(Re)Designing for Part Consolidation: Understanding the Challenges of Metal Additive Manufacturing
JOURNAL OF MECHANICAL DESIGN(2015)
摘要
Additive manufacturing (AM) of metallic parts provides engineers with unprecedented design freedom. This enables designers to consolidate assemblies, lightweight designs, create intricate internal geometries for enhanced fluid flow or heat transfer performance, and fabricate complex components that previously could not be manufactured. While these design benefits may come "free" in many cases, it necessitates an understanding of the limitations and capabilities of the specific AM process used for production, the system-level design intent, and the postprocessing and inspection/qualification implications. Unfortunately, design for additive manufacturing (DfAM) guidelines for metal AM processes are nascent given the rapid advancements in metal AM technology recently. In this paper, we present a case study to provide insight into the challenges that engineers face when redesigning a multicomponent assembly into a single component fabricated using laser-based powder bed fusion for metal AM. In this case, part consolidation is used to reduce the weight by 60% and height by 53% of a multipart assembly while improving performance and minimizing leak points. Fabrication, postprocessing, and inspection issues are also discussed along with the implications on design. A generalized design approach for consolidating parts is presented to help designers realize the freedoms that metal AM provides, and numerous areas for investigation to improve DfAM are also highlighted and illustrated throughout the case study.
更多查看译文
关键词
manifolds,design,metals,manufacturing
AI 理解论文
溯源树
样例
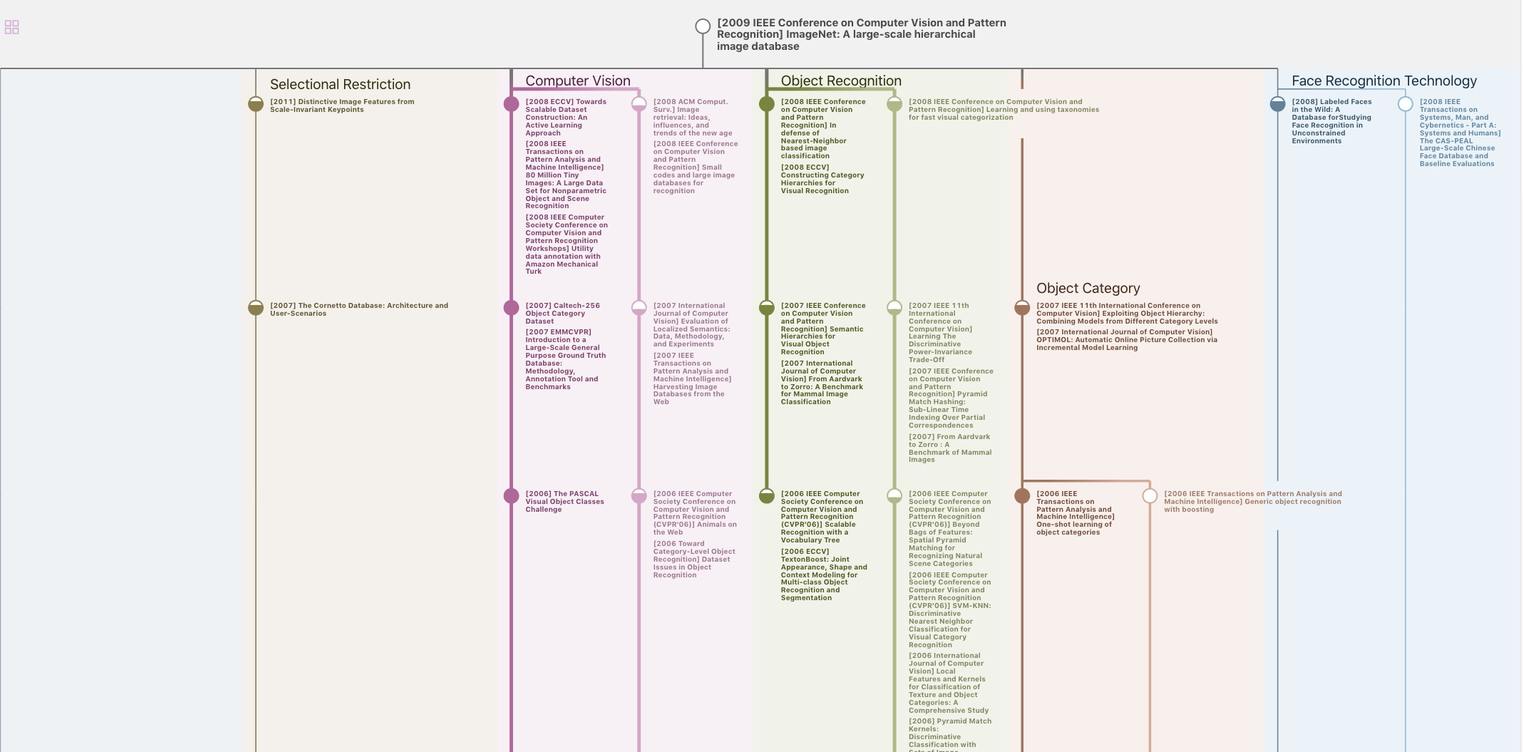
生成溯源树,研究论文发展脉络
Chat Paper
正在生成论文摘要