Effect Of Airfoil Shape And Turning Angle On Turbine Airfoil Aerodynamic Performance At Transonic Conditions
PROCEEDINGS OF THE ASME INTERNATIONAL MECHANICAL ENGINEERING CONGRESS AND EXPOSITION, 2011, VOL 6, PTS A AND B(2012)
摘要
Performance data for high turning gas turbine blades under transonic Mach numbers is significantly lacking in literature. Performance of three gas turbine airfoils with varying turning angles at transonic flow conditions was investigated in this study. Midspan total pressure loss, secondary flow field and static pressure measurements on the airfoil surface in a linear cascade setting were measured. Airfoil curvature and true chord were varied to change the loading vs. chord for each airfoil. Airfoils A, D and E are designed to operate at different velocity triangles. Velocity triangle requirements (inlet/exit Mach number and gas angles) come from 1D and 2D models that include calibrated loss systems. One of the goals of this study was to use the experimental data to confirm/refine loss predictions for the effect of various Mach numbers and gas turning angles. The cascade exit Mach numbers were varied within a range from 0.6 to 1.1. The airfoil turning angle ranges from 120 degrees to 138 degrees. A realistic inlet/exit Mach number ratio, that is representative of that seen in a real engine, was obtained by reducing the inlet span with respect to the exit span of the airfoil, thereby creating a quasi 2D cascade. In order to compare the experimental results and study the detailed flow characteristics, 3D viscous compressible CFD analysis was also carried out.
更多查看译文
关键词
shapes,airfoils
AI 理解论文
溯源树
样例
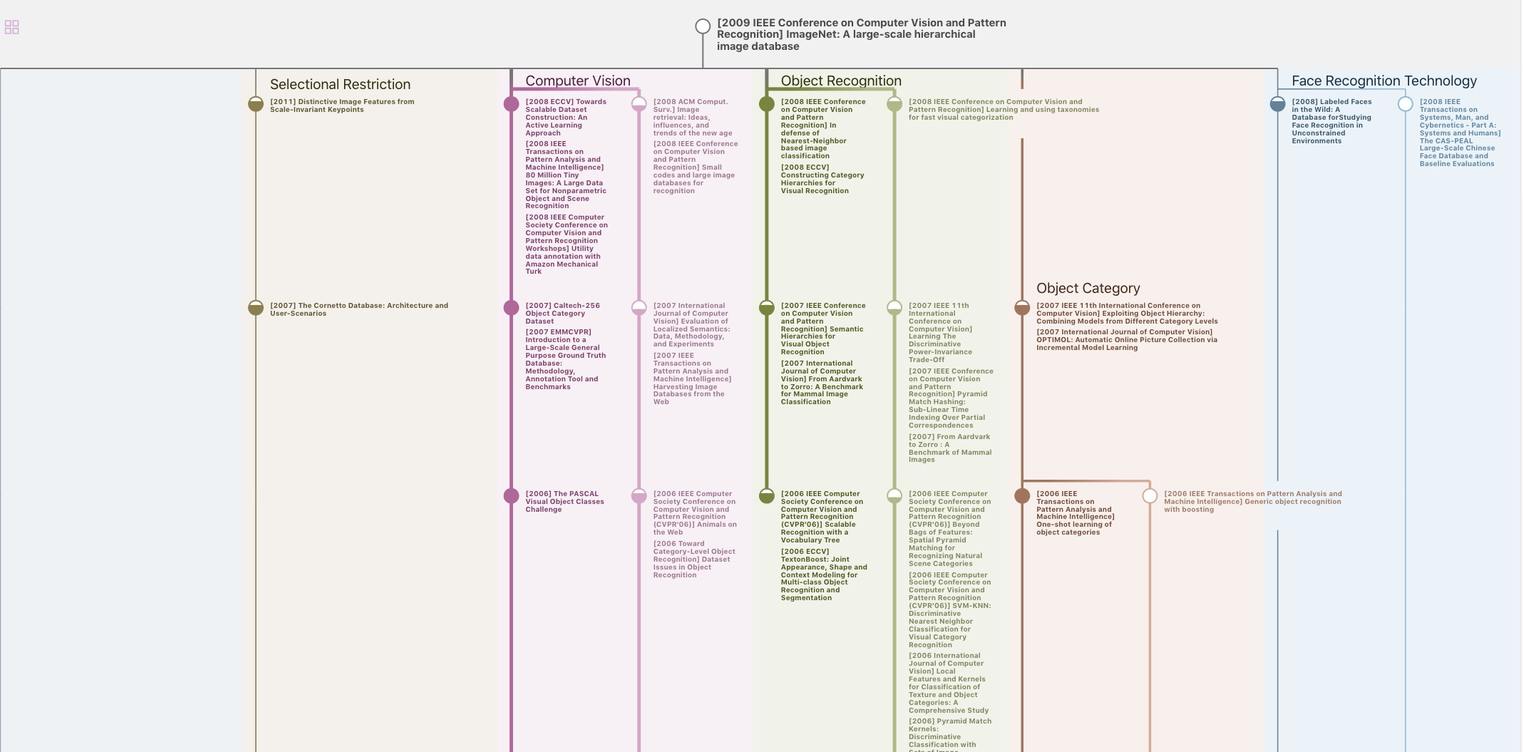
生成溯源树,研究论文发展脉络
Chat Paper
正在生成论文摘要