Experimental Investigation of Numerically Optimized Wavy Microchannels Created Through Additive Manufacturing
JOURNAL OF TURBOMACHINERY-TRANSACTIONS OF THE ASME(2018)
摘要
The increased design space offered by additive manufacturing (AM) can inspire unique ideas and different modeling approaches. One tool for generating complex yet effective designs is found in numerical optimization schemes, but until relatively recently, the capability to physically produce such a design had been limited by manufacturing constraints. In this study, a commercial adjoint optimization solver was used in conjunction with a conventional flow solver to optimize the design of wavy microchannels, the end use of which can be found in gas turbine airfoil skin cooling schemes. Three objective functions were chosen for two baseline wavy channel designs: minimize the pressure drop between channel inlet and outlet, maximize the heat transfer on the channel walls, and maximize the ratio between heat transfer and pressure drop. The optimizer was successful in achieving each objective and generated significant geometric variations from the baseline study. The optimized channels were additively manufactured using direct metal laser sintering (DMLS) and printed reasonably true to the design intent. Experimental results showed that the high surface roughness in the channels prevented the objective to minimize pressure loss from being fulfilled. However, where heat transfer was to be maximized, the optimized channels showed a corresponding increase in Nusselt number.
更多查看译文
AI 理解论文
溯源树
样例
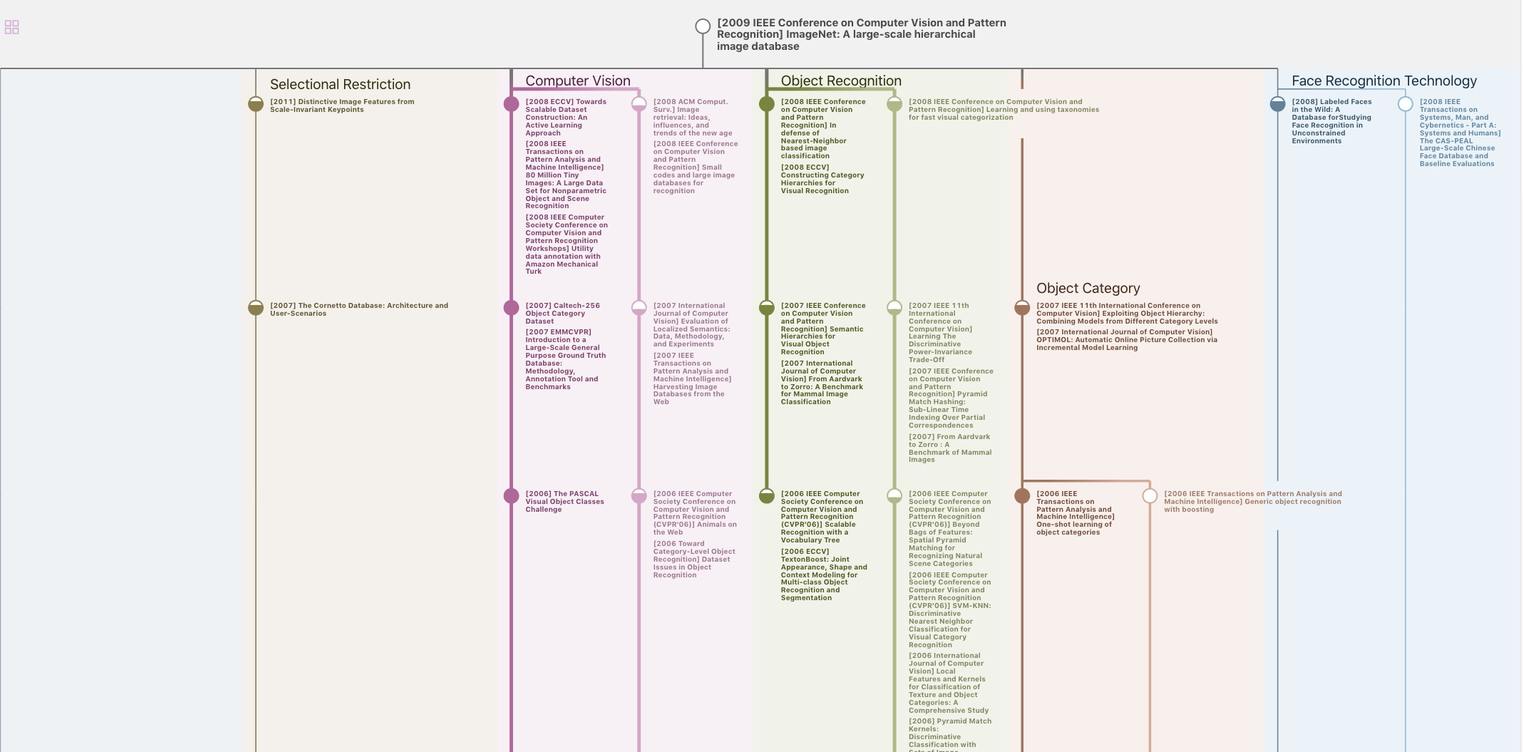
生成溯源树,研究论文发展脉络
Chat Paper
正在生成论文摘要