The growth of carbon coating layers on iron particles and the effect of alloying the iron with silicon
Journal of Alloys and Compounds(2011)
摘要
Magnetic fine particles of metallic Fe coated with graphitic carbon layers were synthesized by annealing Fe 2 O 3 particles with carbon powders at 1673 K in nitrogen atmosphere. For comparison, SiC was added to Fe 2 O 3 . X-ray diffraction measurement showed that the lattice constants of Fe changed depending on the Si contents. Mössbauer spectroscopy confirmed that Fe–Si alloys were formed by the Si addition and that the iron carbide disappeared. Electron microscope images revealed that the thickness of carbon coating layers increased from 24 nm to 36 nm as a result of the Si addition. Soaking tests showed that the corrosion resistance of the carbon-coated Fe particles was improved by the addition of Si. The results suggest that Si caused C to leave the Fe cores and move to the surface to form a carbon coating. Keywords Coating materials Iron particle Carbon coating Solid phase reduction Precipitation 1 Introduction Magnetic fine particles are used in a wide range of applications such as ferrofluids [1] , magnetic recording media [2] , magnetic toner [3] , magnetooptic devices [4] , and biomedical applications [5–8] . Iron oxide (γ-Fe 2 O 3 , Fe 3 O 4 ) particles are typically used in these applications because of their chemical stability. On the other hand, magnetic metal particles, such as Fe, Co, and Fe–Co alloys, have higher magnetizations than iron oxides. Magnetic metal particles can thus be expected to show improved performance in the applications because they can respond more sensitively to magnetic fields. However, metal particles corrode easily, resulting in the deterioration of their high magnetization property. To counter the corrosion problem of metal particles, carbon (C) coatings have been investigated. Metallic Co particles with C coatings were synthesized by the ion beam sputtering method [9] . The laser irradiation method was employed to coat Fe particles with C [10] . The C-encapsulated Fe particles were synthesized by arc discharge methods [11,12] . We have also developed an adequate method for mass-production so as to fabricate Fe fine particles encapsulated by C layers through the carbothermic reduction of iron oxide powders [13] . All these metallic particles were successfully coated, however, the mechanism of the coating was not studied in detail. Saito et al. suggested that the C layers on Fe particles grow following the “dissolution and precipitation” mechanism [11] . At first, C dissolves in liquid Fe at an elevated temperature by an arc discharge. Subsequently, graphitic C layers precipitate on the surface of Fe particles in the cooling process, because the solid solubility limit of C to Fe decrease extremely by 1000 K or less. It is similar to the growth of C nanotubes that uses metallic Fe particles as catalysts [14,15] . Carbon forms a solid solution with Fe, when it reaches the saturation point, and grows to form C nanotubes. The dissolution and precipitation of C is an important mechanism to grow C coating layers on the Fe particles. In this study, silicon (Si) is added in the carbothermic reduction process so as to examine whether the C coating layers is formed by the precipitation of C from Fe cores. The Si is known to show susceptibility toward graphitization in Fe–C–Si [16] . Here, we investigate the effect of Si on the growth of the C coating layers, and the growth mechanism is discussed. 