Investigation of abnormal high impact toughness in simulated welding CGHAZ of a 8%Ni 980MPa high strength steel
Materials Science and Engineering: A(2010)
摘要
It is well known that the toughness in the coarse grain heat affected zone (CGHAZ) is of the lowest in the heat affected zone (HAZ) of a HSLA steel welding joint. In the present work although the grain size in the simulated CGHAZ was as large as 100–300 μm and its tensile strength and elongation were lower than those of the fine grain heat affected zone (FGHAZ), however its Charpy V impact toughness at room temperature reached 193 J, which was appreciably higher than 138 J of the simulated FGHAZ with grain size of 30 μm. This abnormal phenomenon was investigated in this paper by analyzing the micromechanism of ductile rupture in associated microstructures and taking account of the effects of stress triaxiality. Keywords 8%Ni high strength steel Heat affected zone Impact toughness Ductile fracture 1 Introduction Due to its coarse grains and high hardenability, the coarse grain heat affected zone (CGHAZ(CG)), which is overheated to a high temperature (up to 1350 °C) and has very large grains shows the lowest ductility and toughness in a welding joint and deteriorates the performance of the welding structure [1–6] . On the contrary, the fine grain heat affected zone (FGHAZ(FG)), which is heated to the normalization temperature (850–930 °C) and has much finer grains, always shows the mechanical properties (including strength, ductility and toughness) superior than those shown in other regions within the HAZ [7] . In [7] , the hardness of 350–360 Hv was observed in the CGHAZ, which was higher than that of 330–350 Hv in FGHAZ [7] . In Refs. [8] and [9] , as shown in Table 1 , Charpy V energy was decreased from 5.53 J to 3.98 J as the austenitizing temperature was raised, even though the plane strain fracture toughness ( K 1c ) measurement exhibited an approximate 80% to two fold increase (from 34–43 MP am 1/2 to 57–70 MP am 1/2 ) [10] , when the austenitizing temperature increased from 870 °C to 1200 °C. The authors attributed it to the effects of the grain size on the characteristic distance. In Ref. [11] , Cox and Low explained the superior high fracture toughness of the 18 Nickel-200 grade maraging steel for which the rupture mechanism was through the growth of primary voids until impingement-resulting coalescence instead of through the connection by the shear sheets formed by secondary voids. Ref. [12] showed that the fracture toughness (176 kN/m) of the simulated coarse-grained HAZ (heated to 1300 °C with grain size of 128 μm) was higher than that (98 kN/m) of fine grained HAZ (heated to 960 °C with grain size of 28 μm). Ref. [13] also revealed the similar phenomenon that the toughness of CG HAZ region was higher than that of FG HAZ region in an 8% Ni high strength steel. Davis and King [14] showed that the fracture toughness was deteriorated drastically for the simulated specimen subjected to a thermal cycle with peak temperature of 800 °C. The deterioration was attributed to the formation of the mixture of microstructures in the partly transformed zone of HAZ, in which the M/A constituent was distributed in shape of network. In Ref. [15] , Jang et al. showed that: among the coarse-grained HAZs, the inter-critically reheated CGHAZ (IC CGHAZ) was found to have the lowest toughness value (20 J) at 77 K. It indicated that the ICCGHAZ was the primary LBZ in a welding joint at a cryogenic temperature, at which 9% Ni steel is generally used. In that paper the authors thought that the impact toughness variation of the simulated CGHAZ specimens could not be explained by the change in volume fraction of the retained austenite, a factor known as the most important metallurgical factor controlling the cryogenic toughness of 9% Ni steel. Instead, the M/A constituents were observed to form along the boundaries of laths or prior austenite grains. In the case of IC CGHAZ, the M/A constituents containing high carbon content could raise the stress of neighboring matrix and thus could easily induce the brittle fracture at cryogenic temperature. Although the unaltered coarse-grained HAZ (UA CGHAZ) had a slightly larger amount of M/A constituents than that in the IC CGHAZ, it showed a higher toughness