Thermosonic ball bonding behavior of Ag-Au-Pd alloy wire
Electronics Packaging Technology Conference Proceedings(2013)
摘要
Thermosonic wire bonding is a well-known process which combines heat, ultrasonic energy and force to bond small wires to complete an electrical path from a metalized surface on a microchip to another metalized surface on the substrate of the circuit and the bonding occurs through the process of atomic diffusion. The bonding wire materials presently used in the industries are primarily gold (Au) and recently the use of low cost copper (Cu) and palladium coated wire (PdCu) have increased significantly. However, due to the increasing price of Au and reliability concerns with the Cu and PdCu wire has led to the search of alternative bonding wire materials in which silver (Ag) or silver alloy wire (Ag alloy) has emerged as the preferred choice. Cu and 1PdCu wire induces a higher stress on the bond pad and underlying structure due to its inherent hardness value. Ag has similar mechanical properties as Au while it's cheaper and has higher thermal and electrical conductivity as compared to Au. When compared to Cu, Ag is similar in conductivity, but softer in terms of mechanical properties. The pure Ag bonding wire has some issues such as unstable free air ball (FAR) shape and poor reliability. To overcome these issues, alloyed Ag wire (Ag-Au-Pd) was developed and their FAB formation, bondability and reliability were studied. The package used is BOA type and the pad composition is Al-1%Si-0.5%) Cu. The Ag alloy wire delivers good and stable bonding capability using nitrogen as ambient gas. Both the bonded ball and stich bonding show good bond integrity. The reliability is determined by the high temperature storage life test (HTSL) test. Intermetallic compound (IMC) growth behavior during reliability test is characterized by the scanning electron microscopy (SEM) and energy dispersive spectrometer analyses (EDS). Two types of IMCs Ag2Al and Ag3Al were observed. No failure or voids are observed in the bulk IMC or metal-IMC interface after the HTSL test at 150C for 1000 hrs. Additionally these IMCs are fabricated in bulk and their resistivity and co-efficient of thermal expansion (CTE) properties are characterized to understand the likely source of failure of the Ag-Al bond. The CTE of the Ag3Al is lower than the Ag2Al which could be attributed to the lower stretching of lattice constant of former at higher temperature. The interface between the Al and Ag2Al is likely source of crack generation and failure because of the high CTE difference between them. The resistivity of the Ag3Al phase was found to slightly higher than Ag2Al. The information regarding the properties of Ag-Al IMCs are important for the finite element and quantum mechanics based first principle calculation and to ultimately predict their behavior in real life situation. The Ag alloy wire show floor life time of minimum 10 weeks based on bonded ball shape, workability and bondability test and there is no visible appreciable degradation of pull strength and bonded ball shape overtime. Ag alloy wire bonding has the potential to become an emerging technology as an option in microelectronic packaging.
更多查看译文
关键词
finite element analysis,scanning electron microscopy,thermal expansion
AI 理解论文
溯源树
样例
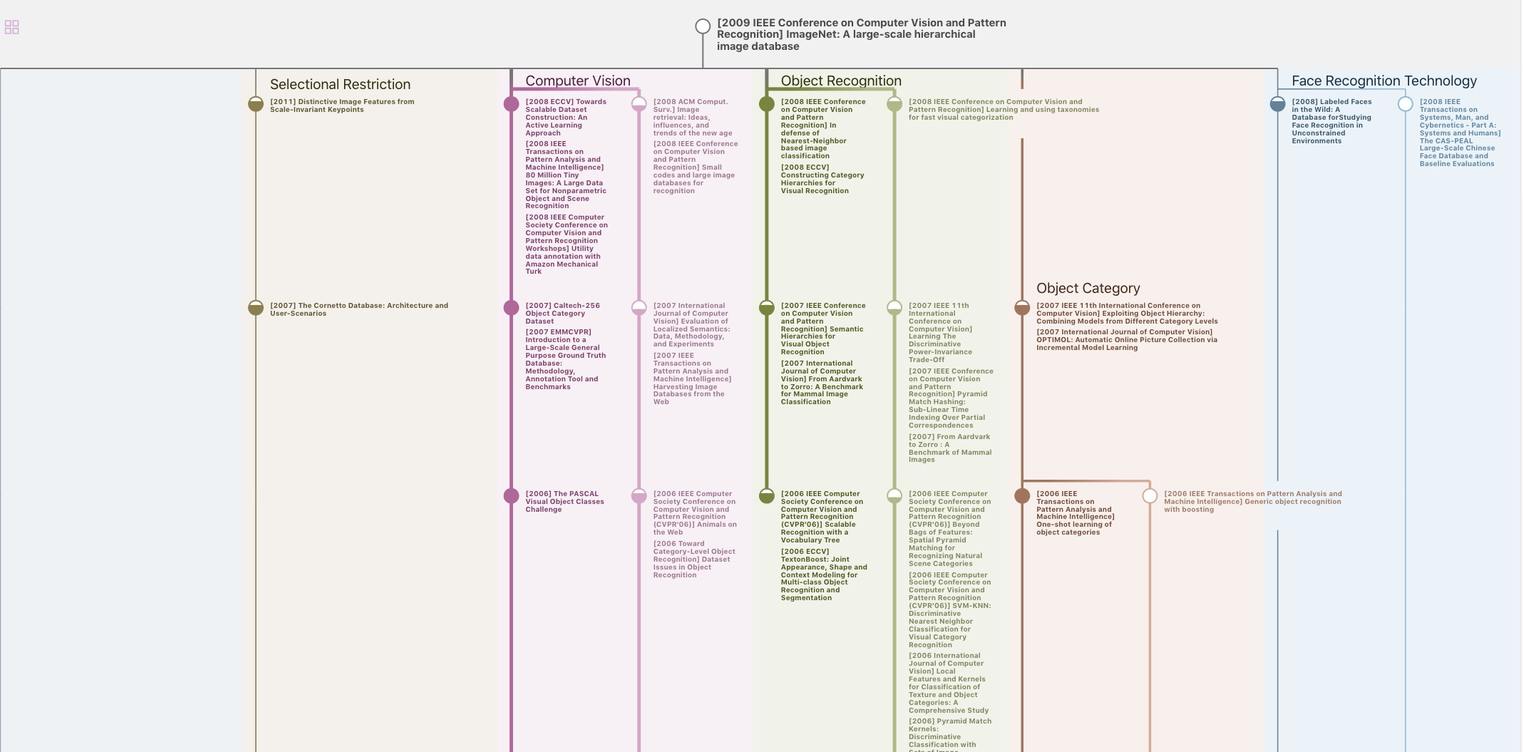
生成溯源树,研究论文发展脉络
Chat Paper
正在生成论文摘要