The surface and subsurface integrity in coupled operation of fused deposited modeling and centrifugal disk finishing
RAPID PROTOTYPING JOURNAL(2022)
摘要
Purpose - This paper aims to investigate the effect of centrifugal disk finishing (CDF) technique on the surface and subsurface characteristics of the fused deposited modeling (FDM) parts in both theoretical and experimental aspects. From theoretical aspect, a novel theoretical model is developed as a function of layer deposition orientation, layer thickness, finishing working time, density ratio and hardness ratio to estimate the surface roughness profile of FDM part at different finishing conditions and finishing time intervals. Meanwhile, from the experimental aspect, an experimental campaign was performed under different mechanical and mechanical-chemical finishing conditions to verify the theoretical model and also assess the surface and subsurface characteristics of the polished parts. Design/methodology/approach - The theoretical model commences with an approximation of surface profile of the FDM part through a sequence of parabola arcs, continues with the calculation of reference line and machined surface profile and leads to a formulation of surface roughness of as-printed and polished surface. In the experimental section, the FDM parts are polished under dry, pure water, 25% and 50% volumetric aqueous acetone solutions finishing conditions through CDF technique. Findings - The comparison between experimental and theoretical results reveals 9% mean absolute error between theoretical and experimental results. Meanwhile, Rq reduction percentage of polished parts under dry, pure water, 25% and 50% aqueous acetone solutions are 66.1%, 54.5%, 56.9% and 67.2%, respectively. The scanning electron microscopy results reveal severe layer damage in dry finishing condition, while the application of 50% aqueous acetone as a polishing solution completely eliminates layer damage. Another promising finding was sticky material phenomenon on the surface of polished part under 25% finishing condition. The Shore hardness test illustrates that the surface hardness improvement of the polished parts under dry, pure water, 25% and 50% aqueous acetone solutions finishing conditions are 8.4%, 2.25%, 4.36% and 10.8%, respectively. The results also revealed that the dimension variation of polished parts under dry, pure water, 25% and 50% aqueous acetone solutions are 0.634%, 0.525%, 0.545% and 0.608%, respectively. The edge profile radius of the as-printed part is 134 mu m, while the edge profiles radius of the polished parts under dry, pure water, 25% aqueous acetone solution and 50% aqueous acetone solution are 785.5 mu m, 545.5 mu m, 623.5 mu m and 721.5 mu m, respectively, at the polishing time of 720 min. Originality/value - This paper fulfills an identified need to study the benefits of the mechanical-chemical polishing technique in comparison to mechanical and chemical polishing strategy of the FDM parts for the first time. Beside the experimental campaign, the novel analytical formulation of surface roughness as a function of mechanical properties of abrasive media and FDM part and finishing specifications provides a valuable insight in the case of material-removal processes.
更多查看译文
关键词
Fused deposition modeling, Centrifugal disk finishing, Roughness prediction, Surface improvement, Additive manufacturing, Mechanical-chemical polishing, Surface roughness, Surface finishing
AI 理解论文
溯源树
样例
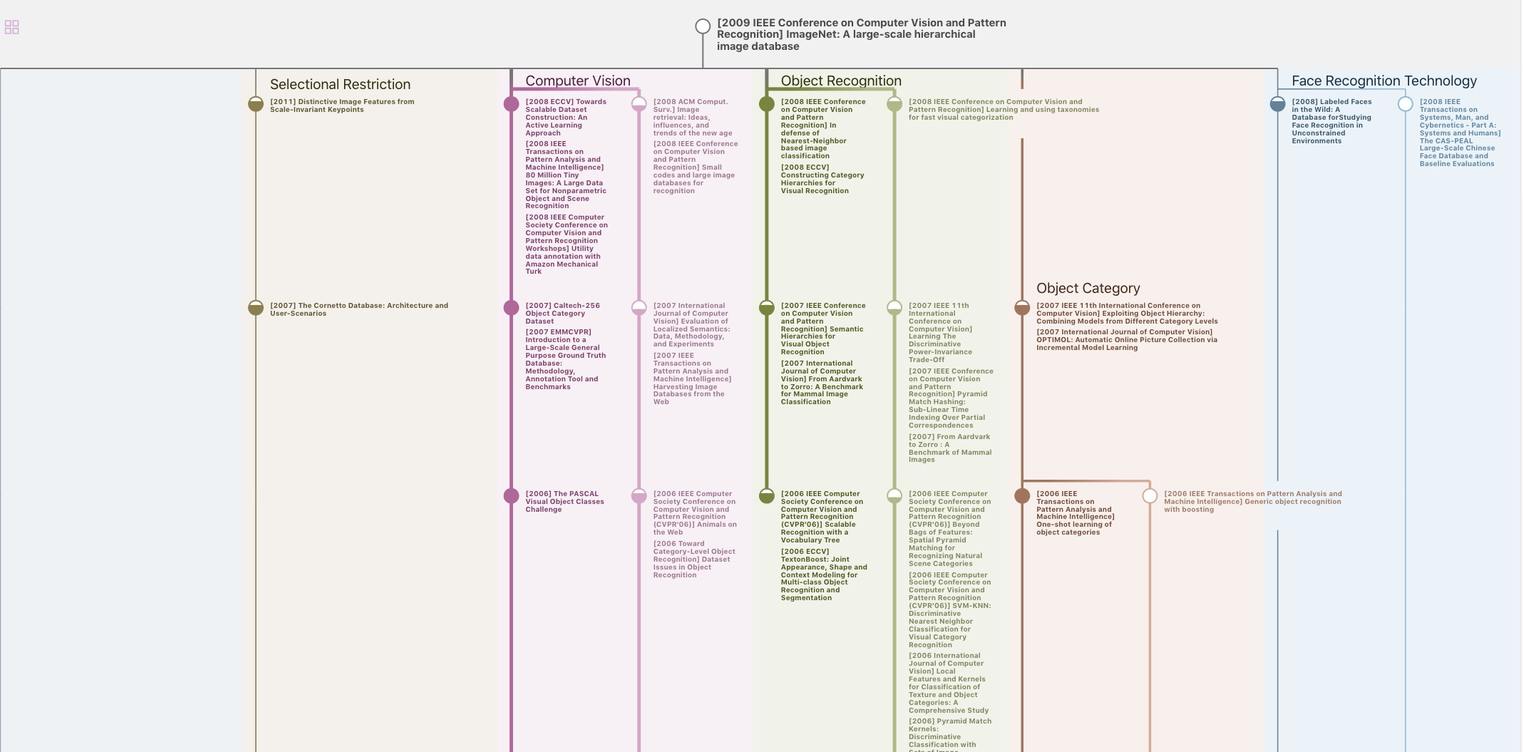
生成溯源树,研究论文发展脉络
Chat Paper
正在生成论文摘要