than that in the IC CGHAZ. It was mainly because of that it is M/A constituent had too small carbon content to critically raise the stress of the neighboring matrix. On the other hand, the high toughness of the super-critically reheated CGHAZ (SCR CGHAZ) was attributed to the fine-grained microstructure and small fraction of the M/A constituents. In the present paper, the abnormal phenomena that the Charpy V toughness in the simulated CG are higher than those in the simulated FG are investigated with analyzing the different ductile fracture micromechanisms in associated microstructures formed by heating to 1320 °C and 900 °C. The effects of the stress triaxiality on the nucleation and growth of the voids are also taken account for the different behaviors of the CG in the tensile tests and the Charpy V tests. 2 Materials and experimental An 8% Ni 980 MPa grade steel with compositions shown in Table 2 was used. Specimens cut in the rolling direction were heated by a heat simulating machine Thermorestor W to preset temperatures: CG (1320 °C), FG (900 °C), 730 °C and 600 °C. The simulated heating procedures were designed as those shown in Table 3 . Actually, in this work the peak temperatures and cooling rates set in the thermal cycles are well designed to simulate possible heating histories and possible HAZ microstructures which occurred and were produced in real welding productions. An actual MAG welding process was carried out with following process parameters: welding energy input = 16 kJ/cm, welding current = 280 A, shielding gas, Ar + 5% CO 2 . Double heating simulations were carried out at following temperatures: 1320 °C + 1320 °C, 1320 °C + 900 °C, 1320 °C + 730 °C, 900 °C + 1320 °C, 900 °C + 900 °C, and 900 °C + 730 °C. The regime of 1320 °C + 1320 °C double heating simulation, which does not present in the actual cycle for multiplayer welding, was deliberately set for identifying the unusual mechanical behavior of the CG region. The formed microstructures were observed by optical microscope (OP), scanning electron microscope (SEM 6700F) and transmission electron microscope (TEM JEOL2001). The grain sizes were measured by linear section method. Microstructures produced in heat simulation and actual welding procedures are described in Table 4 . Retained austenite films were observed by TEM and identified by selected area electron diffraction pattern (SADP). Standard tensile and Charpy V specimens were cut in L–T direction. Dimensions of specimens are shown in Fig. 1 . All tests were carried out at −50 °C and room temperature (RT). The universal test machine SHIMACZU AG-10 TA was used for tensile tests and the instrumented impact machine CIEM-30CPC was used for Charpy V impact tests. The average of toughness values measured in three specimens was taken as the test result. The fracture surfaces of fractured specimens were observed in detail and related to the features of the microstructures. The microstructures and the fracture surfaces of CG and FG zones of the actual weldment were observed and compared with those of corresponding simulated zones. Finite element calculations were carried out for estimation of the stress triaxialities in tensile specimens and Charpy V test specimens. 3 Experimental results 3.1 Microstructures Fig. 2 shows the optical microscope (OP), scanning electron microscope (SEM), transmission electron microscope (TEM) and selected area electron diffraction pattern (SADP) images of simulated CG specimen which was heated to 1320 °C and then rapidly cooled. In Fig. 2 , the optical microstructures of specimen CG show the extreme coarse original austenite grains (100–300 μm) with several large lath bainite packets (100 μm) in each. In Fig. 2 (b), the SEM images show the bainite packets composed of binds of bainite laths and gray islands ( Fig. 2 (b)). The individual bainite laths are separated by retained gray matrix strips, which have the same color and feature of the gray islands ( Fig. 2 (b)). Fig. 2 (c) shows the general pattern of TEM image of bainitic laths. In Fig. 2 (d), numerous thin carbide plats precipitate inside of a bainite lath in an orientation perpendicular to its axis. In Fig. 2 (e), the SADP shows that the dark strip separating the neighboring bainitic laths consists of retained austenite. From Fig. 2 , the microstructure formed by heating to 1320 °C and rapid cooling can be described as follows: the austenite grains heated to 1320 °C grew to extremely large sizes. The carbon and other alloy elements distributed uniformly in the austenite grains. During rapid cooling, the bainitic laths nucleated in austenite with the covariant mode at full length and then grow in width through diffusion [16] with intra-lath carbide precipitation. The bainitic laths had 0.4–1.0 μm in width and the intra-lath carbide plats had 50 nm in length and less than 10 nm in width. Parallel bainitic laths formed the bainitic packets having the sizes up to 100 μm. Due to the high nickel content and the large grain size, the hardenability of the austenite is high. A great area of austenite retained in features of both inter-lath layers and blocky islands as shown in Fig. 2 (b). Parts of the retained austenite transferred to martensite and form low carbon (0.03%), Ni-rich M–A constituents in features of inter-lath strips and blocky islands. The microstructure of the present low carbon, high Ni steel formed by heating to 1320 °C and rapid cooling is considered to be a special lath bainite, presenting in lath-bainite-morphology and with lower-bainite-carbide distribution. Fig. 3 shows the OP, SEM, and TEM images of simulated FG specimen, which was heated to 900 °C and then rapidly cooled. In Fig. 3 (a), the OP image shows the darker lath martensite grains (of 30 μm in size) with bright islands embedded. In the SEM image Fig. 3 (b), the bright laths composed of martensite laths and bainite laths distribute in parallel or in random on the darker gray matrix with many retained islands. Fig. 3 (c) and (d) are the TEM images of the martensite laths where dense dislocations are present however no carbide precipitation can be identified. The reason identifying the microstructure in Fig. 3 (c) and (d) as lath martensite was based on facts that there are no carbide precipitation and the morphology of rather random lath distribution. Due to high Ni content, great areas of austenite was retained in feature of both inter-lath strip and blocky islands. Because the specimen was heated to 900 °C and held only 1 s, the carbon and other alloying elements could not be made uniform in distributions. Although the general carbon content was low (0.03%), local carbon-rich regions in original tempered bainite matrix might retain and transform to the high carbon twin martensite laths ( Fig. 3 (d)). By detailed observation of Fig. 3 (b), numerous black circular points can be found in gray islands and inter-lath layers. It seems that these black points are carbide precipitations however it has not been identified by TEM images. Fig. 4 shows the microstructures of original matrix, specimen heated to 600 °C and specimen heated to 730 °C. The microstructure of the matrix shown in Fig. 4 (a) is tempered bainite with 10% retained austenite. The microstructural morphology consists of lath bainite packets and bright islands. Because the area fractions of the bright islands is much larger than 10% (about 40%), it is reasonable to consider that most parts of austenite in the islands had transformed to the low carbon martensite and formed the Ni-rich M–A constituents. In Fig. 4 (b) and (c) after heated to 600 °C and 730 °C, while the morphology of bainite packets looks unchanged, appreciable depositions can be found in the bright islands by depicting numbers of holes in the islands. This fact supports the argument that the bright islands are composed of decomposable M–A constituent. 3.2 Global mechanical properties Table 5 shows the values of hardness measured in various specimens. From Table 5 the highest hardness presents in the specimen heated to 900 °C and then rapidly cooled, corresponding to the fine grain low carbon martensite microstructure. The specimen heated to 1320 °C and then rapidly cooled has the second high hardness due to absence of tempering. Heating specimens to 600 °C and 730 °C causes minor changes of the hardness. Tables 6 and 7 show the results of tensile tests at RT and at −50 °C respectively. Tables 8 and 9 show the results of Charpy V tests at RT and at −50 °C respectively. Table 10 shows the results of Charpy V tests at RT for double-heating-simulated specimens. Fig. 5 shows the