Aging behaviour and electrochemical properties in Mg–4.8Hg–8Ga (wt.%) alloy
Corrosion Science(2010)
摘要
Research highlights ► Dispersed Mg 21 Ga 5 Hg 3 with Ge 8 Pd 21 tetragonal structure precipitated at 423 K ► Slab and massive Mg 5 Ga 2 with D8 g orthogonal structure precipitated at 439 K ► Slab and massive Mg 5 Ga 2 dissolved in Mg matrix at 506 K ► The best anode for sea water battery is Mg–4.8%Hg–8%Ga alloy aged at 473 K for 8 h Abstract All precipitate morphologies in Mg–4.8%Hg–8%Ga alloy for a range of aging temperatures are investigated in detail using TEM and OM. The results show that Mg 5 Ga 2 and Mg 21 Ga 5 Hg 3 are the dominant precipitate in Mg–4.8%Hg–8%Ga alloy. Mg 5 Ga 2 phases precipitate in slab and massive morphologies. Mg 21 Ga 5 Hg 3 phases precipitate in dispersed particles. There have few papers focused on the relationship between the aging behaviour and the electrochemical and corrosion properties in Mg–4.8%Hg–8%Ga alloy. This study elaborates on the morphological evolution of Mg 5 Ga 2 and Mg 21 Ga 5 Hg 3 precipitates as a function of aging time and temperature and investigates the associated second phase morphology-electrochemical and corrosion response. Keywords A. Magnesium B. Galvanostatic B. Polarization B. Potentiostatic B. TEM C. Anodic dissolution 1 Introduction Magnesium alloys are widely used in high energy density batteries and sacrificial anodes due to many advantages, such as rapid activation, low specific mass, low electrode potential and high current capacity [1–5] . Since 1960s, magnesium alloy batteries have been the subject of comprehensive interest and have been developed for some military and commercial applications, such as torpedo, electromotive and unmanned underwater vehicle power source. The developed magnesium anode materials with high cell voltage are AP65 (Mg–6%Al–5%Pb) [6,7] , Mg–7%Tl–5%Al [1] and Mg–Hg alloys [8] . The specific energy of the sea water battery using Mg–Hg alloys as anode can reach 150 W h/kg [9,10] , compared with 30 W h/kg of lead acid battery. The open potential of Mg–Hg alloys in a 3.5 wt.% NaCl solution is −2.0 V (vs. SCE) [8] , compared with −1.8 V (vs. SCE) of Mg–6%Al–5%Pb alloys [6] . However, the good results of the Mg anodes obtained in high power sea water battery still meet with problems such as bad deformability, large self-corrosion velocity and low current efficiency [11,12] . Especially the Cl − in sea water produces acid environment for the Mg anodes and increases corrosion of the Mg anodes [13–16] . In order to solve these problems, some alloying elements with high over-potential of hydrogen revolution and large electrochemical activity, such as aluminium, zinc, lead and mercury, were added into magnesium anodes in recent years [17–20] . The corrosion and electrochemical properties of the Mg–Al alloys were studied a lot [14,21,22] . The corrosion behaviour of Mg–Al alloys was influenced greatly by the concentration of the Fe impurity element. If the content of Al in intra-crystalline is lower than grain boundary, corrosion occurred in intra-crystalline but not in grain boundary. If a lot of MgAl, Mg 2 Al 3 and Mg 4 Al 3 compounds exist in grain boundary, inter-granular attack occurred and inspired the