Secondary flow stabilization of 100 kW-class micro gas turbine
Journal of Mechanical Science and Technology(2017)
摘要
Experimental and numerical research was conducted to stabilize the secondary flow of a micro gas turbine. The trust balance between the compressor impeller and the turbine rotor should be conserved during the entire operation to satisfy the operation conditions. However, micro gas turbines cannot achieve their design condition if improper events, such as rotor dynamic unbalance, thermal deformation, rubbing, occur. The present research introduces experimental and numerical procedures to stabilize the secondary flow in micro gas turbines. A micro gas turbine and the performance test facility was developed at KIMM (Korea Institute of Machinery and Materials) to improve the core technology that is used in micro gas turbines in the distributed generation industry. For convenience, the micro gas turbine facility was divided into two components: the major components of the micro gas turbine and the assist components. After assembling the micro gas turbine, the motoring test, the self-sustaining test and the part load test were conducted to verify the performance. For stable operation, the secondary flow distribution in a micro gas turbine must be formed properly. However, the secondary flow distribution performs improperly during combustion. At the beginning of the experimental test, a combined thermo-mechanical analysis was conducted to determine the reason for the unstable secondary flow distribution of the developed micro gas turbine. To make a fit-forpurpose secondary flow distribution, a heat shield support was specifically designed and installed so significant improvement could be realized.
更多查看译文
关键词
Combined thermo-mechanical analysis,Micro gas turbine,Secondary flow,Stabilization,Test facility
AI 理解论文
溯源树
样例
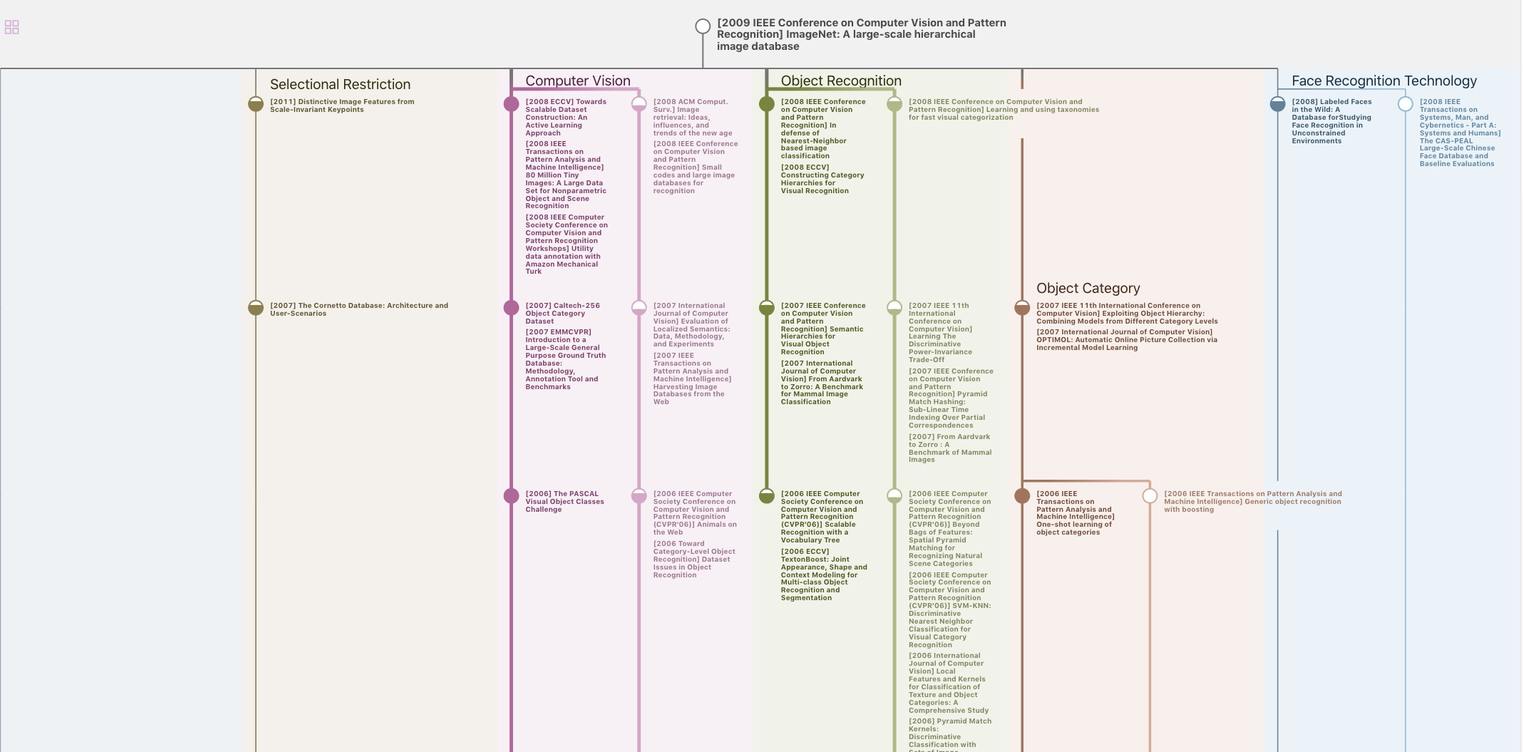
生成溯源树,研究论文发展脉络
Chat Paper
正在生成论文摘要