Experimental Comparison Of Optical Inline 3d Measurement And Inspection Systems
IEEE ACCESS(2021)
摘要
Fast optical 3D inline inspection sensors are a powerful tool to advance factory automation. Many of these visual inspection tasks require high speeds, high resolutions, and repeatability. Stereo vision, photometric stereo, light sectioning, and structured light are the most common principles for inline imaging in the several micrometers to sub-millimeter resolution range. Selecting the correct sensor principle can be challenging as manufacturers' datasheets frequently use different values to describe their systems and do not stick to proposed characterizations defined by the "Initiative Fair Data Sheet'' or the VDE/VDI standards. With the help of standardized parameters, this paper aims to compare four different measurement principles, namely AIT's own single sensor light field camera method, a structured light pattern projector, a laser triangulation sensor, and a stereo camera system, with an approximate field of view of 100 x 100mm. We demonstrate simple yet meaningful experiments to determine lateral resolution, temporal noise, and calibration accuracy to enable an objective system comparison. Additionally, the reproduction of small surface structures and an overall performance on a challenging test object is evaluated. Results show that the measurement principles partly serve different application areas. The provided methods will help end users to select the correct sensor for specific applications.
更多查看译文
关键词
Automatic optical inspection, optical imaging, measurement accuracy, measurement precision, visual inspection, inline imaging, 3D imaging
AI 理解论文
溯源树
样例
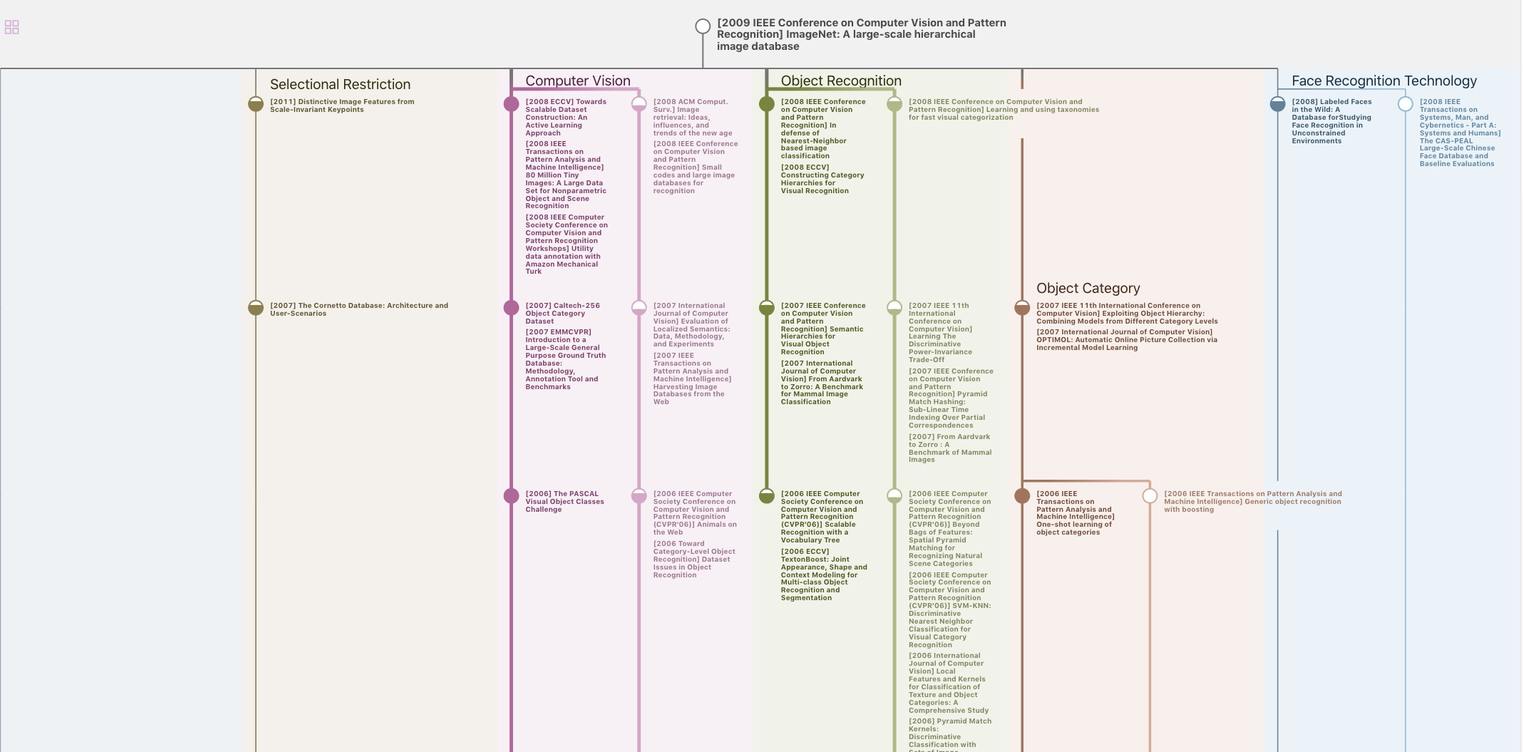
生成溯源树,研究论文发展脉络
Chat Paper
正在生成论文摘要