2 Materials and methods Iron oxide (α-Fe 2 O 3 ), silicon carbide (SiC), and carbon black (C.B.) powders were used as the starting materials. Their diameters were 0.03, 0.01, and 0.02 μm, respectively. The samples were prepared by mixing the starting materials at a predetermined ratio, followed by annealing at 1673 K for 2 h in nitrogen atmosphere. The mixture ratios are shown in Table 1 . Magnetic properties were measured by using a vibrating sample magnetometer (VSM) at room temperature under a field of 1.6 MA/m. X-ray diffraction (XRD) measurements were carried out using a powder diffractometer (PANalytical, model X’pert Pro) to determine metallurgical phases and to estimate lattice constants. It used Cu Kα radiation under an applied power of 45 kV and 40 mA in 2 θ angular intervals of 30°–120°. The samples consisted of fcc γ-Fe and bcc α-Fe phases. The volume fraction of γ-Fe phase was obtained by the direct comparison method, using the following equations [17] , (1) I γ I α = R γ C γ R α C α (2) R α , γ = 1 v 2 F 2 p 1 + cos 2 2 θ sin 2 θ cos θ e − 2 M (3) C α + C γ = 1 where I α,γ is the peak strength of each phase, C α,γ is the volume fraction of each phase, v is the unit cell volume of each phase, F is the structure factor, p is the multiplicity factor, θ is the reflection angle of the peak analyzed, and e −2M is the Debye–Waller factor. The diffraction peaks corresponding to the planes of each phase were compared amongst each other, and then the average value of C γ in each sample was calculated. The analyzed peaks were as follows: (1 1 0) α , (2 0 0) α , (2 1 1) α , (1 1 1) γ , (2 0 0) γ , and (2 2 0) γ . A Mössbauer spectroscope with a 57 Co source was employed by using a conventional constant-acceleration method at room temperature in order to investigate the magnetic structures of the samples. On the Mössbauer measurement, the zero velocity is determined into the center of the spectrum of α-Fe. The microstructure of the samples was observed by using a transmission electron microscope (TEM) under an acceleration voltage of 200 kV. A scanning electron microscope (SEM) was used to observe the surface coating of the samples. The corrosion resistance of the samples was examined by a soaking test, in which the sample of 25 mg was soaked in a 1 ml phosphate buffered saline (PBS) for seven days at room temperature. After the magnetic separation of the samples and the solutions, the iron ion concentration in the solutions was analyzed at different soaking time by using an inductively coupled plasma (ICP) atomic emission spectrometer. In order to estimate the oxidation resistance of the samples, thermogravimetry measurement was conducted. The rate of temperature rise was set at 10 K/min and the samples were heated in air from room temperature to 1273 K. Gibbs free energies (Δ G ) for each reaction were calculated using the software HSC Chemistry® 6.0 (Outokumpu technology) to compare the stability of compounds, Fe 3 C, SiC, FeSi, and Fe 3 Si. 3 Results and discussion 3.1 Magnetic properties depending on Si contents The magnetic properties of the samples that added 0–4 mass% of Si were listed in Table 1 . The addition of Si results in an increase in saturation magnetization ( M s) and decrease in coercivities ( H c). The dependence of the magnetic properties suggests that Fe–Si alloys would be formed by the addition of SiC particles to the starting materials. The coercivities of Fe–1, 2, 3 wt%Si alloy were reported to decrease with Si contents [18] . 