IR Thermographic Analysis of 3D Printed CFRP Reference Samples with Back-Drilled and Embedded Defects
Journal of Nondestructive Evaluation(2018)
摘要
Carbon-fiber composite structures may demonstrate a defective behavior due to manufacturing induced anomalies (delamination, dis-bonds) or service related defectives (impact damage, water ingress). Thus, there is a need for a relatively fast and low cost non-intrusive testing schemes such as infrared thermography (IRT). Still, thermography testing requires calibrated samples and coupons to yield best results. The presented research demonstrates the novel use of 3D printing technology to generate IRT calibration samples. In this text, two carbon fiber reinforced polymer samples are 3D printed; the first mimics a “back-drilled holes” type coupons, while the other is designed to embed air pockets similar to Teflon inserts. The generated samples are then tested using two IRT modalities; namely pulse thermography and lock-in thermography. Furthermore, the resulted thermograms are processed using a principle component analysis, to help highlight the variance of defectives in a consistent manner among the samples. This research findings offer insights on the variation of detectability between embedded and back-printed samples, which might be due to the inserts thickness.
更多查看译文
关键词
Thermography, Composites CFRP, Back drilled holes, Calibration, 3D printing
AI 理解论文
溯源树
样例
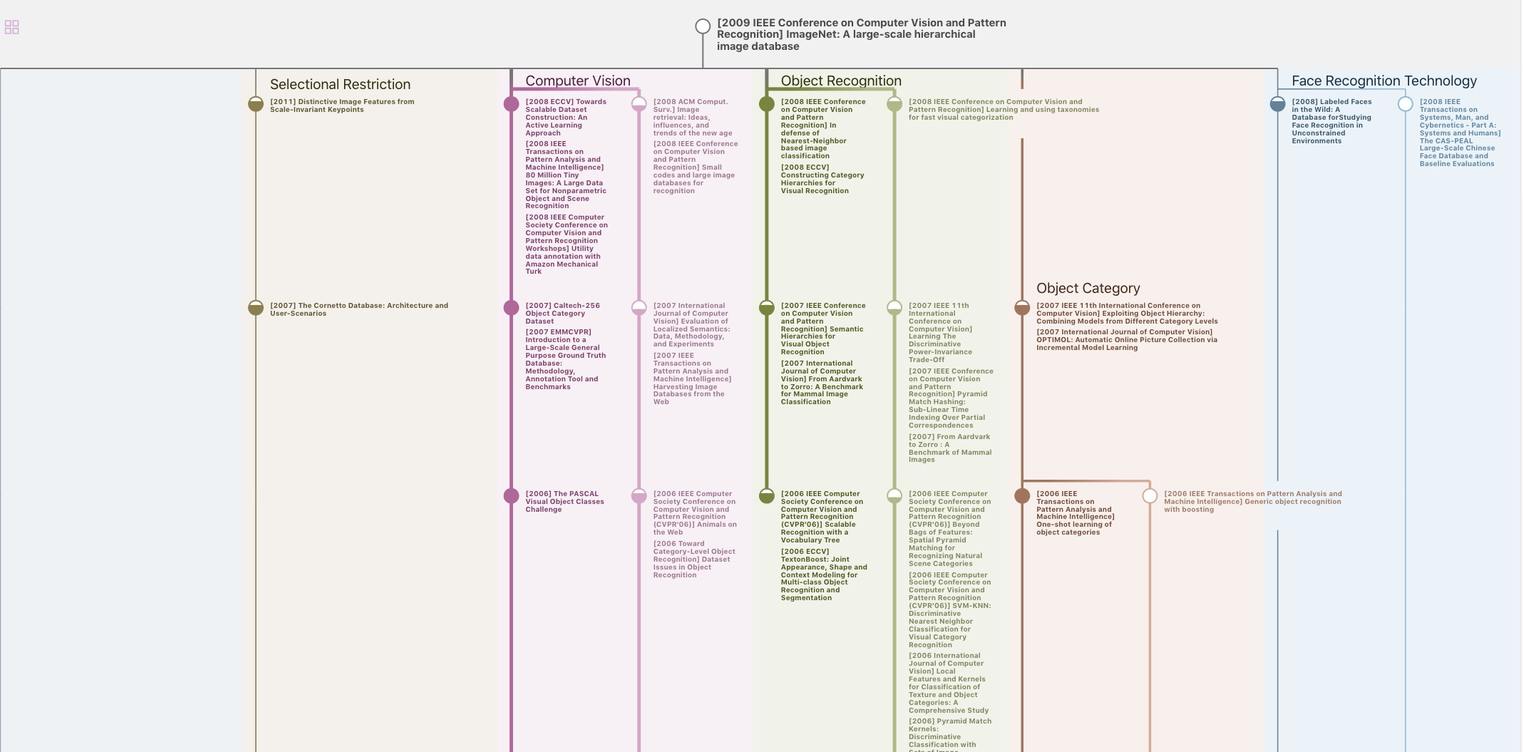
生成溯源树,研究论文发展脉络
Chat Paper
正在生成论文摘要