Alloy design for Al addition on microstructure and mechanical properties of Ni3(Si,Ti) alloy
Materials Science and Engineering: A(2011)
摘要
The effect of Al addition on the microstructure and tensile properties of Ni 3 (Si,Ti) alloys with an L1 2 ordered structure, which were fabricated through thermomechanical processing from arc-melted ingots, was investigated. Al was added to a Ni 3 (Si,Ti) alloy by using two methods such that Al substituted for (1) only Ti and (2) both Ni and Ti along a Ni 3 (Si,Ti)–Ni 3 Al pseudo-binary line. In the case of the alloys prepared by the former method, the addition of more than 4 at.% Al resulted in a two-phase microstructure consisting of disordered fcc Ni solid solution dispersions in the L1 2 matrix, while in the case of the alloys prepared by the latter method, the addition of 4 at.% Al retained the L1 2 single-phase microstructure. In the case of the 4 at.% Al-added alloys, the room-temperature tensile properties were similar and independent of the alloying methods, whereas the high-temperature yield stress was higher in the alloys prepared by the latter method than in the case of the alloys prepared by the former method. These results suggest that a single-phase microstructure consisting of an entire L1 2 structure is favorable for obtaining high-temperature tensile properties. Keywords Mechanical characterization Intermetallics Casting Thermomechanical processing Tensile properties 1 Introduction An L1 2 -type Ni 3 (Si,Ti) alloy, which has been developed by adding Ti to Ni 3 Si [1] , possesses many attractive properties such as those of high-temperature structural materials. For example, the Ni 3 (Si,Ti) alloy shows a positive temperature dependence of yield strength and exhibits higher strength and peak temperature in the strength versus temperature curve than Ni 3 Si [1] . Further, the relatively low density (∼8 g/mm 3 ) and the good corrosion resistance of the Ni 3 (Si,Ti) alloy are favorable properties for structural materials [2] . In addition, a high tensile ductility over a wide range of temperatures due to the prevention of the propensity for an intergranular fracture is a notable feature of the Ni 3 (Si,Ti) alloy [1] . Such high tensile ductility of the Ni 3 (Si,Ti) alloy is noteworthy because most intermetallic alloys have limited ductility, particularly at low temperatures. Recently, heavily cold-rolled thin sheets and foils of the Ni 3 (Si,Ti) alloy were fabricated from conventional polycrystalline ingots via a repeated warm-rolling and annealing process [3] . The Ni 3 (Si,Ti) thin sheet annealed at an intermediate temperature (e.g., around 900 K) exhibited an extremely high tensile strength and yield strength (more than 2 GPa) with a reasonable fracture strain at room temperature and was superior to the commercial nickel alloys and stainless steels below 873 K [3] . However, the tensile strength and the elongation of the annealed Ni 3 (Si,Ti) thin sheets were found to rapidly decrease at temperatures beyond 873 K with an increase in the temperature, and therefore, the improvement of the high-temperature mechanical properties is considerably desired. Thus far, the improvement of high-temperature tensile properties for the Ni 3 (Si,Ti) alloy has been attempted by means of an alloying technique [4–6] . Transition metals, Hf, Nb, Cr, Fe and Mn, were added to the Ni 3 (Si,Ti) alloy at 1 at.% level below their solubility limits [4] . However, their addition was less effective in improving the high-temperature tensile properties of the Ni 3 (Si,Ti) alloy. Further, 2 at.