The Influence Of Partial Force Balancing On The Shaking Moments, Contact Forces, And Precision Of A Delta Robot-Like Manipulator In A Compliant Frame
PROCEEDINGS OF THE ASME INTERNATIONAL DESIGN ENGINEERING TECHNICAL CONFERENCES AND COMPUTERS AND INFORMATION IN ENGINEERING CONFERENCE, 2018, VOL 5B(2018)
摘要
For the Delta robot, a high-speed parallel pick-and-place manipulator, base vibrations are a significant problem. Especially since the Delta robot is suspended above its workpiece, it requires a large, stiff, and heavy base frame for fast and accurate motions. Dynamic balancing of the shaking forces and the shaking moments is a known technique to reduce the dynamic loads on the base frame and to the surroundings. In this paper it is investigated how solely with partial force balancing, dynamic loads and pick-and-place accuracy of a Delta robot-like manipulator can be improved, considering also the compliance of the base frame. This is done since partial force balance solutions can be implemented relatively simply in the current Delta robot designs, whereas full force and moment balance solutions are complex to apply in practice. Numerical simulations with a representative planar model of a Delta robot-like manipulator with a compliant base frame show that with an increasing amount of force balance the shaking moments increase up to 16% for full force balance. The floor contact forces first reduce and then increase with increasing force balance. With 43% force balance the floor contact forces are minimal, giving a 63% reduction. The end-effector accuracy slightly improves with increasing force balance until full force balance yields a 31% accuracy improvement. A further increase of the force (over) balance shows a 59% improvement of end-effector accuracy for 350% force balance. These effects are mainly due to the typical design of the Delta robot base frame and the way the robot is mounted to it.
更多查看译文
AI 理解论文
溯源树
样例
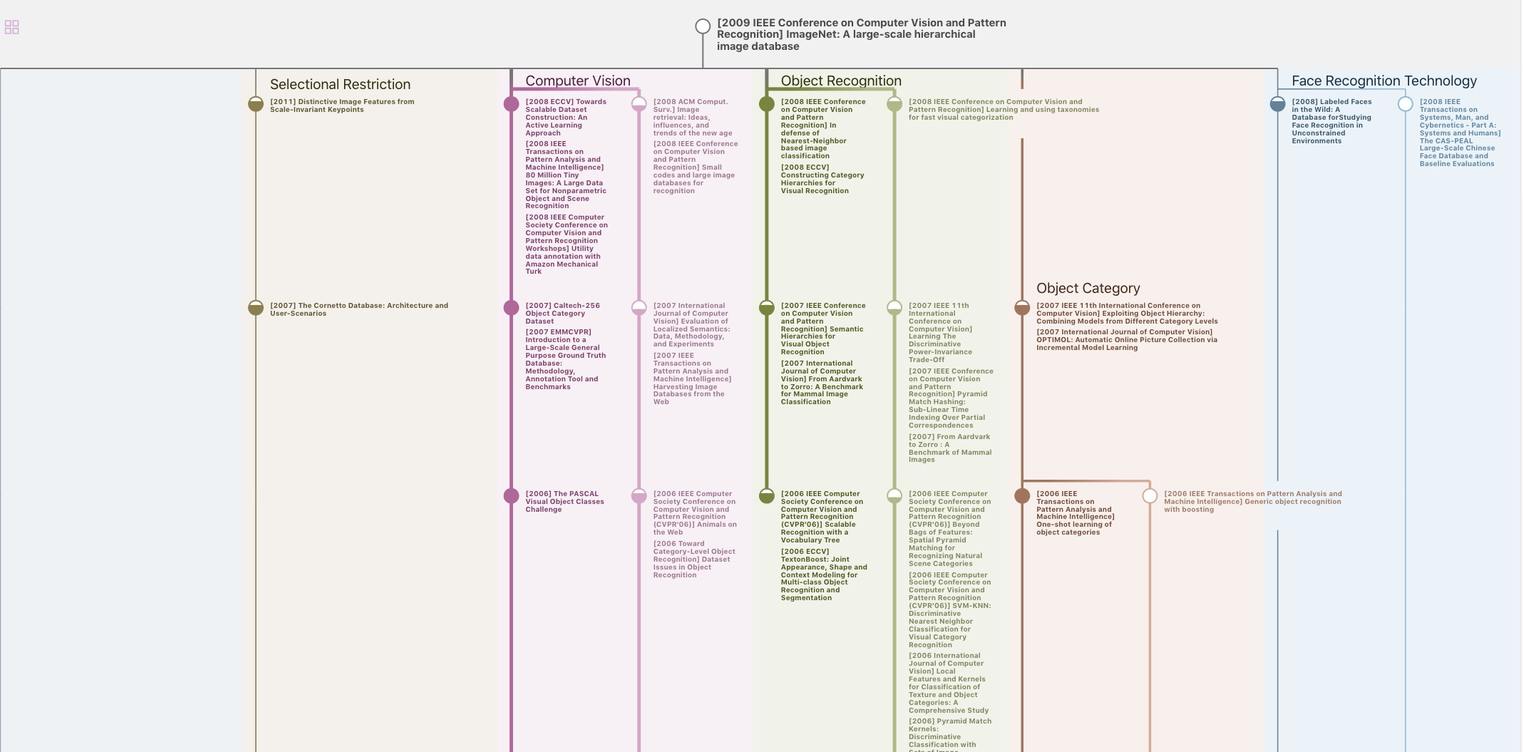
生成溯源树,研究论文发展脉络
Chat Paper
正在生成论文摘要