stress–strain plots measured in specimens tensile-tested at RT. Fig. 6 shows the load–displacement plots measured by the instrumented impact machine. From Tables 5–10 , Figs. 5 and 6 , following important events for the results of global mechanical property can be drawn: (1) Specimen heated to 900 °C has the highest strength. Both specimens heated to 1320 °C and 900 °C without tempering have higher strengths than the strengths of the tempered specimens (matrix, specimen heated to 600 °C and 730 °C). Beside the higher strength specimens heated to 900 °C has higher ductility ψ than that of specimens heated to 1320 °C. (2) Specimens heated to 900 °C (FGHAZ) have the finest grains, the highest strength but the lowest RT Charpy V toughness of 138 J. From Fig. 6 (b), the low toughness results mainly from the low resistance to crack extension, i.e. the low E p in Table 8 . To great surprise, the extremely coarse CG heated to 1320 °C has the highest RT Charpy V toughness of 193 J, which is remarkably higher than 138 J for the FG heated to 900 °C ( Table 8 ). This phenomenon goes against the well recognized facts that the FG posses the highest impact toughness and the CG has the lowest. However, the similar results have been observed in previous investigations [12–14] . Shi [12] and Davis and King [14] showed that fracture toughness is also the best in the simulated coarse-grained HAZ. (3) For double-heating-simulated specimens, the values of toughness of specimens double-heated to1320 °C + 1320 °C (specific specimens for identifying the higher toughness obtained in CG HAZ) or to 900 °C + 1320 °C are higher than that of corresponding single-heating specimens, however, the values of toughness of 1320 °C + 900 °C or 900 °C + 900 °C double-heating specimens are lower than that of single-heating specimens ( Table 10 ). These results identify the highest toughness obtained by heating to 1320 °C and mean that no matter how it is in a single treatment (on the matrix) or in the second treatment in a double heating process (on ever treated specimen) the heating to 1320 °C always improves the toughness. On the contrary no matter in a single treatment or in the second treatment the heating to 900 °C deteriorates the toughness. These results are compared in Table 10 and Fig. 6 (b). 3.3 Microscopic observation 3.3.1 Fracture surfaces of tensile tested specimens The macroscopic features of fracture surfaces of tensile tested specimens heated to 900 °C and 1320 °C are composed of two parts: a fibrous rupture core and a shear lip outside ring, while those of tempered specimens (matrix, heated to 600 °C and 730 °C) are composed of three parts: a fibrous rupture core, a radial shear zone in middle and a shear lip outside ring. Fig. 7 shows the microscopic features of fracture surfaces of specimens fractured at RT by tensile tests. The features of fracture surfaces of specimens fractured at −50 °C show similar pattern as shown in Fig. 7 . From Fig. 7 (a), it is seen that the fracture surfaces of specimens heated to 1320 °C consist of a number of large primary voids (40–60 μm in size) and numerous secondary small voids, which connect the primary voids before they impinge. At the center of the large primary voids, a second phase particle or an inclusion can be found, however nothing can be found in the small secondary voids. With this fact and by comparing Fig. 7 (a) and Fig. 2 (a) and (b), it seems that the large primary voids were nucleated and developed from the island M–A islands and the small secondary voids are produced by breaking the bainitic laths. For specimens heated to 900 °C, 730 °C and 600 °C and the matrix, the fracture surfaces also consist of a number of large primary voids (40–60 μm in size) and numerous secondary small voids, however show more uniform and fine features. Fig. 8 shows a lateral side face of a 900 °C heated specimen fractured by tensile test. This figure shows numerous severely elongated bainitic laths (part of martensite lath) and M–A islands (elongated to bright, long and fine strips). From this figure, it is found that the M–A islands have high plasticity, which are not cracked, even though they have been severely elongated. Fig. 8 also shows a part of the fracture surface. The numerous very small voids on the fracture surface seem to be nucleated from the broken bainitic laths (part of martensite lath) which are shown on the lateral side surface. 