Design, Analysis and Experimental Study of Metal-3D Printed Conformal Cooling Plastic Injection Mold
MECHANICS OF COMPOSITE AND MULTI-FUNCTIONAL MATERIALS, VOL 5(2020)
摘要
Plastic injection molding is a versatile manufacturing process; constituting a major part of plastic manufacturing industry. Complex sizes and shapes of high-quality everyday products; as well as sophisticated industrial goods are producible with it. In this process, plastic products are manufactured inside a tooling called "mold". Molten plastic is injected inside the mold, the mold is then closed down. After some time, the die (mold) is opened and the solidified plastic product is taken out of the die. To obtain a better-quality plastic product, the design of the injection molding tooling, specifically the design of die core and cavity is very critical. Traditionally straight holes are drilled into the solid dies to cool the hot molten plastic inside the cavity. Cooling process takes up a major portion of the production cycle, leading to high cost of production. With the rising competition worldwide in the plastic product business, it has become very important to lower the production cost, and one way of doing so is to reduce the production cycle time. Using conformal cooling channels is a good option for this purpose. The conformal cooling channels "conforms" to the shape of the final plastic product, and they have the potential to improve the performance of the molding dies in terms of uniform and fast cooling, less warping and defects. This is totally achievable by recent developments in additive manufacturing. In this paper, a comprehensive study is presented, starting from design, simulation, 3D printing process and experimental testing of an injection mold with conformal cooling channels in industrial production environment. A traditional mold model is provided by our industrial collaborator. To enhance the overall thermo-mechanical performance of the mold and improve final product quality, a redesign of this mold core is done with conformal cooling channels inside. The final design is 3D printed in pre-alloyed tool-steel powder using Truprint 3000 metal 3D printing machine. The printed core required some heat treatment and finishing processes and added features to be incorporated to make it production ready. Once all the preparation was complete, the core was tested experimentally in a multicavity injection molding machine in real industrial environment at our industrial partner's production facility. This paper describes all the steps starting from design, analysis, die 3D printing and finally ending at final experimental testing.
更多查看译文
关键词
Injection molding, Conformal cooling, Metal 3D printing, Topology optimization, Experimental testing
AI 理解论文
溯源树
样例
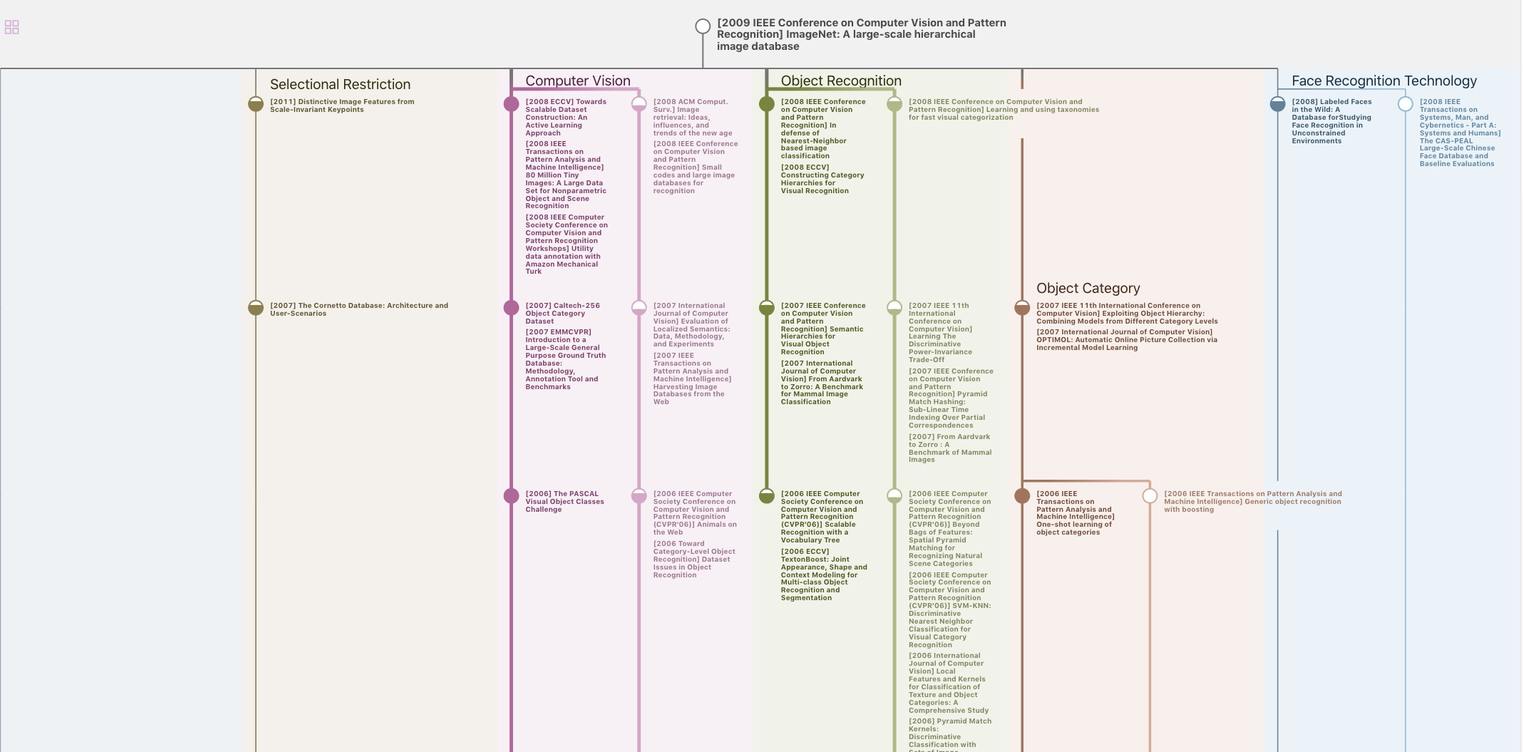
生成溯源树,研究论文发展脉络
Chat Paper
正在生成论文摘要