Advanced 3d Finite Element Simulation Of Thermoplastic Composite Induction Welding
20TH INTERNATIONAL CONFERENCE ON COMPOSITE MATERIALS(2015)
Abstract
The joining of carbon fiber reinforced thermoplastic (CFRTP) composites via electromagnetic (EM) induction welding is a complex multi-physics problem making the process very difficult to study by experiments alone. With the correct combination of experiments and simulations a more complete understanding of the process can be achieved together with an insight into which parameters need to be adjusted in order to optimize the process. The key elements of an induction welding simulation can be demonstrated using single plate heating models. Comparisons can also be made with double plate heating simulations whereby electrical and thermal contact resistance can also be taken into account. In the present work, finite element analysis (FEA) methods have been used to simulate single and double plate static induction heating of carbon fiber based thermoplastic composite laminates with a 2 mm thickness. The static plate heating tests are validated using the finite element simulation software LS-DYNA (R) by comparing point temperature measurements through the thickness of the specimens. Following on from the static experiments, a simulation test-bed has been created in order to study the continuous induction welding of two joining partners allowing the generation of 3D surface plots of temperatures through the thickness of the joint and most importantly at the joining interface. This information can then be used to assess the degree of bonding between the joining partners and overall quality of the weld.
MoreTranslated text
Key words
CFRTP, Induction welding, Finite element simulation
AI Read Science
Must-Reading Tree
Example
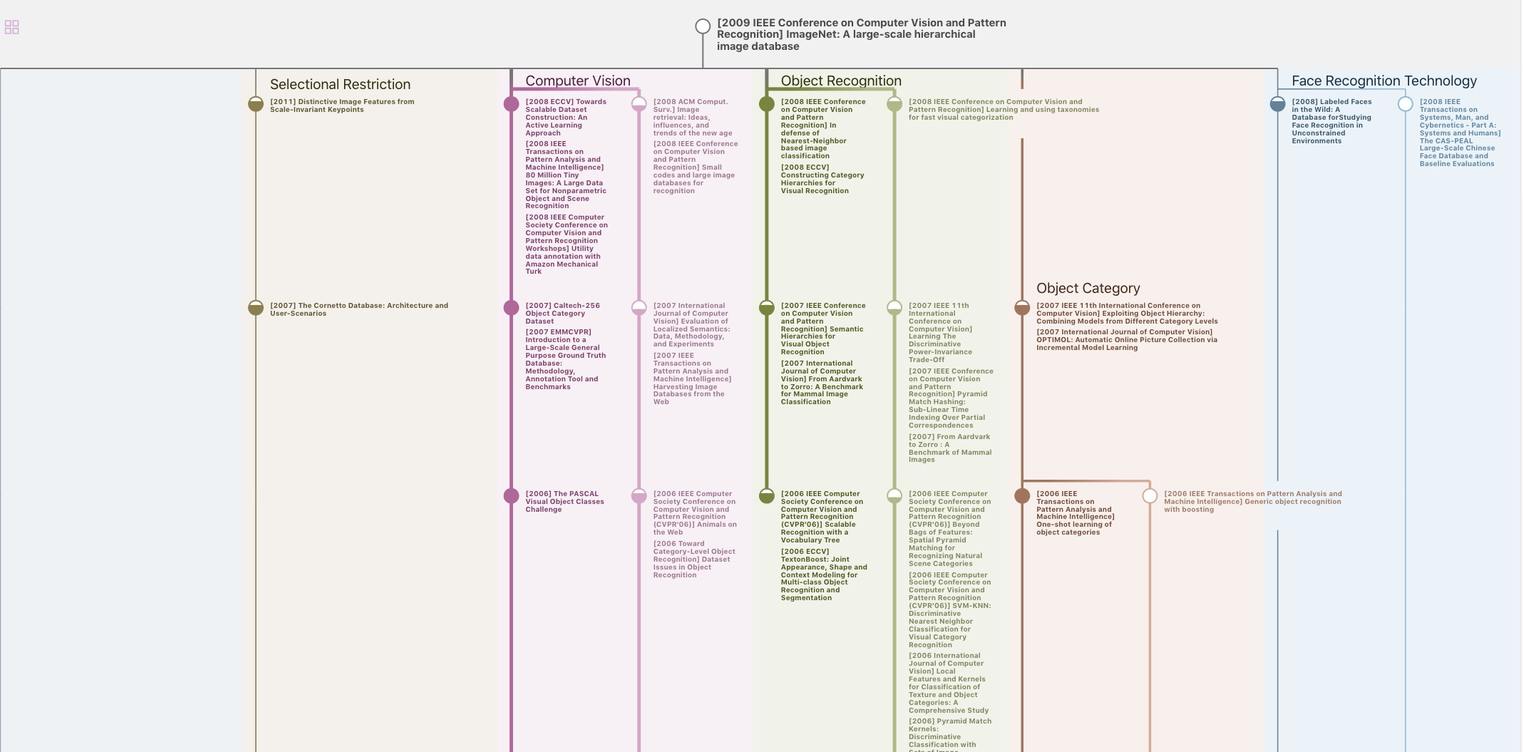
Generate MRT to find the research sequence of this paper
Chat Paper
Summary is being generated by the instructions you defined