3.3.2 Fracture surfaces of Charpy V test specimens Fig. 9 shows fracture surfaces of Charpy V tested specimens: (a) and (b) specimen heated to 1320 °C, presenting the highest toughness of 198 J at −50 °C, (c) specimen heated to 900 °C, presenting the lowest toughness 142 J at −50 °C, (d) specimen heated to 730 °C, having toughness of 187 J. Fig. 10 shows the fracture surfaces of Charpy V specimens which were double-heating treated at various temperatures. From Figs. 9 and 10 , following interesting phenomena are worthy to pay special attention: the characteristic features of the fracture surface of CG specimen are the coalescence of large primary voids as shown in Fig. 9 (a). In Fig. 9 (b), a high magnified picture shows the details of primary void coalescence. This primary void-impingement-resulting coalescence process dominates the rupture processes for specimens single-heated to 1320 °C and also dominates the rupture processes in specimens which are double-heated and ended in heating to 1320 °C ( Fig. 10 (a) and (b)). The features of the fracture surfaces of FG specimens heated to 900 °C are characterized by numerous small secondary voids which connect the middle sized-primary voids before they coalesce ( Fig. 9 (c)). Specimens which are double-heated and ended in heating to 900 °C also show the increasing tendency of rupturing by connection of secondary voids ( Fig. 10 (c) and (d)). Fig. 9 (d) shows the fracture surface of the specimen heated to 730 °C. Fig. 10 (e) shows the fracture surface of a specimen double-heated to 1320 °C + 730 °C. From these two figures, an increase of secondary voids is present comparing to the specimen heated to 1320 °C only. Fig. 11 shows the details of rupture fracture surfaces (a) by connection of numerous secondary voids in FG and (b) by coalescence of large primary voids in CG Fig. 12 shows macro-metallographic morphology of the MAG weldment (a), microstructure of FG region (b), microstructure of CG region (c), macro-fracture morphology of the whole weldment (d), fracture surface of FG region (e) and fracture surfaces of CG region (f) of the actual MAG multiplayer weldment of the present steel (the detailed information is described in a sequent paper on the assessment of the toughness of the welding joint (Ref. [17] ). By comparing the microstructures and the fracture modes of the real welded joint with those of simulated specimens, it is concluded that the microstructural morphology and parameters and the fracture modes are compatible. It proves that the simulation technique used is acceptable. When the Charpy V specimen cut in a location with more coarse grain HAZ in its ligament which shows more primary void-impingement-resulting coalescence in the fracture surface, the measured toughness is higher. This observation also supports that the CG HAZ region is of higher toughness. 4 Discussion 4.1 Comparison of experimental results measured in CG-specimen and FG-specimen As seen in Tables 6, 7 and Fig. 5 , the strengths σ y and σ b at −50 °C and RT measured in tensile tests of CG-specimen are lower than those measured in FG-specimen. The plasticity in terms of ψ is also higher for FG -specimen. These results consist with the microstructures shown in Figs. 2 and 3 , which show the extreme larger grains in CG-specimen (similar to CGHAZ for welding joints as shown in Fig. 12 (c)) and middle size grains in FG (similar to FGHAZ for welding joints as shown in Fig. 12 (b)). This result can be fairly inferred from the Hall–Petch rule. However as shown in Tables 8 and 9 , the values of impact toughness measured in CG-specimen at RT and −50 °C are surprisedly higher than those measured in FG-specimen. Although from Tables 8, 9 and Fig. 6 (a), the maximum loads of Charpy V tests measured in FG-specimen are appreciably higher than those measured in CG-specimen, yet the load drops much faster with the crack propagation. It means that in the FG-specimen the resistance to the crack propagation is lower and at same applied load the deformation then the associated strain is lower than that in the CG-specimen. These phenomena make the impact toughness, particularly the crack propagation energy E p in Tables 8 and 9 being higher for the extreme coarse grain specimen. The reason, why with lower strength and plasticity in tensile test, the CG-specimen exhibits a high resistance to crack extension in Charpy V test, is analyzed in following two paragraphs. 