% of Al, Cr, and Mo metals was added to the Ni 3 (Si,Ti) alloy [6] . The 2 at.% addition of Al was below the solubility limit in the Ni 3 (Si,Ti) matrix; therefore, the new alloy retained the L1 2 single-phase microstructure. On the other hand, the 2 at.% addition of Cr was beyond the solubility limit in the Ni 3 (Si,Ti) matrix and consequently resulted in a two-phase microstructure consisting of disordered fcc Ni solid solution dispersions in the L1 2 matrix. It was found that the addition of Al as well as Cr was slightly effective in improving both high-temperature ductility and oxidation resistance [6] . In the present study, we selected Al as an alloying element for the Ni 3 (Si,Ti) alloy because addition of Al is expected to yield a number of microstructural, mechanical, engineering, and economic advantages such as low density, low cost, the use of a ubiquitous element, high oxidation resistance, high corrosion resistance, and large solubility in the L1 2 matrix. In order to make Al largely soluble in the Ni 3 (Si,Ti) matrix, various alloying procedures were taken into consideration. In this study, the microstructure, cold workability, and high-temperature tensile properties of the Al-added Ni 3 (Si,Ti) alloys were investigated, and the alloy composition and the microstructure preferable for high-temperature structural materials were suggested. 2 Experimental procedure The base composition of the Ni 3 (Si,Ti) alloy used in this study was 79.5 at.% Ni, 11.0 at.% Si, and 9.5 at.% Ti doped with 50 wt ppm B. Boron doping of the Ni 3 (Si,Ti) alloy is necessary to suppress the intergranular fracture due to environmental embrittlement at room temperature [7] . The quaternary element Al was added to the base alloy composition by using two methods: (1) Al substituted only for Ti and (2) Al substituted both for Ni and Ti. The samples prepared by the two methods are hereafter referred to as groups A and B, respectively ( Table 1 ). In the case of group A, the addition of 2, 4, 6 and 8 at.% Al content was designed to reduce the amount of Ti that was harmful for the oxidation resistance of the Ni 3 (Si,Ti) alloy [8] . In the case of group B, the addition of 4 and 8 at.% Al content was designed to reduce the amount of Ni and Ti, forming a continuous L1 2 solid solution along the pseudo-binary Ni 3 (Si,Ti)–Ni 3 Al line, as shown in Fig. 1 . In the alloys of group B, an increased amount of 500 wt ppm B was added because a higher boron content was required in Ni 3 Al than in Ni 3 (Si,Ti) to suppress the intergranular fracture [9] . Alloy ingots were prepared by non-consumable arc melting in an argon gas atmosphere on a copper hearth. All the ingots were homogenized at 1323 K for 48 h in a vacuum and then cut into several plates with a thickness of approximately 10 mm using an electro-discharge machine (EDM). These plates were warm-rolled at 573 K and then annealed at 1273 K for 5 h in a vacuum. This procedure was repeated until the thickness of the plate became 2 mm. The sheets were finally annealed at 1273 K for 1 h in a vacuum before cold rolling. Cold rolling was conducted without intermediate annealing up to 90% reduction in thickness. Reduction in sheet thickness per rolling pass was approximately 0.1 mm both for warm and cold rolling. The thickness of the obtained cold-rolled sheets was approximately 0.2 mm. Microstructural observations were carried out by using a scanning electron microscope (SEM; JEOL, JSM-5600 operating at 15 kV) and a transmission electron microscope (TEM; JEOL, JEM-2000FX operating at 200 kV). Further, X-ray diffraction (XRD; RIGAKU, RINT2500HK) was performed to