn, Ag elements is proved by electron microprobe analysis (EPMA) in Fig. 4 c and d. Diffraction analysis has revealed the presence of Ag 3 Sn phase. Fig. 5 shows the DSC curve of Sn3.5Ag4Ti(Ce,Ga) solder. In accordance with binary phase diagram, the Sn–Ag eutectic has the melting point of 221 °C. The DSC analysis has revealed, that the solder starts to melt at the temperature of 220.5 °C. According to DSC curve in Fig. 5 the solder is molten at the temperature 224.5 °C. Increased melting point of Sn–Ag eutectic is caused by the presence of Ti in solder matrix. In previous study [17] , there was observed melting interval of Sn3.5Ag4Ti(Ce,Ga) solder in the range from 218 to 229 °C. Variable found results of melting interval with this solder were caused by a heterogeneous composition of the solder studied. Distribution of titanium in matrix is not homogeneous. Different samples of solder thus may provide different results. It should be also noted that in work [17] a higher heating rate, namely 10 °C/min was used in DSC analysis. 3.2 Wetting of Sn3.5Ag4Ti(Ce,Ga) solder on Al 2 O 3 ceramics Significance of active metal in solder was proved by comparison of wetting with active tin solder type Sn3.5Ag4Ti(Ce,Ga) and with a pure Sn solder without titanium content at temperature 850 °C ( Fig. 6 ). While pure Sn solder does not wet the surface of ceramics, the active solder with similar composition attains a good wettability of 53°. Similar results were achieved also at testing indium-based solder type In30Sn, which does not wet ceramic surface of Al 2 O 3 without presence of active titanium element ( Fig. 6 ). In order to determine the wettability of Sn3.5Ag4Ti(Ce,Ga) solder in dependence on temperature and wetting time, experiments were performed at temperatures 800, 850 and 900 °C ( Fig. 7 ). Wetting time for individual temperatures was increased within the range of 0, 5, 10, 15 and 20 min. At temperature 850 °C the wettability was determined also after 30 and 43 min. The best wettability of Sn3.5Ag4Ti(Ce,Ga) solder on A 2 O 3 ceramics was achieved at temperature 850 °C ( Θ = 46°). With increasing temperature up to 900 °C the wettability was slightly deteriorated. In previous work [19] , there was studied the wettability of Sn10Ag4Ti solder on A 2 O 3 ceramics in interval from 600 to 1100 °C. Wetting time was 20 and 60 min. For comparison of the attained results it can be stated that Sn10Ag4Ti solder attains the wetting angle 70° at parameters 850 °C/20 min. The Sn3.5Ag4Ti(Ce,Ga) solder shows at the same parameters (850 °C/20 min) the wetting angle of 52.5°. Comparison of results suggests that the addition of Ce element improves the wettability on A 2 O 3 ceramics. 3.3 Microstructure of transition zone of Sn3.5Ag4Ti(Ce,Ga) solder – Al 2 O 3 ceramics Fig. 8 shows a profile of droplet of Sn3.5Ag4Ti(Ce,Ga) solder on the substrate of Al 2 O 3 . Solder droplet was prepared at parameters 900 °C/16 min in vacuum of 10 −4 Pa. Figure shows that the wetting angle at given conditions attains the value of Θ = 57°. Microstructure of Sn3.5Ag4Ti(Ce,Ga) solder – Al 2 O 3 ceramics boundary is shown in Fig. 9 . A pronounced transition zone – reaction layer with average thickness of 2.6 μm was formed on the boundary. EDX analysis of chemical composition has shown that the reaction layer ( Fig. 9 ) contains: 5.35 wt.