Recycling of the product of thermal inertization of cement–asbestos for the production of concrete
Construction and Building Materials(2011)
摘要
A novel field of research in materials science is the recycling of secondary raw materials for construction and building materials such as concrete. This paper describes the successful recycling of as much as 20 wt% of the product of thermal transformation of cement–asbestos for the formulation of concrete. The main mineralogical phases present in the product of transformation of cement–asbestos are C2S, ferrite, and Al-, Ca-, Mg-rich silicates such as akermanite (ideally Ca 2 MgSi 2 O 7 ) and merwinite (ideally Ca 3 Mg 2 Si 2 O 8 ). The behavior of this secondary raw material, termed KRY·AS, in commercial concrete was investigated using five different mixtures in which various portions (0, 5, 10, 15 and 20 wt%) of cement were substituted by KRY·AS. The results of preliminary technological tests (slump test, compressive strength, flexural strength after 28 days, and depth of penetration of water under pressure after 28 days) were discussed and interpreted with the aid of chemical, mineralogical and SEM analyses. One of the major results is that after 28 days, although all the concrete samples are invariably classified as “ordinary concrete” according to the UNI 6132 tests, those diluted with KRY·AS display a lower resistance to compression with respect to the standard. On the other hand, they recover compressive strength and display values identical to that of the standard after 90 days. The addition of the secondary raw material has the effect to slow down the kinetics of setting/hardening because the main cement phase present in KRY·AS is C2S which has a slower rate of hydration with respect to C3S. Keywords Concrete Recycling Cement Rietveld method SEM 1 Introduction By definition, concrete is a construction material consisting of sand, conglomerate gravel, pebbles, broken stone, or slag in a mortar or cement matrix. It is the most widely used construction material and is in principle man made geology [1] . Cement aggregates are sedimentary or crushed, natural rocks. The mixing, placing, compaction, curing, and the subsequent gradual alterations in hardened concrete during its service life are akin to geological processes in nature, albeit in an accelerated and monitored technology fashion. The pioneers of the Portland cement development in the 19th century realized this basic nature of cement and concrete [1] . Modern concrete is more than simply a mixture of cement, water, and aggregates. It often contains mineral components with specific characteristics that give peculiar properties to concrete, or chemical admixtures that have even more specific effects. Consequently, modern concrete may be a very complex chemical material where mineral products and amorphous products interact with organic molecules or polymers [2] . The science of concrete is only beginning to develop and it should be expected that in the years to come, new types of concretes that fulfill different socio-economic needs will be developed [2] . In this scenario, an appealing field of research and development in concrete science/industry is the recycling of secondary raw materials. The recycling of industrial wastes in the concrete manufacturing is of increasing interest worldwide, due to the high environmental impact of the cement and concrete industries and to the rising demand of infrastructures, both in industrialized and developing countries [3] . Since Agenda 21 (Rio Declaration on Environment and Development) was launched in 1992, sustainable development has been a key issues of modern society. The recycling of construction and demolition waste (C&D waste) has emerged as a socioeconomic priority within the European Union and a considerable amount of research and development has taken place in the frame of RILEM ( the international union of testing and research laboratories for materials and structures ) [4] . The increased need for alternative solutions to disposal in landfills, prompted recycling of both hazardous and non-hazardous wastes as secondary raw materials. Recycling is promoted by the recent European Directive 2008/98/EC of 19-11-2008 and in Italy by the Italian D.Lgs 152, 03-04-2006 “ Codice ambientale ”. Thus, the time has come to find suitable and economically viable recycling solutions. As far as concrete is concerned, the literature reports nearly an endless number of interesting application of secondary raw materials recycled for the production of concrete. The recycling of concrete demolition wastes has already been well illustrated: see for example Ref. [5] . The recycling of demolished masonry rubble as coarse aggregate in concrete [6] represents an