determine constituent phases and second-phase dispersions by using Ni-filtrated Cu Kα radiation at an accelerated voltage of 30 kV mostly with a scan speed of 1°. In the XRD measurement, bulk materials of the alloys were used as the specimens. Dog-bone-shaped tensile test pieces with a length of 10 mm, width of 4 mm, and thickness of 0.2 mm were prepared by using the EDM. Room-temperature tensile tests were carried out in air by using the cold-rolled and fully recrystallized (1173 K; 1 h) specimens. High-temperature tensile tests were conducted in a vacuum in a temperature range of room temperature to 973 K by using the fully recrystallized specimens. A strain rate of 8.4 × 10 −5 s −1 was used in both room-temperature and high-temperature tensile tests. After the tensile tests, the fracture surfaces of the test pieces were examined by using an SEM. 3 Results and discussions 3.1 Microstructure Fig. 2 shows the SEM microstructures of the alloys in group A (i.e., alloys #A2, #A4, #A6 and #A8) after homogenization at 1323 K. Alloy #A2 as well as the base alloy (not shown here) showed an L1 2 single-phase microstructure, indicating that 2 at.% Al is soluble in the L1 2 matrix. On the other hand, the other alloys (i.e., alloys #A4, #A6 and #A8) exhibited a two-phase microstructure containing second-phase dispersions. At Al contents above 2 at.%, the volume fraction of the second-phase dispersions increased with an increase in the Al content. Bimodal microstructures were more or less observed in the alloys with a two-phase microstructure: eutectic-like two-phase microstructures consisting of L1 2 and Al (fcc) phases were mixed with a featureless L1 2 single-phase region. This eutectic-like microstructural feature may be explained such that the Al phase with Ni-rich content is formed as a primary phase and present in the dendritic core region during solidification and remains as a two-phase microstructure after homogenization. Fig. 3 shows the XRD profiles of alloy #A4 with a two-phase microstructure, together with the alloys with a single-phase microstructure (i.e., the base alloy and alloy #B4 (see later)). The XRD profiles of all alloys shown in Fig. 3 were basically identical to each other, although the relative peak intensities of each diffraction were slightly different among the shown alloys because of the crystallographic textures of these alloys. The observed reflection peaks could be indexed as an L1 2 phase or an A1 phase, and no other peaks were identified in all the alloys. However, the reflection peaks from the L1 2 and A1 phases were not resolved for alloy #A4 with a two-phase microstructure. This result reveals that the lattice parameters of the L1 2 and A1 phases were almost identical to each other. The lattice parameters of the L1 2 phase or the A1 phase determined from the XRD data were 0.3549 nm for the base alloy and 0.3543 nm for alloys #A4 and #B4. Fig. 4 shows a typical TEM micrograph of alloy #A4 with a two-phase microstructure. The selected-area diffraction pattern (SADP) was obtained from the region containing the second-phase dispersions surrounded by a matrix. There were no other diffraction spots except for the fundamental and ordered diffraction spots arising from an L1 2 structure. This result indicates that the observed second-phase dispersions were fcc (A1 structure) Ni solid solution phase. Further, it is noted that the crystallographic relationship between the fcc Ni solid solution dispersions and the L1 2 matrix was a cube-on-cube relationship although the morphology of the present dispersions was irregularly shaped. However, concerning