The effect of steam addition to the calciner in a calcium looping pilot plant
Powder Technology(2016)
摘要
Calcium looping is a post-combustion carbon capture technology which uses natural limestone as a sorbent. The carrying capacity of the natural limestone, as a CO2 sorbent, decays with each calcination/carbonation cycle. Steam has been shown to decrease the carrying capacity decay and can also be used to reactivate spent sorbent. A testing campaign with continuous CO2 capture and various levels of steam in the oxy-fired calciner was completed in a 100kWth dual-fluidized bed pilot plant. The calciner was operated with steam concentrations of 0vol.%, 15vol.% and 65vol.% at the inlet of the windbox and at 850°C and 910°C at the highest steam concentration. The increase in steam in the calciner decreased the fresh sorbent make-up requirement; for instance a 78% reduction in the make-up was required with 65vol.% steam in the calciner relative to the no-steam case. Reducing the temperature of calcination with 65vol.% steam did not further reduce the make-up requirement. The decreased decay in sorbent carrying capacity was attributed to a stable pore structure resulting from the increase in steam concentration and the corresponding reduction of the CO2 concentration in the calciner. The reduced CO2-induced sintering resulted in an increased surface area and pore volume which was stable over many calcination/carbonation cycles.
更多查看译文
关键词
Calcium looping,Carbon capture and storage,Fluidized bed,Oxy-fuel combustion
AI 理解论文
溯源树
样例
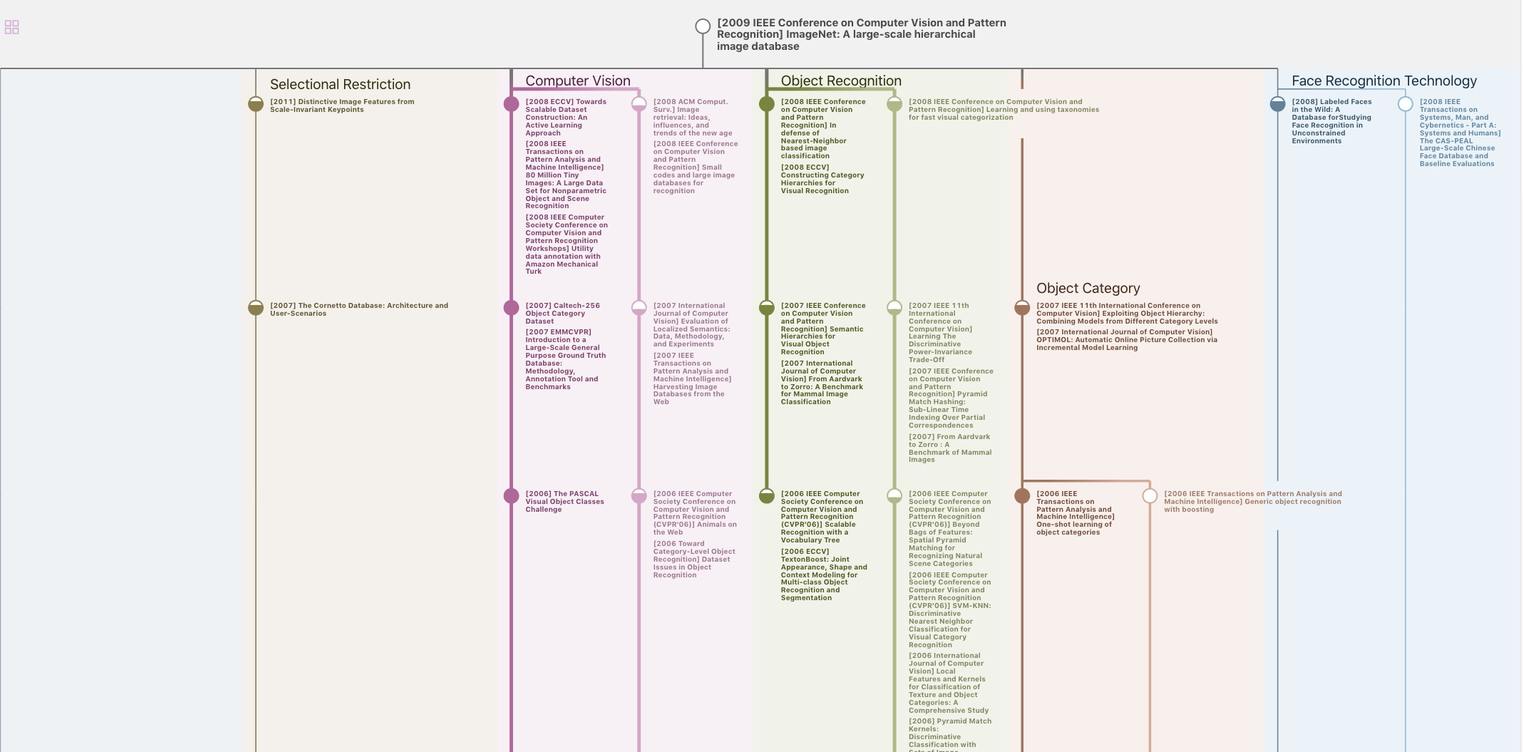
生成溯源树,研究论文发展脉络
Chat Paper
正在生成论文摘要