interesting possibility at a time when the cost of dumping such material is increasing. The development of concrete bricks and paving blocks using recycled aggregates obtained from construction and demolition waste has also been explored by Poon et al. [7] . Natural stone slurry was used to successfully replace fine aggregates in concrete mixtures [8] . The possibility of making concrete tough by introducing rubber phases among the traditional components prompted the use of recycled grinded tire rubbers for this purpose [9] . Bertolini et al. [3] studied the effect of replacing part of Portland cement with fly ash and bottom ash recovered from municipal solid waste incinerators (MSWIs). Fly ash was subjected to a washing treatment to reduce the chloride content, while bottom ash was subjected to dry or wet grinding underwater. Ferreira et al. [10] also investigated the recycling of solid waste fly ash for the production of cement and concrete. Batayneh et al. [11] described the recycling of ground plastics and glass to replace up to 20% of fine aggregates in concrete mixes, while crushed concrete was used to replace up to 20% of coarse aggregates. An important hazardous waste in Italy is asbestos containing material (ACM). Although asbestos is banned in Italy since 1992, ACM may still be easily found in the environment. For example, approximately 2 billion m 2 of cement–asbestos slates still cover roofs of industrial plants and civil buildings [12] . Because all slates invariably show signs of surface degradation [13] , they have to be removed sooner or later as physical–chemical degradation of the slates in the outdoor environment eventually results in the release of asbestos fibers [14,15] . The awareness of the health-threat of asbestos prompted policy of abatement and disposal of ACM in controlled landfills. However, this cannot be regarded as the ultimate solution as a zero risk of fiber dispersion in air and water cannot be guaranteed. An alternative solution is the thermal transformation of ACM into non-hazardous products, and safe recycling as secondary raw material [16] . This alternative to landfill disposal is a viable solution in Italy thanks to the law no. 248 (D.M. 19/07/2004) which legitimates the thermal destruction of asbestos containing wastes and the recycling of the product of transformation. Recently, an industrial process for the thermal destruction of asbestos containing wastes, mainly cement–asbestos, has been developed and patented [16] . The product of the thermal inertization at 1200 °C is mainly composed of SiO 2 and CaO (about 40 wt% each). Having reassured the non-hazardous nature of KRY·AS [17] , the current challenge is to find suitable recycling solutions. Previous works have shown that KRY·AS can be successfully recycled in the production of construction and building materials such as stoneware tiles [16] , clay bricks, glasses, glass–ceramics, ceramic frits, ceramic pigments and plastic materials [18] . Because it is mainly composed of calcium and silica, the use of KRY·AS as CO 2 -free source of Ca in place of Ca-carbonates permits to reduce the CO 2 emissions during the industrial manufacture processes. In fact, the production of 1 t of cement releases about 374 kg of CO 2 whereas the production of 1 t of KRY·AS (via thermal transformation of cement–asbestos which contains about 50 wt% calcite) releases about 250 kg of CO 2 . Recycling of cement–asbestos for the production of cement has been already attempted in the past [19,20] and a process for the direct use of milled cement–asbestos as raw material for the production of cement was patented [21] . In that patented process, cement–asbestos was ground to meal and fed to the flame zone of a rotary kiln of cement clinker production line. This paper describes the recycling of a secondary raw material named KRY·AS (the product of the thermal inertization of cement–asbestos at 1200 °C) in place of cement for the production of a commercial concrete. The results of the technological tests are discussed in terms of quantitative mineral composition and microstructure. 