the detailed microstructure, much more microstructural observations and structural analysis will be required. Fig. 5 shows the SEM microstructures for the alloys in group B after a homogenization heat treatment at 1323 K. In contrast to alloy #A4 ( Fig. 2 b), alloy #B4 exhibited an L1 2 single-phase microstructure although the aluminum content was the same for both alloys. Further, it is noted that alloy #B8 showed a smaller volume fraction of the fcc Ni solid solution than alloy #A8 although the aluminum content was the same for both alloys. These results clearly indicate that the microstructure of the Ni 3 (Si,Ti) alloys depends on the alloying method used. Fig. 6 shows the typical recrystallized microstructures after the annealing of the cold-rolled sheets. It was again confirmed in the recrystallized alloys that alloys #A4 and #B4 showed a two-phase and a single-phase microstructure, respectively. Grain sizes were smaller in the two-phase microstructure (8.0 μm for alloy #A4) than in the single-phase microstructure (10 and 15 μm for the base alloy and alloy #B4) because the suppression of grain growth by the second-phase dispersions occurred in the former microstructure. 3.2 Rolling workability The homogenized alloys were repeatedly warm-rolled and annealed. All the alloys in group A were readily warm-rolled irrespective of the Al content. Alloy #B4 was also warm-rolled without any cracking and fracturing. However, alloy #B8 cracked and failed during the warm-rolling process. In this case, most of the cracks initiated and propagated along the grain boundaries. Moreover, all the alloys in group A and alloy #B4 were heavily cold-rolled up to a 90% reduction in thickness. Although Ti is a key element that ensures the low-temperature tensile ductility of the Ni 3 (Si,Ti) alloys [1] , the rolling workability of the alloys in group A was not adversely affected by the decrease in the Ti content. It has been reported that a remarkable low temperature ductility appeared above the Ti content of 9.0 at.% [1] . However, the Ti content of the present Al-added Ni 3 (Si,Ti) alloys is less than 9.0 at.% (see Table 1 ). In this case, the existence of the disordered Ni solid solution dispersions, which were more deformable than the ordered L1 2 matrix, was assumed to compensate for the reduced ductility due to the reduction of the Ti content in the L1 2 matrix. The Vickers hardness of the homogenized alloys before warm-rolling (i.e., unrolled alloys) is listed in Table 1 . The hardness of alloys in group B was slightly higher than that of alloys in group A possibly due to the hardened L1 2 matrix by soluble aluminum for alloys in group B. Therefore, the reduced workability of alloy #B8 is attributed to the hardened matrix with a high volume fraction of the L1 2 phase. Further, it may be suggested that the low-temperature grain boundary cohesion was reduced by the increased Al content [10] , and consequently, poor workability was caused. 3.3 Tensile properties Fig. 7 shows the nominal stress versus nominal strain curves for the 90% cold-rolled and recrystallized sheets of alloys #A4, #A8 and #B4. The data for the base alloy sheet [3] is also included in this figure as reference. The cold-rolled sheets of all the alloys shown in this figure showed a high fracture strength of more than 2 GPa but a limited tensile elongation irrespective of the microstructure. From Fig. 7 , it appears that the tensile strength and the elongation of the recrystallized sheets of these alloys were basically identical to one another. Here, it is noted that the presence of Ni