Improvement of the Homogeneity of Atomized Particles Dispersed in High Uranium Density Research Reactor Fuels
semanticscholar(1998)
摘要
A study on improving the homogeneous dispersion of atomized spherical particles in fuel meats has been performed in connection with the development of high uranium density fuel. In comparing various mixing methods, the better homogeneity of the mixture could be obtained as in order of Spex mill, V-shape tumbler mixer, and offaxis rotating drum mixer. The Spex mill mixer required some laborious work because of its small capacity per batch. Through optimizing the rotating speed parameter for the V-shape tumbler mixer, almost the same homogeneity as with the Spex mill could be obtained. The homogeneity of the extruded fuel meats appeared to improve through extrusion. All extruded fuel meats with U3Si powder of 50-volume % had fairly smooth surfaces. The homogeneity of fuel meats by V-shaped tumbler mixer revealed to be fairly good on micrographs. Introduction Low enriched uranium (LEU) fuel has been developed to replace high enriched uranium (HEU) fuel in research and test reactors since 1978 [1-2]. Low enriched U3Si2-Al dispersion fuel has been converted in many research reactors [3]. However, the application of the fuel is limited to approximately 90% of all research reactors due to the uranium density of 4.8g/cm. Several high performance reactors still require a higher uranium density fuel up to 8de9 g-U/cm [4]. Uranium density in dispersion fuel can increase basically by choosing a fuel material with higher uranium density or increasing the fuel powder fraction in fuel meats. In the latter method, the fuel powder should be dispersed homogeneously in fuel meat. In general, the homogeneously mixing of fuel and aluminum powders is difficult due to a greater difference of densities. In case that the fuel particles are segregated locally, the segregated area with fuel powder is easy to induce voids during fabrication as well as has an adverse effect on in-reactor performance. As the homogeneity of mixed powders is improved, the fuel powder loading would increase possibly. At KAERI, the atomization process has been applied to the fabrication of dispersion fuels since about 10 years ago [5]. The comminuted fuel particles have angular shapes, while the atomized fuel particles have spherical shapes with smooth surfaces. The homogeneity of mixed powders might be varied with the particle shape. The results of BWXT showed that the atomized U3Si2 spherical particles were more segregated in fuel meat than the comminuted particles [6]. In this study, the homogeneity was evaluated by standard deviation of the measured apparent densities for the mixed powders and fuel meats. The influences of particle shape and density on the homogeneity were investigated. Three kinds of mixing methods, which are the off-axis rotating drum mixing, Spex mill mixing, and V-shape tumbler mixing, were compared by the homogeneity of the fuel powder mixtures with aluminum powder and the fuel meats. An effort was made to choose the mixing method suitable for the atomized spherical fuel powder and to optimize the mixing parameters. Using the optimized mixing parameters, the dispersion fuels with high uranium density were fabricated and examined. Experimental Procedures The homogeneity of the powder mixture was evaluated by the