A study on the minimum steam cooling pressure of EOP for BWR power plants
Nuclear Engineering and Design(2011)
摘要
The minimum steam cooling pressure (MSCP) is an important parameter for safe operation of boiling water reactor (BWR)-type nuclear power plant for the anticipated transient without scram (ATWS) scenario with reactor pressure vessel (RPV) water level unknown. Under such situation, the operator is requested to open the safety/relief valves (SRVs) and control the RPV pressure slightly above the MSCP so that adequate core cooling can be maintained. It is derived based on steam cooling strategy. The MSCP, defined to be the lowest RPV pressure at which the covered portion of the core, is capable of generating sufficient steam to preclude peak cladding temperature (PCT) in the uncovered portion of the core from exceeding 1088 K (1500 °F). It is calculated by two parameters – (1) the minimum bundle steam flow (Wg-1500) to maintain PCT < 1088 K (1500 °F) and (2) the number of SRVs available for opening. For current emergency operating procedure (EOP), only one set of MSCP derived based on one value of Wg-1500 for the ATWS condition. Furthermore, it is derived based on decay power of 2.2% rated power. Thus, the current MSCP used for the ATWS accident scenarios was deemed inadequate. The purpose of this paper (work) is to study the MSCP used in the ATWS conditions. For case of ATWS of 13% full power, controlling RPV pressure at MSCP of current approach ends up with core melt. The Wg-1500 is suggested to be replaced by the steam generation rate at minimum steam cooling RPV water level (MSCRWL), which is a function of power level. Simulation result indicates controlling RPV pressure at MSCP is equivalent to controlling the RPV water level at MSCRWL. The revised MSCP is dependent on the ATWS power level. 1 Introduction Steam cooling is an important core-cooling mechanism in the operation of boiling water reactor (BWR) as the core is uncovered. Under such a situation, adequate core cooling needs to be assured. To provide adequate cooling, minimum steam cooling pressure (MSCP) plays an important role in the operation of BWR, especially for the anticipated transient without scram (ATWS) case and reactor pressure vessel (RPV) water level unknown. For such circumstances, the operators need to open safety/relief valves (SRVs) and regulate the RPV pressure to MSCP by adjusting the injection flow rate into the RPV. As the core is uncovered, metal–water reaction starts as the cladding temperature reaches 1088 K (1500 °F). In the core region, heat is generated by the fission power; in addition, it is also generated by the metal–water reaction when the core is at an elevated temperature level. For the ATWS accident scenario with RPV water level available, providing steam cooling is aimed at maintaining the peak cladding temperature (PCT) below 1088 K (1500 °F). For such a case, at least one of the make-up water systems is available. In order to maximize the pressure suppression capability of the suppression pool, it is desired to reduce the fission power by regulating the RPV water level between top of active fuel (TAF) and minimum steam cooling reactor water level (MSCRWL). MSCRWL is defined as the lowest RPV water level at which the covered portion of the core is capable of generating sufficient steam to preclude PCT in the uncovered portion of the core from exceeding 1088 K (1500 °F) ( Chen et al., 2010 ). The steam generation rate is associated with MSCRWL for each power level. By doing so, the fuel can be cooled properly, fuel damage is prevented, and a longer duration of time is available for the operators to scram the reactor. For the ATWS accident scenario with RPV water level unknown, the operator is requested to regulate the RPV pressure slightly above MSCP, so that adequate core cooling can be maintained. MSCP coupled with Wg-1500 has shown to be important in the EPGs/SAGs ( BWROG, 2001 ) set-point calculation hierarchy involving steam cooling strategy. Theoretically, it is equivalent to regulate the RPV water level slightly above top of active fuel (TAF) with available RPV water level. However, the Wg-1500 used for current MSCP calculation is based on decay power of 2.2% rated power (10 min after shutdown) with core completely uncovered, which is nothing to do with MSCRWL. Thus, the current MSCP used for the ATWS accident scenarios was deemed inadequate. The aim of the study is to discuss the mathematical models for evaluating MSCP and Wg-1500. After studying related materials, the vague concepts involved in evaluating these two parameters were clarified, and those improperly used variables were revised. The definition of Wg-1500 was also modified. Numerous revised values of MSCPs, derived from Wg-1500's