Modeling of Single-Sided Piercing Riveting Process
JOURNAL OF MANUFACTURING SCIENCE AND ENGINEERING-TRANSACTIONS OF THE ASME(2010)
摘要
The performance of adhesive bonded subassemblies and vehicle structures strongly depends on not only the properties of the adherends and adhesives but also the gap between the workpieces. An excessive gap between the joined structural elements could result in the joint strength decreased. In this study, a single-sided piercing riveting (SSPR) of workpieces was proposed and analyzed to ensure the part fit-up. The SSPR process has been modeled using the explicit finite element code LS-DYNA. A 3D model including the workpieces, rivet and riveting tools was generated. The model simulates the rivet piercing and deformation of 2 mm thick aluminum alloy AA5052. It was found that rivet speed and rivet leg chamfers are the main factors to influence the gap between the workpieces and consequently the quality of the riveted joints. To minimize the gap between the workpieces and optimizing the joint strength, proper riveting velocity and rivet leg chamfer are recommended. [DOI: 10.1115/1.4001249]
更多查看译文
关键词
single-sided piercing riveting (SSPR),SSPR-bonding,finite element modeling,aluminum alloy,joint quality
AI 理解论文
溯源树
样例
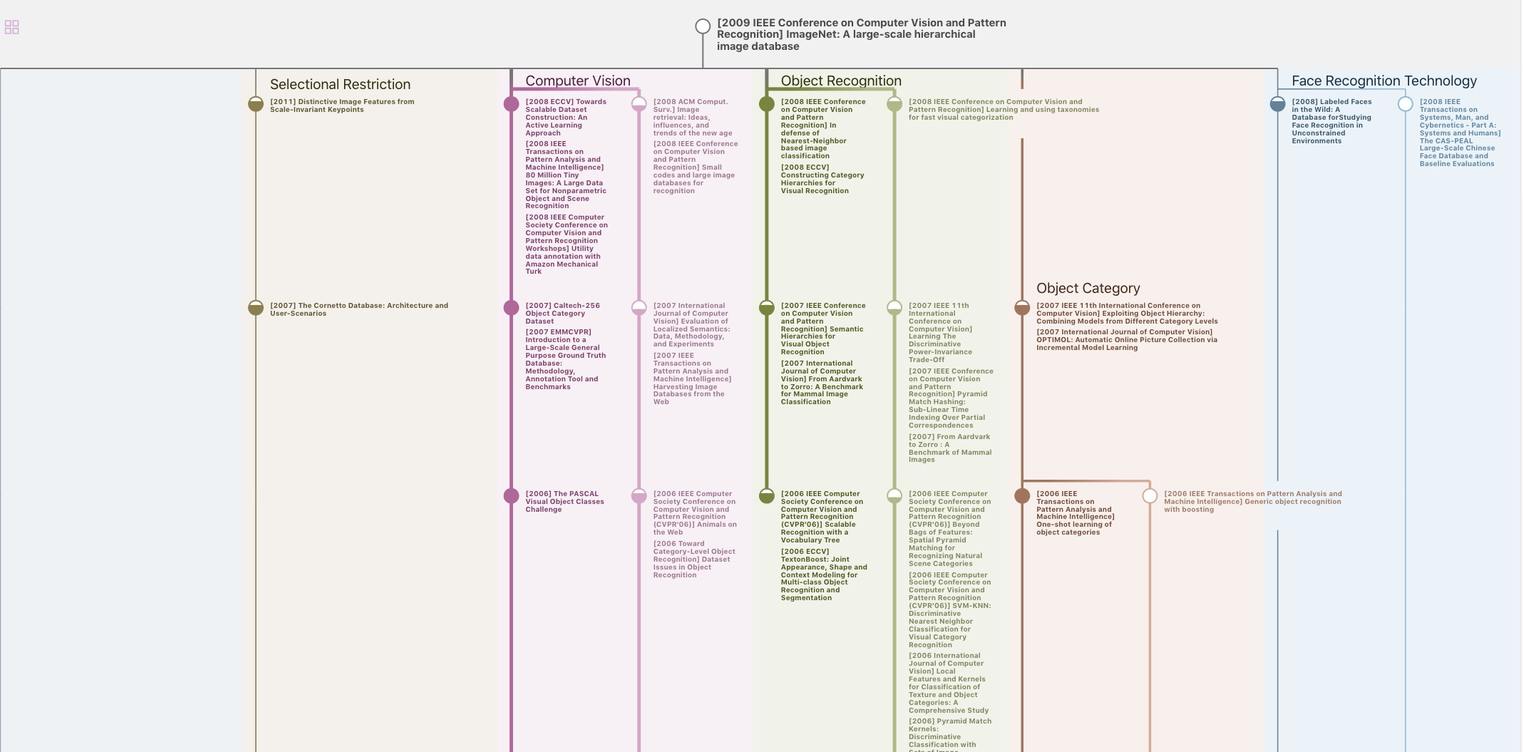
生成溯源树,研究论文发展脉络
Chat Paper
正在生成论文摘要