Quench-Induced Stresses in AA2618 Forgings for Impellers: A Multiphysics and Multiscale Problem
JOM(2015)
摘要
In the fabrication of heat-treatable aluminum parts such as AA2618 compressor impellers for turbochargers, solutionizing and quenching are key steps to obtain the required mechanical characteristics. Fast quenching is necessary to avoid coarse precipitation as it reduces the mechanical properties obtained after heat treatment. However, fast quenching induces residual stresses that can cause unacceptable distortions during machining. Furthermore, the remaining residual stresses after final machining can lead to unfavorable stresses in service. Predicting and controlling internal stresses during the whole processing from heat treatment to final machining is therefore of particular interest to prevent negative impacts of residual stresses. This problem is multiphysics because processes such as heat transfer during quenching, precipitation phenomena, thermally induced deformations, and stress generation are interacting and need to be taken into account. The problem is also multiscale as precipitates of nanosize form during quenching at locations where the cooling rate is too low. This precipitation affects the local yield strength of the material and thus impacts the level of macroscale residual stresses. A thermomechanical model accounting for precipitation in a simple but realistic way is presented. Instead of modelling precipitation that occurs during quenching, the model parameters are identified using a limited number of tensile tests achieved after representative interrupted cooling paths in a Gleeble machine. The simulation results are compared with as-quenched residual stresses in a forging measured by neutron diffraction.
更多查看译文
关键词
Residual Stress,Coarse Precipitation,Thermomechanical Model,Compressor Impeller,Local Yield Strength
AI 理解论文
溯源树
样例
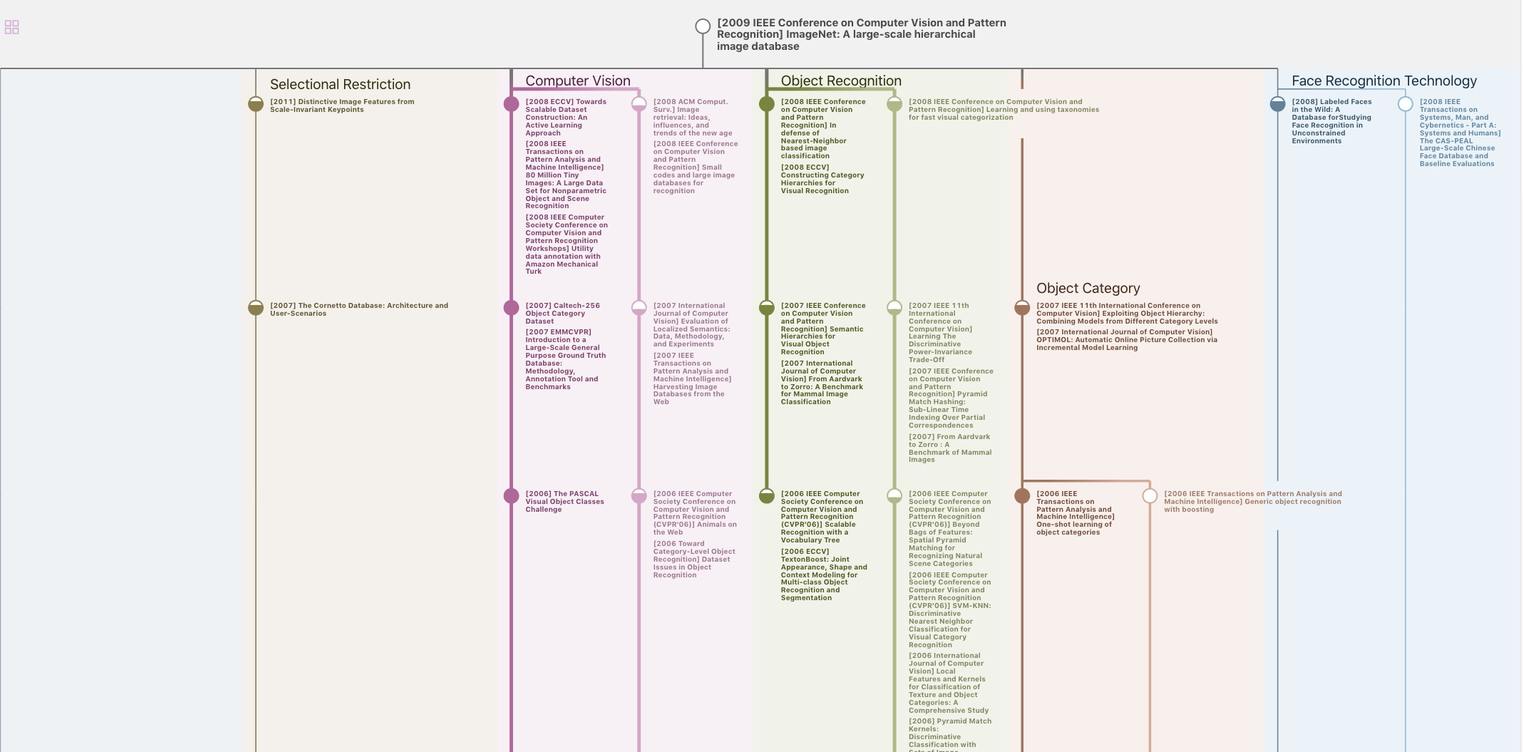
生成溯源树,研究论文发展脉络
Chat Paper
正在生成论文摘要