Laser Based Powder Bed Fusion of Plain Carbon and Low-Alloy Steels: Microstructure and Processability
semanticscholar(2021)
摘要
Despite the prominence of laser based powder bed fusion (LB-PBF) as an additive manufacturing technique, the number of alloys that have been approved for the process remains limited. In traditional manufacturing, ferrous alloys are the most common alloy group, consisting primarily of plain carbon and low-alloy steels. However, in LB-PBF, the production of ferrous alloys is limited to a small number of austenitic/precipitation-hardened stainless steels and tool steels. The lack of plain carbon and lowalloy steels stems from the negative impacts of carbon during processing, which promotes the formation of cracking defects within the as-built material. Hence, to expand the opportunities of LB-PBF, an understanding of how to process these carbon-containing ferrous alloys must be established. This work addresses the LB-PBF processability and microstructure of various plain carbon (0.06 to 1.1 wt.% C) and low-alloy steels (4130, 4140, 4340 and 8620). Microstructural analysis found the as-built specimens to consist of tempered martensite that formed due to the initial rapid cooling and subsequent intrinsic heat treatment that takes place during LB-PBF. Additionally, the presence of retained austenite was observed in alloys with ≥0.75 wt.% C and was caused by the depression of the martensite transformation temperatures, which left some austenite untransformed when cooling to room temperature. In terms of defects, porosity within the as-built specimens could be related to the chosen volumetric energy density (VED) and the carbon content of the alloy. At low VEDs, specimens contained large, irregular pores that related to lack of fusion porosity, while at high VEDs, specimens contained rounded, medium-sized pores that related to keyhole porosity. In terms of carbon content, increasing the amount of carbon was found to reduce the amount lack of fusion porosity at low VEDs while increasing the amount of keyhole porosity at higher VEDs. The decrease in lack of fusion porosity was caused by the improved wettability and flowability of the melt pool, while the increase in keyhole porosity was caused by increase in melt pool depth with higher carbon contents. Besides porosity, cold cracking was observed in some plain carbon and low-alloy steels, forming in specimens with a hardness above certain thresholds: ≥425 HV for Fe-C alloys, >460 HV for 4140 alloys and >500 HV for 4340 alloys. Increasing the VED or the laser power decreased the specimen hardness as both factors enhanced the intrinsic heat treatment of LB-PBF. This meant that cracking (in some alloys) could be avoided if a large enough VED or laser power was used. The carbon content also affected the as-built specimen hardness and thus the cracking susceptibility, a finding that explains why low carbon alloys (<0.43 wt.% C) did not display cracking at any of the tested VEDs, whereas high carbon alloys (≥0.75 wt.% C) displayed cracking at every tested VED. Using these findings, processing windows were established that produced high-density (>99.8%), defect-free plain carbon and low-alloy steel specimens without the requirement of build plate preheating.
更多查看译文
AI 理解论文
溯源树
样例
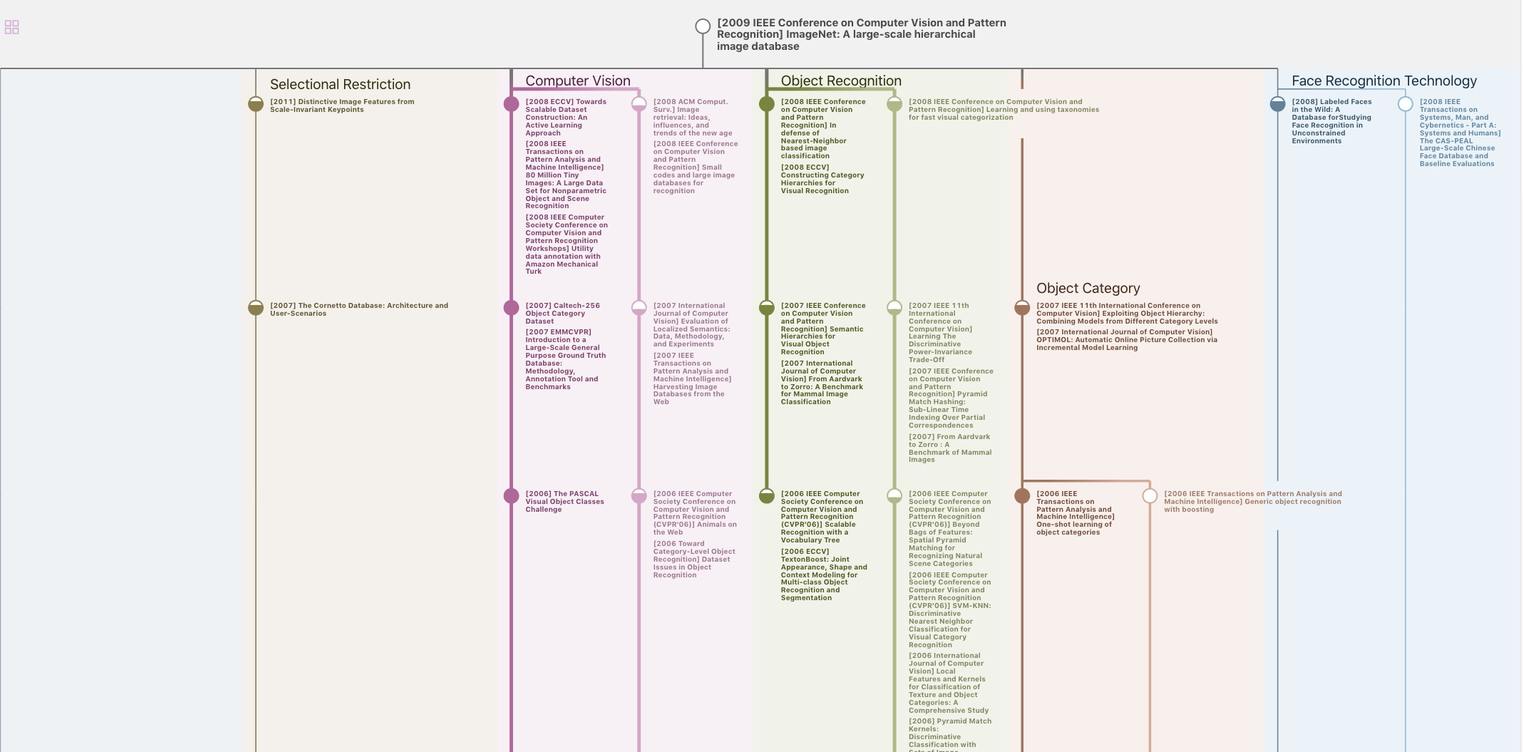
生成溯源树,研究论文发展脉络
Chat Paper
正在生成论文摘要