Proposal for Optimization of Spool Valve Flow Force Based on the MATLAB-AMESim-FLUENT Joint Simulation Method.
IEEE ACCESS(2018)
摘要
This paper focuses on the open-center multi-way valve used in loader buckets. To solve the problem of excessive flow force that leads to spool clamping in the reset process, joint simulations adopting MATLAB, AMESim, and FLUENT were carried out. Boundary conditions play a decisive role in the results of computational fluid dynamics (CFD) simulation. However, the boundary conditions of valve ports depend on the hydraulic system's working condition and are significantly impacted by the port area, which has always been neglected. This paper starts with the port area calculation method, then the port area curves are input into the simulation hydraulic system, obtaining the flow curves of valve port as output, which are then applied as the boundary conditions of the spool valve CH) simulation. Therefore, the steady-state flow force of the spool valve is accurately calculated, and the result verifies the hypothesis that excess flow force causes spool clamping. Based on this, four kinds of structures were introduced in an attempt to improve the situation, and simulating calculation and theoretical analysis were adopted to verify the effects of improvement. Results show that the four structures could reduce the peak value of flow force by 17.8%, 60.6%, 61.6%, and 55.7%, respectively. Of the four, structures II, III, and IV can reduce the peak value of flow force to below reset spring force value, thus successfully avoiding the spool clamping caused by flow force.
更多查看译文
关键词
Spool clamping,port area calculation,joint simulation,CFD,steady-state flow force,improved structure
AI 理解论文
溯源树
样例
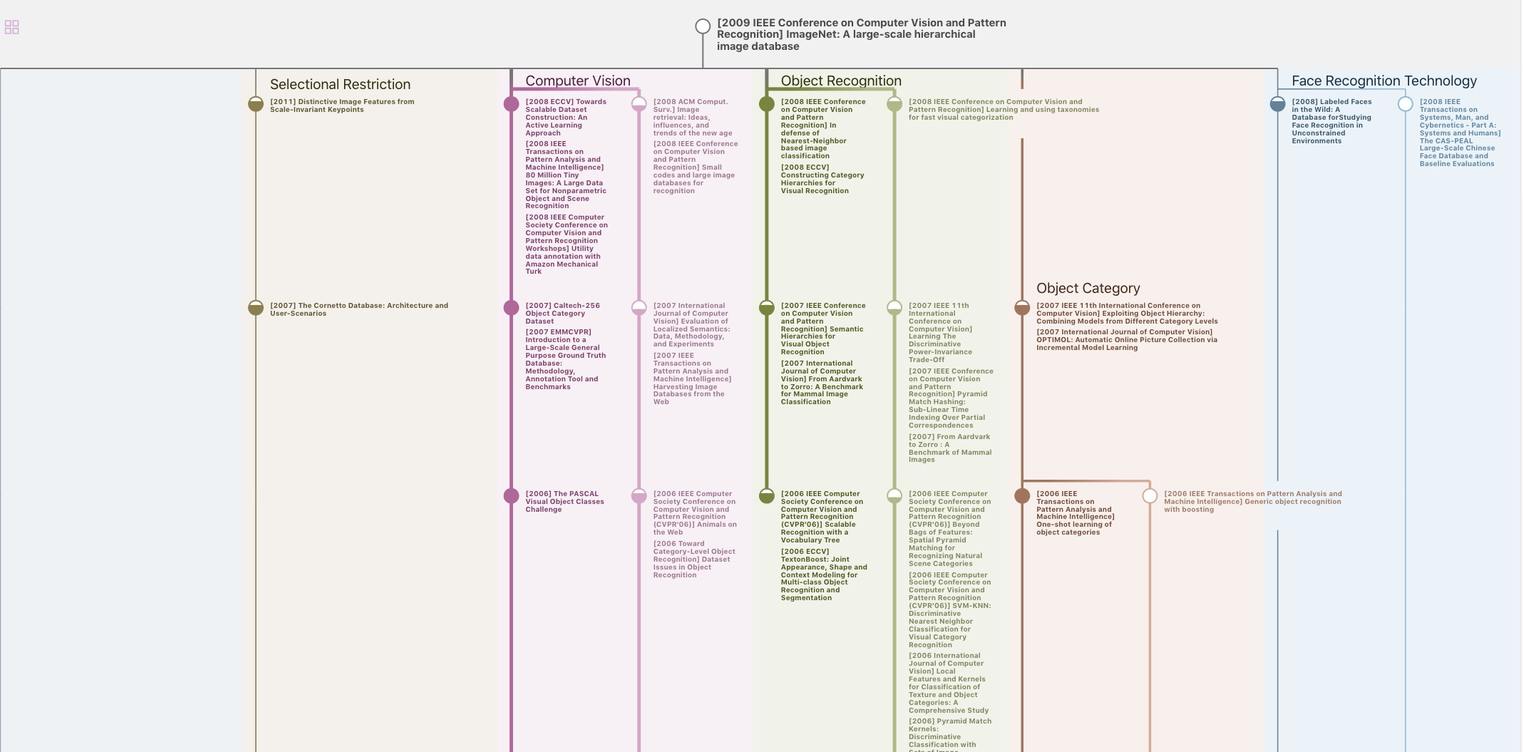
生成溯源树,研究论文发展脉络
Chat Paper
正在生成论文摘要