Fatigue Tests And Fracture Behavior Analysis Of Porous Implant Materials Fabricated By 3d Metal Printing Technology
SENSORS AND MATERIALS(2021)
摘要
3D-printed Ti-6Al-4V materials can be used for implantation upon the confirmation of medical device specifications. Moreover, Young's coefficient of porous Ti-6Al-4V is close to that of the human bone, and it can allow the growth of bone cells through holes to fuse with implant materials. In this study, porous Ti-6Al-4V samples were fabricated by 3D printing. The fabricated porous Ti-6Al-4V samples had four rows of holes in the front and one or two rows of holes in the side. The mechanical properties and fatigue lifetimes of the porous Ti-6Al-4V samples were analyzed, where the samples were prepared by selective laser melting (SLM) 3D printing followed by post-heat treatment at a temperature of 500, 700, or 925 degrees C in a vertical tube furnace for 2 h with a heating rate of 10 degrees C/min. A tensile testing machine was used to measure Young's modulus and tensile strength of the porous Ti-6Al-4V alloy samples. Upon microstructural observation by SEM, the as-fabricated 3D-printed sample showed a fine needle-like martensite structure, and the 500- and 700-degrees C-treated samples showed a needle-like beta-structure. Additionally, the 925-degrees C-treated sample showed a coarse beta-structure. The porous Ti-6Al-4V sample subjected to post-heat treatment at 500 degrees C had the lowest Young's modulus and the highest tensile strength, where the strengths used in the fatigue testing were 0.1, 0.2, and 0.6 times the yield strength. The fatigue lifetimes of the porous Ti-6Al-4V samples with one and two rows of holes in the lateral side were 128941 and 22721 cycles at 0.2 times the yield strength, respectively.
更多查看译文
关键词
3D printing of porous materials, mechanical properties, fatigue testing, heat treatment, manufacturing process
AI 理解论文
溯源树
样例
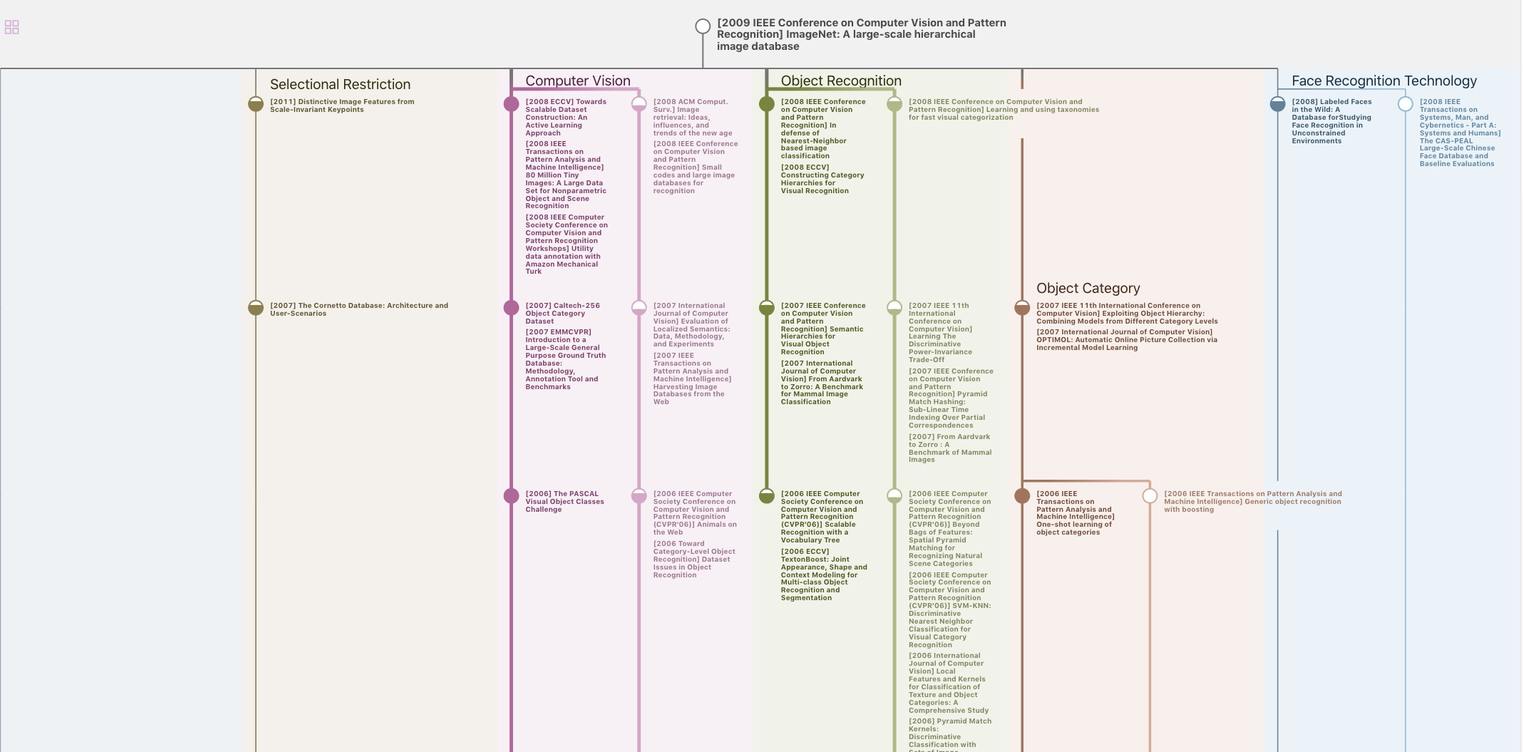
生成溯源树,研究论文发展脉络
Chat Paper
正在生成论文摘要