which in turn were dependent on the ATWS power levels. It is noted that the revised Wg-1500 values were associated with MSCRWL. The development of the set of values of MSCP for the Kuosheng Nuclear Power Plant ( Taiwan Power Company, 1988 ) of Taiwan Power Company (TPC) by using this revised algorithm was also verified by the set of values obtained by using Modular Accident Analysis Program Version 5.00 (MAAP5) code ( Fauske & Associates, Inc., 2008 ). MAAP5 is a severe accident analysis code, developed by Electrical Power Research Institute. It has been used in developing the severe accident management strategy of nuclear power plants in Taiwan ( Chen et al., 2010; Chien et al., 2008, 2010; Chuang et al., 2009; Su et al., 2006; Wang et al., 2004, 2005; S.-J. Wang et al., 2006; T.-C. Wang et al., 2006 ). 2 Description of current MSCP and Its calculation based on BWROG EPG/SAGs Revision 2 The MSCP is the lowest RPV pressure at which steam flowing through open SRVs is sufficient to preclude any clad temperature from exceeding 1088 K (1500 °F) even if the reactor core is not completely covered. The MSCP is a function of the number of SRVs open. It is utilized to preclude fuel damage during the coolant injection and core recovery by coolant when the reactor may not be able to scram. In the accidents a table of MSCP values are used that correlates the RPV pressure to the number of SRVs open. This table is applied in EOP for the RPV flooding in an ATWS case. The table uses RPV pressure to decide whether there is enough steam to cool the core, especially when RPV water level is unknown. The approach of this section is to establish this table to preclude the peak cladding temperature in the core from exceeding 1088 K (1500 °F) by the steam cooling. In BWROG EPG/SAGs Revision 2 ( BWROG, 2001 ), the MSCP is determined by the assumptions as follows: 1. The reactor core is completely uncovered. 2. The reactor has been shutdown from rated power for 10 min. 3. The assumed reactor axial power shape was the most limiting top-peaked power shape prior to core uncovery. 4. All steam which flows through the SRVs has passed upward through the core. 5. An SRV will pass 110% of nameplate flow at 103% of nameplate pressure. According to above assumptions, the MSCP, represented in gauge pressure (PaG), can be formulated as ( BWROG, 2001 ): (2-1) MSCP ( N SRV ) = W g-core- 1 N SRV × d W d P SRV − 101,325 where W g-core-1 is the minimum core steam flow required to maintain PCT < 1088 K (1500 °F) and d W d P SRV is the specific SRV flow rate under critical flow condition in kg/s Pa. The term W g-core-1 is given by: (2-2) W g-core- 1 = N buns × Wg- 1500 where Wg-1500 is the minimum bundle steam flow required to maintain PCT < 1088 K (1500 °F) and N buns is the number of fuel bundles in core. The term absolute per one SRV is defined by: d W d P SRV = W SRV-est P SRV-ref , and W SRV-est = 1.10 × SRV nameplate flow rate, and P SRV-ref = 1.03 × SRV nameplate pressure. The factors of 1.10 in W SRV-est expression and 1.03 in P SRV-ref expression are assumed to be proper values to adjust differences between the vendor design data and the expected valve performance under actual operating conditions. 3 Description of MAAP5 Code In this study, MAAP5 code ( Fauske & Associates, Inc., 2008 ) was used to generate MSCP and the results obtained were compared with those obtained from the existing methodology (used by BWROG). MAAP5 is an integrated severe accident analysis code, widely used by the researchers, owners, and vendors in the nuclear industry. It can simulate the response of light water reactor power plants during a variety of severe accident sequences, including mitigations actions for accident management. The code provides a flexible, efficient, and integrated tool for evaluating the in-plant and ex-plant effects of a wide range of postulated accidents and for examining the impact of operator actions on accident progressions. The entire spectra of severe accident phenomena, including core heat-up, degradation and relocation, lower plenum phenomenology, corium-concrete interactions, containment hydraulics, hydrogen combustion, and radionuclide release and transport, are treated in MAAP5. All control volumes of the plant, including reactor vessel, containment, and emergency core cooling system (together with the associated control logic of ECCS) are provided. Users only need to provide the plant data in performing calculations using the code. The default values associated with the severe accident phenomena were used with no modification. For BWRs, water in the shroud downcomer, lower plenum, CRD tubes, and core regions, comprise the water control volumes. Fig. 1 illustrates the nodalization of these control volumes and identifies the