self-corrosion of magnesium. More important, the Mg–Al anodes have no enough electrochemical activity to produce huge battery power. When the Mg sea water battery was used, the AZ alloys were chosen as anodes. Refs. [14,23–25] reported corrosion and electrochemical behaviours of the AZ alloys. Intra-granular corrosion was the most predominant corrosion mechanism of AZ31B alloy in 3.5% NaCl solution. The existence of twins and increase of grain size accelerated the corrosion of AZ31B alloys. A model of the atmospheric corrosion process of AZ91D was presented, where microgalvanic elements were formed with the а-phase as anode and where the eutectic а/β-constituent in the vicinity of the а-phase is the site of the cathodic reactions. The same corrosion process but a higher corrosion rate occurred in AM50 alloys, with lower aluminium content both in the grains and in the grain boundaries compared to the AZ91D alloy [25] . The actual specific energy of the Mg–Mn battery is 54 W h/kg [26] . According to Ref. [27] , the addition of Ce or La produces cathodic intermetallic compounds with RE addition and improved the corrosion resistance of AM60 alloy. The addition of Zn in Mg–Mn alloys refined the grain size and improved the corrosion resistance [28] . Song [29] explained the negative difference effect (NDE) of the Mg alloys. Decreasing NDE of the Mg anodes can produce large current efficiency. Liu [30] build a mathematic model to explain the negative difference effect of Mg alloys using Tafel dynamic formula. Shi [31] measured corrosion rates of the AZ91 alloys, Mg–10Gd-3Y–0.4Zr alloys, Mg–Cu alloys, Mg–Mo alloys, ZE41 alloys and Mg–6Zn–Mn–(0.5–2)Si–(0–0.2)Ca alloys using Tafel extrapolation. But the hydrogen evolution rate, weight loss rate and rate of Mg 2+ leaving the metal surface were recommended to evaluate the corrosion rate of the Mg anodes. According to researches [8,15,32–37] , gallium and mercury can greatly activate magnesium anodes due to the dissolution–redeposition mechanism and gallium can also enhance the corrosion resistance of the amalgams [38] . Mg 5 Ga 2 [39] and Mg 21 Ga 5 Hg 3 [40,41] intermetallic compounds exist in the Mg–Hg–Ga anodes and their morphologies and distribution influence the electrochemical and corrosion properties of the Mg–Hg–Ga anodes. This study will focus on the aging behaviours of Mg–4.8%Hg–8%Ga alloy under different aging conditions and the relationship between these precipitates and the associated electrochemical performance. 2 Experimental Mg–Hg master alloys were first melted in a sealed iron tube filled with argon, as described in a previous paper [36] . Then the Mg–Hg alloys, Mg and Ga with 99.99% purity were melted in a muffle furnace. The chemical composition of the Mg–4.8%Hg–8%Ga alloy (seen in Table 1 ) was determined by ESA and atomic absorption spectrum analysis. Homogenization of the specimens was carried out at 773 K for 24 h. Aging treatment was designed according to the DSC (Differential Scanning Calorimetry) measurements, which were performed with a NETZSCH DSC 200 F3 and the heating up ratio is 30 K/min. Fig. 1 shows the DSC curve of the Mg–4.8%Hg–8%Ga alloy. It can be seen that there are two exothermic peaks at 423 and 439 K and