Interlaminar modelling to predict composite coiled tube failure
The APPEA Journal(2015)
摘要
In a field operation that uses coiled tubing in its applications, fibre-reinforced polymer matrix composite tubing is seldom used. Fibre-composite coiled tubes offer advantages, compared to steel material, through a reduction in weight and improvement in fatigue life. The stiffness of composite material degrades progressively when increasing the number of cyclic loading. The fatigue damage and failure criteria of fibre-reinforced composite coiled tubes are more complex than that of steel; hence, failure predictions are somewhat unreliable. Among the defects in composite materials, interlaminar delamination is the foremost problem in fibre-reinforced composite material, and it leads to a reduction in strength and stiffness especially in cyclic-load conditions. Delamination causes a redistribution of the load path along the composite structure, which is unpredictable; therefore, delamination in a composite coiled tube in an oil and gas field eventually leads to final failure, which could be catastrophic. A-ply-by-ply mathematical modelling and numerical simulation method was developed to predict interlaminar delamination of filament-wound composite coiled tubes under a combination of different loading scenarios with consideration to low-cycle fatigue. The objective of this paper is to explain interlaminar delamination as an initial crack and source of stress concentration in composite coiled tubes in the framework of meso-cracking progression of matrix damage modelling of composite laminates. The paper focuses on delamination failure because the largest span of the composite lifecycle is at the crack propagation phase, which manifests itself in the form of delamination. The analysis shows that the crack front tip is not uniform, and also shows that carbon fibre possesses higher stiffness values compared to glass fibre. The paper confirms that 2D modelling cannot express the real release strain energy rate at the crack front tip. Mode-I testing, however, showed that the double cantilever beam (DCB) only represents the normal stress from the release strain energy rate. The results also indicated that there were other sources contributing to the strain energy release rate, such as inter-layer frictions and normal stress in the end notched flexure (ENF) testing mode.
更多查看译文
AI 理解论文
溯源树
样例
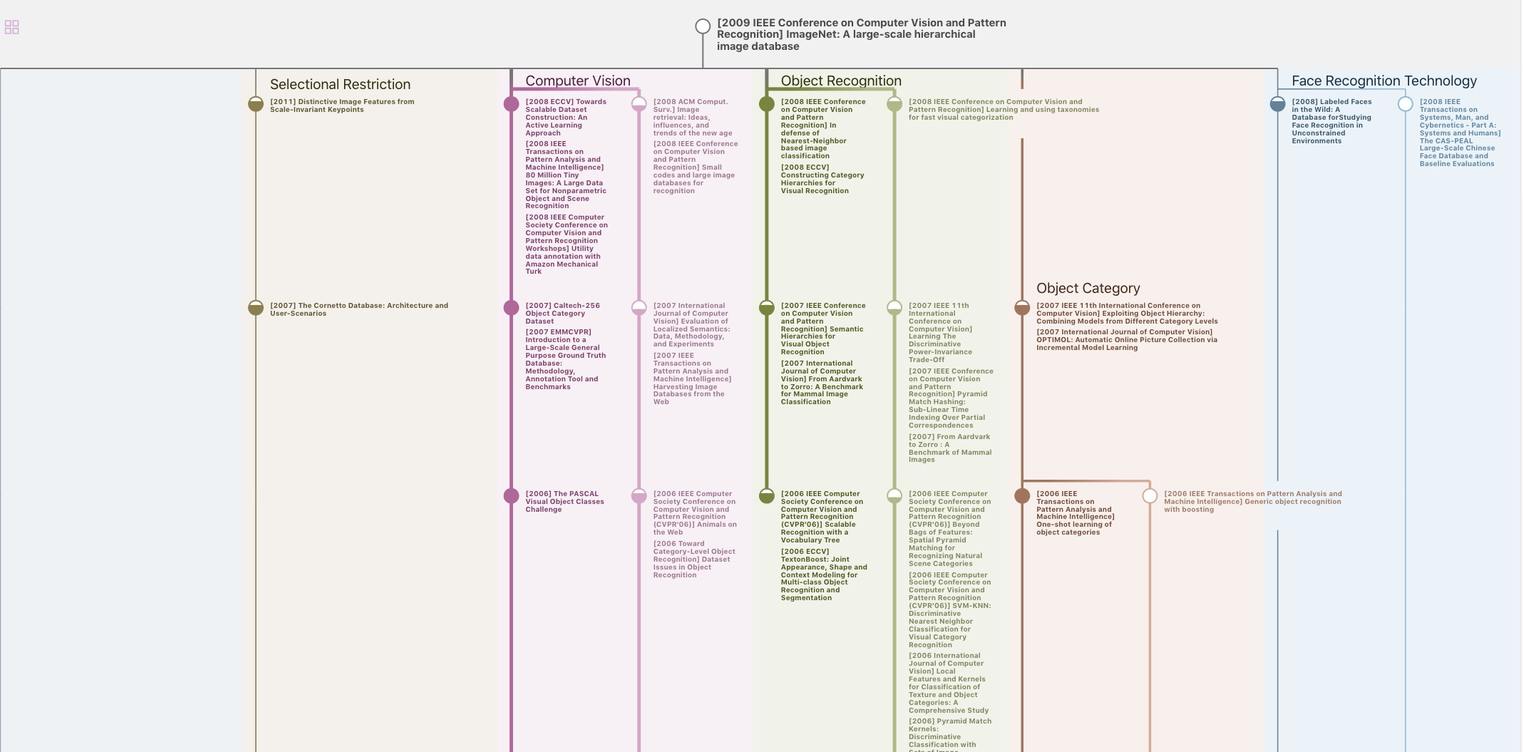
生成溯源树,研究论文发展脉络
Chat Paper
正在生成论文摘要