Cogging Torque Reduction by Means of Pole Segmentation Optimization on the Permanent Magnet Synchronous Machine
Anais do Congresso Brasileiro de Automática 2020(2020)
摘要
One of the main obstacles during the design of permanent magnet machines consists in reducing the developed torque ripple characteristic of this type of machine. The main component of such ripples is a parasitic torque, called cogging torque. A technique present in the literature to reduce this parasitic torque considers the segmentation of the poles. This allows a decrease in the cogging torque, however reducing the air gap flux density too and thus the torque mean. Thus, in order to keep the torque mean reduction in reasonable levels, optimization techniques can be employed with the pole segmentation. The variables to be optimized are the number, distance and width of the segments. The present article proposes two methods to optimize these variables in order to minimize the cogging torque, but also maintain a satisfactory flux density value. Some constraints are added to account for the machine construction feasibility. The proposed methods were validated through a nite element analysis. The results proved the effectiveness of the proposed methods, with a reduction by up to 76% in the cogging torque and keeping, in the best case, about 95% of the reference machine air gap flux density and 78% in the worst one.
更多查看译文
AI 理解论文
溯源树
样例
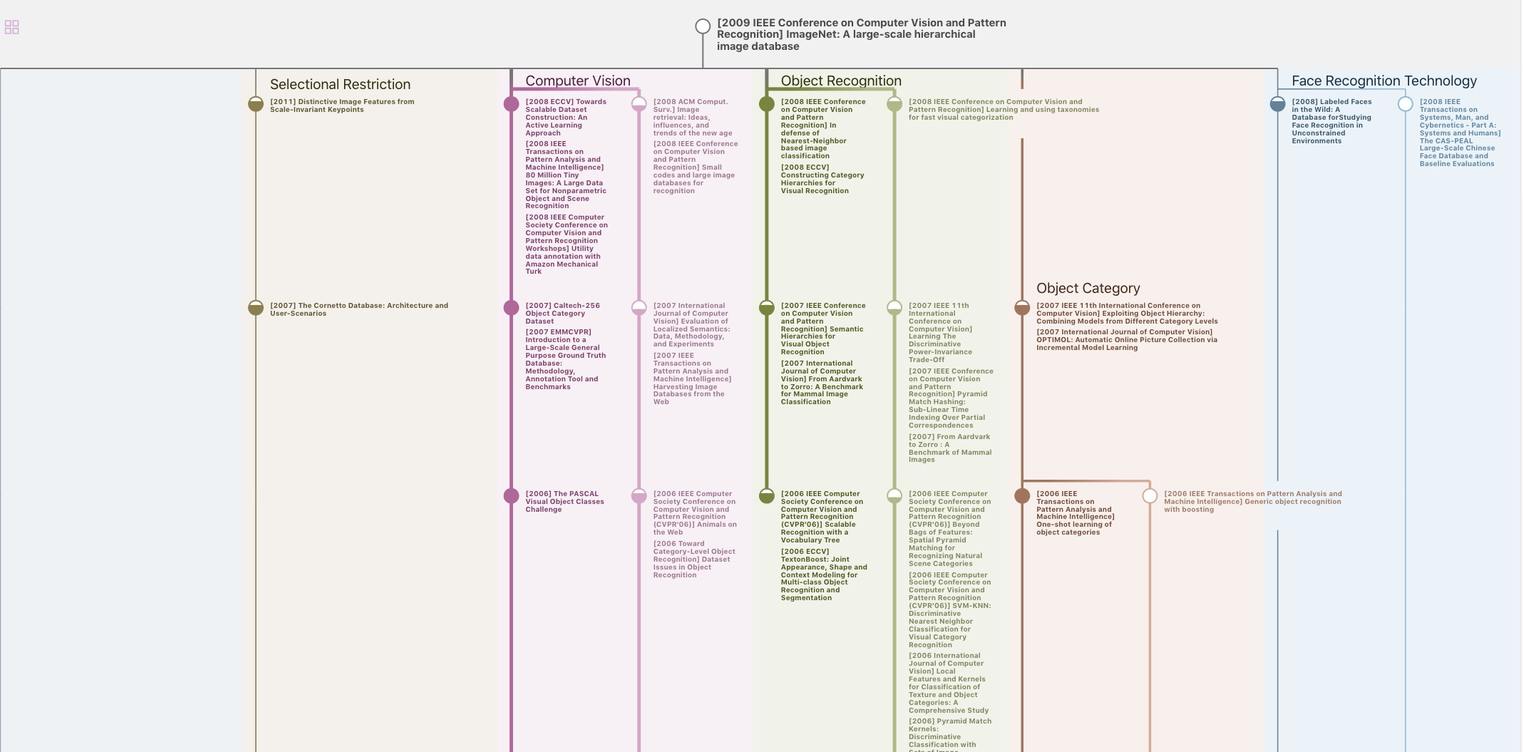
生成溯源树,研究论文发展脉络
Chat Paper
正在生成论文摘要