2 Experimental 2.1 Materials The secondary raw material used in this study (KRY·AS) was prepared by prolonged thermal treatment of a standard sealed pack of 61 cement–asbestos slates removed from an industrial site. The size of each corrugated slate was 122 × 57 × 1 cm. The pack was placed in a discontinuous industrial kiln and exposed to a temperature ramp with a total duration of 40 h, including a 21 h long isothermal step at 1200 °C. The characterization of the untreated slates and KRY·AS as well as details of the firing cycle are extensively described in [16] . The high temperature transformation of cement–asbestos prompted the formation of cement phases such as C2S and ferrite (ideally Ca 4 Al 2 Fe 2 O 10 ), and Al-,Ca-,Mg-rich silicates such as akermanite (ideally Ca 2 MgSi 2 O 7 ) and merwinite (ideally Ca 3 MgSi 2 O 8 ). The cement used in this study is a commercial product (Normal Cement CEM II/A – L, Class 42.5 N). The aggregate used to formulate the concrete mixture is a two components (sand 53 wt% and gravel 47 wt%) natural Italian commercial product. Both the sand and the gravel are composed of quartz and feldspars with minor calcite, illite/muscovite, chlorite and amphibole. For both the sand and the gravle, the water absorption is <3 wt%. The aggregate size distribution is reported as the wt% passing through a sieve with opening expressed in mm. Sand: 1.4 wt% 0.125 mm, 3.7 wt% 0.25 mm, 40.4 wt% 0.5 mm, 62.1 wt% 1 mm, 71.1 wt% 2 mm, 77.2 wt% 4 mm, 79.5 wt% 5.6 mm, 81.8 wt% 6.3 mm, 90.4 8 wt% 8 mm, 98 wt% 10 mm, 100 wt% 11.2 mm. Gravel: 0.6 wt% 0.125 mm, 1.2 wt% 0.25 mm, 1.4 wt% 0.5 mm, 1.6 wt% 1 mm, 1.8 wt% 2 mm, 2.2 wt% 4 mm, 2.9 wt% 3.5 mm, 3.5 wt% 6.3 mm, 5.9 wt% 8 mm, 17.6 wt% 10 mm, 29.5 wt% 11.2 mm, 43.7 wt% 12.5 mm, 57.9 wt% 14 mm, 76.2 wt% 16 mm, 95.4 wt% 20 mm, 99.5 wt% 22.4 mm, 100 wt% 25 mm. The batches of KRY·AS and cement were characterized with chemical and mineralogical analyses. Chemical analyses were performed using X-ray fluorescence spectroscopy (Philips PW2480). Loss of ignition was determined by calcination at 1050 °C. X-ray powder diffraction (XRPD) data for qualitative and quantitative phase analyses were collected using a Philips PW 1730 instrument with a Ni-filtered Cu Kα radiation generated with 40 kV and 30 mA. Divergence and receiving slits of 1/2° were applied. A step scan of 0.02°2 θ was performed using a counting statistics of 10 s/step. Samples for XRPD measurements were hand ground in agate mortar and mounted in Al sample holders using a side-loading technique. The quantitative phase analyses were performed using the Rietveld method [22] . The refinements were accomplished with the GSAS [23] package and its graphical interface EXPGUI [24] . For full quantitative analyses (i.e. determination of both crystalline and glass content) using the combined Rietveld-RIR method [25] , 10 wt% corundum (NIST 676) was added to the sample and included in the refinements. 2.2 Technological tests To investigate the behavior of KRY·AS in a commercial concrete mixture, five different mixtures were prepared: (1) standard: cement 15 wt%, water 8.6 wt%, aggregate 76.4 wt%; (2) 5 K: cement 14.25 wt%, KRY·AS 0.75 wt%, water 8.6 wt%, aggregate 76.4 wt%; (3) 10 K: cement 13.5 wt%, KRY·AS 1.5 wt%, water 8.6 wt%, aggregate 76.4 wt%; (4) 15 K: cement 12.75 wt%, KRY·AS 2.25 wt%, water 8.6 wt%, aggregate 76.4 wt%; (5) 20 K: cement 12.0 wt%, KRY·AS 3.0 wt%, water 8.6 wt%, aggregate 76.4 wt%. No organic/inorganic additives were added to the cement paste. The rheological properties of the pastes were determined with the Abrams cone test (slump test: UNI EN 206-1). The following technological tests were performed on the hardened concrete blocks: – Determination of the compressive strength (UNI EN 12390-3:2003) after 3 days, 7 days, 28 days, 60 days and 90 days. – Determination of the flexural strength (UNI EN 12390-5:2002) after 28 days. – -Determination of the depth of penetration of water under pressure (UNI EN 12390-8:2002) after 28 days. 2.3 Mineralogical tests To better understand the evolution of the system during the hydration and setting stages, the microstructure of each sample (standard, 5 K, 10 K, 15 K, and 20 K) was investigated by Scanning Electron Microscopy (SEM), using a Philips XL-40 instrument equipped with secondary and backscatter electron (SE and BSE, respectively) detectors after 0, 3, 7, 28, 60, and 90 days. In addition, an energy dispersive X-ray fluorescence spectrometer (EDS) system attached to the instrument allowed to collect chemical compositional data. Besides the real samples subject to the technological characterization, three additional sample batches were prepared to investigate in detail the evolution of the cement + KRY·AS system during the hydration and setting stages. The three sample batches were prepared without the inert phase: (1) standard: cement 100 wt% + water; (2) 10 K: cement 90 wt% and KRY·AS 10 wt% + water; (3) 20 K: cement 80 wt% and KRY·AS 20 wt% + water. For each sample, the evolution of the system was investigated after 0, 3, 7, and 28 days. The microstructure of the samples was investigated by SEM under the very same conditions described above. XRPD data for the quantitative phase analysis of the evolving systems were collected using a θ / θ diffractometer (PANalytical, Cu Kα radiation, 40 kV and 40 mA), equipped with a real time multiple strip (RTMS) detector. Divergence and anti-scattering slits of 0.125° and 0.25°, respectively, was mounted in the incident beam pathway. The pathway of the diffracted beam included a Ni filter, a soller slit (0.02 rad) and an antiscatter blade (5 mm). A virtual step scan (0.0167°2 θ ) was used. For all XRPD measurements, the samples were hand ground in agate mortar and mounted in aluminum sample holders using a side-loading technique. The quantitative phase analyses were performed using the methods described above in Section 2.1 . 