MEMS pressure sensor fabricated by advanced bulk micromachining techniques
Proceedings of SPIE(2013)
摘要
We present the design and implementation of a MEMS pressure sensor with an operation potential under harsh conditions at high temperatures (T = 300-800 degrees C). The sensor consists of a circular HEMT (C-HEMT) integrated on a circular AlGaN/GaN membrane. In order to realize MEMS for extreme conditions using AlGaN/GaN material system, two key issues should be solved: (a) realization of MEMS structures by etching of the substrate material and (b) formation of metallic contacts (both ohmic and Schottky) to be able to withstand high thermal loads. In this design concept the piezoresistive and piezoelectric effect of AlGaN/GaN heterostructure is used to sense the pressure under static and/or dynamic conditions. The backside bulk micromachining of our SiC wafer in the first experiment started with FS-laser ablation down to similar to 200 -270 mu m deep holes of 500 mu m in diameter. Because no additional intermediate layer can stop the ablation process, the number of laser pulses has to be optimized in order to reach the required ablation depth. 2D structural-mechanical and piezoelectric analyses were performed to verify the mechanical and piezoelectric response of the circular membrane pressure sensor to static pressure load (in the range between 20 and 100kPa). We suggested that suppressing the residual stress in the membrane can improve the sensor response. The parameters of the same devices previously fabricated on bulk substrates and/or membranes were compared. The maxima of drain currents of our C-HEMT devices on SiC exhibit more than four times higher values compared to those measured on silicon substrates.
更多查看译文
关键词
residual stress,AlGaN/GaN membrane,CHEMT,laser ablation,high temperature metallization
AI 理解论文
溯源树
样例
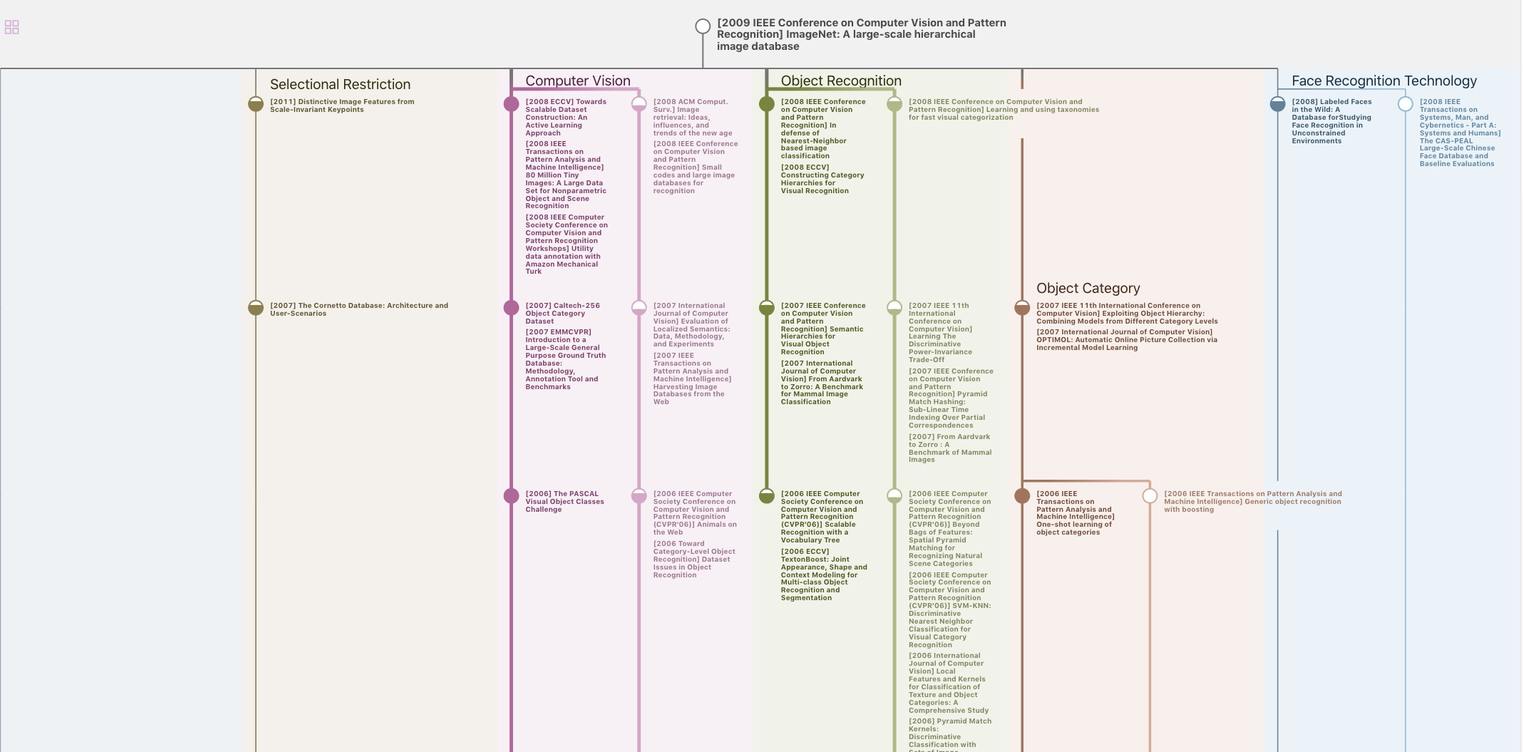
生成溯源树,研究论文发展脉络
Chat Paper
正在生成论文摘要