3D printing assisted finite element analysis for optimising the manufacturing parameters of a lumbar fusion cage
Materials & Design(2019)
摘要
The study herein combines the use of fused filament fabrication (FFF) with finite element analysis (FEA) to enhance the understanding of certain manufacturing parameters (i.e. material, infill density, infill pattern, and outer vertical shell) in the design process of a lumbar fusion cage. Three FFF materials with distinct mechanical properties namely polycarbonate (PC), acrylonitrile butadiene styrene (ABS), and polylactic acid (PLA) were tested. Three infill densities (i.e. 25%, 50%, 75%) were investigated along with two different infill patterns (i.e. rectangular and honeycomb). Compressive modulus and compressive yield strength values obtained from standard mechanical analysis were used as input for FEA to assess numerically the mechanical performance of a lumbar fusion cage under physiological static loading. The findings suggest that both infill density and infill pattern influence the quality of the finished part in terms of both printing accuracy and mechanical response. FEA results indicate that both PC and ABS can be safely adopted to fabricate a porous lumbar cage with a 50% honeycomb infill density and a honeycomb infill pattern. This paper demonstrates that 3D printing assisted FEA can be used to predict the performance of a lumbar cage design with varying manufacturing parameters and potentially reduce product design and development time.
更多查看译文
关键词
ABS,CAD,DSC,Ec,FEA,FFF,IVG,Ns,PC,PLA,SEM,SLA,σcy,μCT
AI 理解论文
溯源树
样例
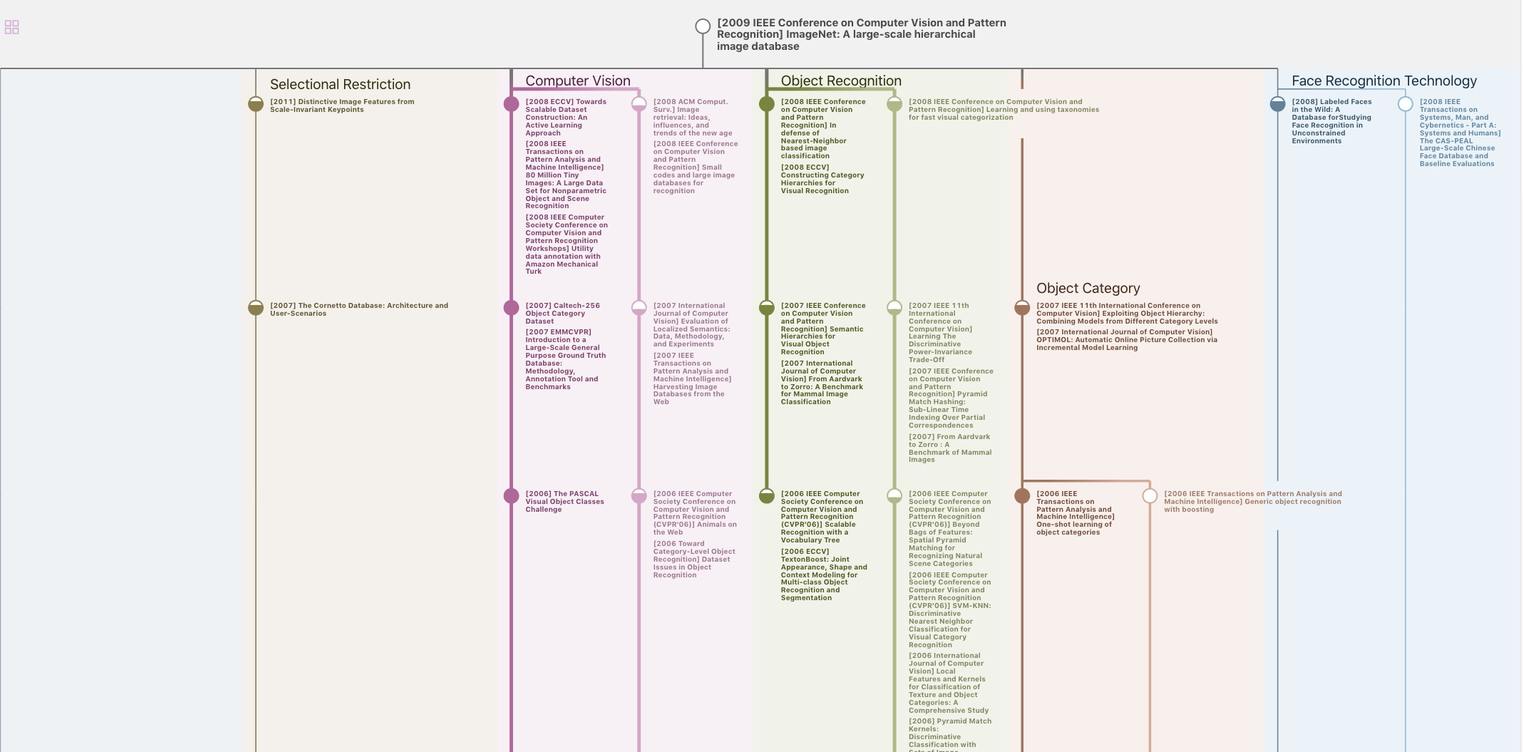
生成溯源树,研究论文发展脉络
Chat Paper
正在生成论文摘要