3 Results and discussion Fig. 1 shows the graphical output of the Rietveld refinement of the raw materials used for the preparation of the concrete mixtures and Table 1 the Rietveld agreement factors and relative weight estimates. The batch of KRY·AS used for the study contains β-larnite (C2S) as main mineralogical phase and other minor phases such as ferrite, periclase, quartz, and Ca-, Mg–silicates such as akermanite and merwinite. The main differences between cement and KRY·AS are that the latter is higher in Mg and C2S. KRY·AS can be considered to be comparable to a low temperature cement aggregate [26] . The Normal Cement CEM II/A – L used here contains about 20 wt% calcite (see Table 1 ). It is likely that a minor fraction of calcite is due to carbonation of the cement in contact with air. This process seems to be highly correlated with the air permeability of the cement [27] . Amorphous phase is observed in both KRY·AS and cement. Although still matter of debate, the presence of amorphous phase in cements has already been reported in the literature [28] . Figs. 2–4 report a gallery of high magnification SEM images of selected samples (standard, 10 K, and 20 K in Figs. 2–4 , respectively) taken during the setting/early hardening time (3, 7, 28, and 60 days). Spot chemical analysis (EDS) were collected to help the identification of the observed crystalline phases but are not reported here for sake of clarity. After 3 days, the standard shows the presence of both well formed acicular ettringite crystals and portlandite platelets ( Fig. 2 , 3 days). On the other hand, although they are clearly visible in the SEM images (see Figs. 3 and 4 , 3 days), the formation of large ettringite and portlandite crystals seems to be somehow inhibited in the mixtures diluted with KRY·AS. This indicates that the addition of KRY·AS may alter the setting/hardening behavior. As a matter of fact, the main phase present in KRY·AS is C2S with a notorious slower rate of hydration with respect to C3S [29–31] . After 7 days, large ettringite crystals are still observed in the standard mixture ( Fig. 2 , 7 days). This is not the case for the KRY·AS diluted samples. On the other hand, large portlandite crystals are observed later for both 10 K and 20 K mixtures ( Figs. 3 and 4 , 7 days). The inhibition of ettringite formation in C2S-rich cements has already been reported in the literature: Fitkos and Philipou found that most of the sulfates in hydrated cement rich in C3S are in the form of ettringite, while a part of the ettringite is transformed to monosulphate for hydrated cement rich in C2S [32] . During the hardening time, C–S–H with a tobermorite structure begins to form. These crystals, with their typical elongated habit, are clearly visible in all the mixtures ( Figs. 2–4 , 28 and 60 days). It was not possible to assess whether the observed crystal habit of the C–S–H phase is a precursor to type I C–S–H. In agreement with Zampini et al. [33] , the “sheaf of wheat” crystal habit appears to be a general precursor to morphologies commonly seen in mature cements. The calcium silicate hydrate (C–S–H) phase often accompanied by large portlandite crystals even in the KRY·AS diluted concrete samples. The evolution of the crystal morphology and microstructure of the cements is confirmed by the results of the XRPD study (see Table 2 and Fig. 5 ). Table 2 displays the results of the quantitative phase analyses of the samples at different setting stages with the standard deviations on the weight estimates calculated according to Larson and von Dreele [23] . Fig. 5 shows the evolution of the main mineralogical phases. Cement hardening is accompanied by hydration of C2S and C3S phases and formation of the paracrystalline/semi-amorphous C–S–H phase. The calculated amorphous phase plotted in Fig. 5 a includes the C–S–H phase. The trends and relative amounts of amorphous phase formed after 28 days are comparable to the values reported by Scrivener et al. [34] . If we apply the same stoichiometric calculation reported in [34] , the amount of C–S–H formed can be estimated from the amount of anhydrous silicate phases C3S and C2S consumed according to the reactions: C3S + 5.3H → C1.7SH4 + 1.3CH and C2S + 4.3H → C1.7SH4 + 0.3CH. After 28 