one endothermic peak at 506 K. For determining the precipitates and dissolved phases, the specimens were aged at 423, 473 and 523 K for 2–160 h. Microstructure and corroded surface of the specimens were observed using TEM (Transmission Electron Microscope) and OM (Optical Microscope), and TEM observation was carried out using Tecnai G2 20 ST. The specimens for TEM were polished to 0.08 mm with emery paper and ion milled with RES 101. Potentiodynamic and galvanostatic experiments were performed with a Potentiostat–Galvanostat (Model 263A) in a 3.5% (mass fraction) NaCl solution. The scanning rate of potentiodynamic measurement is 5 mV/s and the anodic current density in the galvanostatic test is 180 mA/cm 2 . The specimens were polished with emery paper and buffed to a mirror finish. Each of them was sealed with epoxy resin except for an exposed surface of 10 mm × 10 mm submitted to the electrochemical tests in a three-electrode cell. A platinum sheet was used as the auxiliary electrode and a saturated calomel electrode (SCE) with a standard electrode potential of 0.2412 V (SHE) was used as the reference electrode. 3 Results and discussion 3.1 Microstructure 3.1.1 Influence of homogenization on microstructure Fig. 2 shows the microstructures of (a) cast alloy and (b) homogenized alloy. The cast Mg–4.8%Hg–8%Ga alloy has inter-granular compounds with high Hg and Ga contents according to ESA measurements. The specimen aging at 773 K for 24 h has homogenized microstructure and no residual intermetallic compounds at the grain boundaries. 3.1.2 Influence of aging on microstructure Fig. 3 shows the TEM images of the Mg–4.8%Hg–8%Ga alloys after different aging treatments. As seen in Fig. 3 a, no second phase exist in homogenized specimen, which is consistent with Fig. 2 b. Fig. 3 also reveals three morphologies of precipitates, which are dispersed particles, slab and massive structures. According to these figures, the different precipitate morphologies with different dimensions were measured and shown in Table 2 . For dispersed precipitates, the size increased from 0.01 to 0.1 μm when the aging time increased from 2 to 160 h and increased from 0.005 to 0.03 μm when the aging temperature increased from 423 to 523 K. From Fig. 3 b, c, g and h, it can be observed that the number density of the dispersed precipitates increased when the aging time increased from 2 to 96 h and then decreased when the aging time prolonged to 160 h. The lower number density translates into a larger interspacing between the precipitates. From Figs. 3 d–f and h, it was observed that there were another slab and massive structures precipitated at 473 K in aged Mg–4.8%Hg–8%Ga alloys. Figs. 3 d and e showed that the slab structure was oriented to one direction and some precipitated together with massive structure. When aging time prolonged to 160 h the orientation of the slab structure disappeared in Fig. 3 h. Fig. 4 a shows the energy dispersive X-ray analysis result of the slab structure named A. It contains 28.47% Ga, 5.60% Hg and 65.94% Mg (mole fraction), which is closed to the content of Mg 5 Ga 2 compound. From Fig. 3 b–h and Table 2 it can be seen that the slab structure precipitated after aging at 473 K for 8 h. The