Prediction of microstructure, residual stress, and deformation in laser powder bed fusion process
Computational Mechanics(2017)
摘要
Laser powder bed fusion (L-PBF) process has been investigated significantly to build production parts with a complex shape. Modeling tools, which can be used in a part level, are essential to allow engineers to fine tune the shape design and process parameters for additive manufacturing. This study focuses on developing modeling methods to predict microstructure, hardness, residual stress, and deformation in large L-PBF built parts. A transient sequentially coupled thermal and metallurgical analysis method was developed to predict microstructure and hardness on L-PBF built high-strength, low-alloy steel parts. A moving heat-source model was used in this analysis to accurately predict the temperature history. A kinetics based model which was developed to predict microstructure in the heat-affected zone of a welded joint was extended to predict the microstructure and hardness in an L-PBF build by inputting the predicted temperature history. The tempering effect resulting from the following built layers on the current-layer microstructural phases were modeled, which is the key to predict the final hardness correctly. It was also found that the top layers of a build part have higher hardness because of the lack of the tempering effect. A sequentially coupled thermal and mechanical analysis method was developed to predict residual stress and deformation for an L-PBF build part. It was found that a line-heating model is not suitable for analyzing a large L-PBF built part. The layer heating method is a potential method for analyzing a large L-PBF built part. The experiment was conducted to validate the model predictions.
更多查看译文
关键词
Additive manufacturing,Laser powder bed fusion,Finite element analysis,Residual stress,distortion
AI 理解论文
溯源树
样例
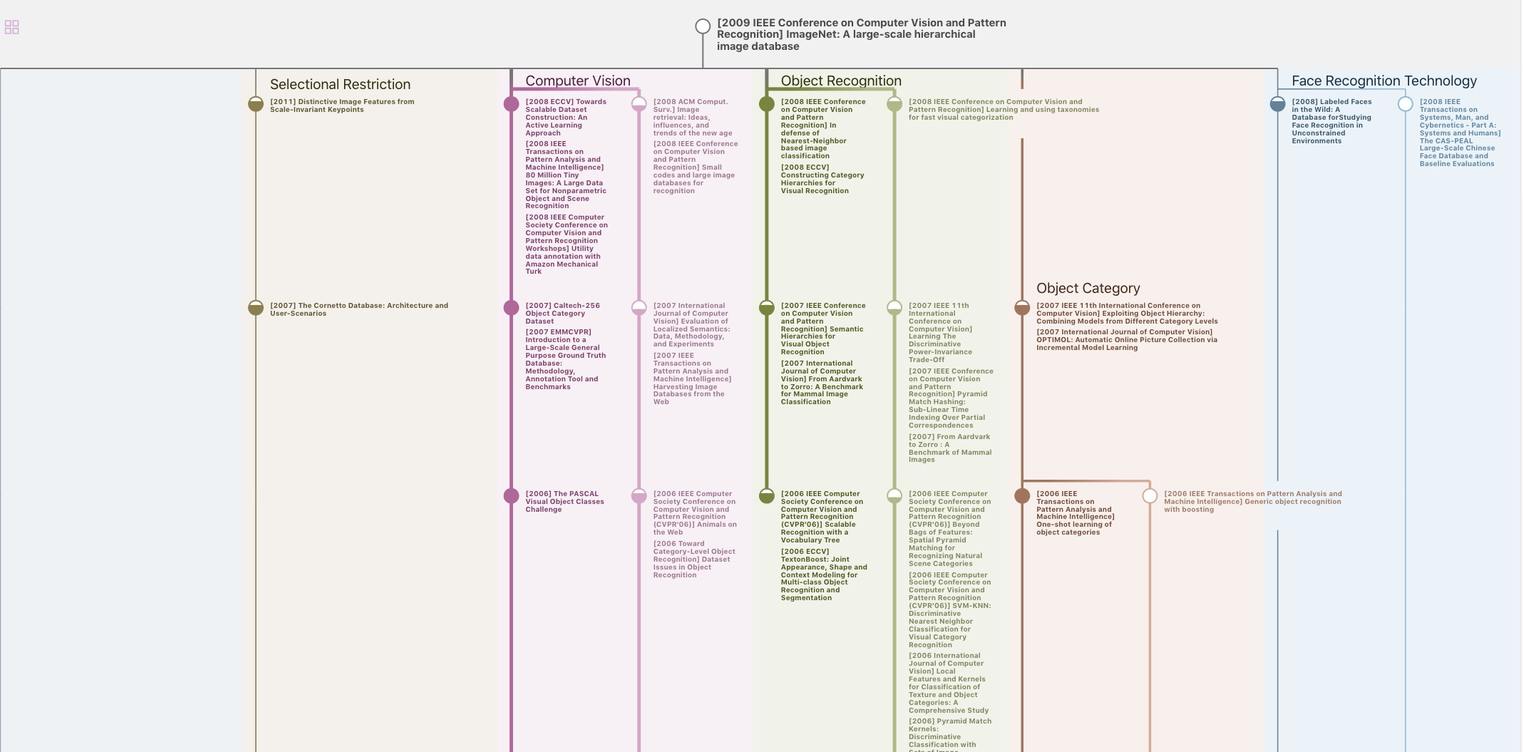
生成溯源树,研究论文发展脉络
Chat Paper
正在生成论文摘要