Performance of a radial vacuum insulator stack
2015 IEEE Pulsed Power Conference (PPC)(2015)
摘要
Electrostatic breakdown (“flashover”) can limit the maximum delivered power in pulsed power systems. One problematic region is the solid-vacuum interface. The solid/vacuum interface surface is generally the component most likely to suffer undesired breakdown in a well-designed pulsed power system driving a load in vacuum. A relatively small (in total number) and localized amount of neutrals or plasma can be enough to allow a self-sustaining discharge. A discharge along the solid-vacuum interface can readily and quickly desorb ions and neutrals from the insulator material. The spurious discharge can carry almost unlimited current, generally constrained only by the current source or the inductance of the current path. Radial insulator assemblies, where power flows along the axis of the insulator (used in a coaxial power feed with concentric insulators of differing diameters, maintaining radial electric field direction) can be lower insertion inductance and smaller in total size than axial insulators. Radial insulators have additional electric field grading and mechanical stress issues compared to an axial insulator system. With an interest in quantifying and improving performance of a radial insulator system, we have built a prototype 60 cm diameter assembly with four series insulator rings and 0.23 m
2
total stressed area. By driving the insulator with a ~2 MV, 15 ns (effective time) negative pulse from a low energy system, we are able to study insulator performance of a multi-level stack with a reasonable data rate in a relevant regime (~180 kV/cm). The prototype insulator assembly is designed to demonstrate key concepts important for a large system, including 1) improved electric field uniformity using equipotential redistribution, 2) mechanical assembly viability with reasonable machining tolerances, and 3) useful electric field hold-off. The system is scalable to larger size insulators with acceptable electric field uniformity and mechanical stress in the insulating plastic. Mated to a (generally optimal) 40Ω oil-insulated transmission line, the electric field uniformity on the plastic-vacuum interface tested here is better than ±1%. Without equipotential redistribution, the electric field non-uniformity would be of order ±46%. To facilitate future fabrication of larger insulator assemblies, the Rexolite® 1422 cross-linked polystyrene plastic rings are cut from sheet or individually cast, then machined; a large monolithic slab of insulator material is not needed. We will discuss basic properties of vacuum interfaces, discuss scaling formulae used to relate performance of different systems, and show results of testing.
更多查看译文
关键词
radial vacuum insulator stack,electrostatic breakdown,flashover,pulsed power systems,solid/vacuum interface surface,self-sustaining discharge,insulator material,spurious discharge,radial insulator assemblies,coaxial power feed,concentric insulators,radial electric field direction,insertion inductance,electric field grading,mechanical stress issues,axial insulator system,radial insulator system,multilevel stack,electric field uniformity,equipotential redistribution,mechanical assembly viability,machining tolerances,electric field hold-off,insulating plastic,oil-insulated transmission line,plastic-vacuum interface,Rexolite 1422 cross-linked polystyrene plastic rings,vacuum interfaces,resistance 40 ohm
AI 理解论文
溯源树
样例
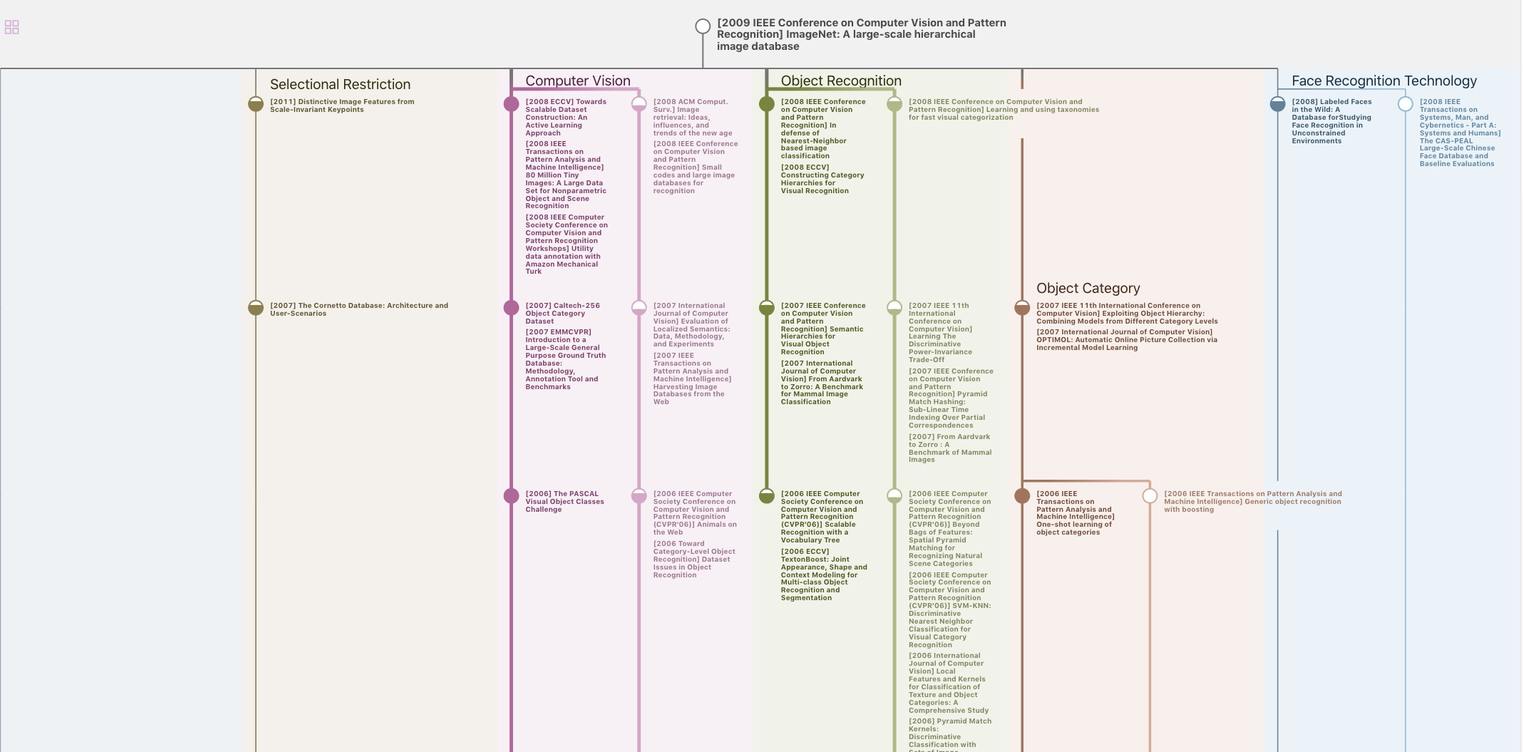
生成溯源树,研究论文发展脉络
Chat Paper
正在生成论文摘要