length of the slab structure increased from 0.1 to 3.0 μm when the aging time prolonged from 8 to 160 h. The width of the slab structure showed no significant change with increasing aging times and only increased from 0.05 to 0.10 μm when the aging time increased from 96 to 160 h. From Fig. 3 f it can be observed that the massive structure can precipitated along the grain boundary. Fig. 4 b shows the energy dispersive X-ray analysis result of the massive structure named B in Fig. 3 e. It contains 25.85% Ga, 4.18% Hg and 69.97% Mg (mole fraction), which is also closed to the content of Mg 5 Ga 2 compound. As seen in Table 2 , the length and width of the massive structure both increased with the increasing aging time. Fig. 5 a shows the diffraction pattern of the Mg–4.8%Hg–8%Ga alloy after aging at 473 K for 96 h. The calibration in Fig. 5b–d demonstrated that there existed three group diffraction spots, which were hexagonal, orthogonal and ring spots. As seen in Fig. 5 b the zone axis of the Mg matrix diffraction pattern is [0 0 0 1]m and the spots are in the { 01 1 ¯ 0 } crystal plane. The orthogonal spots correspond to Mg 5 Ga 2 precipitates with D8 g crystal structure. Combined ESA results (seen in Fig. 4 ) with the calibration (seen in Fig. 5 c), the slab and massive structures are determined to be Mg 5 Ga 2 phase. According to the calibration result in Fig. 5 c, the (1 1 2) p and (2 2 0) p of Mg 5 Ga 2 phase overlap the ( 1 ¯ 1 0 0 ) m and ( 0 1 1 ¯ 0 ) m of Mg matrix. This leads to stronger facular points in these diffraction spots. The ring spots correspond to Mg 21 Ga 5 Hg 3 precipitates with Ge 8 Pd 21 tetragonal structure [41] . The calibration result was shown in Fig. 5 d. Combined Fig. 3 with the diffraction pattern, it can be induced that the diffraction ring with Mg 21 Ga 5 Hg 3 tetragonal structure are produced by dispersed precipitates. According to Table 2 , dispersed precipitates and slab and massive structures both precipitated at 473 K but slab and massive structures disappeared at 423 and 523 K. Comparing with the DSC analysis result, it can be induced that the exothermic peaks at 423 and 439 K denote individually the precipitation of Mg 21 Ga 5 Hg 3 and Mg 5 Ga 2 compound and the endothermic peak at 506 K denote the dissolving of the slab and massive Mg 5 Ga 2 compound. 3.2 Electrochemical and corrosion behaviours 3.2.1 Galvanostatic measurements Fig. 6 shows galvanostatic curves of the Mg–4.8%Hg–8%Ga alloys after different heat treatments. The stable potentials of all specimens are fitted according to the galvanostatic curves and shown in Table 3 . From Fig. 6 it can be observed that all specimens show stable discharge curves with activation time of less than 50 s except the homogenized specimen. Activation time of 170 s and the most positive stable potential of −1.547 V (vs. SCE) lead to the worst electrochemical activity in the homogenized specimen [8] . It may due to the lack of cathodic precipitates, which can make corrosion electric couple with Mg matrix and inspire its activation dissolution. When the aging times prolong from 2 to 160 h at 473 K, the stable potentials of the specimens first move negative and then move positive. The most negative potential of −1.935 V (vs. SCE) occurs in the specimen aged for 96 h. The most negative stable potential leads to the least anodic polarization as well as the best electrochemical activity [8] . For the specimen aged at 473 K, the number density of the precipitates increased when the aging time increased to 96 h and then decreased when the aging time prolonged to 160 h. A larger number of the precipitates promote the dissolution of the Mg matrix as well as the electrochemical activity. According to dissolution–deposition activation mechanism [36] , the precipitates, especially Mg 21 Ga 5 Hg 3 phases can dissolve with the dissolving of Mg matrix and produce Hg and Ga ions, which are deoxidized by Mg and deposited on the surface of the Mg alloy. The deposed Hg and Ga sediment can strip the corrosion film and combine with Mg atoms to produce Mg amalgam, which react severely with water and maintain the activation reaction circle. When the aging time prolonged to 160 h, the precipitates gathered and grew-up. This leads to a decreased number density of activation points and produces a positive stable potential of −1.650 V (vs. SCE). Considering the stable potentials of the specimens aged at different temperatures for 8 h, the specimens aged at 473 and 523 K for 8 h have close ones, which are more negative than −1.8 V (vs. SCE). It may due to a large number of dispersed Mg 21 Ga 5 Hg 3 and slab and massive Mg 5 Ga 2 precipitates. More positive stable potential as well as worse electrochemical activity occurs in the specimen aged at 423 K for 8 h and when measuring for 80–200 s, polarization occurs and the stable potential shuffled about 200 mV. This may due to less size and number density of the dispersed Mg 21 Ga 5 Hg 3 precipitates. 3.2.2 Potentiodynamic measurements Fig. 7 shows the potentiodynamic curves of the Mg–4.8%Hg–8%Ga alloys after different heat treatments. It can be seen that they are typical Tafel curves. No passivation behaviours occur in the specimens. The corrosion current densities and corrosion potentials were calculated from the Tafel curves and list in Table 3 . From the calculated corrosion current densities it can be seen that the corrosion resistances of these specimens from large to small is homogenized state > aged at 423 K for 8 h > aged at 473 K for 2 h > aged at 437 K for 8 h > aged at 523 K for 8 h > aged at 473 K for 96 h > cast > aged at 473 K for 160 h. According to Refs. [23,25,42] , the corrosion resistance of Mg anodes is greatly influenced by morphology, size and distribution of the precipitates because of their cathodic qualities in the corrosion galvanic cell. No second phases exist in the homogenized specimen and the uniform electrochemical property leads to small potential difference as well as small corrosion driving-force. As seen in Table 3 , the smallest corrosion current density of 1.23 mA/cm 2 occurs in the homogenized specimen. In the specimen aged at 473 K for different times, the increasing time leads to increasing sizes and number densities of the cathodic precipitates as well as the increasing galvanic corrosion driving-force. In the specimen aged at 473 K for 160 h, the dispersed Mg 21 Ga 5 Hg 3 and slab and massive Mg 5 Ga 2 precipitates gathered and