Inferring the Material Properties of Granular Media for Robotic Tasks
ICRA(2020)
摘要
Granular media (e.g., cereal grains, plastic resin pellets, and pills) are ubiquitous in robotics-integrated industries, such as agriculture, manufacturing, and pharmaceutical development. This prevalence mandates the accurate and efficient simulation of these materials. This work presents a software and hardware framework that automatically calibrates a fast physics simulator to accurately simulate granular materials by inferring material properties from real-world depth images of granular formations (i.e., piles and rings). Specifically, coefficients of sliding friction, rolling friction, and restitution of grains are estimated from summary statistics of grain formations using likelihood-free Bayesian inference. The calibrated simulator accurately predicts unseen granular formations in both simulation and experiment; furthermore, simulator predictions are shown to generalize to more complex tasks, including using a robot to pour grains into a bowl, as well as to create a desired pattern of piles and rings.
更多查看译文
关键词
granular media,material properties
AI 理解论文
溯源树
样例
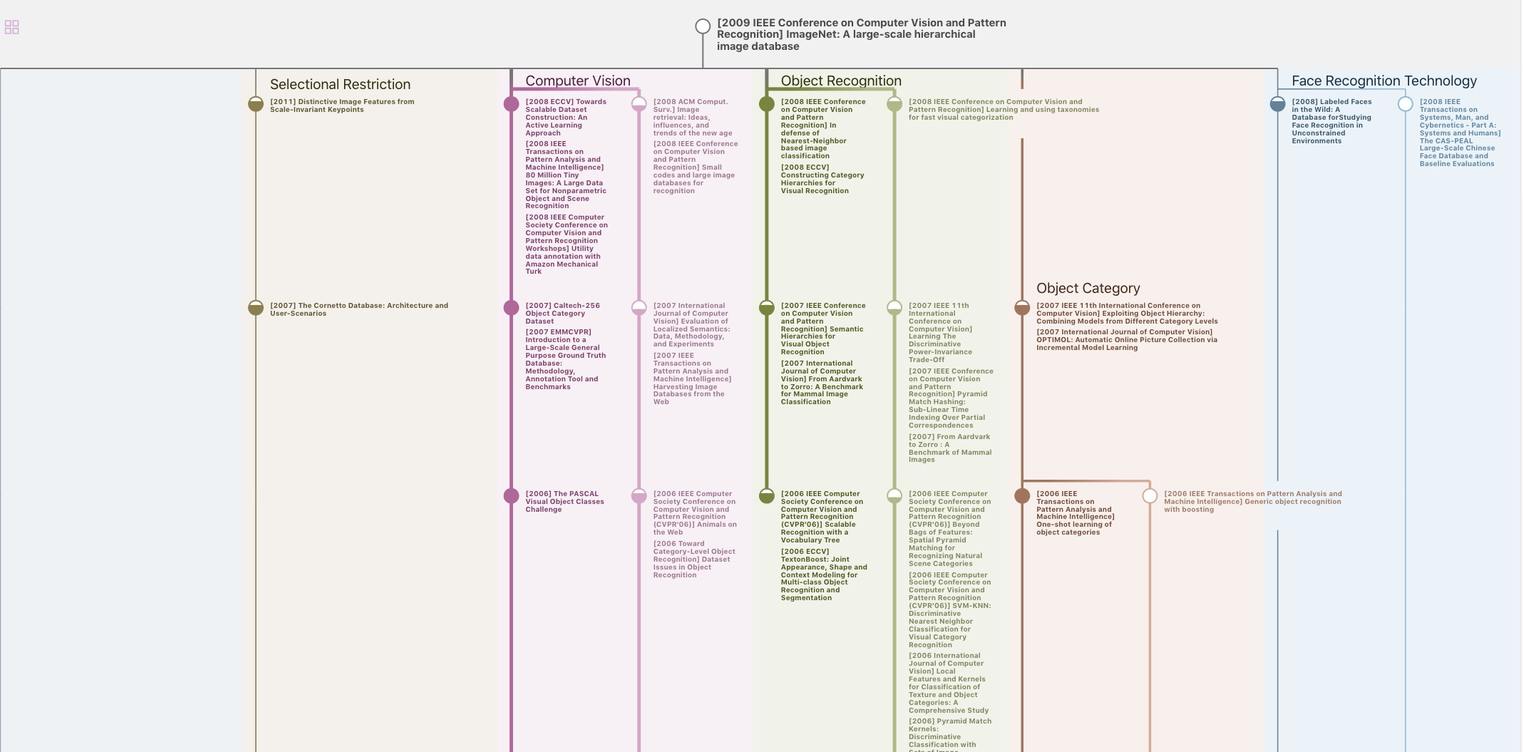
生成溯源树,研究论文发展脉络
Chat Paper
正在生成论文摘要