structures modeled in each control volume in the RPV. MAAP5 solves a set of lumped parameter, nonlinear, first order, coupled, ordinary differential equations in time. Most of the differential equations express the conservation of mass or energy. Momentum balances in MAAP5 are considered to be quasi-steady, which reduces them to algebraic expressions. Therefore there are no differential equations in MAAP5 expressing the conservation of momentum. In MAAP5 code, the important phenomena in the reactor core, the reactor coolant system, and the containment also determined. The core heatup and melt relocation in the reactor vessel themselves involve complex phenomena. They have been extensively documented in the subroutine descriptions for HEATUP and associated routines. HEATUP subroutine calculates the core temperatures and fuel-cladding-coolant interactions and models the thermal-hydraulic behavior of the reactor core and the response of core components during all accident phases. HEATUP includes and invokes models for calculating water depletion and recovery within the reactor core, hydrogen (H 2 ) generation, natural circulation flows, radiative and convective heat transfer within and from the core, and molten pool formation including the dynamics of the surrounding crust. HEATUP calculates rates-of-change of the core state variables, except for melt relocation. These rates are determined from mass and energy balances. The main core component state variables are the nodal masses and energies of the fuel (UO 2 ), cladding (zircaloy (Zr), ZrO 2 , stainless steel (SS), steel oxide (SSO), and the U–Zr–O mixture), fuel canister (Zr and ZrO2), control blade (B 4 C, SS, SSO, and the B–Zr–SS–C–O mixture), and control/water rod (Ag–In–Cd or B 4 C, and SS and SSO or Zr and ZrO 2 ) components. Additional state variables include the cladding strains and ballooning, and the fraction of the non-volatile decay power in each node. Individual temperatures are calculated for the fuel, cladding, fuel can (where applicable), control blade (where applicable), and control/water rod components for each core node. In MAAP5 code, all important heat transfer processes between the fuel, cladding, fuel can, control blade, control/water rod, and coolant components are modeled in each core node. Also modeled are the radial thermal radiation between neighboring nodes with a proper view factor, the radiation to core shroud/barrel, conduction/convection heat transfer between nodes (axial and radial), oxidation of Zr and SS, the fuel-cladding interaction, and the fuel can-control blade interactions. In this study, a function was developed and implemented in the code to acquire the output results of the MAAP5-calculated PCT in the core region. In addition, a control loop with proportional and integral (PI) controller, developed by Chen et al. (2010) , was coupled with MAAP5 code to control the injection flow rate. With these added features, the MSCRWL, Wg-1500, and MSCP can be generated automatically using the MAAP5 code. 4 Inadequacy of current approach In the accidents a table of MSCP values are used that correlates the RPV pressure to the number of SRVs open and is used in EOP for ATWS case with RPV water level unknown. However, the assumptions of the current approach are not adequate for an ATWS case to set-up the steam cooling strategy. It is necessary to clarify the inadequacy existed in the current approach, described below. In estimating the value of W g-core-1 in Eq. (2-2) , the bundle steam flow rate (Wg-1500) required to maintain the PCT < 1088 K (1500 °F) was used. However, assumption 1 and 2 in the current approach were not adequate for an ATWS case. In this study, to verify the current MSCP results obtained from the BWROG approach by using MAAP5 code, the Kuosheng NPP was used as a reference plant. The current MSCP calculated by BWROG (as indicated in Table 1 ) was used to control RPV pressure such that the core can be maintained at a safe and stable state. However, MAAP5 code predicted a molten core if a constant core power level of 13% rated power was used with the current MSCP table (as shown in Figs. 2–5 ). The power level is assumed to be 13% and kept constant during the transient. These simulating results indicate the inadequacy of the current approach. The MSCP table derived based on decay power of 2.2% of the rated power and RPV water level at the bottom of the active fuel (BAF) cannot be applied for the ATWS cases. There is nothing to do with the ATWS power. 