grew-up. The non-uniform microstructure produces the worst corrosion resistance and the largest corrosion current density of 24.9 mA/cm 2 . Considering the corrosion current densities of the specimens aged at 423, 473 and 523 K for 8 h, the best corrosion resistance occurs in the specimen aged at 423 K for 8 h. It may due to the smallest sizes and number densities of the precipitates. As an anode material for sea water battery with high power, negative stable potential is very important for achieving the working potential of sea water battery. Meanwhile less corrosion rate is required for large current efficiency. According to the electrochemical and corrosion properties of Mg–4.8%Hg–8%Ga alloys after different heat treatments as shown in Table 3 , the best produced alloy for application in sea water battery is the Mg–4.8%Hg–8%Ga alloys aged at 473 K for 8 h. It was also confirmed in a simple sea water cell experiment with CuCl as cathodic. The simple cell results demonstrated that the specific energy of the sea water battery using the Mg–4.8%Hg–8%Ga alloy aged at 473 K for 8 h as anode can reach 135 W h/kg, compared with 30 W h/kg of lead acid battery and 88 W h/kg of Mg/AgCl sea water battery [43] . The corrosion rate of the Mg–4.8%Hg–8%Ga alloy aged at 473 K for 8 h in potentiodynamic measurement is 2.76 mA/cm −2 , compared with 2.94 mA/cm −2 of Mg–6%Al–5%Pb alloys [7] . 4 Conclusions The influences of precipitate morphology evolution on the electrochemical and corrosion properties were studied in aged Mg–4.8%Hg–8%Ga alloys. Dispersed Mg 21 Ga 5 Hg 3 with Ge 8 Pd 21 tetragonal structure precipitated at 423 K. Slab and massive Mg 5 Ga 2 with D8 g orthogonal structure precipitated at 439 K and dissolved in Mg matrix at 506 K. The number densities of the dispersed Mg 21 Ga 5 Hg 3 and slab and massive Mg 5 Ga 2 precipitates increased when the aging time increased to 96 h and decreased when the aging time increased to 160 h in the Mg–4.8%Hg–8%Ga alloys aged at 473 K. The size and number density of the dispersed Mg 21 Ga 5 Hg 3 increased when the aging temperature increased from 423 to 523 K in the Mg–4.8%Hg–8%Ga alloys aged for 8 h. The larger number densities of the precipitates promote activation dissolution of Mg matrix according to the dissolving–deposition mechanism. The most negative stable potential of −1.935 V (vs. SCE) occurs in the Mg–4.8%Hg–8%Ga alloy aged at 473 K for 96 h. Bad electrochemical properties occurs in the Mg–4.8%Hg–8%Ga alloy aged at 473 K for 160 h due to gathering and growing-up of the Mg 21 Ga 5 Hg 3 and Mg 5 Ga 2 precipitates. Larger sizes and number densities of the dispersed Mg 21 Ga 5 Hg 3 and slab and massive Mg 5 Ga 2 precipitates in the Mg–4.8%Hg–8%Ga alloys lead to larger galvanic corrosion driving-force as well as the worse corrosion resistance. The best produced alloy for application in sea water battery is the Mg–4.8%Hg–8%Ga alloys aged at 473 K for 8 h. References [1] D. Aurbach G.S. Suresh E. Levi A. Mitelman O. Mizrahi O. Chusid M. Brunelli Progress in rechargeable magnesium battery technology Adv. Mater. 