% Al; 37.33 wt.% Ti; 2.84 wt.% Ag and 54.48 wt.% Sn. The line course of concentration of individual elements is shown in Fig. 10 . 3.4 Measurement of shear strength of soldered joints fabricated with Sn3.5Ag4Ti(Ce,Ga) solder Based on the knowledge attained by wetting angle measurement, combined joints of ceramics/ceramics and ceramics/metal were fabricated in the conditions of high-temperature activation in vacuum of 10 −4 Pa at temperature 850 °C/10 min. For comparison, also joints fabricated in conditions of ultrasonic activation in the air at temperature 280 °C/1 min were used. The output of ultrasonic power was 400 W, and the ultrasound frequency was 40 kHz. The results of shear strength are shown in Fig. 11 . Fractographic analysis performed on fractured surfaces by SEM was aimed at the study of morphology. Fig. 12 a shows a fractured surface of specimen after shear strength test. Loss in cohesion strength occurred due to weakening of tin matrix, but also spots with fragmentation of reaction boundary were observed. In all cases ductile failure of specimens occurred. Fig. 12 a shows a cup morphology of reaction boundary ceramics/solder with fragments of particles from reaction layer of ceramics with orientation of ripples to the plane of shear strain. Decohesion has occurred also in the solubility range of metallic substrate. Fig. 12 b shows a manifestation of damage in solubility range of silumin with fragmented constituents of Ag–Al phase. Fig. 12 d characterizes the transition between the solubility range of steel and tin matrix. 4 Conclusions The work dealt with the study of wettability of Sn3.5Ag4Ti(Ce,Ga) solder on ceramic material of Al 2 O 3 . Microstructure of Sn3.5Ag4Ti(Ce,Ga) solder is composed of a tin matrix with non-uniformly distributed constituents of intermetallic Ti–Sn phases and uniformly distributed fine needles of a phase rich in silver. The diffraction analysis performed on the specimen of Sn3.5Ag4Ti(Ce,Ga) solder showed the presence of the following most probable phases: Ag 3 Sn, Ti 6 Sn 5 , Ti 3 Sn. DSC analysis allowed to determine the melting interval of Sn3.5Ag4Ti(Ce,Ga) solder. The solder with close-to-eutectic composition exerted the melting interval within the range from 220.5 to 224.5 °C. The partially dissolved Ti constituents present in solder matrix are not fully molten in the mentioned melting interval. In spite of the fact that Sn3.5Ag4Ti(Ce,Ga) solder contains just a small amount of active Ti element, it is capable to wet the surface of Al 2 O 3 ceramics. The best wettability of solder Θ = 46° was achieved at temperature 850 °C/43 min. At temperature increase up to 900 °C, the wettability was slightly deteriorated. It may be generally stated that the Sn3.5Ag4Ti(Ce,Ga) solder wets the Al 2 O 3 ceramics only with a great wetting angle. The shear strength of soldered joints of ceramics/ceramics and ceramics/metal fabricated with Sn3.5Ag4Ti(Ce,Ga) solder varied from 17 to 35 MPa. The shear strength of joints fabricated in vacuum was slightly higher than in the case of joints fabricated by use of power ultrasound. Acknowledgements The contribution was prepared with the support of VEGA 1/0211/11 project Development of lead-free solder for higher application temperatures and research of material solderability of