3.2 Study of phases by X-ray diffraction measurement The X-ray diffraction patterns of the samples S0–S4 were measured, and two phases of bcc (α-Fe) and fcc (γ-Fe) were detected. Each lattice parameter was obtained from the X-ray diffraction peaks ( Fig. 1 ). The lattice parameters of bcc and fcc phase become small with the Si additions. The reported lattice parameters of bcc Fe–Si alloys [19] , which are single crystals, are plotted in Fig. 1 . It is clear that the lattice parameters ( a bcc ) in the present study almost correspond to the reported ones. This suggests that bcc Fe–Si alloys are successfully formed according to the added composition of Si. The lattice parameters ( a fcc ) of the fcc phase decrease with the addition of Si. This would be concerning the formation of the fcc Fe–Si alloys. The peak strength of the fcc phase decreases with the Si additions ( Fig. 2 (a) ). The volume fractions of the fcc phase were estimated by the direct comparison method, using Eqs. (1)–(3) (see section 2 ). The results are represented by white circles in Fig. 2 (b). The volume fractions of the fcc phase were also estimated from Mössbauer spectrum ( Fig. 3 , Table 2 ), which are represented by black circles in Fig. 2 (b). The fcc phase decreases with the addition of Si, and disappear at 4 mass% of Si. The Fe–Si phase diagram shows that the fcc γ phase of Fe–Si exist in the Si density from 0 mass% to 3.8 mass% at 1185–1587 K [20] . Considering that the annealing temperature was 1673 K, the γ phase would be formed during cooling, and it would remain up to room temperature. The disappearance of the γ phase at 4 mass% of Si suggests that the fcc phase consists of Fe–Si alloys. Consequently, the added Si has uniformly dissolved into Fe, and Fe–Si alloys are synthesized in the present study. 3.3 Magnetic structure by Mössbauer spectrum analysis The Mössbauer spectra of the samples S0–S4 are shown in Fig. 3 . The results are summarized in Table 2 . As mentioned in the previous section, the fcc γ-Fe phase represented by a singlet pattern near zero velocity (blue line in Fig. 3 ) decreases with the addition of Si, and disappears at 4 mass% of Si. The sextets fitted by red line in Fig. 3 were assigned to the bcc α-Fe. They are the basic components in all samples. From the hyperfine fields “ H i ,” two types of the bcc phase, which are represented by “Fe–Si(I)” and “Fe–Si(II)” in Table 2 , are assigned in the sample S1–S4. The Fe–Si(I) fitted by green line in Fig. 3 is the component that Si occupies as one of the nearest neighboring sites (8 sites) of an Fe atom in the bcc structure. The Fe–Si(II) fitted by pink line in Fig. 3 is one that Si atoms occupy two of the nearest neighboring sites of an Fe atom in the bcc structure. Each H i of the Fe–Si(I) and