4.2 Different micromechanisms of rupture for CG-specimen and FG-specimen Fig. 9 (a) and (b) shows the fracture surfaces of Charpy V specimen of CG. It is apparent that the ductile rupture is caused by the primary voids, which nucleate, grow until impingement-resulting coalescence and final rupture. In this case the rupture obeys the criterion of critical void growth. According to the void growth model of Rice and Tracey [18] : (1) d R R = A ⋅ e ( 3 σ m / 2 σ eq ) d ε eq the critical radius R c can be expressed [18] as (2) Ln R c R 0 = 0.283 ε f ( 3 σ m / 2 σ eq ) The fracture strain ɛ f should increase when the critical radius R c increases at same stress triaxiality σ m / σ eq . As shown in Fig. 9 (b), the critical radius R c of the primary voids grows to as large as 100 μm, close to the size of the lath bainite packets. Thus the corresponding fracture strain ɛ f should reach a higher level and provides a higher resistance to crack propagation. However for FG-specimen, as shown in Fig. 9 (c), the final rupture is caused by the shear sheets formed by numerous secondary voids, which connect the primary voids long before their impingement. Thus in FG-specimen the final rupture happens at less ɛ f , once it can produce the secondary voids to connect the primary voids before they reach to impinge. Thus the primary voids in FG grow to much smaller size ( Fig. 9 (c)) than those growing in specimen-CG ( Fig. 9 (b)). The total plastic strain, then the energy spent in fracture is less for the FG-specimen than for the CG-specimen. From Fig. 10 for double-heated specimens, the similar fracture mechanisms are present. For specimens which are subjected to the second heating to 1320 °C (1320 + 1320, 900 + 1320), the coalescence of large primary voids dominate the rupture processes ( Fig. 10 (a) and (b)) and results in the high toughness. While specimens which are subjected to the second heating to 900 °C (1320 °C + 900 °C, 900 °C + 900 °C) are ruptured by connection of small secondary voids ( Fig. 10 (c) and (d)) and show a lower toughness. From Fig. 9 , it is found that for both CG-specimen and FG-specimen, the primary voids are nucleated by inclusions, which leave black holes at the centers of the primary voids. But the original phase, which nucleates numerous small secondary voids in FG specimens cannot be identified in the fracture surfaces. Fig. 11 shows fracture surfaces in same magnification, one for FG specimen (a) and the other for CG specimen (b). In Fig. 11 (a) two primary voids (1 and 2) of 20–40 μm are connected by small secondary voids and numerous small secondary voids distribute on the fracture surface. In Fig. 11 (b), two large primary voids (100 μm in sizes) coalesce directly. Apparent plastic striations are present on void surfaces however on whole vision field no secondary void is produced. From above analyses, the key point is the production of numerous secondary voids in the FG-specimen at a lower plastic strain, while in the CG-specimen only a few of second voids are produced even at the fracture strain. Fig. 3 (a) and (b) show the optical image and SEM image of microstructures of FG-specimens. By comparing the fracture surfaces ( Fig. 9 (c) and the microstructures ( Fig. 3 (a)), it is found that the sizes of primary voids correspond to the sizes of bainite and martensite lath packets (20–30 μm) and the sizes of the secondary voids correspond to the sizes of the bainitic and martensite laths. Fig. 3 (c) and (d) shows the transmission electron micrographs of FG-specimens. Fig. 3 (c) shows the lath martensite without carbide precipitation. The martensite laths with the width in the range of 0.2–0.4 μm are considered to be much more brittle than the bainite laths. It is then inferred that the laths of the martensite are broken first and nucleate the second voids at a lower level of plastic strain, before the primary voids grow to impingement and coalescence. In Fig. 3 (b) numerous black circular points can be found in gray islands and inter-lath sites. It seems that these black points are