solid solution dispersions with a disordered fcc structure does not considerably affect the room-temperature tensile properties of the Ni 3 (Si,Ti) sheets. The co-existed Ni solid solution (fcc) phase with the L1 2 phase seems to be not so much soft (weak) at least at room temperature, whereas it becomes much more softened at high temperature compared with the L1 2 phase, as described later. For the present L1 2 /fcc two-phase microstructure, an interface strengthening may somewhat operate at room temperature. Fig. 8 shows the changes in the tensile strength, yield stress (0.2% proof stress) and tensile elongation with testing temperature for alloys #A4 and #B4, and the base alloy sheets [3] . In general, the tensile strength of the three alloys monotonously decreased with an increase in the testing temperature. On the other hand, the yield stress showed a peak at around 773 K. It is well known that Ni 3 (Si,Ti) shows a positive temperature dependence of yield stress (i.e., strength anomaly) [11] , which is caused by the Kear–Wilsdorf (K–W) locking. The strength anomaly was remarkable for the alloys with an L1 2 single-phase microstructure while it was reduced for alloy #A4 with a two-phase microstructure. It has been reported that the strength anomaly for Ni 3 Al and Ni 3 Ga with an L1 2 structure is remarkably affected by non-stoichiometry (i.e., chemical composition of the L1 2 phase) [12] . In these alloys, Al- or Ga-rich deviations from stoichiometry result in more significant effect on the strength anomaly than Ni-rich deviation. In other words, the strength anomaly of the L1 2 phase with Ni-poor composition is significant than that with Ni-rich composition. In the present Ni 3 (Si,Ti) alloy, the existence of Ni solid solution phase suggests that the L1 2 matrix has relatively Ni-poor composition, by which the strength anomaly can be strong. In the case of alloy #A4 with relatively high volume fraction of the Ni solid solution phase, the reduction of the strength anomaly is suggested to be the fact that the effect due to the presence of Ni solid solution was more remarkable than the effect due to the composition deviation in the L1 2 matrix. The tensile elongation (fracture strain) at room-temperature is slightly higher in the base alloy than in alloys #A4 and #B4. One of the reasons explaining this result may be the reduction of the deformability of the L1 2 phase due to the reduced content of Ti. As described in Section 3.2 , Ti is a key element for the Ni 3 (Si,Ti) alloy to ensure ductility especially at room temperature; therefore, alloys #A4 and #B4 with less Ti content shows lower elongation than the base alloy. The tensile elongation of the base alloy steadily decreased with an increase in the temperature. In contrast, the tensile elongation of alloy #A4 with a two-phase microstructure was maintained at a high value until 873 K; it rapidly increased beyond 873 K and then reached approximately 70% at 973 K. The improvement of the tensile elongation at a high temperature is attributed to the existence of the ductile Ni solid solution dispersions. Further, the large tensile elongation observed at 973 K may be due to the dynamic recrystallization that was promoted by the presence of Ni solid solution dispersions in the L1 2 matrix [13] . There is a possibility that the Ni solid solution (A1) phase is preferentially deformed at high temperature, resulting in high density of dislocation in this phase and/or in the vicinity of interfaces between A1 and L1 2 phases. It is suggested that recrystallization occurs preferably in these highly strained