Fe–Si(II) is 30.5–30.8 T and 27.2–27.5 T, respectively. The values are extremely similar to that of the reported one [21] , which was 0.917 ± 0.005 and 0.834 ± 0.005 times the value of α-Fe. The calculated volume fractions (“ A.R. ” in Table 2 ) of Fe–Si(I) and Fe–Si(II) in the sample S2 are also similar to the calculated probability of each type of alloy in Fe–2.2mass%Si [21] . The appearance of these Fe–Si components suggests that Si dissolves in the bcc Fe phase. Iron carbide (Fe 3 C), which is fitted by brown line in Fig. 3 (a), appears only in sample S0. The Fe 3 C phase disappears by the addition of more than 1 mass% of Si. This means that Si easily alloys with Fe, and facilitates the decomposition of Fe–C. 3.4 Change in C coating layers in morphologies Fig. 4 shows the TEM images of Fe particles encapsulated by C in samples S0–S4. The particle sizes of all samples are ∼700 nm in diameter. The surface coating layers were assigned to graphitic C in the previous study [22] . The magnified images (right-side images) show that the C coating layers become thick as a result of the Si addition. The thickness of the C coating layers was measured for about 40 particles of each sample. The averaged thicknesses increase from 24 nm to 36 nm as shown in Fig. 5 . It is considered that the addition of Si helps in precipitating C from the Fe cores, so that the graphitic C coating layers become thick. Fig. 6 shows the backscattered electron images of samples S0 and S3. The surface coating of the sample S0 is inhomogeneous shown as the two-colored surface in Fig. 6 (a). The white and gray area would represent bare Fe and C coating layers, respectively. Fig. 6 (b) reveals that C coating layers encapsulate Fe homogeneously. The addition of Si is effective in creating thick coating layers and homogeneous coatings. 3.5 Corrosion resistance In order to confirm homogeneous coatings, the corrosion resistance of samples S0–S4 was studied ( Fig. 7 ). At first, Fe ion concentrations in the PBS buffer were measured after the soaking test, as shown in Fig. 7 (a). The addition of Si clearly controls the elution of Fe ion to 1 ppm or less, which corresponds to10% or less of the Fe ion concentration eluted from the sample S0. Next, TG analysis was conducted as shown in Fig. 7 (b). The samples were heated in air, and the weight changes were measured. In the TG curves, increase in the weight represents the oxidation of the samples. Carbonyl Fe powders as a reference begins to oxidize from 473 K. On the other hand, the oxidation beginning temperature is ∼673 K and 800 K in samples S0 and S4, respectively. The samples S0 and S4 exhibit excellent oxidation resistance, which is due to the C coating layers. Sample S4 has a highest oxidation beginning temperature. This suggests that Fe particles in S4 are sufficiently encapsulated with C. 3.6 Calculation of free energies Gibbs free energies (Δ G ) for each compound were calculated as shown in Fig. 8 . The ΔG for FeSi and Fe 3 Si is smaller than that of Fe 3 C. This means that Fe alloys stably with Si and not C. Fig. 8 also shows that FeSi and Fe 3 Si is stable compared with SiC. This suggests that the dissolution of Si in Fe is more stable than that in C. These results support that when the mixture of Fe, C, and Si is reacted, the formation of Fe–Si alloys is the most stable. As mentioned above, the addition of Si results in the decomposition of Fe 3 C ( Table 2 ) and the formation of sufficient C encapsulation ( Figs. 4 and 6 ). The growth mechanism of the C coating layers is shown in Fig. 9 . When Si is added into Fe–C particles, Si easily dissolves into Fe so that C leave the Fe cores to the surface, resulting in C coating layers. 