carbide particles however it has not been identified by TEM images. In Fig. 8 , some voids on the lateral side face may be caused by these carbide particles but as shown by this figure, the secondary voids result mainly from the breaking of the matensite or bainite laths. By comparing the fracture surface ( Fig. 9 (a) and (b)) and the microstructure ( Fig. 2 (a) and (b)) of CG specimens, the primary voids correspond to the large bainitic packets. The tiny carbide plates (only 0.01 × 0.04 μm in size) precipitated inside the bainite are considered being not able to nucleate small voids. It can be concluded that although the grain sizes of CG specimens are extreme large, yet due to the high temperature (1320 °C) heating, the carbon content is unified in the original austenite grain. After fast cooling the lath bainite microstructure keeps uniform in carbon content without local accumulation. The sizes of the carbide precipitation plates inside the bainitic lath are very small (only 0.01 × 0.04 μm in size). The carbide plates with such tiny size can only be broken and nucleate the voids at a very high level of plastic strain. However, this high plastic strain cannot be reached before the coalescence of the primary voids in a notched Charpy V specimen with high stress triaxiality. And just this high stress triaxiality increases the rate of primary void growth. Though the retained austenite films observed at the lath boundaries of the CG-specimen must have some effects on the resistance to the crack propagation, yet it is not identified in the fracture surfaces of specimens fractured at RT. However, from Tables 6 and 7 , the tensile elongations measured at −50 °C are higher than those measured at RT. These results are considered to be related to the extra plasticity caused by the stress-induced phase transition from the retained austenite to the martensite at −50 °C. Further work will be carried out for investigating this phenomenon. 4.3 Effects of stress triaxiality on the nucleation and growth of the voids Tables 6 and 7 show that both the strengths at −50 °C and RT measured in tensile tests of CG-specimen are lower than those measured in FG-specimen, while the Charpy V toughness is higher. The reason is analyzed as follows: Fig. 7 shows fracture surfaces of CG-specimen (a) and (b) and that of FG-specimen (c) fractured by tensile tests at RT. Comparing Fig. 9 (a) and (b) and Fig. 7 (a) and (b) for CG-specimen, it can be found that: in the impact test, the fracture is dominated by primary voids, which grow until impingement-resulting coalescence and final rupture, while in the tensile test the final rupture is caused by the secondary voids which connect the neighboring primary voids before their impingement. In FG-specimen, the fracture surfaces for both impact test ( Fig. 9 (c)) and tensile test ( Fig. 7 (c)) show rupture being caused by the shear sheets formed by numerous secondary voids which connect the neighboring primary voids long before their impingement. Therefore, the phenomena, that the CG-specimen shows the abnormal superior impact toughness, but the inferior tensile properties, can be attributed to the change of fracture mechanisms from the primary void-coalescence in the notch impact test to the secondary void-connection in the tensile test. In Charpy V tests, the energy, which is spent on the fracture by void growing until impingement-resulting coalescence in the CG-specimen is higher than that spent in the FG-specimen where the fracture is caused by forming shear sheets of the secondary voids to connect the neighboring primary voids before their impingement. However, in tensile tests, both CG-specimen and FG-specimen are fractured with the similar mechanism of connection of the primary voids by the secondary voids. The tensile properties of the CG-specimen are inferior due to its intrinsic inferiority such as large grain size. Then the question is why for the CG-specimen, the fracture mechanism is changed from primary void coalescence in the Charpy V test to the secondary void connection in the tensile test. It is attributed to the difference of the stress triaxialities between these two types of tests. In the Charpy V impact test, due to the notch the stress triaxiality is high, up to 1.6 by FEM calculation, while in the tensile