Optimizing The Geometric Parameters Of Cutting Edge For The Finishing Machining Of 30cr Alloy Steel
INTERNATIONAL JOURNAL OF COMPUTATIONAL METHODS(2019)
摘要
In order to optimize the geometric parameters of cutting edge for the finishing machining of 30Cr alloy steel, a two-dimensional (2D) finite element (FE) model of orthogonal cutting was built with FE software AdvantEdge. The optimized methodology of the cutting edge geometric parameters was likewise proposed based on the simulated results. Thereafter, the geometric parameters of the cutting edge were optimized based on a comprehensive criterion that combines chip deformation coefficient and tool stress. The chip deformation coefficient indirectly determines the surface roughness, whereas tool stress determines tool wear, thereby affecting the dimensional precision of the components. The rake angle ranges from 12 degrees to 20 degrees while the cutting edge radius ranges from 12 mu m to 20 mu m in the optimization process. The optimal rake angle for the finishing machining 30Cr alloy steel is 16 degrees, while the optimal cutting edge radius is 14 mu m with a given relief angle of 7 degrees.
更多查看译文
关键词
Numerical simulation, finishing machining, chip deformation coefficient, tool stress, geometric parameters of cutting edge
AI 理解论文
溯源树
样例
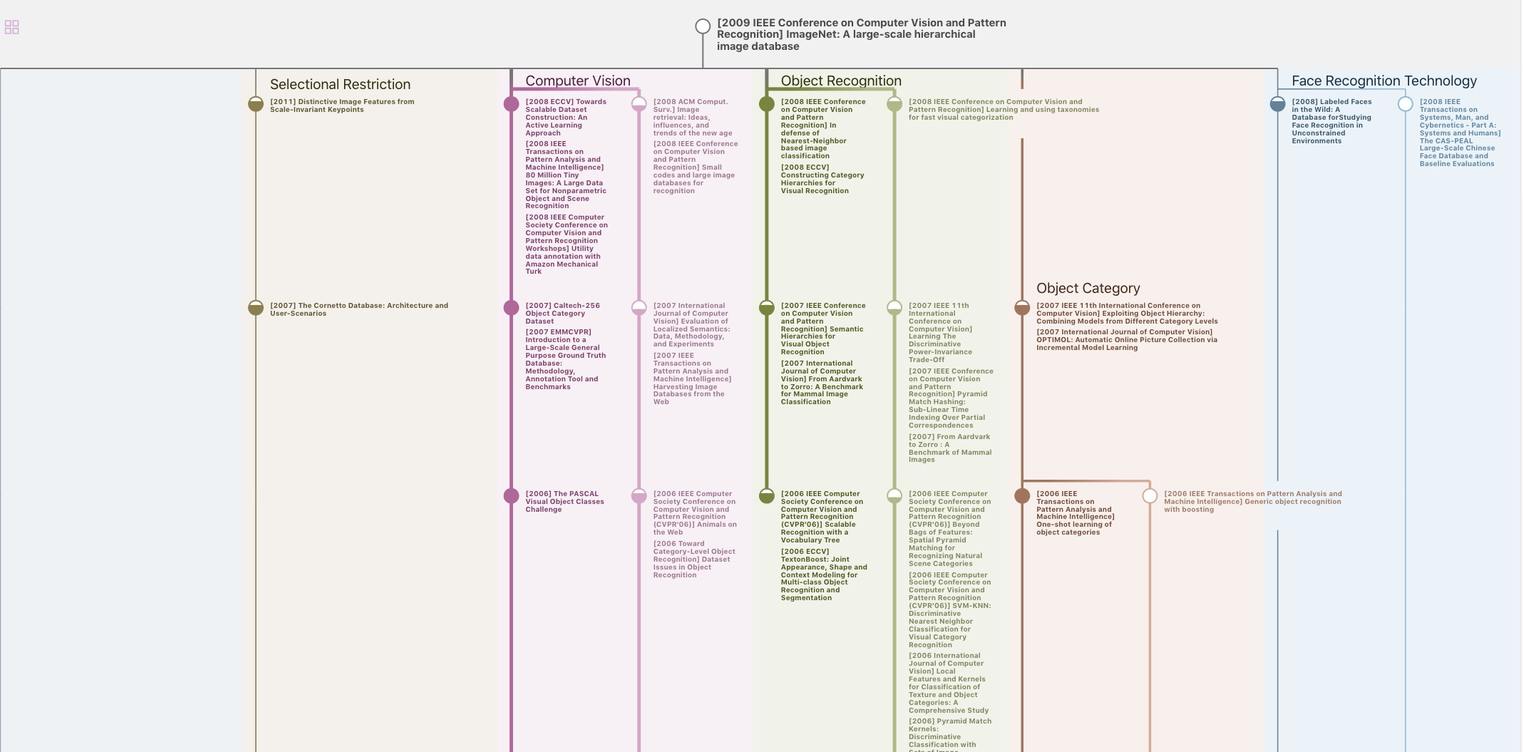
生成溯源树,研究论文发展脉络
Chat Paper
正在生成论文摘要