regions (i.e., inhomogeneous microstructure). The tensile elongation of alloy #B4 with an L1 2 single-phase microstructure also steadily decreased with an increase in temperature, but the decrease in the tensile elongation was apparently smaller in alloy #B4 than in the base alloy. This indicates that the L1 2 single-phase microstructure containing Al is effective in improving the high-temperature ductility of the Ni 3 (Si,Ti) alloy without reducing the high-temperature yield stress. Therefore, the two-phase microstructure containing disordered fcc Ni solid solution dispersions in the ordered L1 2 matrix is useful for improving the high-temperature ductility of the alloy but is unfavorable for enhancing the high-temperature yield stress. Fig. 9 shows the SEM fractography of alloys #A4 and #B4 and the base alloy sheets tensile-deformed at room temperature and 873 K. High-temperature tensile tests were conducted using fully recrystallized specimens whose microstructures are shown in Fig. 6 . In the case of the base alloy, the transgranular fracture mode with ductile dimple patterns observed at room temperature ( Fig. 9 c) changed to a brittle intergranular fracture as the testing temperature increased ( Fig. 9 f). On the other hand, alloy #A4 with a two-phase microstructure showed ductile dimple patterns at a high temperature of 873 K ( Fig. 9 d) as well as at room temperature ( Fig. 9 a). Therefore, the observed high tensile ductility at a high temperature for alloy #A4 is attributed to the suppression of the propensity to intergranular fracture due to the presence of the Ni solid solution dispersions. The Ni solid solution dispersion with disordered fcc structure is considered to be more deformable than the ordered L1 2 matrix especially at high temperatures, as mentioned above. Therefore, it is likely that deformation preferentially occurs in the Ni solid solution dispersions, leading to reduction of stress concentration at L1 2 grain boundaries. In the case of alloy #B4 with the same single-phase microstructure as the base alloy, the fracture surface showed a ductile dimple pattern not only at room temperature ( Fig. 9 b) but also at a high temperature ( Fig. 9 e) in contrast to the behavior of the base alloy. It may be suggested that the high-temperature grain boundary cohesion of Ni 3 (Si,Ti) was enhanced by the addition of Al. It is known that some L1 2 compounds, including Ni 3 (Si,Ti) [14,15] , are embrittled at a high temperature by atmospheric oxygen. Combined with the boron condensation at grain boundaries, the invaded or residual oxygen has been reported to reduce the high-temperature grain boundary cohesion, resulting in an intergranular fracture [14,15] . This embrittlement is assumed to occur at a very low pressure of oxygen (e.g., at a low vacuum degree). It may be anticipated that Al or Cr having a strong affinity to oxygen traps the invaded oxygen and reduces its harmful action, resulting in the suppression of an intergranular fracture. In order to clarify the beneficial effect of Al on the high-temperature tensile ductility of the Ni 3 (Si,Ti) alloy, further studies are required. 3.4 Alloy design for Al-added Ni 3 (Si,Ti) alloy It was recognized from the present study that the addition of Al to Ni 3 (Si,Ti) was a useful method for improving the high-temperature tensile ductility of the alloy ( Fig. 8 c). When Al was added to Ni 3 (Si,Ti) in such a manner that Al substituted only for Ti, an L1 2 single-phase microstructure changed into a two-phase microstructure containing Ni solid solution phase dispersions, resulting in the reduction of the high-temperature yield stress. On the other hand, when Al was added in such a way that it substituted both for Ni and Ti along the pseudo-binary Ni 3 (Si,Ti)–Ni 3 Al, an L1 2 single-phase microstructure was retained at least up to 4 at.