Modeling and optimization for rotary ultrasonic face milling of carbon fiber reinforced polymers
MATEC Web of Conferences(2017)
摘要
Carbon fiber reinforced polymers (CFRP) have got paramount importance in aerospace, and other industries due to their attractive properties of high specific strength, high specific stiffness, high corrosion resistance, and low thermal expansion. However, due to their properties like heterogeneity, anisotropy, and low heat dissipation, the issues in machining like excessive cutting forces and high surface roughness have found. In this research, a cutting force model has developed for rotary ultrasonic face milling of CFRP composites. The experimental machining was carried out on CFRP-T700. From the analysis, it has found that experimental and simulation values of cutting forces have variation/error below than 10% in the most of the groups of parameters. However, the error found higher in few cases, due to heterogeneity, anisotropy and some other properties of these materials. The formula for contact area of the abrasive core tool improved and an overlapping cutting allowance has applied the first time. The optimal combination of parameters has investigated for cutting force and surface roughness. The developed cutting force model then further validated with pilot experiments and found the same results. So, the model developed in this paper is robust and can be applied to predict cutting force and optimization.
更多查看译文
AI 理解论文
溯源树
样例
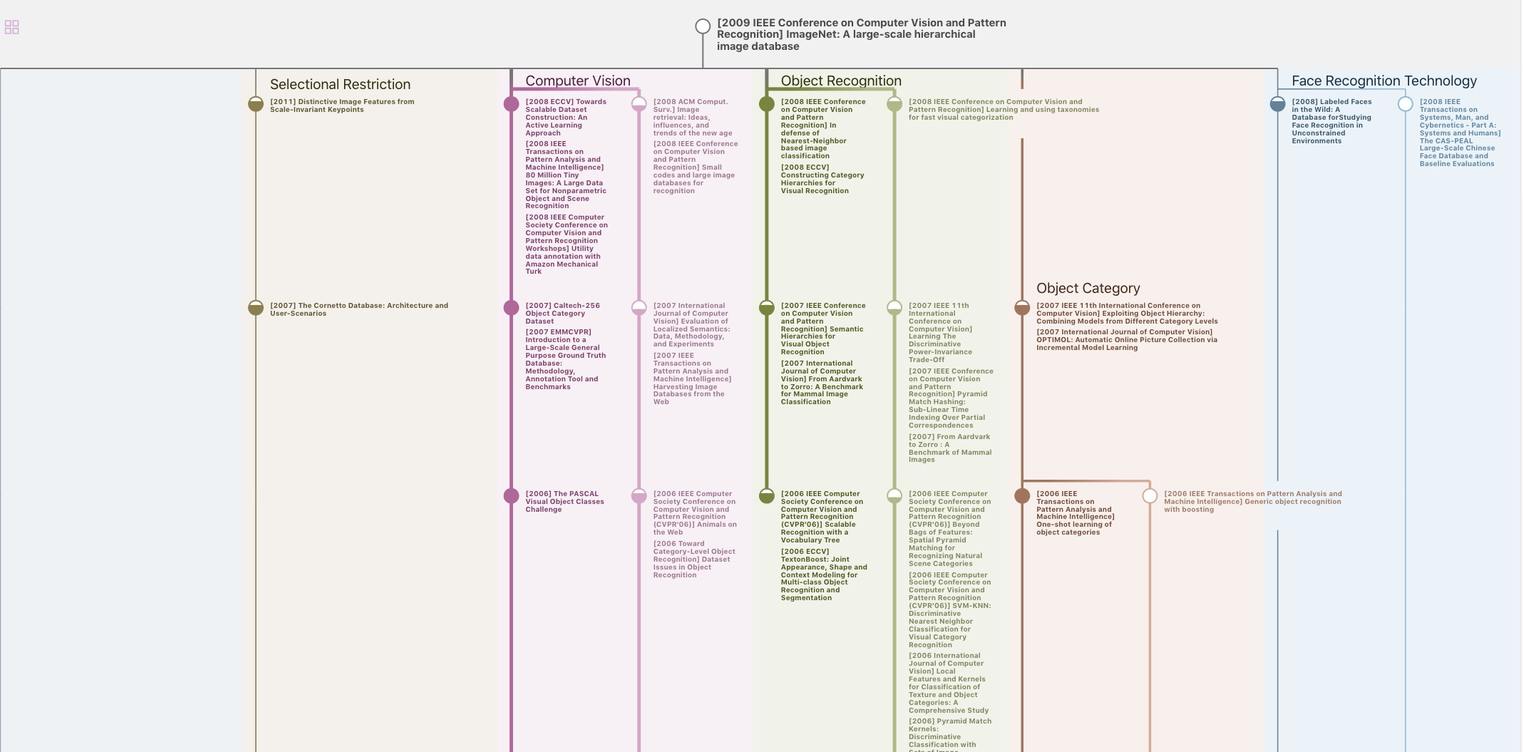
生成溯源树,研究论文发展脉络
Chat Paper
正在生成论文摘要