Obtaining nanostructural materials by the electroacoustic spraying method
Russian Engineering Research(2007)
摘要
1 The electroacoustic spraying (ELASing) method [1 and 2] is based on the combined synchronous impulsive action of highly concentrated energy fluxes (electric spark and axial/torsional ultrasonic oscillations (USOs)), the action of which can be interpreted as impact with shearing. The coatings that are obtained by the ELASing method make it possible to significantly increase (by 6 to 8 times) the service life of the machine parts and cutting tools. The numerous physical and chemical processes that take place in ELASing in the extremely nonuniform conditions have not been adequately studied, therefore it is difficult to evaluate the influence of all the factors on the wear resistance of the hardened surface. It has been established by the previous studies that the basic factors leading to the hardening of the surface layer in the ELASing process include the following: the creation of a dual barrier to the emergence of the dislocations to the surface [3]; the increase of the density and the polygonization of the dislocations in the direction of the applied external force [4]; the achieving of high strength of the bonding of the coating with the substrate as a result of the intensification of the diffusion processes [5]. One of the least studied factors contributing to the hardening process is the creation of the ultrafine dispersed and amorphous structures in the surface layer. Interest in the studies in this field has increased recently, since it has been established (primarily for the metals) that the reduction of the size of the grains (crystallites) below some threshold value leads to considerable change of the properties of the material. The new materials have high strength and hardness, and have higher fracture toughness and increased wear resistance [6, 7]. Synchronous pulsed action of the powerful axial/torsional USOs and the low-voltage ( U = 10‐40 V) electric discharge on the workpiece takes place in the ELASing process. It is known [8] that the USOs can create in the 1 Proc. of Fifth International Scientific-Engineering Conference “Assuring and Improving the Quality of Machines in Their Various Life Cycle Stages” (Bryansk, 2006) contact zone local pressures to 10 GPa with an application rate to 20 GPa/s. The result is significant increase of the probability of the appearance of the deformation twins that lead to the forming of the ultrafine dispersed fragmented structure. At the high melt cooling rates (about 10 6 K/s), the formation and growth of the new crystallization centers slow significantly, and terminate upon reaching some critical rate. In this case the material acquires an amorphous structure. However, if the cooling rate is quite high but does not exceed the critical value, the material has an ultrafine dispersed structure. In the ELASing process, the high cooling rates are achieved as a result of the high degree of supercooling that is caused by the small volume of the material that is melted and transported in a single spark discharge in comparison with the volume of the substrate. Thus, we can presume that the high rate of cooling with practically simultaneous intense plastic deformation will lead to the forming of the ultrafine dispersed fragmented and, possibly, nanocrystalline structure of the material. Analytic evaluation of the critical cooling conditions. We have calculated with the use of the technique and data of [9] the critical cooling rates for the various materials. The two-dimensional Stefan problem with boundary conditions of the second kind was solved to determine the melt cooling rate through the entire thickness of the deposited material [10]. The solution, obtained by the numerical methods in the Femlab finite-element analysis program, made it possible to estimate the percent content of the amorphous and crystalline phases and calculate the dimensions of the crystallites. The computations were made for the case when the anode material was copper (Cu), tungsten (W), and iron (Fe), and the cathode material was iron. The power of the heat source was varied in the course of the calculation (by varying the voltage U ). The most important results are presented in the table.
更多查看译文
关键词
plastic deformation,iron,boundary condition,diffusion process,low voltage,critical value,surface layer,wear resistance,energy flux,oscillations,copper,dislocations,finite element analysis,service life,numerical method,fracture toughness,life cycle
AI 理解论文
溯源树
样例
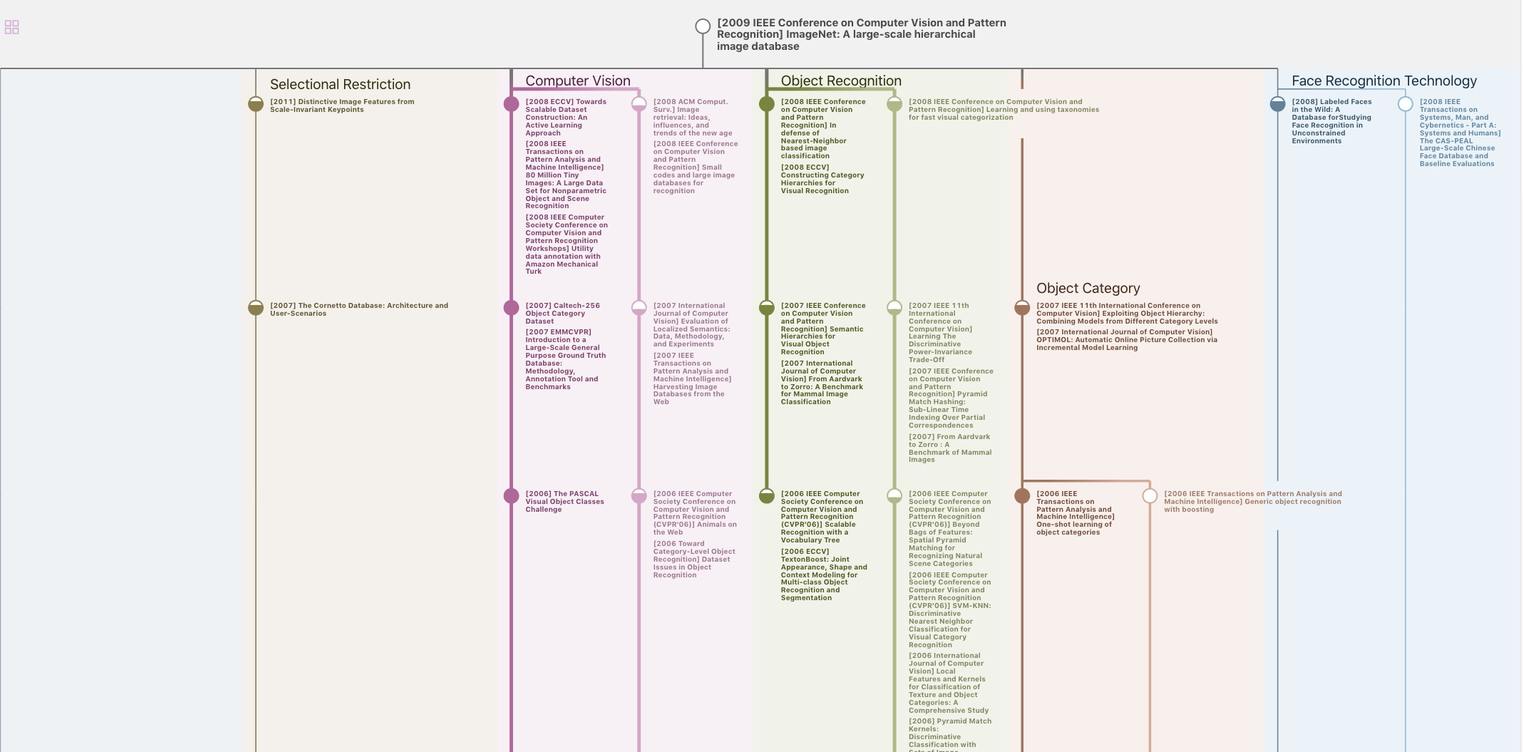
生成溯源树,研究论文发展脉络
Chat Paper
正在生成论文摘要