Microstructural modification of Ti–6Al–4V by using an in-situ printed heat sink in Electron Beam Melting® (EBM)
Journal of Materials Processing Technology(2015)
摘要
Unidirectional heat transfer during additive manufacturing (AM) processes results in anisotropy of microstructure and mechanical properties in fabricated components. In the present study, the influence of in-situ printed heat sinks on the microstructure of Ti–6Al–4V was investigated. Different numbers of heat sinks were designed and produced by the Electron Beam Melting® (EBM) process. The coupons were characterized by an optical microscope, scanning electron microscope, tensile and hardness tests, and fracture analysis. An increase in the number of heat sinks was accompanied by a reduction in grain thickness. While elongated grains still formed in all coupons, due to the dominant heat transfer along the buildup direction. The refinement of microstructure was confirmed by a reduction in the average thickness of α-lath from 1.73μm in the coupon with no heat sink to 1.01μm in the coupon with the highest number of the heat sinks. The ultimate tensile strength and hardness were increased by increasing the number of heat sinks. The results of fractorgraphy suggested that coupons with the maximum number of heat sinks (5-HS) showed a more ductile fracture. Also, digital reconstruction of the fracture surface showed that the unmelted powder particles had an influence on the crack initiation.
更多查看译文
关键词
Additive manufacturing,Electron Beam Melting® (EBM),Ti–6Al–4V,Anisotropy,Fractography,Mechanical properties
AI 理解论文
溯源树
样例
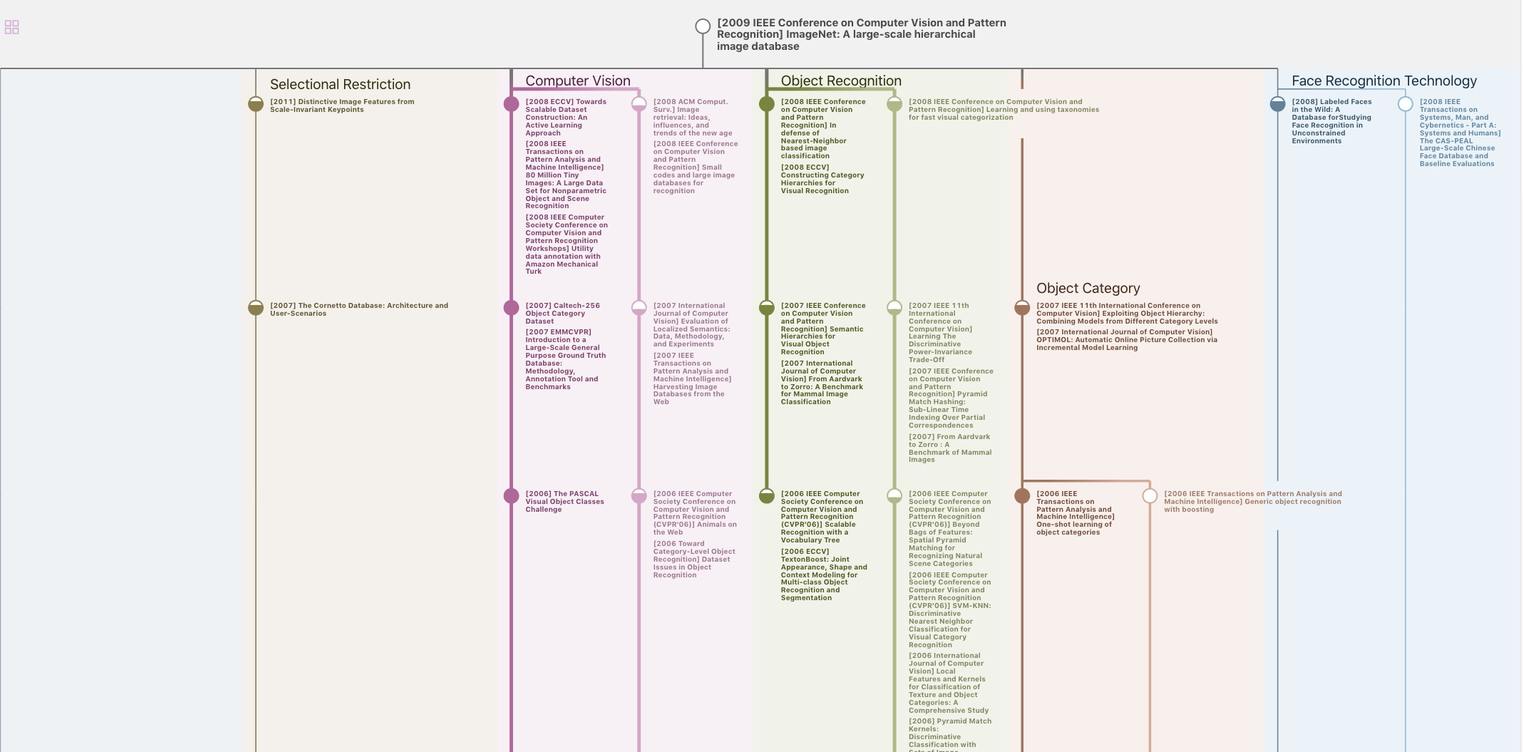
生成溯源树,研究论文发展脉络
Chat Paper
正在生成论文摘要