Correlating in-situ sensor data to defect locations and part quality for additively manufactured parts using machine learning
Journal of Materials Processing Technology(2022)
摘要
In this work, process monitoring data, including layerwise imagery, multi-spectral emissions, and laser scan vector data, were collected during laser-based powder bed fusion additive manufacturing and correlated to fatigue performance. All parts were X-ray CT scanned post-build, and internal flaws were identified via an automated defect recognition software. Convolutional neural networks were trained to discriminate flaws from nominal build conditions using in situ data modalities only. Trained classifiers were then tested against a previously unseen data set collected from an independent build, and classification performance and metrics for information content provided by each individual modality were formally established. Correlations were drawn between the detected flaw populations and the corresponding fatigue properties, demonstrating that fatigue critical lack-of-fusion flaws can be detected via machine learning of in situ sensor data. The present results also show that, at least from a classification accuracy perspective, flaw detection via ML on process monitoring data is a viable path forward for real-time flaw detection and automated, interlayer repair strategies. However, strategies for extracting and analyzing sensor data in real-time without incurring excessive increases in build time must first be developed. These developments represent necessary components to draw direct correlations between in situ data modalities, internal part quality, and fatigue performance.
更多查看译文
关键词
Additive manufacturing,Process monitoring,Machine learning,Qualification
AI 理解论文
溯源树
样例
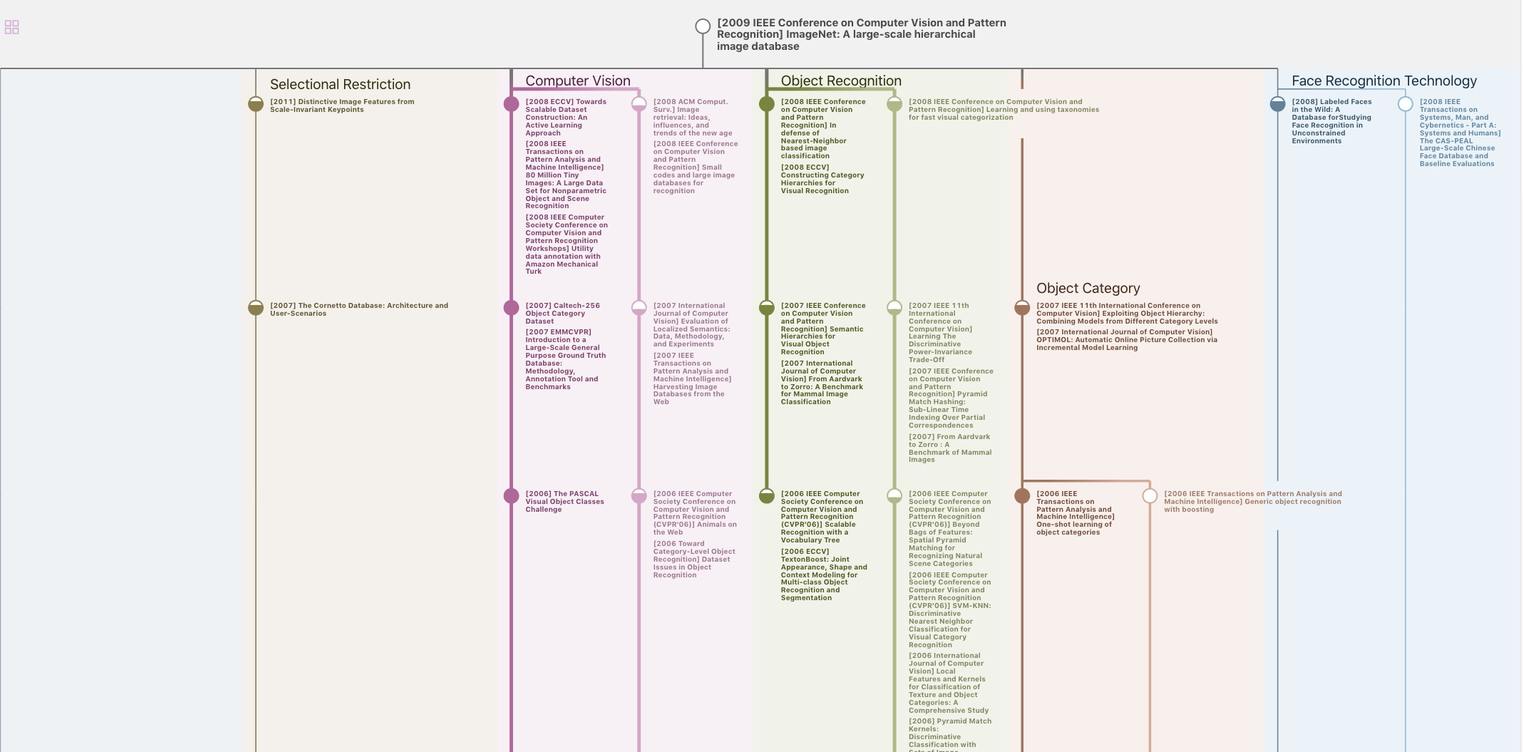
生成溯源树,研究论文发展脉络
Chat Paper
正在生成论文摘要