Baking system of aditya upgrade tokamaka
semanticscholar(2018)
摘要
In tokamaks, baking of vacuum vessel and first wall components is a prerequisite in order to obtain impurity free pure plasmas. Baking is performed to remove various kinds of impurities such as H2O, Carbon and Oxygen from the v essel wall and first wall components. ADITYA tokamak has been recently upgraded ADITYA-U tokamak to achieve shaped plasmas [1]. The Aditya U tokamak is equipped with a comprehensive baking system for baking the stainless steel v acuum vessel, pumping systems & associated diagnostic systems along with the graphite limiter and diverter tiles up to 150 C. T h e DC Glow discharge cleaning is also carried out in presence of baking to achieve better wall conditions for high performance plasma discharges in the machine. The structure of the Aditya Upgrade vacuum v essel is quite complex, with ~ 111 standard and customize port openings [2]. The baking of the vessel is carried out by positioning the current carrying filament heat in g elements around it . Due to space limitation between vessel and toroidal magnetic coils in the high-field (in-board) side, 1.5 mm thick silicon heaters has been designed and procured from M/s. Marathon Heaters, India. In -situ Installation of h eat er s has been quite challenging due to structural complexity of vacuum vessel. For efficient heat insulation, 6 mm thick silicon jacket designed and fabricated according to vacuum vessel profile and installed on vacuum vessel. A detail analysis has been carried in ANSYS for its optimum performance and to examine its effect on vacuum vessel, especially on the several weld joints. Whole baking system consists of ~ 80 heaters installed on different sectors of the vacuum vessel, pumps and diagnostics. The heaters are controlled in close loop by a Programmable Logic Controller (PLC) based automatic baking control system, which is developed in house. It comprises of three main phases, temperature ramp -up phase, constant heating phase (~ 150 C) and rampdown to room temperature phase. All these phases are individually controlled as required. The complete baking system has been tested thoroughly for its automatic operations for long hours (~48 Hours), integration, ruggedness, reliability, small form factor before integrating it to tokamak operation system for regular long-hour operation s. It also has been optimized for cost effectiveness. The detailed hardware concept, software design and prototype testing results and its regular operation in presence and absence of GDC will be discussed in this paper. Partial pressure of impurity gases is monitored in every baking cycle which decides and controls the baking temperature and duration automatically. Further, the potency of lithiumization carried out before, during and after baking has been compared for the first t ime in Aditya-U tokamak by estimating the lithium lifetime on the walls with plasma operation. The observation of conditioned vacuum vessel and effect of baking with different temperatures and durations on overall plasma performance along with technical challenges faced during installation, commissioning of baking system in Aditya-U will be presented in this paper.
更多查看译文
AI 理解论文
溯源树
样例
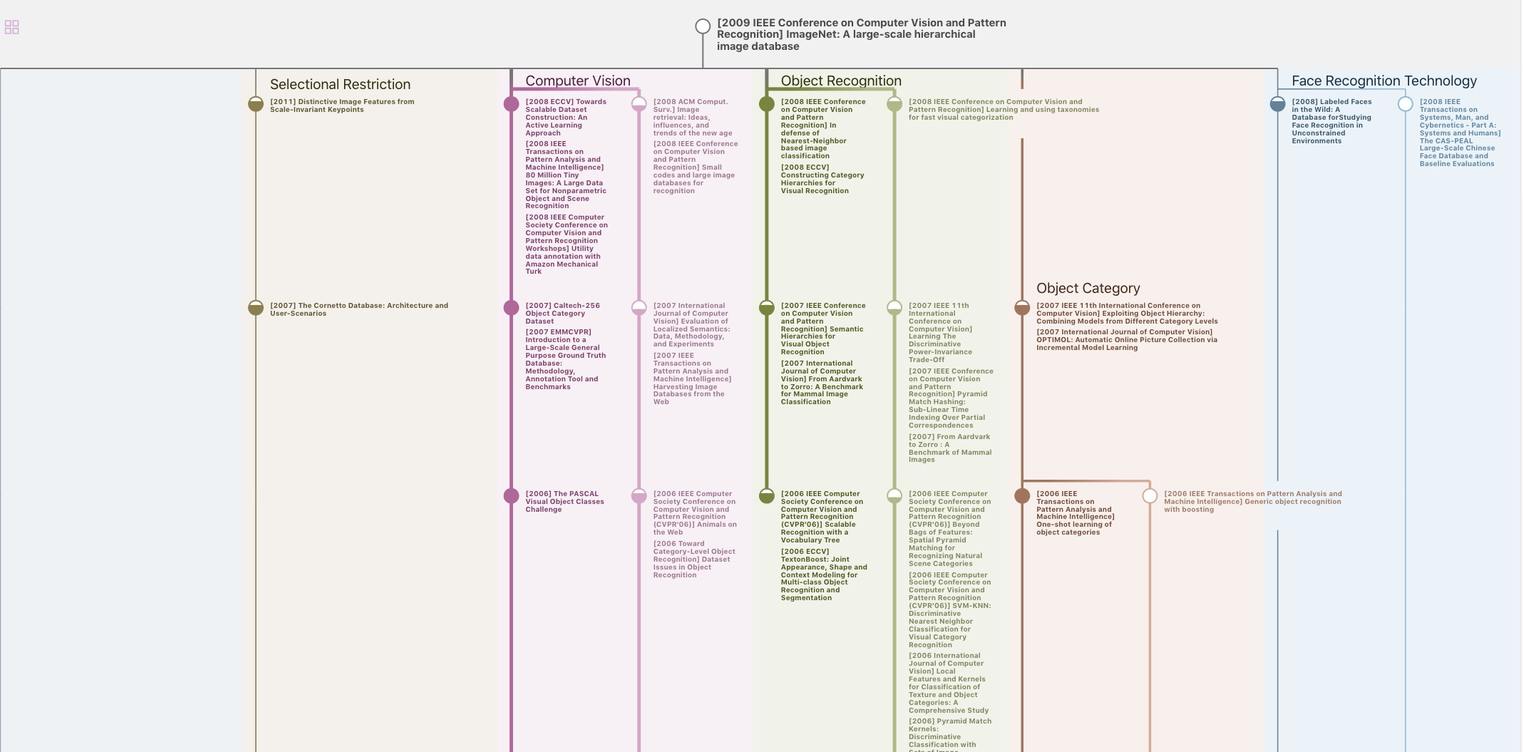
生成溯源树,研究论文发展脉络
Chat Paper
正在生成论文摘要