Stochastic micromechanical modeling of transverse punch shear damage behavior of unidirectional composites
JOURNAL OF COMPOSITE MATERIALS(2019)
摘要
Punch shear in unidirectional composites is induced by transverse shear loading that progressively perforates the laminate within a narrow shear annulus. At lower micromechanical length scales, punch shear loading creates unique micromechanical damage mechanisms dominated by transverse fiber shear failure, fiber-matrix interphase debonding and large inelastic deformation and cracking of the matrix. A new punch shear experimental method has been developed to test unidirectional S glass/DER353 epoxy composite ribbons at sub-millimeter length scale. The experimental data consist of a statistical measurement of the continuum response (load-deformation and punch shear strength) and the characterization of micromechanical damage modes. A simplified 2D micromechanical finite element model incorporating Weibull fiber strength distribution has been developed and correlated with the experimental data. The 2D micromechanical finite element model can simulate the punch shear failure of the ribbon incorporating mixed mode fiber fracture, and fiber-matrix debonding mechanisms using zero thickness cohesive elements. Results from stochastic simulations of punch shear experiments show that an equivalent 2D micromechanical finite element model can predict the micromechanical damage mechanisms and the statistical distribution of punch shear strength of the continuum with favorable correlation with the experiments. This paper presents a combined experimental and computational approach in simulating the stochastic non-linear progressive punch shear behavior of unidirectional composites for the first time in the literature.
更多查看译文
关键词
Punch shear,unidirectional composites,micromechanical modeling,fiber fracture,fiber-matrix interface debonding,matrix plasticity
AI 理解论文
溯源树
样例
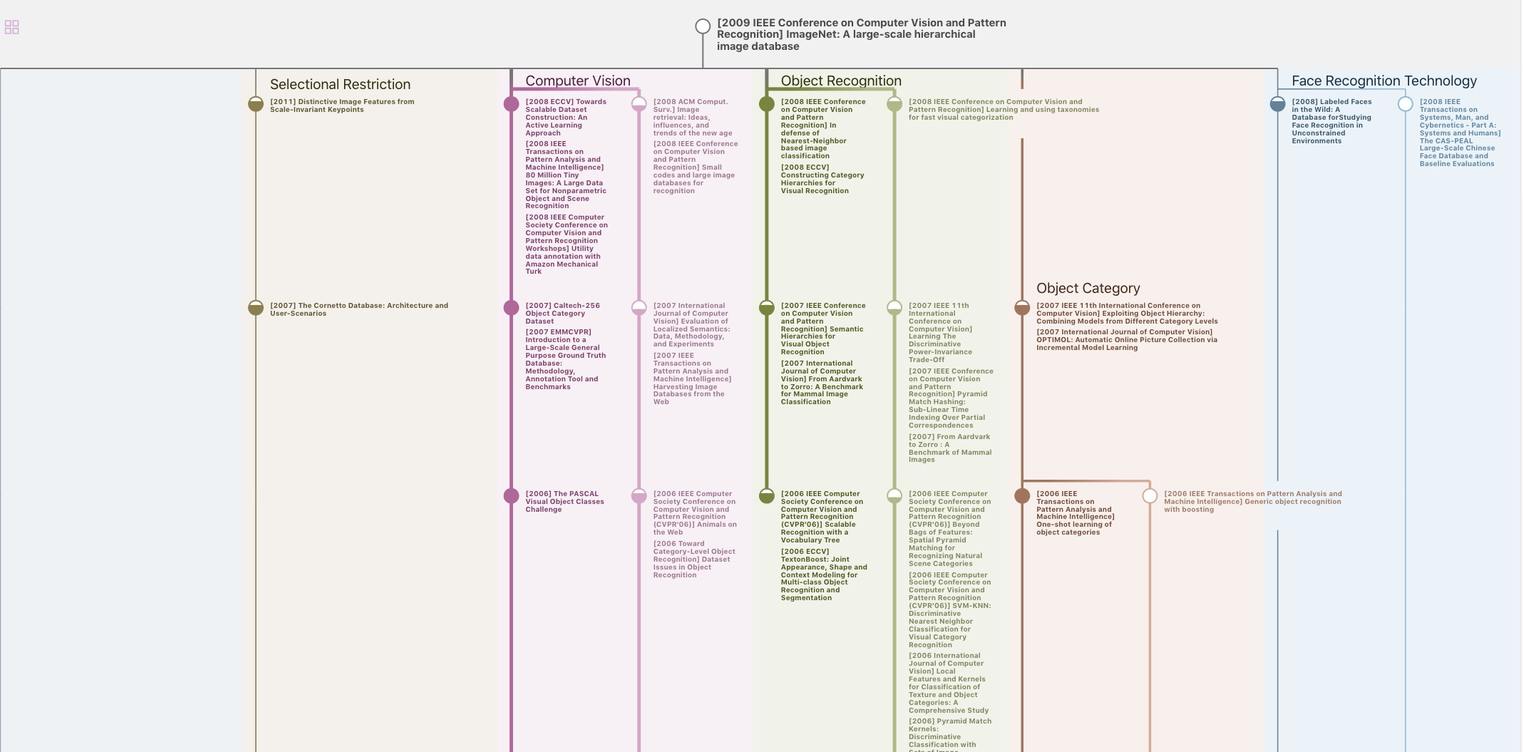
生成溯源树,研究论文发展脉络
Chat Paper
正在生成论文摘要