days, in the standard concrete mixture, 27 out of 45 wt% of amorphous phase is actually C–S–H (19.3 wt% and 7.7 wt% from the consumed 19.6 wt% C3S and 5.8 wt% C2S, respectively). The addition of KRY·AS to the standard mixture determines an increase of the amount of C2S at expenses of the C3S phase ( Fig. 5 a). The amount of C–S–H determined by stoichimetric calculation from C3S and C2S consumption in the mixture richer in KRY·AS (20 K) is 28.2 wt% (17.1 wt% from the consumption of 17.2 wt% C3S and 11.1 wt% from the consumption of 8.4 wt% C2S, respectively). Despite the amount of C–S–H in the 10 K and 20 K mixture is comparable to that of the standard mixture, the overall amount of amorphous phase increases after 28 days of setting/hardening. (49 wt% in 10 K, 50 wt% in 20 K) with respect to the standard (45 wt%). The larger amorphous fraction may be related to the formation of a hydrotalcite-like phase of very low crystallinity from the hydration of the Mg-rich phases (such as periclase) conveyed by KRY·AS in the reacting system. Such pseudo-amorphous hydrotalcite-like phases are commonly formed by hydration of slag cements [29,35] . These phases have a composition similar to meixnerite Mg 0.75 Al 0.25 (OH) 2 (OH) 0.25 (H 2 O) 0.5 K 30 , which may also occur as mineral phase [29] . Pytel and Malolepszy [36] and Fernandez et al. [37] identified the possible incorporation of Mg into the C–S–H structure and observed a new phase attributed to the formation of a magnesium silicate hydrate (M–S–H), but its structure is still unknown [38] . Because the amount of ferrite in the starting 10 K and 20 K mixtures is higher, it is possible that a minor fraction of the amorphous phase is actually an AFm phase formed during the hardening time at expenses of ferrite (see the decrease of the weight estimate of ferrite with time in Fig. 5 a). The AFm phases C4(A,F) X 2 × n H 2 O, where X denotes one formula unit of a single charged anion, occurring in cements are mineralogically and chemically complex. Its layer structure incorporates variable amounts of water as well as anions such as hydroxyl, sulfate, silicon, aluminate, or carbonate. Solid solutions between hydroxy- and sulfate- AFm and Al- and Fe-containing compounds are extensive [26,39] . Fig. 5 b shows a decrease of calcite with time, presumably because of the formation of low-crystallinity calcium mono-carbo-aluminate [39] . This trend is similar to that observed by Lothenback and Winnefeld [39] who studied the hydration of Portland cement. In agreement with the literature data [26] , portlandite also slowly forms during hardening but its weight estimate after 28 days is twice as high in the standard with respect to the 20 K mixture ( Fig. 5 a and Table 2 ). Again this should be due to a larger amount of amorphous fraction (C–S–H + hydrotalcite? + AFm ?) formed in place of portlandite in the Mg-rich KRY·AS mixtures. For different systems, literature reports that magnesium oxide would hinder the precipitation of portlandite [38] as competing reaction paths are observed in the presence of Mg. The latter drives the formation of brucite-like phases precursors of hydrotalcite instead of portlandite [26] . The SEM study performed on samples after 28 days of hardening time, invariably showed the presence of some spherical aggregates with a mean diameter of about 15–30 μm in the concrete mixtures. A SEM image of a typical aggregate with the relative EDS spectra is shown in Fig. 6 . Their chemistry is extremely heterogeneous and does not seem to be related to a single mineralogical phase. According to the model proposed by Coppola [40] , their origin is due to the synergetic action of different factors. Concrete possesses an intrinsic porosity due to the shrinkage of the gel phase, capillarity and air bubbles. Such pores become interconnected because of the formation of connected fractures during the hardening period (open porosity). Water rich in ions of different nature, evaporating through such preferential channels, deposits its ion load in the pores. When oversaturation of the solution is reached, precipitation and formation of such crystalline or pseudo-crystalline spherical aggregates is promoted. Such spherical aggregates have already been observed and described in the literature see for example Refs. [41–43] . Table 3 reports the results of the slump test which gives a semi-quantitative indication on the rheology of the system. This standard Abrams cone test (UNI EN 206-1) defines the following classes: S1: humid (Δ h 10–40 mm); S2: plastic (Δ h 50–90 mm); S3: semi-liquid (Δ h 100–150 mm); S4: liquid (Δ h 160–210 mm); S5: super-liquid (Δ h ⩾ 220 mm). All the samples are classified as S4 (fluid) but sample 10 K (semi-liquid) indicating a very good workability