19 2007 4260 4267 [2] R. Renuka Influence of allotropic modifications of sulphur on the cell voltage in Mg–CuI(S) sea water activated battery Mater. Chem. Phys. 59 1999 42 48 [3] J. Giraudet D. Claves K. Guerin M. Dubois F. Masin A. Hamwi Magnesium batteries: towards a first use of graphite fluorides J. Power Sources 173 2007 592 598 [4] R. Renuka AgCl and Ag 2 S as additives to CuI in Mg–CuI sea water activated batteries J. Appl. Electrochem. 27 1997 1394 1397 [5] H. Zhao P. Bian D. Ju Electrochemical performance of magnesium alloy and its application on the sea water battery J. Environ. Sci. Suppl. 21 2009 S88 S91 [6] N. Muniyandi P.B. Mathur Studies on magnesium and its alloys in battery electrolytes Corrosion 27 1991 68 71 [7] R. Udhayan D.P. Bhatt On the corrosion behaviour of magnesium and its alloys using electrochemical techniques J. Power Sources 63 1996 103 107 [8] Y. Feng R.C. Wang K. Yu C.Q. Peng J.P. Zhang C. Zhang Activation of Mg–Hg anodes by Ga in NaCl solution J. Alloy Compds. 473 2009 215 219 [9] N.E. Bagshaw S. Warrell Anodic dissolution of magnesium alloys related to lead chloride–magnesium sea water batteries J. Thompson Power Sources: Research and Development in Non-Mechanical Electrical Power Sources 1981 E-Publishing Inc. London 117 139 [10] F. Sammoura K.B. Lee L.W. Lin Water-activated disposable and long shelf-life microbatteries Sens. Actuators A 111 2004 79 86 [11] K.V. Rao Performance evaluation of Mg–AgCl batteries for under water propulsion Defence Sci. J. 5 2001 161 170 [12] L.S. Guang A. Andrej Corrosion mechanisms of magnesium alloys Adv. Eng. Mater. 1 1999 11 33 [13] Y. Feng R.C. Wang K. Yu C.Q. Peng W.X. Li Influence of Ga and Hg on microstructure and electrochemical corrosion behavior of Mg alloy anode materials Trans. Nonferr. Met. Soc. China 17 2007 1363 1366 [14] W. Lei P.Z. Bo S. Tadashi Corrosion behavior of AZ91 magnesium alloy in dilute NaCl solutions Mater. Des. 31 2010 857 863 [15] D.I. Uhlenhaut A. Furrer P.J. Uggowitzer J.F. Loffler Corrosion properties of glassy Mg70Al15Ga15 in 0.1 M NaCl solution Intermetallics 17 2009 811 817 [16] Z.Q. Ma X. Pang L. Zuo X. Cao S.M. Zeng Mechanism of activation of anode of Mg alloy sea water battery Surf. Technol. 37 2008 5 7 [17] B.H. Xi T. Xia Survey of power battery for torpedo propulsion Torpedo Technol. 13 2005 7 12 [18] S. Font J.P. Descroix G. Sarre Advanced reserve batteries for torpedoes propulsion H. Cherry Proceedings of the 31st Power Sources Symposium 1984 Electrochemical Soc. Penniton 362 368 [19] J.G. Kim J.H. Joo S.J. Koo Development of high-driving potential and high-efficiency Mg-based sacrificial anodes for cathodic protection J. Mater. Sci. Lett. 19 2000 477 479 [20] Z.Q. Ma W.X. Li K. Yu Electrochemical characteristics of magnesium alloys in synthetic sea water Mater. Protect. 35 2002 16 18 [21] A. Pardo M.C. Merino A.E. Coy R. Arrabal F. Viejo F. Matykina Corrosion behaviour of magnesium/aluminium alloys in 3.5 wt.