% Al, and favorable high-temperature tensile properties were obtained. With respect to a continuous L1 2 solid solution, it has been reported that among L1 2 Ni 3 B (where B is b-sub group element)-ordered alloys, Ni 3 Al, Ni 3 Ga, Ni 3 Ge, and Ni 3 Si form a tetrahedron of the continuous solid solution [16] . In order to further add Al to Ni 3 (Si,Ti), whether or not, or what amount of a continuous L1 2 solid solution is formed between Ni 3 (Si,Ti) and Ni 3 Al should be clarified. 4 Conclusion The effect of Al addition on the microstructure and tensile properties of the L1 2 -type Ni 3 (Si,Ti) alloys was investigated. The following results were obtained from the present study: 1. The alloys prepared by substituting only Ti with Al had a two-phase microstructure containing disordered fcc Ni solid solution dispersions in the L1 2 matrix when more than 4 at.% of Al was added to the Ni 3 (Si,Ti) alloy. On the other hand, the 4 at.% Al-added alloy prepared by substituting both Ni and Ti with Al exhibited an L1 2 single-phase microstructure. 2. The Al-added Ni 3 (Si,Ti) alloys prepared in this study were capable of cold-rolling into thin sheets with a thickness of 0.2 mm except the 8 at.% Al-added alloy prepared by substituting both Ni and Ti with Al. 3. In the case of the thermomechanically processed 4 at.% Al alloys, the high-temperature yield stress was higher in the alloy prepared by substituting both Ni and Ti with Al than in the alloy prepared by substituting only Ti with Al. 4. With respect to both the high-temperature yield stress and the high-temperature tensile elongation, the alloys with a single-phase microstructure consisting of an entire L1 2 structure were suggested to be favorable as high-temperature structural materials. Acknowledgments This work was supported in part by a Grant-in-Aid for Scientific Research from the Ministry of Education, Culture, Sports, Science and Technology, by Research for Promoting Technological Seeds from the Japan Science and Technology Agency, and by the Amada Foundation for Metal Work Technology. References [1] T. Takasugi M. Nagashima O. Izumi Acta Metall. Mater. 38 1990 747 755 [2] T. Takasugi D. Shindo O. Izumi M. Hirabayashi Acta Metall. Mater. 38 1990 739 745 [3] Y. Kaneno T. Myoki T. Takasugi Int. J. Mater. Res. 99 2008 1229 1236 [4] T. Takasugi M. Yoshida J. Mater. Sci. 26 1991 3517 3525 [5] T. Takasugi Intermetallics 8 2000 575 584 [6] Y. Fujimoto Y. Kaneno T. Takasugi Mater. Res. Soc. Symp. Proc. 1128 2009 245 [7] T. Takasugi M. Yoshida J. Mater. Sci. 26 1991 3032 3040 [8] T. Takasugi H. Kawai Y. Kaneno Mater. Sci. Technol. 17 2001 671 680 [9] C.T. Liu C.L. White J.A. Horton Acta Metall. 33 1985 213 229 [10] T. Takasugi O. Izumi Acta Metall. 33 1985 1247 1258 [11] T. Takasugi M. Yoshida Philos. Mag. A 67 1993 447 462 [12] O. Noguchi Y. Oya T. Suzuki Metall. Trans. 12A 1981 1647 1653 [13] T. Takasugi S. Rikukawa S. Hanada Acta Metall. Mater. 40 1992 1895 1906 [14] C.T. Liu C.L. White J.A. Horton Acta Metall. 35 1987 643 649 [15] T. Takasugi H. Suenaga O. Izumi J. Mater. Sci. 26 1991 1179 1186 [16] Y. Oya S. Ochiai T. Shinoda T. Suzuki Z. Metallkd. 75 1984 53 57
更多查看译文
关键词
Mechanical characterization,Intermetallics,Casting,Thermomechanical processing,Tensile properties
AI 理解论文
溯源树
样例
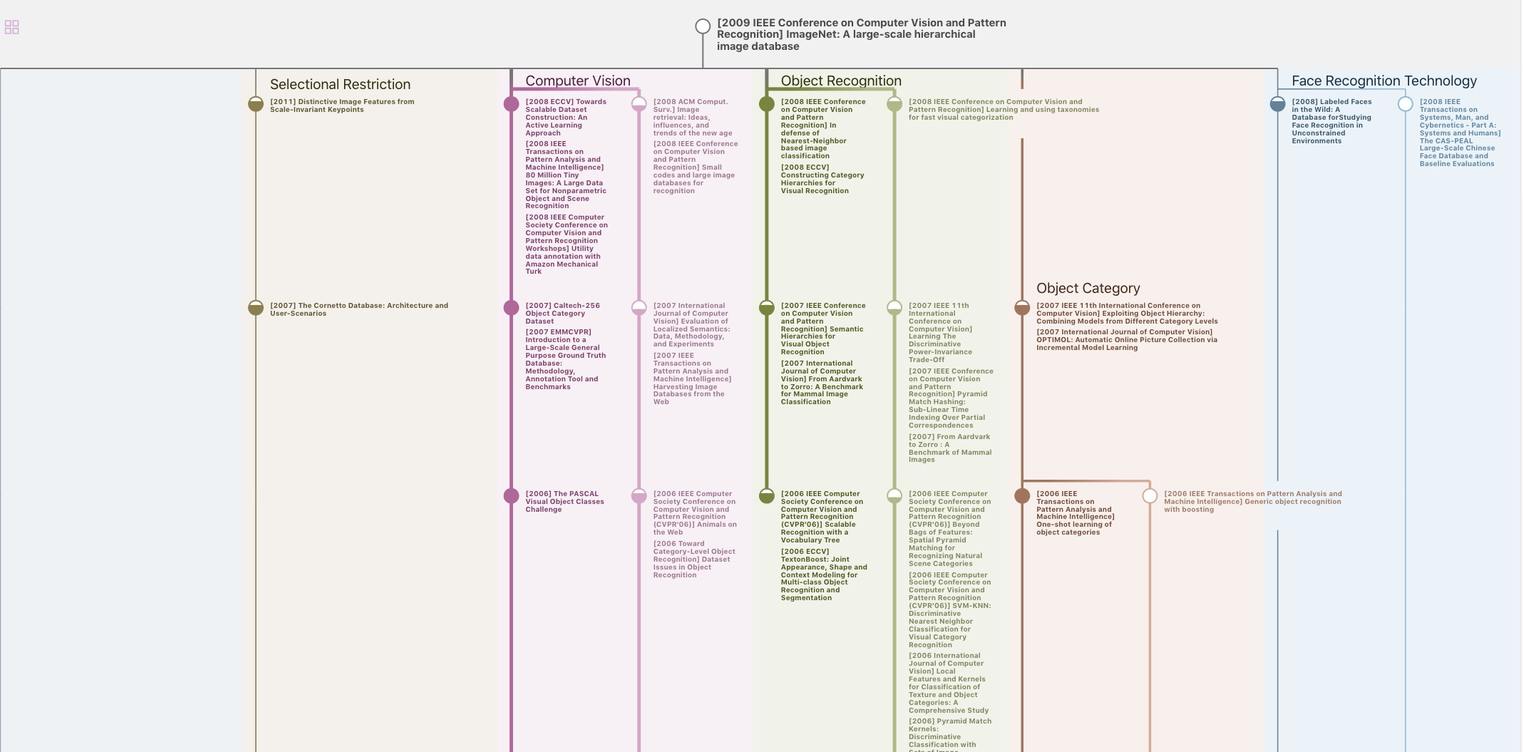
生成溯源树,研究论文发展脉络
Chat Paper
正在生成论文摘要