5 Revisions on Wg-1500 and MSCP In previous study, the MSCRWL is generated using MAAP code ( Chen et al., 2010 ). A corresponding vapor generation rate associated with MSCRWL was generated at the same time. With RPV water level controlled to MSCRWL, the peak cladding temperature (PCT) in the uncovered portion of the core can be maintained from exceeding 1088 K (1500 °F). The MSCRWL and the associated steam flow rate are dependent each other and function of the ATWS power level. The proper Wg-1500 for generation of MSCP is the steam generation rate associated with MSCRWL. The correct MSCP table can be generated from Eqs. (2-1) and (2-2) using the revised Wg-1500 that is power dependent. The Wg-1500 value can be obtained from previous study ( Chen et al., 2010 ). On the other way, the revised Wg-1500 and MSCP can also be generated using MAAP5 at the same time. Three parameters are required for the generation of revised Wg-1500 using MAAP5 – the power shape, reactor power level, and the temperature of injection flow. In addition, a typical conservative axial power shape as shown in Table 2 was used. The injection temperature is a function of reactor power which is obtained from the thermal kits ( Westinghouse Electric Corporation, 1978 ). In this simulation, the reactor power was manually input with 13% of the rated power and two SRVs opened. The inlet temperature of the injection flow was set to be the feedwater temperature that was obtained from the thermal kits as shown in Table 3 . The calculated results of MSCP with revised Wg-1500 are shown in Table 4 . In this case, the PCT of 1088 K (1500 °F) is used as target by adjusting the injection flow rate through PI controller. The responses of key parameters, such as PCT, RPV water level, RPV pressure, injection flow rate, and steam flow rate for generation of MSCP by MAAP5 are shown in Figs. 6–10 . Fig. 6 shows the PCT gradually approaches its set point of 1088 K. Fig. 7 shows the response of RPV water level. It eventually approaches the MSCRWL of 8.3 m. Fig. 8 shows the response of steam flow rate. It eventually approaches a constant value. So is the injection flowrate as shown in Fig. 9 . It approaches the same value of steam flow rate. Fig. 10 shows the response of RPV pressure. It approaches the MSCP value of 4.33 MPa automatically. Base on these results, it demonstrates that the MAAP5 code with PI controller is adequate to determine the revised Wg-1500 and MSCP. 6 Verification of MSCP with revised Wg-1500 by MAAP5 code MSCP was used in EOP for ATWS accident scenario with RPV water level unknown. At a fixed number of SRVs open, operator can control RPV pressure by adjusting the injection flow rate into RPV. In this study, the Kuosheng NPP was used as a reference plant for the verification of MSCP with opening 2 SRVs. In this case, the reactor power is of 13% rated power measured from the instrument. Based on Table 4 , the operator decided to open 2 SRVs. In order to demonstrate the revised MSCP, MAAP5 code with PI controller is used to simulate the ATWS accident scenario with RPV water level unknown. In this case, the RPV pressure of 4.33 MPa (MSCP) is used as target by adjusting the injection flow rate through PI controller. The responses of RPV pressure, RPV water level, and PCT are shown in Figs. 11–14 . Fig. 11 shows the RPV pressure gradually approaches its set point. Fig. 12 shows the response of injection flowrate. It eventually approaches a constant value. So is the RPV water level as shown in Fig. 13 . It approaches the MSCRWL of 8.3 m. Fig. 14 shows the response of PCT. It approaches 1088 K (1500 °F) automatically. It is clear that controlling the RPV pressure to MSCP is equivalent to controlling RPV water level to MSCRWL ( Table 5 ). The methodology developed in this study for obtaining adequate steam flow rate at a specified power level and the corresponding steam flow at MSCRWL has demonstrated that adequate core cooling would be preserved, indicating that for each power level, there is a corresponding steam flow rate for adequate core cooling. Computer simulation indicates controlling RPV pressure to MSCP is equivalent of controlling RPV water level to MSCRWL. This approach was proven to be a more elaborated means for establishing MSCP table in the EOP compared to the one provided by the BWROG, which gives an MSCP table based on single power level of 2.2% of rated. 