Numerical Contribution For The Optimization Of A Welding Procedure - Identification Of An Equivalent Heat Source
MATERIAUX & TECHNIQUES(2014)
摘要
The use of narrow gap for thick component welding as applied in nuclear industries and especially by AREVA NP, requires the mastering of several parameters and especially shrinkage. The prediction through numerical simulation is very helpful for welding procedure definition. This paper describes an approach used to determine a 3D heat source dedicated to a new industrial welding process configuration (deep narrow groove multipass low-carbon steel gas metal arc welding (GMAW), two pass per layer) to assess the groove shrinkage which occurs during welding by numerical simulation. The revelant bead shape and temperatures in the solid zone are identified by optimazing a multiobjective problem. The optimization is performed with experimental datas from fine temperature measurements on the welding mock-up. Finally, the identified 3D heat source model is a combination of two volumetric heat sources. It can be used as thermal loading for subsequent thermal metallurgical mechanical calculations, notably for shrinkage prediction.
更多查看译文
关键词
Narrow gap TIG welding, numerical simulation, heat source, heat transfer, inverse heat conduction problem
AI 理解论文
溯源树
样例
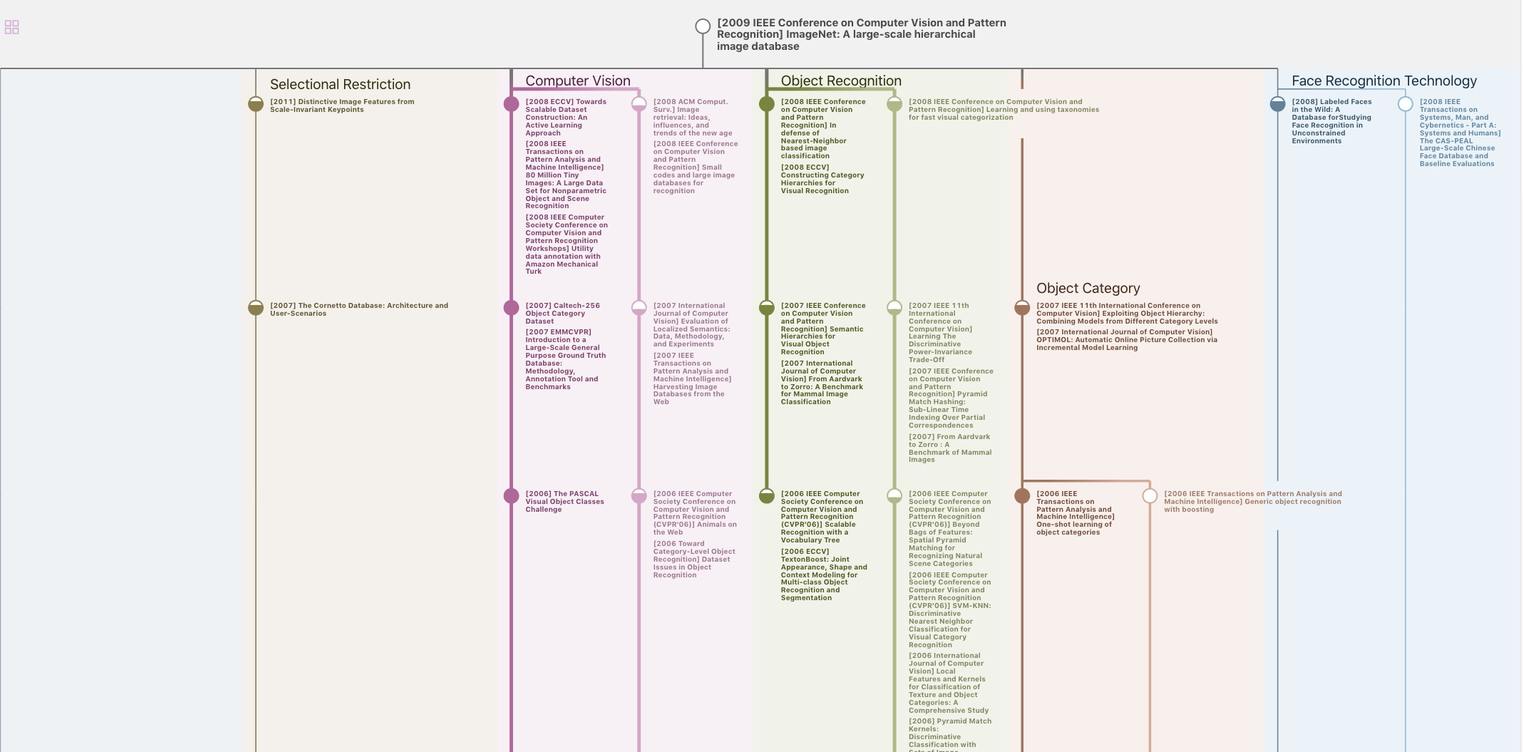
生成溯源树,研究论文发展脉络
Chat Paper
正在生成论文摘要