standard deviations of composition calculated from the apparent densities measured for a number of samples taken from the powder mixture. The apparent densities of samples were measured using the Hall Flow Meter consisting of a precision volume cup and a funnel. For the fuel meats, the densities were measured for the samples taken by cutting fuel rods. In order to investigate the effect of a different particle shape on the homogeneity, two kinds of powders, which are Cu-Sn alloy powder spherical and irregular Cu powder, were mixed with Al powder using the Spex mill mixer and off-axis rotating drum mixer, and then compared for homogeneity. Using atomized and comminuted U3Si powders the comparison of homogeneity was also performed. The influence of the density difference of powders on homogeneity of mixture was investigated by mixing spherical Cu-Sn and U3Si powders in an off-axis rotating drum mixer. A mixing test for the irregular Cu powders with different size distributions and Al powders was carried out using the off-axis rotating drum mixing method. The homogeneities of mixtures were compared for various size distributions of Cu powders. Atomized U3Si powders were mixed with Al powders in three kinds of mixing methods, which are off-axis rotating drum mixer, Spex mixer and V-shape tumbler mixer. The angle between the cylinder and the centerline in the off-axis rotating drum mixer is 40°. The volume fraction of the powders charged in mixer is between 25 and 40 %. The operating conditions of mixers are as shown in Table 1. For the selected mixing method suitable for atomized powders, the operating parameters such as rotating speed and time were optimized. Using the optimized mixing conditions, the fuel meats with high fuel powder fraction were prepared and investigated for the homogeneity in comparison with the previously fabricated ones. Table 1. Operation conditions of three kinds of mixers Off-Axis Rotating Drum Mixer Spex Mill V-shape Tumbler Mixer Rotating Speed (RPM) 50 1,700 25,50,75 Amount of Mixture (cm) 50 10 50 Results and Discussion The spherical Cu-Sn powder showed to have less homogeneous distribution in Al powder than the irregular Cu powder in off-axis drum mixing and Spex mill mixing methods as shown in Figure 1. The apparent densities of Cu-Sn and Cu powders are 5.07 g/cm and 2.92 g/ cm. If considering that the true densities of those powders are 8.87 g/cm and 8.9 g/cm, respectively, the irregular Cu powder has a greater amount of voids than the spherical powder. It is assumed that the voids allow small aluminum particles to be seated. The irregular shape powder with a rough surface is considered to have more friction to the flow of aluminum powder. The comminuted U3Si powder with an irregular shape was shown to have a little smaller standard deviation in mixture than the atomized powder with a spherical shape as shown in Figure 2. 0 1 2 3 4 5 6 7 8 9 10 0.00 0.04 0.08 0.12 0.16 0.20 Off-axis Rotating Drum Mixer 50 Vol. % Al Powder Mixture Rotating Speed : 50 rpm Spherical Powder : Cu-Sn Irregular Powder : Cu St an da rd D ev ia tio n Mixing Time, Hours 0 10 20 30 40 50 60 0.00 0.04 0.08 0.12 0.16 0.20 Spex Mill 50vol% Al Powder Mixture Spherical Powder : Cu-Sn Irregular Powder : Cu St an da rd D ev ia tio n
更多查看译文
AI 理解论文
溯源树
样例
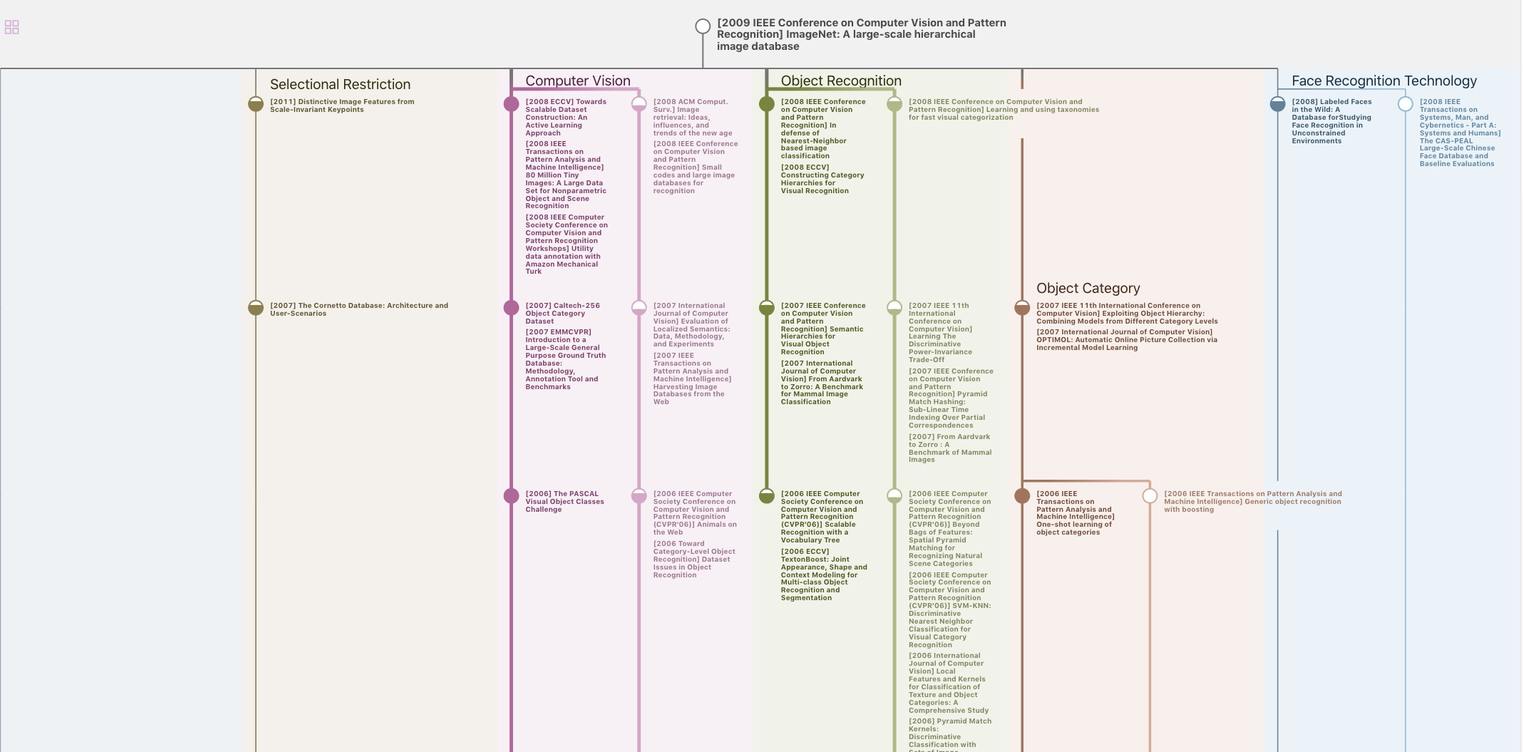
生成溯源树,研究论文发展脉络
Chat Paper
正在生成论文摘要