7 Conclusion Steam cooling strategy is used in ATWS of BWR. In ATWS case, RPV water level is controlled between TAF and MSCRWL in order to reduce the reactor power. In the case of ATWS with RPV water level unknown, RPV pressure is controlled to MSCP to maintain adequate core cooling. However, the current MSCP is derived from a fixed value of Wg-1500, which is derived based on decay power with RPV water level at BAF. There is nothing to do with the ATWS power. Computer simulation indicates by controlling RPV pressure at the current MSCP may cause core melt. On the contrary, the proper way of MSCP is derived based on the Wg-1500 associated with MSCRWL. The Wg-1500 and MSCRWL are dependent each other depending on the reactor power and power shape. Computer simulation indicates controlling RPV pressure to MSCP is equivalent to controlling RPV water level to MSCRWL. In summary, at a specified power level, a corresponding Wg-1500 was developed which could maintain adequate core cooling. At the time for which Wg-1500 was determined, a corresponding set of values of MSCP and number of SRVs open was also generated. A number of sets of values based on various power levels would form the MSCP tables for EOP use. The approach developed in this study has proven to be a more elaborated means for establishing MSCP table in the EOP compared to the current MSCP. Acknowledgements The authors would like to appreciate the technical support of the personnel at Kuosheng NPP and at Taiwan Power Company. This work is partially supported financially by Institute of Nuclear Energy Research and Chung Yuan Christian University through a grant (Grant No. CYCU-98-CR-ME ). References BWROG, 2001 BWROG BWROG EPGs/SAGs Revision 2 2001 General Electric Company Chen et al., 2010 J.-J. Chen S.-J. Wang C.-S. Chien K.-S. Chiang J.-T. Teng Determination of BWR minimum steam cooling reactor water level and associated steam flow using MAAP4 code Nucl. Eng. Des. 240 2010 3791 Chien et al., 2008 C.-S. Chien S.-J. Wang S.-C. Chiang Development of parameter identification capability for MAAP4 code Nucl. Technol. 161 2008 203 Chien et al., 2010 C.-S. Chien S.-J. Wang J.-J. Chen K.-S. Chiang Study on the minimum number of SRVs required for emergency depressurization in EOP of BWR power plants Nucl. Eng. Des. 240 2010 2842 Chuang et al., 2009 M.-J. Chuang S.-J. Wang S.-Y. Fann S.-C. Chiang Simplification of the severe accident management guideline for the containment flooding in a Mark-III containment Nucl. Technol. 167 2009 247 Fauske, 2008 Fauske & Associates, Inc., 2008. MAAP5-Modular Accident Analysis Program for LWR Power Plants. Su et al., 2006 W.-N. Su S.-J. Wang S.-C. Chiang Development of drywell water level computational aid and application on containment flooding strategy of Mark-III system Nucl. Technol. 155 2006 253 Taiwan Power Company, 1988 Taiwan Power Company, 1988. Final Safety Analysis Report of Kuosheng Nuclear Power Station. Wang et al., 2004 S.-J. Wang K.-S. Chiang S.-C. Chiang Analysis of PWR RCS injection strategy during severe accident Nucl. Technol. 146 2004 199 S.-J. Wang et al., 2006 S.-J. Wang C.-S. Chien S.-C. Chiang Development of accumulator calculation aid for determining RCS injection volume Nucl. Eng. Des. 236 2006 1330 Wang et al., 2005 T.-C. Wang S.-J. Wang J.-T. Teng Analysis of severe accident management strategy for a BWR-4 Nuclear Power Plant Nucl. Technol. 152 2005 253 T.-C. Wang et al., 2006 T.-C. Wang S.-J. Wang J.-T. Teng Analysis of the Chinshan raw water system performance for severe accident Nucl. Technol. 156 2006 347 Westinghouse Electric Corporation, 1978 Westinghouse Electric Corporation Thermal performance data for Taiwan Power Company Kuosheng 1 & 2 1978 AJ405-0151 Jyh-Jun Chen (BS and MS, Mechanical Engineering, Chung Yuan Christian University, Taiwan in 2002 and 2004, respectively) is a Ph.D. candidate at Chung Yuan Christian University. His interests include severe accident analysis, transient analysis, and nuclear power plant simulation. Shih-Jen Wang (MS, Nuclear Engineering, National Tsing Hua University, Taiwan, 1976; Ph.D., Nuclear Engineering, University of Tennessee, 1983) is a senior researcher at Institute of Nuclear Energy Research. His interests include modeling and simulation of nuclear power plants, transient analysis, severe accident analysis, and the related optimization research in nuclear industry. Ya-Chuan Huang (BS and MS, Mechanical Engineering, Chung Yuan Christian University, Taiwan in 2003 and 2005, respectively) is an assistant researcher at INER. Her interests include severe accident analysis and nuclear power plant simulation. Jyh-Tong Teng has been a professor in Department of Mechanical Engineering, Chung Yuan Christian University (CYCU) since August 1989. He graduated from ME department, Montana State University with a BS degree in 1973, ME Department, University of California, Berkeley with MS and Ph.D. degrees in 1975 and 1978, respectively. Professor Teng has served in a number of positions at CYCU, including departmental chair of ME, dean of College of Engineering and dean of Office of International Affairs. His areas of research include evaluation of compartment fire and smoke behavior, analysis of engine thermal-fluidic phenomenon, thermal management of electronic device and system, microchannel thermo-fluidics, evaluation of nuclear power plant safety and severe accident management.
