Effect Of Quenching Temperature And Cooling Rate On The Mechanical Properties Of Direct Quenched Micro-Alloyed Steel For Hot Forging
KOREAN JOURNAL OF MATERIALS RESEARCH(2012)
摘要
Recently, automobile parts have been required to have high strength and toughness to allow for weight lightening or improved stability. But, traditional micro-alloyed steel cannot be applied in automobile parts. In this study, we considered the influence of quenching temperature and cooling rate for specimens fabricated by vacuum induction furnace. Directly quenched micro-alloyed steel for hot forging can be controlled according to its micro structure and the heat-treatment process. Low carbon steel, as well as alloying elements for improvement of strength and toughness, was used to obtain optimized conditions. After hot forging at 1,200 degrees C, the ideal mechanical properties (tensile strength >= 1,000MPa, Charpy impact value >= 100 J/cm(2)) can be achieved by using optimized conditions (quenching temperature : 925 to 1,050 degrees C, cooling rate : >= 5 degrees C/sec). The difference of impact value according to cooling rate can be influenced by the microstructure. A fine lath martensite micro structure is formed at a cooling rate of over 5 degrees C/sec. On the other hand, the second phase of the M-A constituent microstructure is the cause of crack initiation under the cooling rate of 5 degrees C/sec.
更多查看译文
关键词
high strength and toughness, micro-alloyed steel, direct quenched
AI 理解论文
溯源树
样例
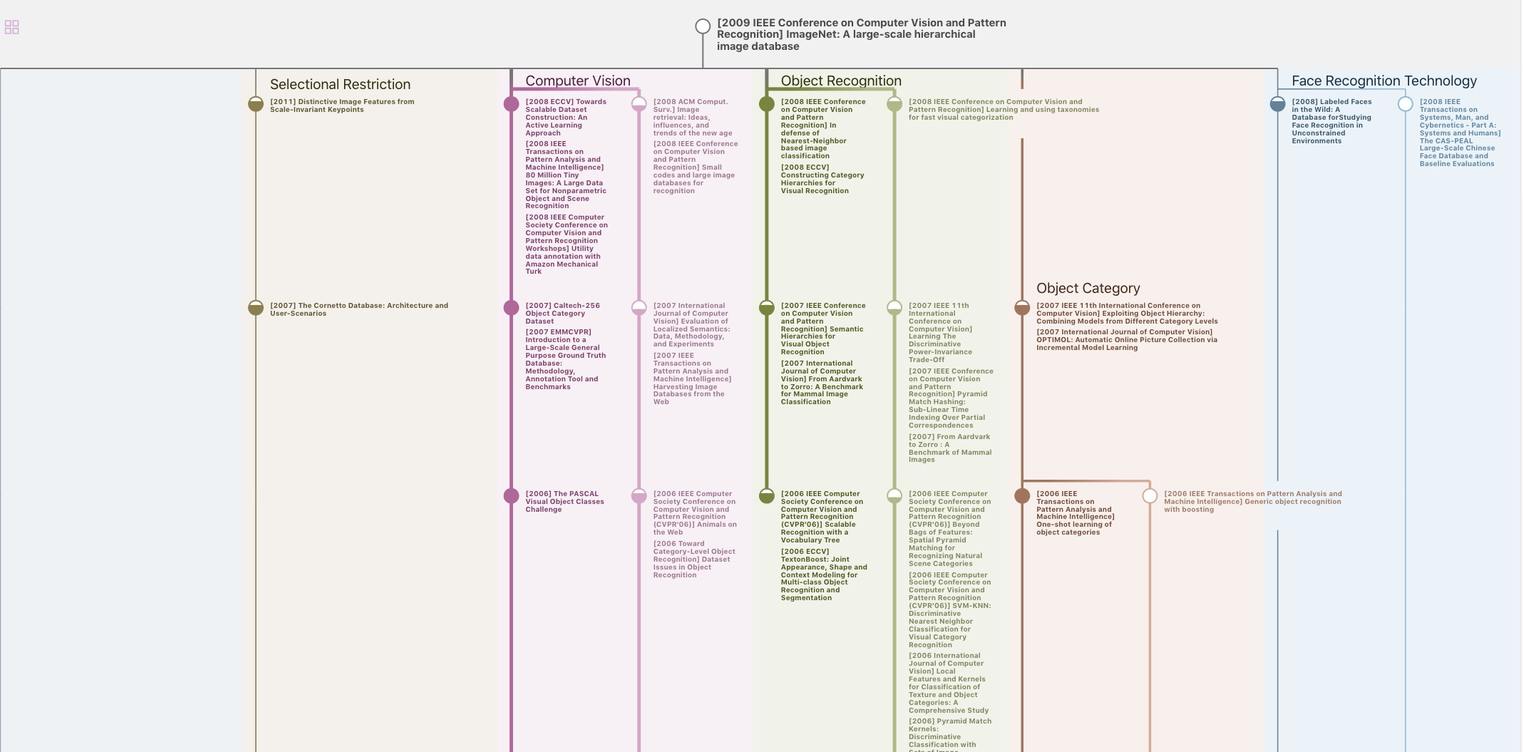
生成溯源树,研究论文发展脉络
Chat Paper
正在生成论文摘要