of the cement mixtures according to the UNI EN 206-1 standards. We believe the slight discrepancy observed for sample 10 K with respect to the others is likely due to practical problems during the test such as the determination of the relative lowering of the cement mass which may be affected by some degree of subjectivity. The time-dependence of the compressive strength of the concrete samples determined strictly following the standard rules UNI EN 12390-3:2003 which also permits the calculation of the standard deviation (see the determination of the precision in the related standard rules ISO 5725-1) is reported in Table 4 , and plotted in Fig. 7 . The compressive strength obviously increases with hardening time and reaches values as high as 30 MPa after 90 days for all the samples. After 28 days, the hardening time used for the classification of the concrete material, the samples diluted with KRY·AS display a lower resistance to compression with respect to the standard ( Table 4 and Fig. 7 ). Notwithstanding, all the samples are classified as “ORDINARY” (C25/30 for the standard and 5 K, C20/25 for the 10 K, and C16/C20 for the 15 K and 20 K, respectively) according to the UNI 6132 tests. With time, the samples diluted with KRY·AS recover compressive strength and display values close to that of the standard ( Fig. 7 ) after 90 days. As already pointed out, the addition of KRY·AS slows down the kinetics of setting/hardening because the main cement phase present in KRY·AS is C2S which has a slower rate of hydration with respect to C3S [29] . The C2S hydration process is characterized by an extended induction period in which the hydration rate is very slow [44] . The slower kinetics of hydration of C2S with respect to C3S reflects in the observed trend of the compressive strength with hardening time [26] which shows that the contribution to compressive strength of C2S at earlier hardening period is very low with respect to that of C3S. However, C2S recovers with time and the compressive strengths of the cements become comparable. This model applies here for the C2S-rich KRY·AS diluted samples which display a compressive strength identical to that of the standard only after longer hardening times ( Fig. 7 ). Table 5 and Fig. 8 reports the values of the flexural strength which were measured after 28 days according to the UNI EN 12390-5:2002 standard test. Because there is no standard determination of the precision for this method, the standard error of each measure was calculated as σ = σ x / N with N = number of measured samples. The same reasons invoked to interpret the results of the compressive strength apply here. After 28 days, the action of KRY·AS, as retardant of the hardening process, determines lower but still acceptable values of flexural strength in the concrete samples 10–20 K. According to the classification of concrete based on the values of the flexural strength, sample 20 K with the highest content of KRY·AS should be classified in the T2.5 class. The result of the test for the measurement of the penetration depth of water in the concretes is depicted in Fig. 9 . All the values are considered acceptable on from an applicative standpoint. However, it is clear that the penetration depth increases linearly with the KRY·AS addition in the concrete mixture, indicating an increase of the open porosity and permeability of the concrete test blocks. It is difficult to evaluate the effect of concrete porosity on its resistance to degradation. In determining the rate of infiltration of an aggressive medium into concrete, the distribution of the pores in the cement portion of this composite has to be considered, especially their size and connectivity. In concrete, this pore structure is affected by the presence of the aggregate [45] . Besides that, we have seen that the KRY·AS C2S-rich diluted systems evolve later to yield mechanical resistances comparable to that of the standard and hence it is not possible here to predict if and to which extent such permeability may favor later chemical attack (e.g. chloride penetration). 