Thermal performance optimization in electric vehicle power trains by locally orthotropic surface layer design
JOURNAL OF MECHANICAL DESIGN(2018)
摘要
In this paper, the application of orthotropic material orientation optimization for controlling heat flow in electric car power trains is presented. The design process is applied to a case model, which conducts heat while storing heat-sensitive electronic components. The core of the case is designed using a low thermal conductivity material on order to focus the heat flow into the surface layer, which is designed using a high thermal conductivity material. Material orthotropy is achieved in the surface layer of the case by removing the material at points determined by the optimization analysis. For this purpose, an orthotropic material orientation optimization method was extended to calculate optimal material distribution. This is achieved by transforming the initially obtained optimal orientation vector field into a scalar field through the use of coupled time-dependent nonisotropic Helmholtz equations. Multiple parameters allow the control of the scalar field and therefore the control over material distribution in accordance to the optimal orientation. This allows the material distribution pattern to be scaled depending on the desired manufacturing method. The analysis method is applied to divert heat flow from a specific section of the model while focusing the heat flow to another section. The results are shown for a model with a 0.1 mm thick surface layer of copper and are compared to those results from several other materials and layer thicknesses. Finally, the manufactured design is presented.
更多查看译文
AI 理解论文
溯源树
样例
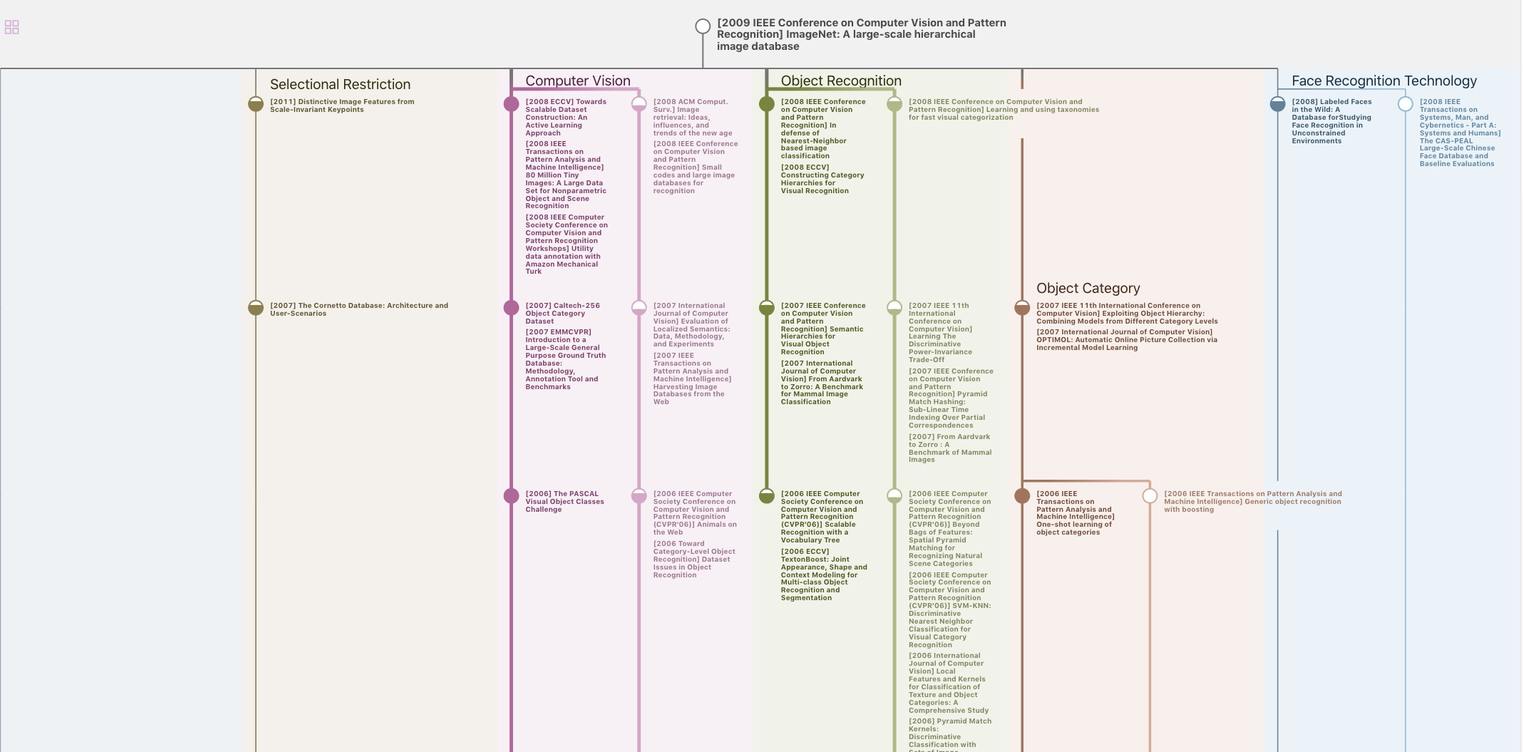
生成溯源树,研究论文发展脉络
Chat Paper
正在生成论文摘要