Automated visual detection of geometrical defects in composite manufacturing processes using deep convolutional neural networks
JOURNAL OF INTELLIGENT MANUFACTURING(2021)
摘要
Detection of fiber composite material boundaries and defects is critical to the automation of the manufacturing process in the aviation industry. This paper describes a process to evaluate four well-performing deep convolutional neural network models (Mask R-CNN, U-Net, DeepLab V3+, and IC-Net) for use in such a process. A custom-captured dataset of images showing fiber cut-pieces with geometrical defects was annotated and augmented for training deep convolutional neural network models; results show acceptable detection accuracy for gripper and fabric based on the Intersection over Union (IoU) scores of up to 0.92 and 0.86, respectively. However, wrinkle detection initially achieves a significantly lower IoU score of 0.40 in the best case. This discrepancy is mainly due to geometrical ambiguities, as wrinkles do not have a clearly defined boundary and are hard to distinguish even for human eye. The model is then evaluated as a binary predictor based on per-component detection success; the model achieves a recall rate (i.e., the ratio of the wrinkles detected to all existing wrinkles) of 0.71 and a precision score (i.e., the ratio of those detected being actually wrinkles) of 0.76. From a practical point of view, this model can outperform a human operator based on the results presented. Two complementary approaches are also introduced for the detection of wrinkles at the early stages of formation as well as the completely formed wrinkles. The developed method can be readily used in a variety of composite manufacturing processes or adapted to other similar tasks.
更多查看译文
关键词
Deep learning, Computer vision, Composite manufacturing, Automation, Robotics, Quality control
AI 理解论文
溯源树
样例
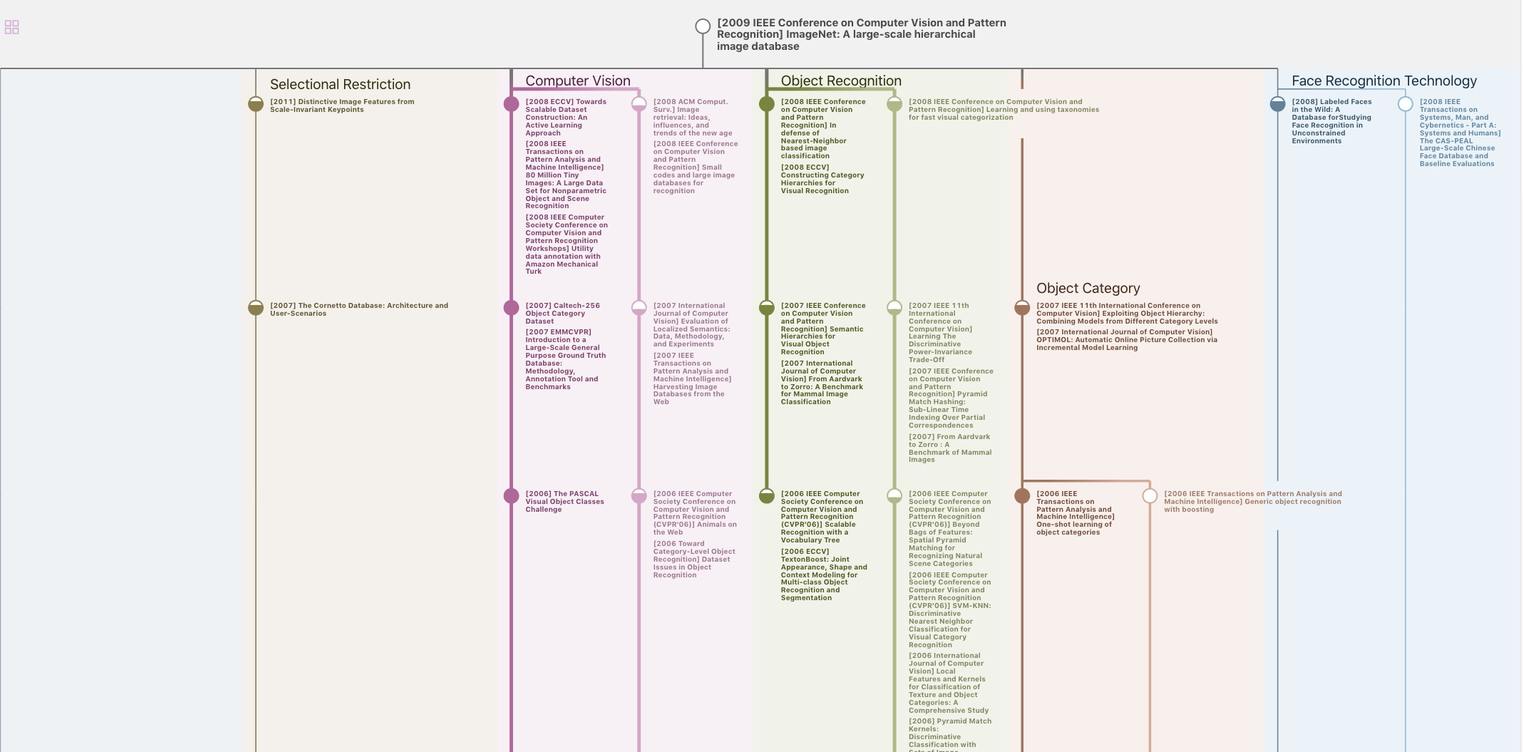
生成溯源树,研究论文发展脉络
Chat Paper
正在生成论文摘要