4 Conclusions This work has demonstrated that the recycling of the product of thermal inertization of an hazardous waste such as cement–asbestos (termed KRY·AS) in concrete is very promising. Landfills for disposal of asbestos containing wastes are avoided because the product of transformation of asbestos containing wastes is no longer a waste to be disposed but a safe secondary raw material. The secondary raw material can be used in place of cement. This implies a reduction of the request for natural raw materials such as calcium carbonate with a limitation of the environmental impact caused by the extraction of the minerals from quarries and mines. Besides that, the substitution of the product of transformation of cement–asbestos for the commercial cement (CEM II/A – L in this study) in concrete allows to reduce the CO 2 emission in the environment caused during the cement production. The successful recycling of quantities as large as 20 wt% of KRY·AS in place of cement in commercial concrete is accompanied by a significant reduction of the cost of the concrete. If we assume that the cost of an ordinary commercial cement in Italy is about 100 €/t, the use of 20 wt% KRY·AS, whose commercial value is around 30 €/t, in place of cement permits to save 14 €/t. According to the UNI EN 206-1:2006 regulation, a concrete product diluted with as much as 20 wt% KRY·AS with the features the described in this paper may be utilized for: (i) indoor environments with very low moisture content; (ii) as reinforced concrete injected in chemically inert soil or unaggressive water; (iii) as unreinforced concrete under periodical dry/wet cycles but not subject to abrasion, frost nor chemical attack; (iiii) component of liquid storage tanks or foundations. The preliminary results of the technological tests presented in this work will be further strengthened by investigations on durability such as volume stability, porosity, and permeability of hardened concrete produced with KRY·AS. Acknowledgements ZETADI s.r.l. has granted the project within a long term cooperation agreement with the Earth Sciences Dept., The University of Modena and Reggio Emilia, Italy. Cave di Lonate Pozzolo s.r.l., Lonate Pozzolo (VA, Italy) is a partner in the project and provided the raw materials for the formulation of the concretes. Tecno Piemonte S.p.A., Romagnano Sesia (NO, Italy) is acknowledged for the technological tests on the concretes. M. Bortolotti is kindly acknowledged for support in lab activities. The staff of the Centro Interdipartimentale Grandi Strumenti (CIGS) of the University of Modena and Reggio Emilia is greatly acknowledged for support during the SEM and diffraction experimental sessions. M. Lassinanantti Gualtieri is acknowledged for useful discussions and critical revision of the first draft of the manuscript. We thank two anonymous referees for their comments and suggestions which improved the quality of the manuscript. References [1] G.M. Idorn Innovation in concrete research—review and perspective Cement Concr Res 35 2005 3 10 [2] P.C. Aïtcin Cements of yesterday and today. Concrete of tomorrow Cement Concr Res 30 2000 1349 1359 [3] L. Bertolini M. Carsana D. Cassago A.Q. Curzio M. Collepardi MSWI ashes as mineral additions in concrete Cement Concr Res 34 2004 1899 1906 [4] Hansen Torben C. Proceedings of the EDA – RILEM international symposium on re-use of concrete and brick materials; June 1985. [5] Torring M. Management of concrete demolition wastes. In: Odd E, Gjørv, Koji Sakai, editors. Concrete technology for a sustainable development in the 21st century; 2000 E&FN Spon. ISBN 0-419-25060-3. [6] F.M. Khalaf A.S. DeVenny Recycling of demolished masonry rubble as coarse aggregate, concrete: review J Mater Civ Eng 16 4 2004 331 340 [7] C.S. Poon S.C. Kou L. Lam Use of recycled aggregates in molded concrete bricks and blocks Construct Build Mater 16 2002 281 289 [8] N. Almeida F. Branco J.R. Santos Recycling of stone slurry in industrial activities: application to concrete mixtures Build Environ 42 2007 810 819 [9] M.C. Bignozzi F. Sandrolini Tire rubber waste recycling in self-compacting concrete Cement Concr Res 36 2006 735 739 [10] C. Ferreira A. Ribeiro L. Ottosen Possible applications for municipal solid waste fly ash J Hazard Mater B96 2003 201 216 [11] M. Batayneh I. Marie I. Asi Use of selected waste materials in concrete mixes Waste Manage 27 2007 1870 1876 [12] Gualtieri AF, Elmi G. Understanding the high temperature reaction sequence during the thermal treatment of cement–asbestos slates. In: Proceedings of the European conference on asbestos risks and management ARAM, Rome; 4–6 December, 2006. [13] A.F. Gualtieri D. Mangano M. Lassinantti Gualtieri A. Ricchi E. Foresti G. Lesci Ambient monitoring of asbestos in selected Italian living areas J Environ Manage 90 2009 3540 3552 [14] Babic BR. The use of cement fibre composites in prolonged wet environments. In: 10th international inorganic-bonded fiber composites conference, Curran associates, São Paulo; 2006. p. 260–73. [15] C.M.R. Dias M.A. Cincotto H. Savastano Jr. V.M. John Long-term aging of fiber–cement corrugated sheets—the effect of carbonation, leaching and acid rain Cement Concr Compos 30 2008 255 265 [16] A.F. Gualtieri C. Cavenati I. Zanatto M. Meloni G. Elmi M. Lassinantti Gualtieri The transformation sequence of cement–asbestos slates up to 1200 °C and safe recycling of the reaction product in stoneware tile mixtures J of Hazard Mater 152 2008 563 570 [17] F. Giantomassi A.F. Gualtieri L. Santarelli M. Tomasetti G. Lusvardi C. Lucarini Biological effects and comparative cytotoxicity of thermal transformed asbestos-containing materials in a human alveolar epithelial cell line Toxicol In Vitro 24 6 2010 1521 1531 [18] A.F. Gualtieri C. Giacobbe L. Sardisco M. Saraceno M. Lassinantti Gualtieri G. Lusvardi Recycling of the product of thermal inertization of cement–asbestos for various industrial applications Waste Manage. 