更多查看译文
关键词
minimum steam,eop
AI 理解论文
溯源树
样例
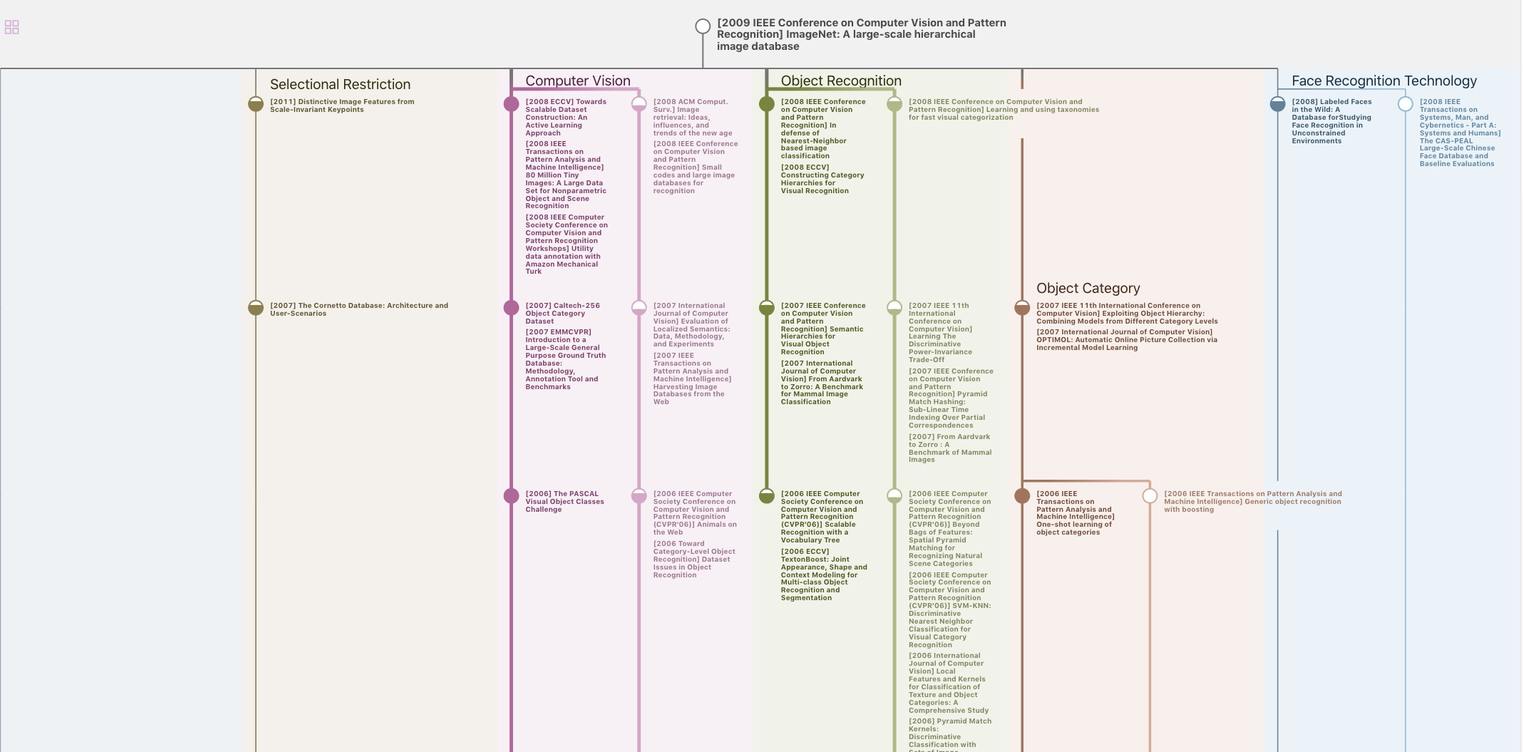
生成溯源树,研究论文发展脉络
Chat Paper
正在生成论文摘要