Improving Fatigue Limit and Rendering Defects Harmless through Laser Peening in Additive-Manufactured Maraging Steel
METALS(2022)
摘要
Additive-manufactured metals have a low fatigue limit due to the defects formed during the manufacturing process. Surface defects, in particular, considerably degrade the fatigue limit. In order to expand the application range of additive-manufactured metals, it is necessary to improve the fatigue limit and render the surface defects harmless. This study aims to investigate the effect of laser peening (LP) on the fatigue strength of additive-manufactured maraging steel with crack-like surface defects. Semicircular surface slits with depths of 0.2 and 0.6 mm are introduced on the specimen surface, and plane bending-fatigue tests are performed. On LP application, compressive residual stress is introduced from the specimen surface to a depth of 0.7 mm and the fatigue limit increases by 114%. In a specimen with a 0.2 mm deep slit, LP results in a high-fatigue-limit equivalent to that of a smooth specimen. Therefore, a semicircular slit with a depth of 0.2 mm can be rendered harmless by LP in terms of the fatigue limit. The defect size of a 0.2 mm deep semicircular slit is greater than that of the largest defect induced by additive manufacturing (AM). Thus, the LP process can contribute to improving the reliability of additive-manufactured metals. Compressive residual stress is the dominant factor in improving fatigue strength and rendering surface defects harmless. Moreover, the trend of the defect size that can be rendered harmless, estimated based on fracture mechanics, is consistent with the experimental results.
更多查看译文
关键词
additive manufacturing, maraging steel, laser peening, compressive residual stress, surface defect, fatigue limit
AI 理解论文
溯源树
样例
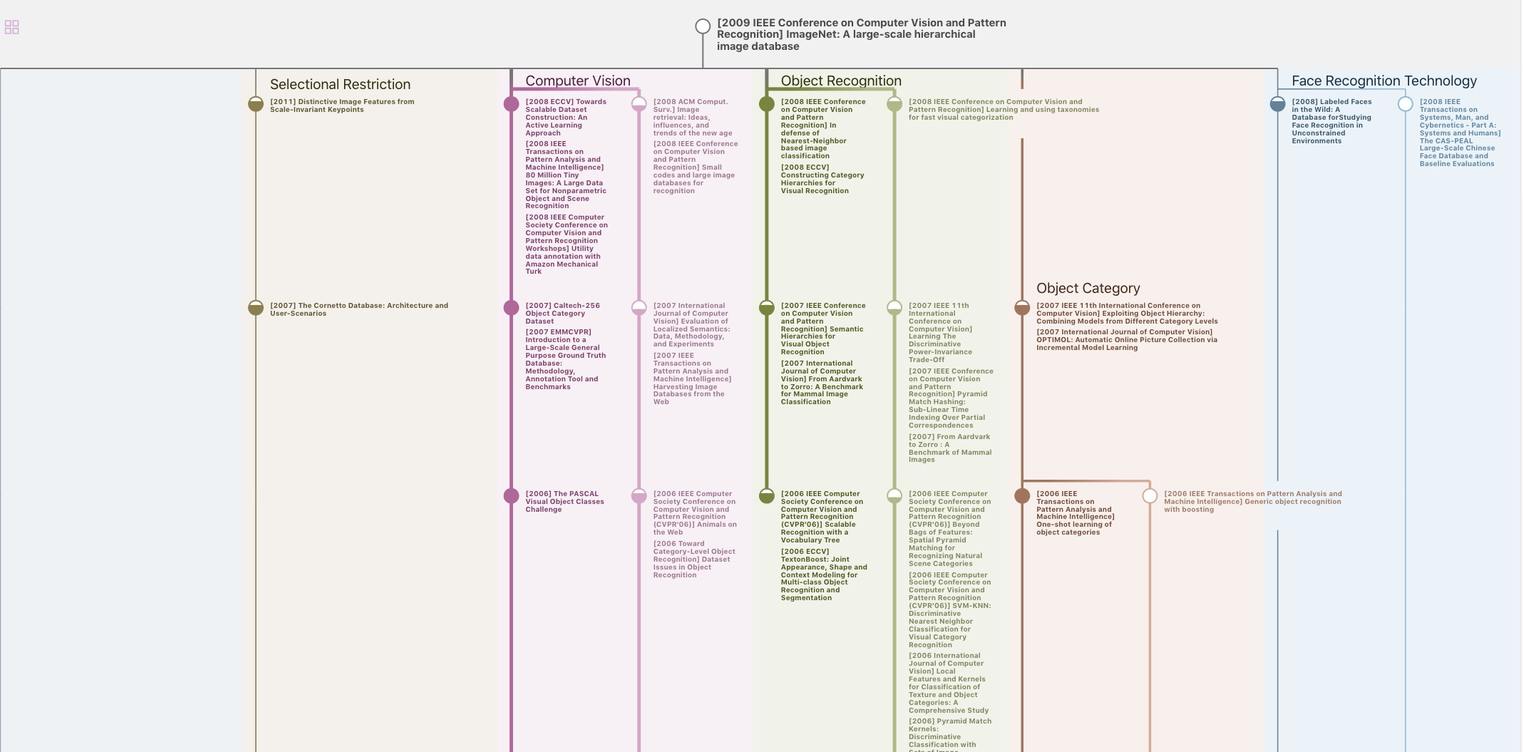
生成溯源树,研究论文发展脉络
Chat Paper
正在生成论文摘要