A Human-Guided Vision-Based Measurement System for Multi-Station Robotic Motion Platform Based on V-Rep
ROBOTICA(2020)
摘要
In the manufacturing process of sophisticated and individualized large components, classical solutions to build large machine tools cannot meet the demand. A hybrid robot, which is made up of a 3 degree-of-freedom (3-DOF) parallel manipulator and a 2-DOF serial manipulator, has been developed as a plug-and-play robotized module that can be rapidly located in multi-stations where machining operations can be performedin situ. However, processing towards high absolute accuracy has become a huge challenge due to the movement of robot platform. In this paper, a human-guided vision system is proposed and integrated in the robot system to improve the accuracy of the end-effector of a robot. A handheld manipulator is utilized as a tool for human-robot interaction in the large-scale unstructured circumstances without intelligence. With 6-DOF, humans are able to manipulate the robot (end-effector) so as to guide the camera to see target markers mounted on the machining datum. Simulation is operated on the virtual control platform V-Rep, showing a high robust and real-time performance on mapping human manipulation to the end-effector of robot. And then, a vision-based pose estimation method on a target marker is proposed to define the position and orientation of machining datum, and a compensation method is applied to reduce pose errors on the entire machining trajectory. The algorithms are tested on V-Rep, and the results show that the absolute pose error reduces greatly with the proposed methods, and the system is immune to the motion deviation of the robot platform.
更多查看译文
关键词
Human-guided manipulator,Vision-based measurement system,Pose estimation,5-DOF hybrid robot,V-Rep
AI 理解论文
溯源树
样例
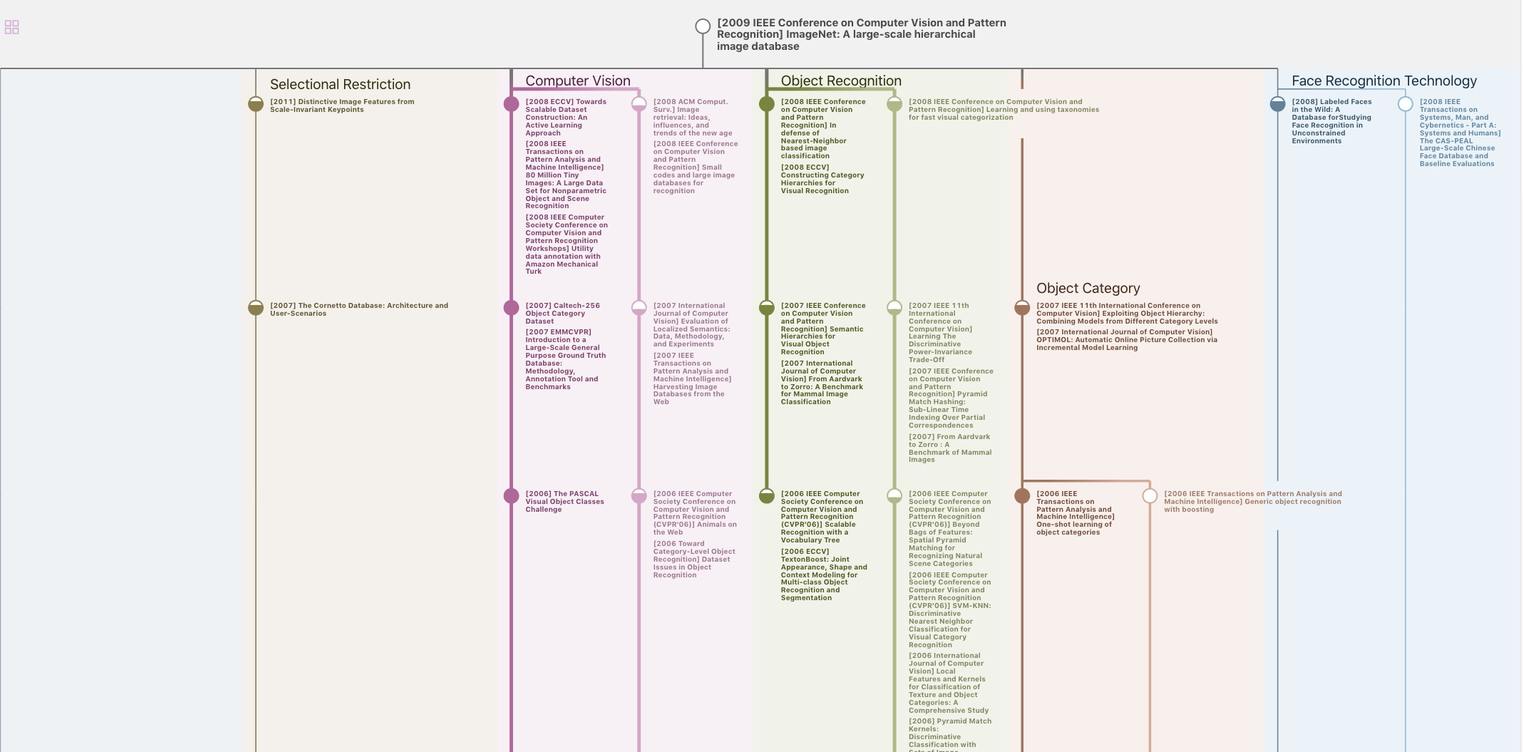
生成溯源树,研究论文发展脉络
Chat Paper
正在生成论文摘要