% NaCl Corros. Sci. 50 2008 823 834 [22] M. Liu P.J. Uggowitzer A.V. Nagasekhar P. Schmutz M. Easton G.L. Song A. Atrens Calculated phase diagrams and the corrosion of die-cast Mg–Al alloys Corros. Sci. 51 2009 602 619 [23] N.N. Aung W. Zhou Effect of grain size and twins on corrosion behaviour of AZ31B magnesium alloy Corros. Sci. 52 2010 589 594 [24] M.F. He L. Liu Y.T. Wu Z.X. Tang W.B. Hu Corrosion properties of surface-modified AZ91D magnesium alloy Corros. Sci. 50 2008 3267 3273 [25] M. Jonsson D. Persson The influence of the microstructure on the atmospheric corrosion behaviour of magnesium alloys AZ91D and AM50 Corros. Sci. 52 2010 1077 1085 [26] H.L. Li Y.H. Huang S.W. Li Z.K. Yang Magnesium anode plates, CN 1461067A 2003 [27] W.J. Liu F.H. Cao A. Chen L.R. Chang J.Q. Zhang C.N. Cao Corrosion behaviour of AM60 magnesium alloys containing Ce or La under thin electrolyte layers. Part 1: microstructural characterization and electrochemical behaviour Corros. Sci. 52 2010 627 638 [28] D.S. Yin E.L. Zhang S.Y. Zeng Effect of Zn on mechanical property and corrosion property of extruded Mg–Zn–Mn alloy Trans. Nonferrous Met. Soc. China 18 2008 763 768 [29] G.L. Song Corrosion and Protection of Magnesium first ed. 2006 Chemical Industry Beijing [30] Z.M. Shi M. Liiu A. Atrens Measurement of the corrosion rate of magnesium alloys using Tafel extrapolation Corros. Sci. 52 2010 579 588 [31] L.J. Liu M. Schlesinger Corrosion of magnesium and its alloys Corros. Sci. 51 2009 1733 1737 [32] D.O. Flamini S.B. Saidman J.B. Bessone Aluminium activation produced by gallium Corros. Sci. 48 2006 1413 1425 [33] S.H. Deng D.Q. Yi L.H. Zhao L.L. Zhou B. Wang C.N. Ji B. Lan Study on Mg alloy anode material for sea water battery Bett. Technol. 131 2007 402 405 [34] H.A.E.I. Shayeb F.M. Abd Ei S.Z.E. Abedin Effect of gallium ions on the electrochemical behaviour of Al, Al–Sn, Al–Zn and Al–Zn–Sn alloys in chloride solutions Corros. Sci. 4 2001 643 645 [35] M. Nestoridi D. Pletcher R.J.K. Wood S.C. Wang R.L. Jones K.R. Stokes I. Wilcock The study of aluminium anodes for high power density Al/air batteries with brine electrolytes J. Power Sources 178 2008 445 455 [36] Y. Feng R.C. Wang K. Yu C.Q. Peng W.X. Li Influence of Ga content on electrochemical behavior of Mg–5at%Hg anode materials Mater. Trans. JIM 49 2008 1077 1080 [37] J.B. Bessone The activation of aluminium by mercury ions in non-aggressive media Corros. Sci. 48 2006 4243 4256 [38] M.R. Pinssco E. Angelini E. Cordano F. Prsalbino Structural characterization and corrosion resistance of Ga-precious metal alloys formed by liquid–solid reaction at room temperature J. Alloy Compds. 317–318 2001 411 418 [39] Y. Feng R.C. Wang K. Yu W.X. Li Influence of heat treatment on electrochemical behavior of the Mg anode materials J. Cent. South Univer. Technol. 14 2007 12 15 [40] Y. Feng R.C. Wang C.Q. Peng W.N. Guang Influence of Mg 21 Ga 5 Hg 3 compound on the electrochemical properties of Mg–Hg–Ga alloys Trans. Nonferr. Met. Soc. China 19 2009 154 159 [41] L.M. Zeng Y. Feng R.C. Wang Y.Q. Chen Crystal structure and properties of the new ternary compound Mg 21 Ga 5 Hg 3 Intermetallics 17 2009 873 877 [42] N. Liu J.L. Wang L.D. Wang Y.M. Wu L.M. Wang Electrochemical corrosion behavior of Mg–5Al–0.4Mn–xNd in NaCl solution Corros. Sci. 51 2009 1328 1333 [43] M. Hiroi Pressure effects on the performance and the E.M.F. of the Mg–AgCl sea water battery J. Appl. Electrochem. 10 1980 203 211
更多查看译文
关键词
A. Magnesium,B. Galvanostatic,B. Polarization,B. Potentiostatic,B. TEM,C. Anodic dissolution
AI 理解论文
溯源树
样例
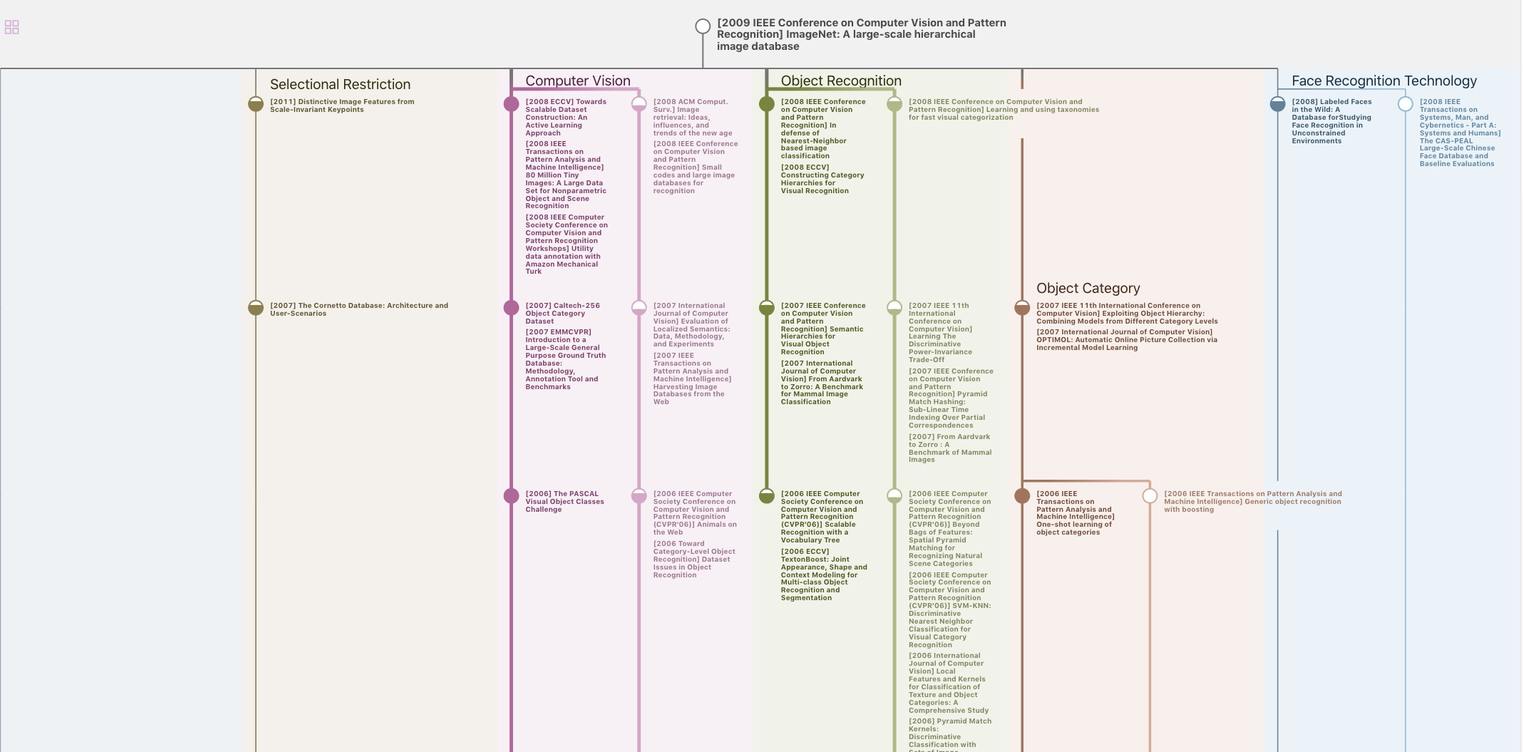
生成溯源树,研究论文发展脉络
Chat Paper
正在生成论文摘要