A Two-Step Fabrication Method for 3D Printed Microactuators: Characterization and Actuated Mechanisms
Journal of Microelectromechanical Systems(2020)
摘要
The fabrication and integration of microactuators with 3D micromechanisms are necessary to develop microrobots with higher capability and complexity. In this work, a two-step fabrication method combining 3D printing with two-photon polymerization (TPP) and aluminum sputtering is demonstrated. Actuators using two different transduction mechanisms (thermal and electrostatic) were fabricated in this process, and a thermal actuator was printed with a mechanism in three-dimensional space without additional assembly steps. This work also provides parameterized characterizations which can be used as design guidelines for building actuators and mechanisms. A design approach to electrically isolate the actuators from the substrate is introduced so that the device can be functional after two fabrication steps without patterning the metal layer. Metal coverage on the sidewalls of trenches are characterized, which provides a design space for deciding electrode gaps and heights in electrostatic actuators. Using these guidelines, 500 μm long thermal actuators showed a maximum displacement of 18.0 μm at 8.31mW and reliably actuated up to 8,500 cycles. An interdigitated electrostatic comb-drive actuator was also successfully demonstrated, displacing 12.7 μm when 160V was applied. Finally, a 3D actuated mechanism was designed by incorporating a thermal actuator with 3D compliant mechanisms to flap 250 μm long wings. Flapping motion was successfully demonstrated. [2020-0010].
更多查看译文
关键词
Microactuators,microelectromechanical systems (MEMS),microfabrication,microrobotics,3D printing,two-photon polymerization (TPP)
AI 理解论文
溯源树
样例
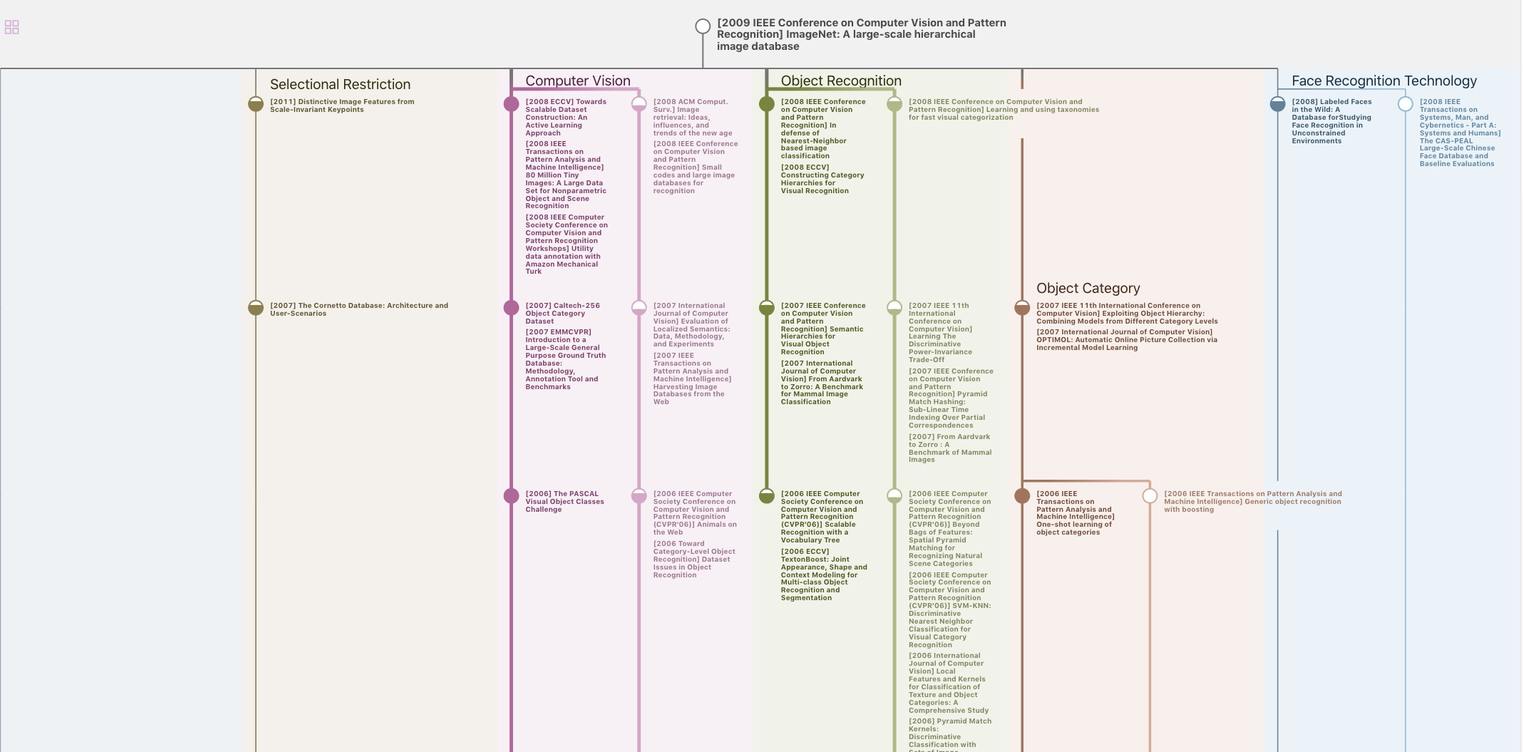
生成溯源树,研究论文发展脉络
Chat Paper
正在生成论文摘要