test it varies from 0.33 to approximate 1.0 from a smooth specimen to a necking one at area reduction of 65–70%. According to formula (2) Ln ( R c / R 0 ) = 0.283 ε f ( 3 σ m / 2 σ eq ) for the Charpy V specimen with a high stress triaxiality σ m / σ eq , the critical void radius R c is reached at a lower fracture strain ɛ f , which cannot cause the breaking of the tiny carbide plates precipitated inside the bainite laths or cause the breaking of the bainite laths in the CG-specimen. Therefore no (or only a few) secondary voids are produced in the fracture process ( Fig. 9 (b)). However, in the FG-specimen, the brittle martensite laths are broken at a less strain level and form numerous second voids, which connect the insufficiently growing primary voids and make an early fracture and lower toughness. In the tensile tests, the stress triaxiality is low and the plastic strain, which should be reached is high. Even, in the CG-specimen, the secondary voids can be nucleated by breaking bainitic laths ( Fig. 2 (b)) at the high plastic strain before the impingement of the primary voids. The final fracture is caused also by the connection of insufficiently growing primary voids by the second voids (As shown in Fig. 7 (a)). 5 Conclusion The abnormal high impact toughness observed in the coarse grain zone of the welding HAZ (CGHAZ) of an 8% Ni high strength steel is caused by following factors: The microstructure is dominated by the low carbon (0.03% shown in Table 2 ) uniform lath bainite without carbide particles, which is large enough to nucleate the second voids in a notched specimen. For notched impact CG-specimens the ductile rupture in the range from −50 °C to room temperature is caused by the void growth-impingement-coalescence-final rupture. There are no (or few) second phase particles that can form the shear sheets of second voids to connect the neighboring primary voids long before their coalescence. The superior toughness of CG-specimens than that of FG-specimens appears only in notched specimen due to its high stress triaxiality, where the specimen is fractured at a lower fracture strain. This strain level is lower than what needs to nucleate the voids by breaking the tiny carbide plates precipitated inside the bainitic laths or the bainite laths in CG specimens. Acknowledgements This work was financially supported by the National Nature Science Foundation of China (Nos. 50905081 , 50671047 ), National Hi-tech Research and Development Program of China (863 Program) ( 2006AA03A206 ). The authors wish to express their appreciation to Mr. Edmund for his help in English editing. The authors also wish to thank the editors and reviewers for their comments and suggestions. References [1] J. Neves A. Loureiro J. Mater. Process. Technol. 153–154 2004 537 543 [2] A. Loureiro Key Eng. Mater. 230–232 2001 31 35 [3] D. Kaplan A. Lambert-Perlade Rev. Metall. 98 10 2001 889 [4] E.F. Nippes W.F. Savage Welding J. 39 12 1949 599 616 [5] S Tamura Jpn Welding J. 28 10 1960 21 29 [6] S Tamura Jpn Welding J. 27 12 1958 723 729 [7] D. Chae C.J. Young D.M. Goto D.A. Koss Metall Mater Trans. A 32A 2001 2229 2237 [8] R.O. Ritchie B. Francis W.L. Server Metall. Trans. A 7A 1976 831 838 [9] R.O. Ritchie R.M. Horn Metall. Trans. A 9A 1978 331 341 [10] G.Y. Lai W.E. Wood R.A. Clark V.F. Zackay E.R. Parker Metall. Trans. 5 1974 1663 1670 [11] T.B. Cox J.R. Low Metall. Trans. 5 1974 1457 1470 [12] Yaowu Shi Zhunxiang Han J. Mater. Process. Technol. 207 2008 30 39 [13] Jixiang Peng Tianhong Zhang Wanping Deng Junxu Zhang Trans. China Welding Inst. 28 3 2007 105 108 (in Chinese) [14] C.L. Davis J.E. King Mater. Sci. Technol. 9 1993 8 15 [15] J.-i. Jang J.-B. Ju B.-W. Lee D. Kwon W.-S. Kimc Mater. Sci. Eng. A 340 2003 68 79 [16] V.T.T. Miihkinen D.V. Edmonds Mater. Sci. Technol. 3 1987 432 440 [17] R. Cao, W. Feng, W.S. Du, Z.L. Tian, Y. Peng, J.H. Chen, Effects of weld metal property and fraction on the toughness of welding joints of a 8%Ni 980 MPa high strength steel, J. Mater. Process. Technol., submitted for publication. [18] J.R. Rice T.M. Tracey J. Mech. Phys. Solids 21 1978 395 410
更多查看译文
关键词
8%Ni high strength steel,Heat affected zone,Impact toughness,Ductile fracture
AI 理解论文
溯源树
样例
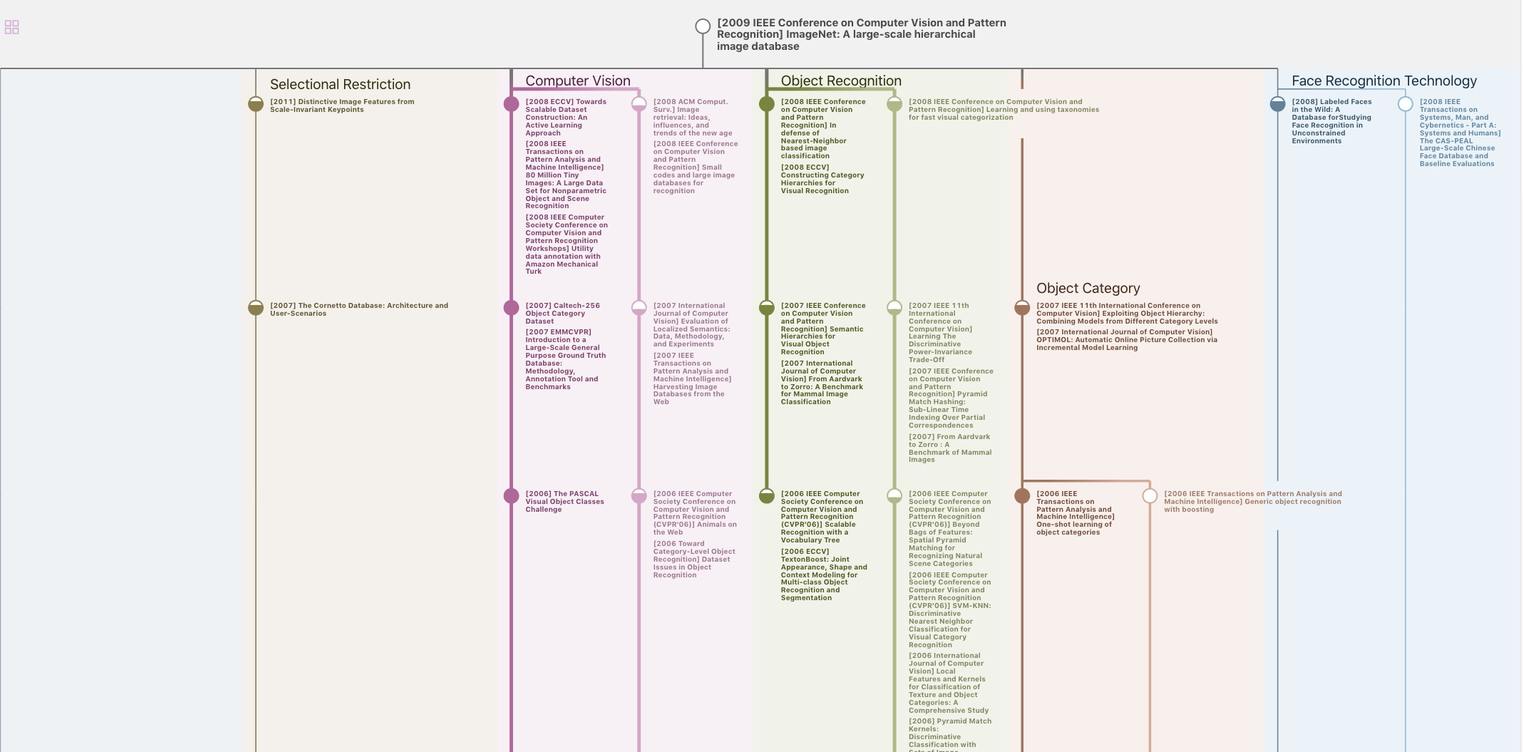
生成溯源树,研究论文发展脉络
Chat Paper
正在生成论文摘要