4 Conclusion Silicon carbide was added in the carbothermic reduction process, and the growth mechanism of the C coating layers on Fe particles was studied. Silicon successfully dissolved in Fe particles, so that the generation of Fe 3 C was controlled. And then, the growth of the C coating layers was facilitated. Thermodynamic consideration suggests that Si helps in the decomposition of Fe–C. Therefore, the C coating layers result from the precipitation of C from Fe core particles. This supports the assumption that the growth of C coating layers on iron particles follow the “dissolution and precipitation model”. Moreover, it is clear that the carbothermic reduction method in the present work can control the C coating layers by Si addition. This method is expected to contribute to industrialization of magnetic metal particles. References [1] K. Raj R. Moskowitz J. Magn. Magn. Mater. 85 1990 233 245 [2] M.P. Sharrock IEEE Trans. Magn. MAG-25 1989 4374 4389 [3] M.E. Mchenry S.A. Majetich J.O. Artman M. Degraef S.W. Staley Phys. Rev. B 49 1994 11358 11363 [4] T. Gasche M.S.S. Brooks B. Johansson Phys. Rev. B 53 1996 296 301 [5] R. Semelka T. Helmberger Radiology 218 2001 27 38 [6] R.S. Molday D. Mackenzie J. Immunol. Methods 52 1982 353 367 [7] S. Goodwin C. Peterson C. Hoh C. Bittner J. Magn. Magn. Mater. 194 1999 132 139 [8] R. Hiergeist W. Andra N. Buske R. Hergt I. Hilger U. Richter W. Kaiser J. Magn. Magn. Mater. 201 1999 420 422 [9] T. Hayashi S. Hirono M. Tomita S. Umemura Nature 381 1996 772 774 [10] L. Díaz M. Santos C. Ballesteros M. Maryško J. Pola J. Mater. Chem. 15 2005 4311 4317 [11] Y. Saito T. Yoshikawa M. Okuda N. Fujimoto S. Yamamuro K. Wakoh K. Sumiyama K. Suzuki A. Kasuya Y. Nishina Chem. Phys. Lett. 212 1993 379 383 [12] X.L. Dong Z.D. Zhang S.R. Jin B.H. Kim J. Appl. Phys. 86 1999 6701 6706 [13] H. Tokoro S. Fujii T. Oku J. Mater. Chem. 14 2004 253 257 [14] B.C. Satishkumar A. Govindaraj R. Sen C.N.R. Rao Chem. Phys. Lett. 293 1998 47 52 [15] H. Yan Q. Li J. Zhang Z. Liu Carbon 40 2002 2693 2698 [16] A.A. Zhukov V.I. Savulyak T.F. Arkhipova Met. Sci. Heat Treat. 42 2000 47 52 [17] B.D. Cullity Elements of X-ray Diffraction 16th ed. 2004 Agune Syoufusya Tokyo [18] G.F. Hanejko W.G. Ellis J.T. Hale Advances in Powder Metallurgy & Particulate Materials 2 1998 8.13-8.26 [19] M. Polcarová K. Godwod J. Bak-misiuk S. Kadečková J. Brádler Phys. Stat. Sol. (a) 106 1998 17 23 [20] T.B. Massalski J. Murray L. Bennett H. Baker Binary Alloy Phase Diagrams 1986 American Society for Metals Ohio [21] M.B. Stearns Phys. Rev. 129 1963 1136 1144 [22] H. Tokoro S. Fujii S. Muto S. Nasu J. Appl. Phys. 99 2006 08Q512-1-3
更多查看译文
关键词
Coating materials,Iron particle,Carbon coating,Solid phase reduction,Precipitation
AI 理解论文
溯源树
样例
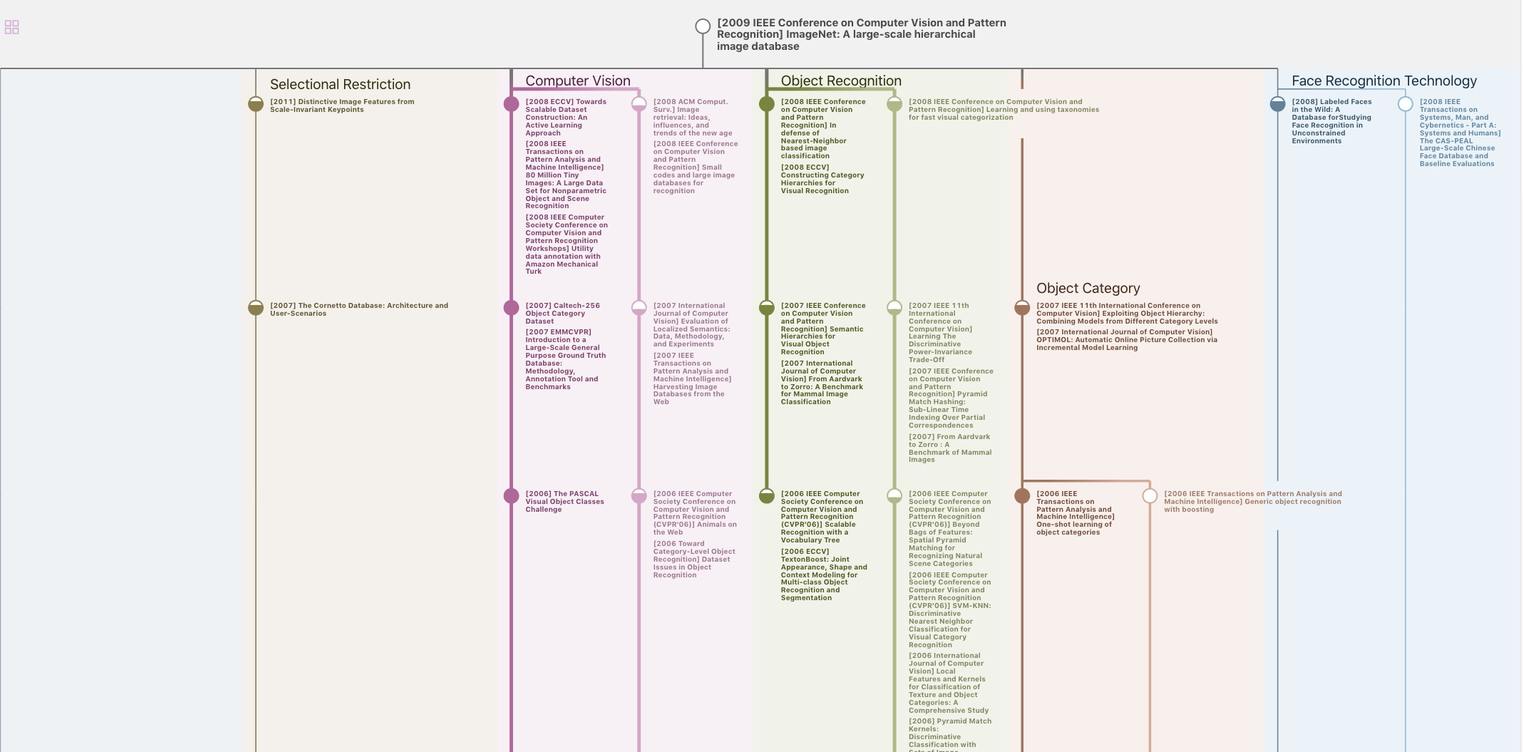
生成溯源树,研究论文发展脉络
Chat Paper
正在生成论文摘要