Modeling and optimization of machining parameters for minimizing surface roughness and tool wear during AISI 52100 steel dry turning
Materials Today: Proceedings(2022)
摘要
AISI 52100 steel machining has drawn a greater interest in industrial and manufacturing applications due to its high strength, sublime hardness, and impressive wear resistance. Conventional cutting fluid-assisted machining is an objectionable option owing to its threat to the environment and operators. Dry machining or near dry machining is the primary choice to promote sustainable manufacturing. Multi-objective optimization is becoming an indispensable phase in choosing cutting conditions for desirable machinability characteristics. In the present work, a multi-objective optimization approach is utilized to model and optimize the surface roughness and tool flank wear during the dry cutting of AISI 52100 steel. To examine and quantify the relationship between process input and output parameters, a full factorial design, a response surface methodology (RSM), and a desirability function approach is adopted. The obtained optimum levels of the control factors are cutting speed at 119.734 m/min, feed rate at 0.1 mm/rev, and depth of cut at 0.4 mm; and the corresponding predicted surface roughness and tool wear are 2.967 µm and 0.052 mm, respectively. Model fitness and efficacy were judged through confirmation tests. A correlation coefficient (R2) of 0.9921 for surface roughness and 0.9876 for tool wear indicates a significant agreement between model predictions and experimental results. Thus, the RSM model used in the work can minimize the expensive experimental trials of machining processes.
更多查看译文
关键词
Multi-objective optimization,Response surface methodology,Dry machining,AISI 52100 steel,Tool wear,Surface roughness
AI 理解论文
溯源树
样例
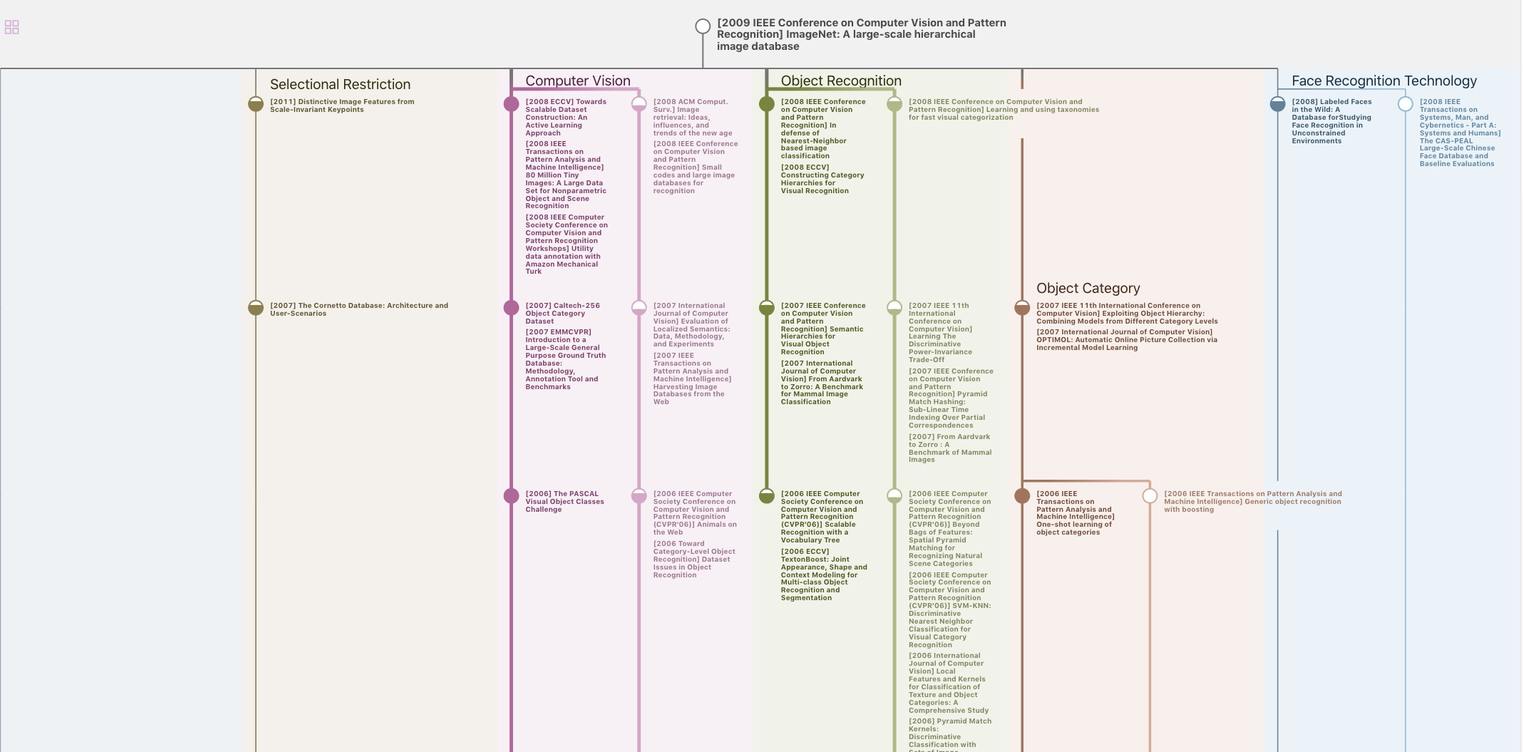
生成溯源树,研究论文发展脉络
Chat Paper
正在生成论文摘要