Analysis and correction of defects within parts fabricated using powder bed fusion technology
SURFACE TOPOGRAPHY-METROLOGY AND PROPERTIES(2015)
摘要
Quality assurance is an important topic for additive manufacturing (AM) and often seen as a requirement for the transition and adoption of the technology toward fabrication of end use applications. AsAMtechnologies are used for production, it is necessary to ensure high quality, repeatable, and reproducible components are manufactured. Various nondestructive examination techniques have been used to evaluate AM-fabricated parts to determine part quality post-fabrication (e.g. scanning and/or microstructural characterization). In situ monitoring methods have been developed for AM technologies to enable defect detection and have potential to be used for in situ monitoring and correction of fabrication anomalies (e.g. undesired temperature gradients and porosity). In this research, defects (e.g. pores) were seeded into parts fabricated using the powder bed fusion AM process, electron beam melting, and monitored using in situ infrared (IR) thermography. Results from layerwise thermography were compared with results obtained using computer tomography (CT) scanning techniques. Although the measured geometry of the seeded defects between IR thermography and CT was substantially different (area difference of similar to 60%), the thermographs did provide a good indication of defects present within a fabricated part. Furthermore, defect correction methods were evaluated including post-processing methods such as hot isostatic pressing as well as in situ correction methods such as layer re-melting. Re-melting a porous layer successfully corrected defects and demonstrates a potential method for in situ defect correction if implemented in future systems equipped with automatic feedback control of powder bed fusion processes.
更多查看译文
关键词
infrared thermography,computer tomography,powder bed fusion,monitoring,defect detection,electron beam melting
AI 理解论文
溯源树
样例
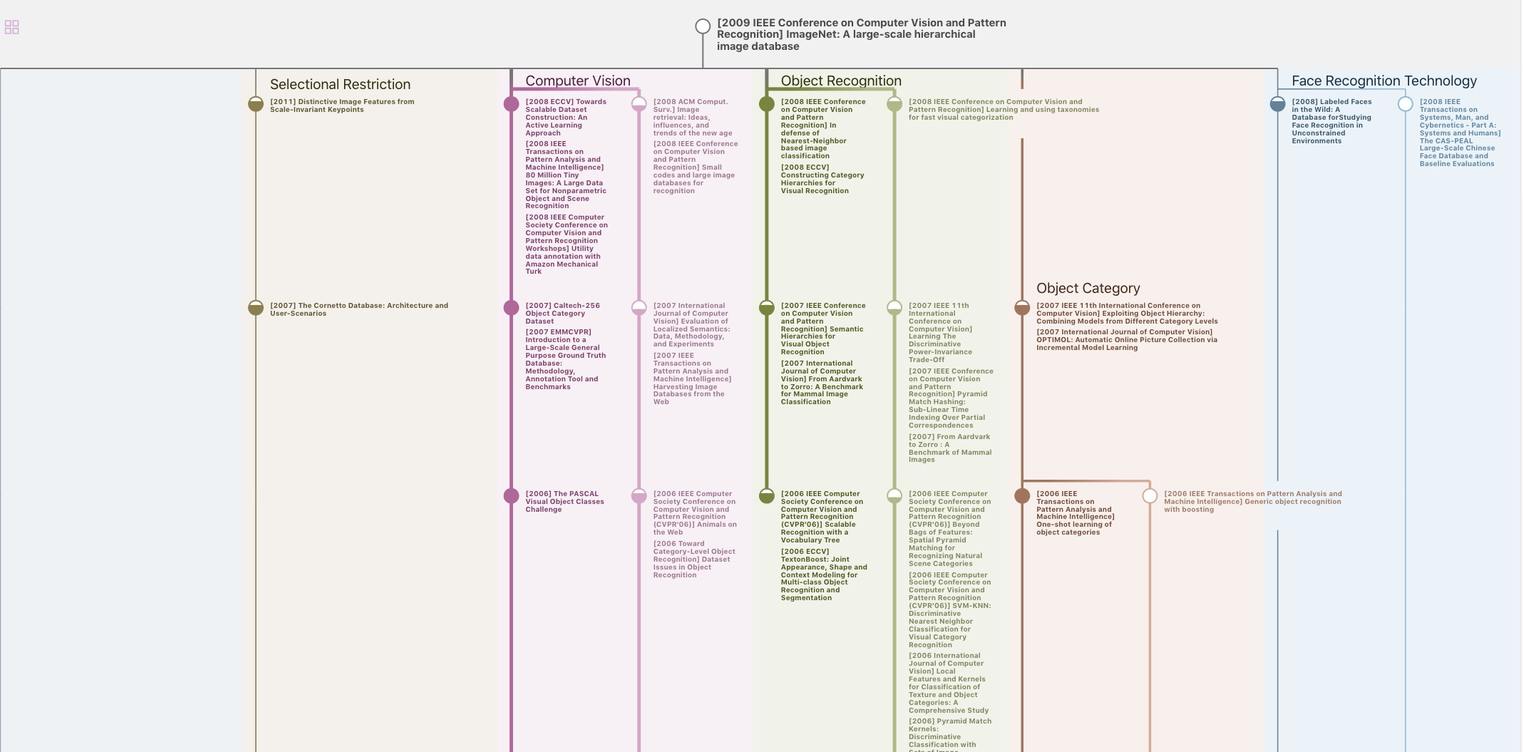
生成溯源树,研究论文发展脉络
Chat Paper
正在生成论文摘要