Experimentally validated simulations of blind hole drilling in 3d woven carbon/epoxy composite with processing-induced residual stresses
American Society for Composites 2021(2021)
摘要
Manufacturing-induced residual stresses in carbon/epoxy 3D woven composites arise during cooling after curing due to a large difference in the coefficients of thermal expansion between the carbon fibers and the epoxy matrix. The magnitudes of these stresses appear to be higher in composites with high throughthickness reinforcement and in some cases are sufficient to lead to matrix cracking. This paper presents a numerical approach to simulation of development of manufacturing-induced residual stresses in an orthogonal 3D woven composite unit cell using finite element analysis. The proposed mesoscale modeling combines viscoelastic stress relaxation of the epoxy matrix and realistic reinforcement geometry (based on microtomography and fabric mechanics simulations) and includes imaginginformed interfacial (tow/matrix) cracks. Sensitivity of the numerical predictions to reinforcement geometry and presence of defects is discussed. To validate the predictions, blind hole drilling is simulated, and the predicted resulting surface displacements are compared to the experimentally measured values. The validated model provides an insight into the volumetric distribution of residual stresses in 3D woven composites. The presented approach can be used for studies of residual stress effects on mechanical performance of composites and strategies directed at their mitigation.
更多查看译文
关键词
blind hole drilling,carbon/epoxy composite,3d woven carbon/epoxy,residual stresses,processing-induced
AI 理解论文
溯源树
样例
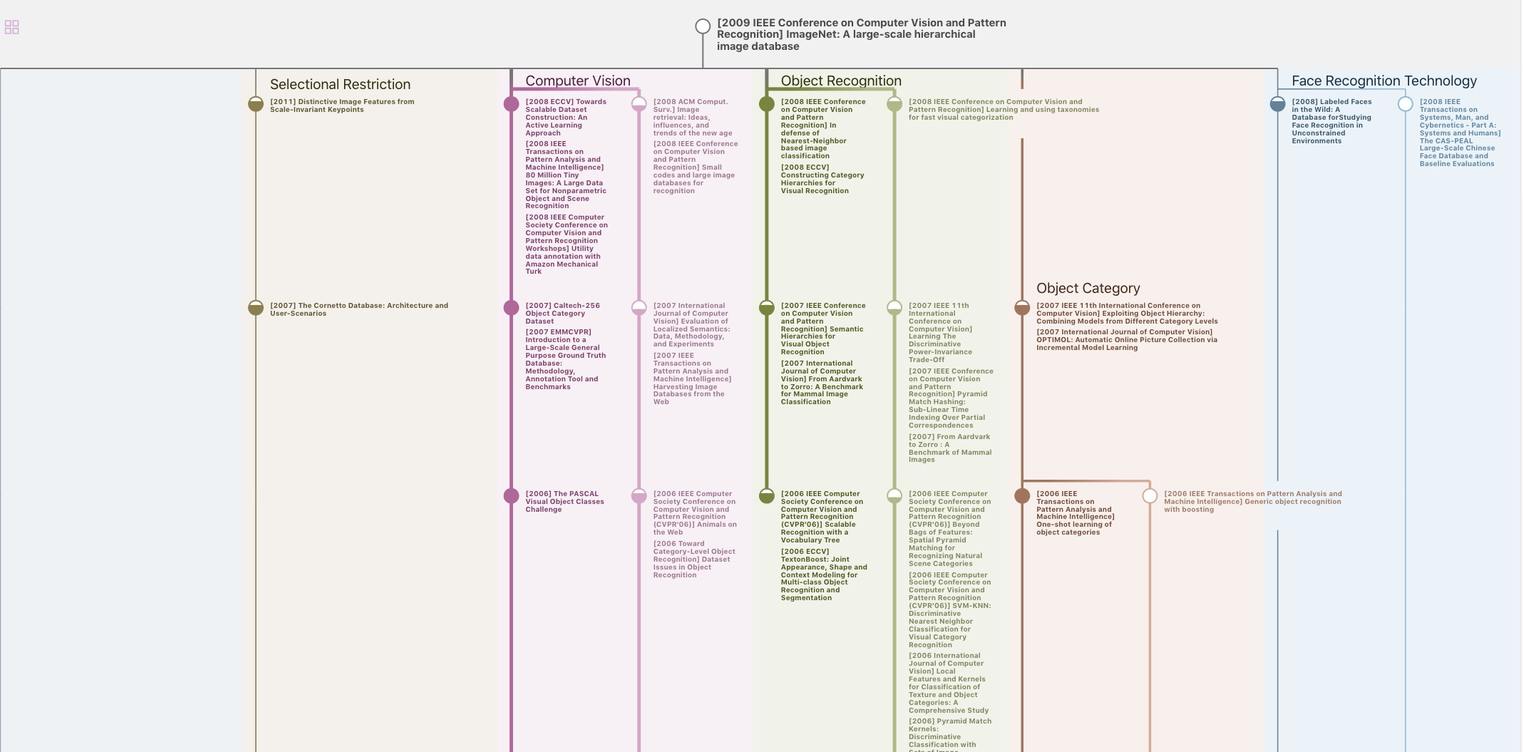
生成溯源树,研究论文发展脉络
Chat Paper
正在生成论文摘要