metallic and ceramic materials. The authors of contribution thank Assoc. Prof. RNDr. Vladimír Labaš, PhD. for the DSC analysis of Sn3.5Ag4Ti(Ce,Ga) solder and they also thank Ing. Peter Žúbor, PhD. for the SEM analysis. They also thank Mrs. Bachratá from ÚMMS SAV Bratislava for performing the wettability measurements. References [1] A.P. Xian Joining of sialon ceramics by Sn-5 at% Ti–X ternary active solders J Mater Sci 25 1 1994 39 46 [2] N. Honglong G. Zhiting M. Jusheng H. Fuxiang Q. Zhiyong H. Zhongde Joining of sapphire and hot pressed Al 2 O 3 using Ag70.5Cu27.5Ti2 brazing filler metal Ceram Int 29 2003 689 694 [3] S.Y. Chang Y.T. Hung T.H. Chuang Joining alumina to inconel 600 and UMCo-50 superalloys using an Sn10Ag4Ti active filler metal J Mater Eng Perform 12 2003 123 127 [4] W.R. Smith Active solder joining of metals ceramics and composites Weld J 10 2001 30 35 [5] R.R. Kapoor T.W. Eagar Tin-based reactive solders for ceramic/metal joints Metall Trans 20B 1989 919 924 [6] G.L. Jian Wetting of ceramic materials by liquid silicon, aluminium and metallic melts containing titanium and other reactive elements Ceram Int 20 6 1994 391 412 [7] G. Yu N. Li Y. Li Y. Wang Study on surface reaction layer of titanium cast with Al 2 O 3 -based investment materials Adv Mater Res 97–101 2010 1029 1032 [8] F. Hillen D. Pickart-Castillo J.I. Rass E. Lugscheider Solder alloys and soldering processes for flux-free soldering of difficult to-wet materials Weld Cut 52 8 2000 E162 E165 [9] S. Kang J.H. Selverian Interactions between Ti and alumina-based ceramics J Mater Sci 27 1992 4536 4544 [10] Q. Gu Y.X. Wang Y.D. Cui X. Chen K. Tao Interfacial reaction of Ti and sapphire Wuli Xuebao/Acta Phys Sinica 45 5 1996 [11] J.J. Stephens F.M. Hosking T.J. Headley P.F. Hlava F.G. Yost Reaction layers and mechanisms for a Ti-activated braze on sapphire Metall Mater Trans A, Phys Metall Mater Sci 334 12 2003 2963 2972 [12] A. Xian Joining of sialon ceramics by Sn-5 at% Ti based ternary active solders J Mater Sci 32 1997 6387 6393 [13] Y. Jiuchun X. Zhiwu S. Lei M. Xing Y. Shiqin Ultrasonic assisted fabrication of particle reinforced bonds joining aluminum metal matrix composites Mater Des 32 2011 343 347 [14] R. Koleňák P. Žúbor Soldering of ceramic materials using ultrasonic energy Weld World 49 2005 546 553 [15] S.Y. Chang T.H. Chuang L.C. Tsao C.L. Yang Z.S. Yang Active soldering of ZnS–SiO 2 sputtering targets to copper backing plates using an Sn3.5Ag4Ti(Ce,Ga) filler metal J Mater Process Technol 202 2008 22 26 [16] S.Y. Chang T.H. Chuang C.L. Yang Low temperature bonding of alumina/alumina and alumina/copper in air using an Sn3.5Ag4Ti(Ce,Ga) filler J Electron Mater 36 9 2007 1193 1198 [17] Y.S. Chang C.L. Tsao J.M. Chiang N.C. Tung H.G. Pan H.T. Chuang Active soldering of indium tin oxide (ITO) with Cu in air using an Sn3.5Ag4Ti(Ce,Ga) filler J Mater Eng Perform 12 4 2003 383 389 [18] C. Kuper W. Peng A. Pisch F. Goesmann R. Schmidt-Fetzer Phase formation and reaction kinetics in the system Ti–Sn Z Metallkd 89 12 1998 855 862 [19] Y.H. Chai P.W. Weng H.T. Chuang Relationship between wettability and interfacial reaction for Sn10Ag4Ti on Al 2 O 3 and SiC Substrates Ceram Int 24 1998 273 279
更多查看译文
AI 理解论文
溯源树
样例
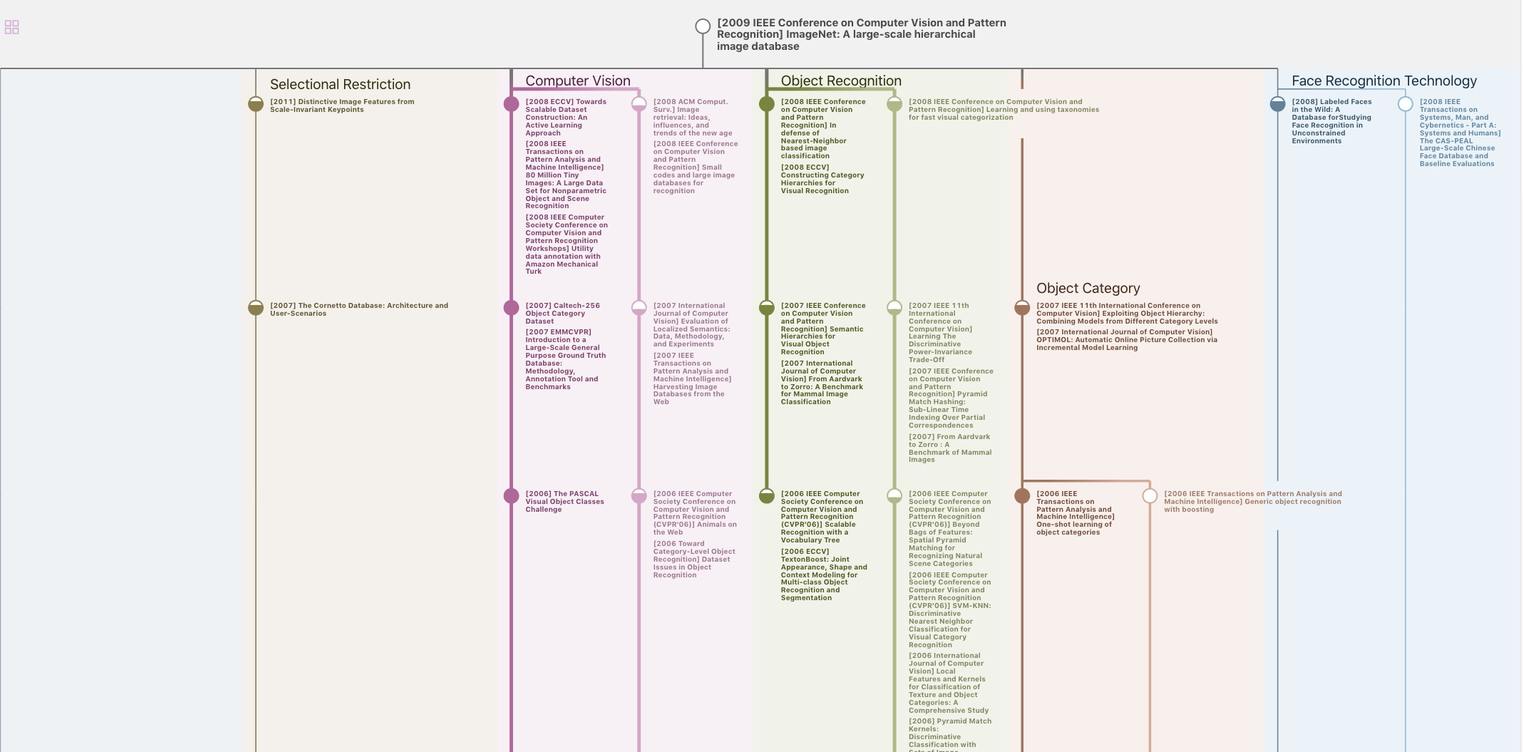
生成溯源树,研究论文发展脉络
Chat Paper
正在生成论文摘要