31 2011 91 100 [19] S. Ambrosius H. Gundlach J. Kieser Thermal utilization of cement-bound asbestos products in cement kilns ZKG Int 49 8 1996 444 453 [20] S. Sprung V. Hoenig C. Schneider S. Gajewski Environmentally compatible utilization of asbestos cement products ZKG Int 51 10 1998 527 541 [21] Gleichmar G, Kieser J, Ambrosius S, Görmar H, Krähmer A, Buhrandt WJ. Process of treatment and environment friendly utilization of asbestos cement products. US Patent nr. 5676,750; October 14th, 1997. [22] H.M. Rietveld Profile refinement for nuclear and magnetic structures J Appl Crystallogr 2 1969 65 71 [23] Larson AC, von Dreele RB. GSAS generalized structure analysis system, Laur 86-748, Los Alamos National Laboratory, Los Alamos, New Mexico; 1994. [24] B.H. Toby EXPGUI, a graphical user interface for GSAS J Appl Crystallogr 34 2001 210 213 [25] A.F. Gualtieri Accuracy of XRPD QPA using the combined Rietveld-RIR method J Appl Crystallogr 33 2000 267 278 [26] Taylor HFW. Cement chemistry. Ed. Academic Press; 1990. p. 475. [27] L.J. Parrot Some effects of cement and curing upon carbonation and reinforcement corrosion in concrete Mater Struct 29 3 1996 164 173 [28] P.S. Whitfield L.D. Mitchell Quantitative Rietveld analysis of the amorphous content in cements and clinkers J Mater Sci 38 2003 4415 4421 [29] H. El-Didamony A.M. Shararab I.M. Helmy S. Abd El-Aleem Hydration characteristics of β-C2S in the presence of some accelerators Cement Concr Res 26 8 1996 1179 1187 [30] D. Menetrier D.K. McNamara I. Jawed J. Skalny Early hydration of β-C 2 S: surface morphology Cement Concr Res 10 1980 107 110 [31] Brunauer S, Greenberg SA. The hydration of tricalcium silicate and β-dicalcium silicate at room temperature. In: Proceedings 4th international symposium of chemistry of cement, vol. 43, no. 1, Washington; 1962. p. 135–41. [32] C. Ftikos T. Philippou Preparation and hydration study of rich C2S cements Cement Concr Res 20 1990 934 940 [33] D. Zampini S.P. Shah H.M. Jennings Early age microstructure of the paste-aggregate interface and its evolution J Mater Res 13 7 1998 1888 1898 [34] K.L. Scrivener T. Füllmann E. Gallucci G. Walenta E. Bermejo Quantitative study of Portland cement hydration by X-ray diffraction/Rietveld analysis and independent methods Cement Concr Res 34 2004 1541 1547 [35] A.M. Harrisson N.B. Taylor Microstructure and microchemistry of slag cement pastes Mater Res Soc Symp Proc 85 1987 213 222 [36] Pytel Z, Malolepszy J. The role of MgO in the synthesis of CSH and tobermorite. In: Justnes H, editor. Proceedings international congress of the chemistry of cements, 10th, Amarkai AB, Goeteborg; 1997. [37] L. Fernandez C. Alonso A. Hidalgo C. Andrade The role of magnesium during the hydration of C3S and C–S–H formation. Scanning electron microscopy and mid-infrared studies Adv Cement Res 17 1 2005 9 21 [38] L. Fernandez C. Alonso C. Andrade A. Hidalgo The interaction of magnesium in hydration of C3S and CSH formation using 29 Si MAS-NMR J Mater Sci 43 2008 5772 5783 [39] B. Lothenbach F. Winnefeld Thermodynamic modelling of the hydration of Portland cement Cement Concr Res 36 2006 209 226 [40] L. Coppola Calcestruzzi Resistenti al Gelo. Passato, Presente, Futuro L’Industria Italiana del Cemento 689 1994 438 452 [in Italian] [41] G.M. Idorn Expansive mechanisms in concrete Cement Concr Res 22 6 1992 1039 1046 [42] Petrov N. Effets combinés de différents facteurs sur l’expansion des bétons causée par la formation différée de l’ettringite, Ph.D. thèse, Université de Sherbrooke; 2003. [43] Petrov N, Tagnit-Hamou A. Is Microcracking really a precursor to DEF and consequent expansion? In: Sixth CANMET/ACI international conference on recent advances in concrete technology, Bucharest (Bulgaria); 2003. p. 405–20. [44] Hewlett PC. Lea’s chemistry of cement and concrete. 4th ed. Elsevier ltd.; 2004. p. 1092. [45] P. Halamickova R.J. Detwiler D.P. Bentz E.J. Garbocz Water permeability and chloride ion diffusion in Portland cement and mortars: relationship to sand content and critical pore diameter Cement Concr Res 25 4 1995 790 802
更多查看译文
关键词
Concrete,Recycling,Cement,Rietveld method,SEM
AI 理解论文
溯源树
样例
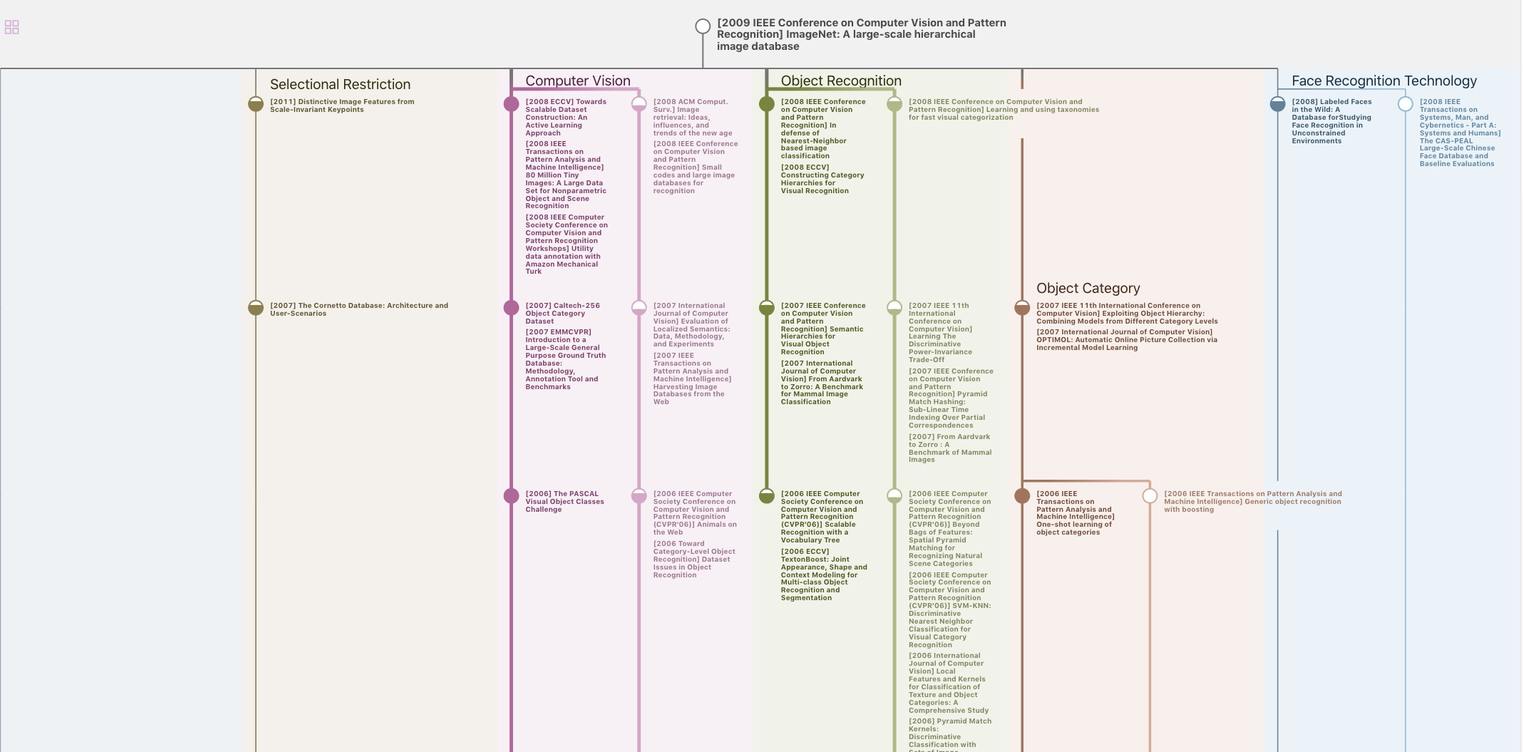
生成溯源树,研究论文发展脉络
Chat Paper
正在生成论文摘要